| Til bund | | Forside |
Miljøprojekt nr. 1009, 2005
Behandlingsteknologier for batterier
Fase 1. Kortlægning af eksisterende behandlingsmetoder
Indholdsfortegnelse
Forord
Sammendrag og konklusioner
Summary and conclusions
1 Indledning
2 De forskellige batterityper
3 Status for batteriområdet i Danmark
4 Kortlægning af eksisterende behandlingsteknologier
5 Dansk løsning
6 Referencer og litteratur
Bilag Beskrivelse af anlæg
Forord
Denne rapport beskriver resultaterne af fase 1 i projektet "Vurdering af eksisterende behandlingsteknologier og de bedst egnede løsninger for batterityper indsamlet i Danmark". Projektet er delvist
finansieret af midler fra Udviklingsordningen under Program for renere produkter m.v.
Projektet er delt i to faser:
Fase 1. Kortlægning af eksisterende behandlingsmetoder
Fase 2. Praktisk afprøvning af metode til behandling af alkali- og brunstensbatterier
Fase 1 er udført i perioden januar 2001 - maj 2002 af Kommunekemi a/s ved cand. scient. Steen Vestervang. Endvidere har kemiingeniørstuderende Ane Schmidt medvirket i foråret 2001.
Fase 2 er påbegyndt i starten af 2002.
Projektet har været fulgt af en følgegruppe bestående af:
Lotte Rahbek (formand), Miljøstyrelsen
Ole Kristensen, Kommunekemi a/s
Steen Vestervang, Kommunekemi a/s
Fra maj 2002 har Anne Nielsen, Miljøstyrelsen afløst Lotte Rahbek i forbindelse med færdiggørelse af rapporten.
Sammendrag og konklusioner
Formålet med fase 1 i denne undersøgelse har været - med speciel fokus på alkali- og brunstensbatterier - at beskrive de behandlingsmetoder, der i dag eksisterer for brugte batterier. I fase 2 er i et
pilotanlæg gennemført en praktisk afprøvning af en metode til forbehandling af alkali- og brunstensbatterier.
Batterier kan opdeles i primære (engangsbatterier) og sekundære (genopladelige) batterier. De primære batterier er bl.a. de velkendte alkali- og brunstensbatterier, der udgør hovedparten af de batterier der
anvendes i Danmark, og anvendes bredt i husholdninger.
Forbruget af primære batterier i Danmark er anslået til ca. 2.500 tons om året, og ca. 2.400 tons af disse er alkali- og brunstensbatterier /1/. Hertil kommer forbruget af sekundære batterier, men der findes
ikke samlede opgørelser over dette forbrug. For lukkede NiCd-batterier er forbruget dog anslået til 218-328 tons i 1997 /20/. Forbruget af blyakkumulatorer, der hovedsageligt anvendes i biler, er 15.000 -
16.000 tons pr. år /21/.
Der er i Danmark ikke en indsamlingsordning, der omfatter alle batterier. Kun for blyakkumulatorer og NiCd-batterier er der etableret særlige ordninger. Indsamlingsraten for blyakkumulatorer er i dag tæt
på 100% /21/, mens den for NiCd-batterier er vurderet til ca. 50 % /37/.
Ses bort fra de store sekundære batterier må indsamlingspotentialet for både primære og sekundære, små batterier formodes at være 2.500 - 3.000 tons årligt, idet der dog også skal tages hensyn til både
”pulterkammer-” og ”pipeline-effekten”. Regnes med en indsamlingsrate på 75% bliver den indsamlede mængde på 1.900 - 2.300 tons pr. år.
Af hensyn til den videre behandling af de indsamlede batterier, er det nødvendigt at sortere dem i typer. Der er udviklet systemer til automatisk sortering og det vurderes, at teknologien i dag er så langt
fremme, at automatiske sorteringsanlæg, både med hensyn til omkostninger og kvalitet, er konkurrencedygtige med manuel sortering. Den automatiske sortering forventes at blive lettere fremover, da flere og
flere af de indsamlede kviksølvfrie alkalibatterier vil være mærket med en UV-markør, der let kan detekteres.
Ved en fremtidig batteriindsamling i Danmark bør der således etableres et centralt automatisk sorteringsanlæg.
For lithium-, NiCd-, NiMH-batterier samt knapceller vil de indsamlede mængder blive så små, at det ikke vil være rentabelt at etablere en behandling udelukkende for danske batterier. For NiCd- og
NiMH-batterier samt kviksølvholdige knapceller er der i dag behandlingskapacitet i Europa, mens der for lithiumbatterier er ved at blive etableret europæiske behandlingsmuligheder.
Alkali- og brunstensbatterier udgør langt den største fraktion (80-90%), hvorfor det for disse kan være relevant at etablere en eller anden form for behandling i Danmark.
De væsentligste indholdsstoffer i alkali- og brunstensbatterier er: zink (20-25%), jern (15-20%) og mangan (20-25%). Nyere alkalibatterier produceret i Europa er ikke tilsat kviksølv og det er heller ikke
tilladt at importere batterier til EU, der er tilsat kviksølv. Kviksølvfrie alkalibatterier skal ligesom brunstensbatterier ikke betragtes som farligt affald, men kan principielt afbrændes i
husholdningsforbrændingsanlæg eller deponeres på almindelige lossepladser. Imidlertid må det forventes, at der i nogen tid endnu også vil indsamles gamle batterier, der kan indeholde helt op til 1% kviksølv.
Ved en forbrænding i almindelige forbrændingsanlæg eller ved deponering på losseplads mistes de ressourcer der er i batterierne. Årligt er dette ca. 500 tons zink, 400 tons jern og 500 tons mangan.
Ønskes disse ressourcer genvundet er der principielt to forskellige oparbejdningsmetoder:
- Oparbejdning i metalindustrien (stålværker, zinkværker og lign.)
- Oparbejdning i anlæg specielt designet til batterier
Økonomisk er oparbejdning i metalindustrien det mest attraktive. Prisniveauet er ofte under 2.000 kr. pr. tons, hvis batterierne tilsættes som en delstrøm i råmaterialet. Problemerne ved denne metode er
imidlertid, at disse anlæg generelt ikke kan håndtere kviksølv og for meget organisk materiale (plastik etc.). Dette kan ved behandling af batterier give emissionsproblemer, hvorfor de tilsættes som en
delstrøm (typisk 5%). Herved kan der ske en fortynding af emissionerne.
Endvidere kan oparbejdning på stålværker give tekniske problemer, idet kobber fra batterierne ophobes i stålet, hvor det ødelægger stålets egenskaber. Der er dog delte meninger om hvorvidt dette er et
problem, og det afhænger i høj grad af, hvilken stålkvalitet der fremstilles. Endelig er genanvendelsesgraden forholdsvis lav (20-40%).
Der findes ikke stålværker i Danmark, der kan behandle batterier, så ved denne løsning er det derfor nødvendigt, at transportere batterierne til behandling i udlandet. Ved 1.000 - 2.000 km transport vil
transportomkostningerne være i størrelsesordnen 500 - 1.000 kr. pr. tons.
Oparbejdning i specialanlæg er typisk dyrere fordi anlæggene er væsentligt mindre i forhold til metalværkerne. Prisniveauet ligger typisk mellem 5.000 og 10.000 kr. pr. tons. Et enkelt sted er prisen endda
over 10.000 kr. pr. tons.
Til gengæld er flere af disse anlæg indrettet således, at de kan behandle batterier med kviksølv, ligesom der er taget højde for det organiske indhold i batterierne, og endelig er der en høj genanvendelsesgrad
(50-70%). Tilsyneladende er der en sammenhæng mellem prisniveau og kvalitet, således at de dyreste virksomheder generelt også har den højeste miljømæssige standard og genanvendelsesgrad.
I tabel 1 er vist en forenklet sammenligning af fordele og ulemper ved oparbejdning af brunstens- og alkalibatterier i henholdsvis metalindustrien og specialanlæg.
|
Pris |
Miljø |
Genanvendelsesgrad |
Metalindustrien |
++ |
(-) |
- |
Specialanlæg |
- |
+ |
+ |
Tabel 1. Oparbejdning af brunstens- og alkalibatterier. Forenklet sammenligning af fordele (+) og ulemper (-) i henholdsvis metalindustrien og specialanlæg.
På grund af den forholdsvis lille mængde alkali- og brunstensbatterier, der vil kunne indsamles i Danmark, vurderes den mest optimale løsning for disse batterier at være:
- Forbehandling/afgiftning af batterierne på dansk anlæg
- Endelig oparbejdning i udlandet
Forbehandlingen af alkali- og brunstensbatterierne kan være en pyrolyse eller forbrænding af batterierne i en separat proces, hvorved plastik og lignende samt evt. kviksølv, cadmium og bly fjernes fra
batterierne. Herefter er batterierne ”afgiftet” og kan uden miljømæssige problemer anvendes hvor som helst i metalindustrien, men problemet ved denne metode er imidlertid den lave genanvendelsesprocent
på 20-40%. Ønskes der en højere genanvendelsesprocent, er det nødvendigt efter afgiftningen at neddele batterierne, sortere materialet i fraktioner, og sende disse til specialiserede oparbejdere. Herved kan
opnås en genanvendelsesprocent på op mod 70%.
I fase 2 i dette projekt belyses mulighederne yderligere for en forbehandling af brunstens- og alkalibatterier ved at gennemføre praktiske forsøg med pyrolyse på et pilotanlæg opstillet på Kommunekemi.
Samlet set kan en dansk behandlingsmodel se således ud:
- Indsamling af alle batterier
- Sortering i typer på centralt placeret sorteringsanlæg
- NiCd-, NiMH-, lithiumbatterier, knapceller m.v. sendes på grund af den lille mængde til oparbejdning i udlandet
- Alkali- og brunstensbatterier forbehandles/”afgiftes” på et anlæg i Danmark, hvorefter den endelig oparbejdning sker på anlæg i udlandet.
Summary and conclusions
The purpose of phase 1 in this description - especially focusing on alkaline manganese batteries and zinc-carbon batteries - has been to describe the existing treatment methods for spent batteries. In phase 2
we have carried out a practical test for pre-treatment of alkaline manganese batteries and zinc-carbon batteries in a pilot plant.
Batteries can be divided into primary batteries that can only be discharged and secondary batteries that can also be recharged. Primary batteries include the well-known alkaline manganese batteries and
zinc-carbon batteries, and they comprise the majority of the batteries used in Denmark. These are increasingly being used in households.
The consumption of primary batteries in Denmark has been estimated at app. 2,500 tonnes annually, and app. 2,400 tonnes of these are alkaline manganese batteries and zinc-carbon batteries/1/. To this
must be added the consumption of secondary batteries, but there is no overall statement of this consumption. For closed NiCd batteries consumption has been estimated at 218-328 tonnes in 1997 /20/. The
consumption of lead accumulators, primarily used in cars, is 15-16,000 tonnes annually /21/,
In Denmark there is no organized collection scheme for all types of batteries. However, a special scheme has been established for lead accumulators and NiCd batteries. The collection rate for lead
accumulators is today close to 100% /21/, while it has been estimated at app. 50% for NiCd batteries/37/.
Excluding the big secondary batteries, the collection potential for primary as well as secondary small batteries is estimated at 2,500-3,000 tonnes annually, also taking into account the “hoarding effect” and
the “pipeline effect”. Estimating a collection rate of 75%, the collected quantity will be 1,900-2,300 tonnes annually.
Concerning the further treatment of the collected batteries, it is necessary to separate the batteries into different types. Systems for automatic separation have been developed, and it is estimated that today's
technology is so advanced that an automatic separation plant can compete with manual separation as regards costs and quality. Automatic separation is expected to be easier in the future as an increasing
number of the mercury-free alkaline manganese batteries being collected have been marked with a UV marker, which can easily be detected.
Any future battery collection scheme in Denmark should include a central, automatic separation plant.
The collected quantities for lithium, NiCd and NiMH batteries as well as button cells will be so small, that it will not be economical to establish a treatment plant for Danish batteries alone. For NiCd and
NiMH batteries and mercury containing button cells, treatment capacity today exists in Europe, whereas for lithium batteries European treatment possibilities are being established.
Alkaline manganese batteries and zinc-carbon batteries form by far the greatest fraction (80-90%), and therefore it may be relevant to establish some kind of treatment in Denmark. The most essential
substances in alkaline manganese batteries and zinc-carbon batteries are: zinc (20-25%), iron (15-20%) and manganese (20-25%). Alkaline manganese batteries of more recent date and produced in
Europe do not contain mercury, and it is illegal to import mercury-containing batteries into EU. Like zinc-carbon batteries, mercury-free alkaline manganese batteries are not considered as hazardous waste,
but can in principle be incinerated in household incineration plants or be deposited at ordinary refuse dumps. However, it is probable that old batteries, containing up to 1% mercury, will be collected for
some time yet.
By incineration in ordinary incineration plants or by depositing at refuse dumps, the resources in the batteries are lost. This loss is annually app. 500 tonnes of zinc, 400 tonnes of iron and 500 tonnes of
manganese.
In principle, two different processing methods for recovery of these resources exist, i.e.:
- Processing within the metal industries (steelworks, zinc works etc.)
- Processing in plants, primarily designed for batteries
From an economic perspective, processing within the metal industries is most attractive. The price level is often under DKK 2,000 per tonne, if the batteries are added as a substream to the raw material.
The problems of this method are, however, that the plants in general are not able to handle mercury and too much organic material (plastic etc.). In treatment processes of batteries this might result in
emission problems. They are therefore added as a substream (typically of 5%), and by doing this, the emissions might be diluted.
Processing in steelworks might also result in technical problems, as copper from the batteries can accumulate in the steel and thus destroy the characteristics of the steel. There is some disagreement whether
this is a problem, and it depends to a high extent of the steel quality being manufactured. Finally the degree of recycling is relatively low (20-40%).
There are no steelworks in Denmark able to treat batteries, so with this solution it would be necessary to transport the batteries for treatment abroad. At 1,000-2,000 kilometres of transport, the transport
costs would be app. DKK 500-1,000 per tonne.
Processing in special plants is typically more expensive because the plants are considerably smaller compared to the metal works. The price level is typically between DKK 5,000 and 10,000 per tonne. At
one of the special plants the price is more than DKK 10,000 per tonne.
On the other hand, several of these plants are adapted to treating batteries containing mercury. The organic content of the batteries can be treated and finally the recycling rate is high (50-70%). Apparently
there is a connection between price level and quality, meaning that the most expensive companies in general have the highest environmental standard and degree of recycling.
In table 1, a simple comparison of advantages and disadvantages of processing alkaline manganese batteries and zinc-carbon batteries in metal industries and special plants is shown respectively.
Price |
Environment |
Degree of recycling |
Metal industries |
++ |
(-) |
- |
Special plants |
- |
+ |
+ |
Tabel 1.: Processing of alkaline manganese batteries and zinc-carbon batteries. A simple comparison of advantages (+) and disadvantages (-) in metal industries and special plants is shown respectively.
Because of the comparatively small quantity of alkaline manganese batteries and zinc-carbon batteries to collect in Denmark, the best solution for these batteries is:
- Pre-treatment/detoxication of the batteries in Danish plants
- Final processing abroad
Pre-treatment of alkaline manganese batteries and zinc-carbon batteries can be a pyrolysis or incineration of the batteries in a separate process, during which plastic, possible mercury, cadmium and lead are
removed from the batteries. Then the batteries are “detoxicated” and can be used anywhere in the metal industries without environmental problems. The problem with this method is, however, the low degree
of recycling at 20-40%. If a higher degree of recycling is requested, it is necessary to subdivide the batteries after detoxication, separate the material in fractions and send these to specialized processing
companies. In this way a rate of recycling of up to 70% can be obtained.
In phase 2 in this project, the possibilities of pre-treating alkaline manganese batteries and zinc-carbon batteries are further examined by making practical tests with pyrolysis at a pilot plant at Kommunekemi.
Overall, a Danish treatment model might look as follows:
- Collection of all batteries
- Separation into types at a centrally located separation plant
- NiCd, NiMH and lithium batteries and button cells etc. are sent for processing abroad due to the small quantity
- Alkaline manganese batteries and zinc-carbon batteries are pretreated/”detoxicated” at a plant in Denmark, after which final processing will take place at plants abroad.
1 Indledning
1.1 Formål
Fase 1: Formålet har været teknisk og økonomisk at beskrive de behandlingsmetoder der i dag eksisterer for forskellige batterityper. Dog med speciel fokus på alkali- og brunstensbatterier. På baggrund
heraf er det vurderet, hvilke metoder der er de mest egnede til batterier indsamlet i Danmark.
Fase 2: Formålet har været at afprøve en metode til forbehandling af alkali- og brunstensbatterier i et pilotanlæg.
Projektet er afgrænset til at indeholde en vurdering af sorterings- og behandlingsteknikker, mens selve indsamlingen af batterierne ikke er vurderet.
1.2 Baggrund
Salget af tørbatterier i Danmark er 2.500 - 3.000 tons pr. år, hvoraf 80-90% er brunstens- og alkalibatterier. Alkaliske batterier har tidligere været tilsat op til 1% kviksølv, men de fleste producenter
benytter i dag ikke kviksølv i disse batterier, og fra 2000 er det blevet forbudt i Danmark at sælge alkali- og brunstensbatterier med et kviksølvindhold på over 5 ppm.
Dette betyder at alkaliske batterier, batterier uden kviksølv samt brunstensbatterier ikke længere betragtes som farligt affald, og derfor ikke skal indsamles særskilt. Derimod skal de miljøfarlige batterier som
f.eks. nikkel-cadmium og kviksølvholdige batterier stadig indsamles og behandles.
Det har imidlertid vist sig vanskeligt for den almindelige forbruger, at skelne mellem miljøfarlige og ikke miljøfarlige batterier, hvilket kan bevirke, at mange af de miljøfarlige batterier ikke udsorteres, men
ender sammen med dagrenovationen.
Det kan derfor være hensigtsmæssigt at etablere en obligatorisk indsamlingsordning for alle batterier. Herefter kan batterierne sorteres centralt, og de farlige batterier kan sendes til oparbejdning. Imidlertid
bliver der en meget stor restfraktion (80-90%), der især består af alkali- og brunstensbatterier, der indeholder ressourcer som zink, mangan og jern. Det er ønskeligt at oparbejde denne fraktion også, men
der har ikke umiddelbart været kendskab til en metode der, både miljømæssigt og økonomisk, har været attraktiv.
Nærværende projekt indeholder en beskrivelse af de teknikker der er til rådighed ved behandling af forskellige batterityper, og en nærmere beskrivelse af de teknikker, der er kendskab til ved behandling af
brunstens- og alkalibatterier. Endelig udføres der praktiske forsøg med behandling af alkali- og brunstensbatterier. Der har været fokuseret mest på alkali- og brunstensbatterier, fordi disse udgør langt den
største andel af de batterier der sælges i Danmark, og fordi der har manglet viden om behandlingsmuligheder for netop disse typer.
Resultaterne kan således danne baggrund for udarbejdelse af regler for en eventuel separat indsamlingsordning for batterier.
2 De forskellige batterityper
Fælles for alle batterityper er, at de er opbygget af én eller flere elektrokemiske celler, der indeholder aktive materialer, hvis kemiske energi omdannes til elektrisk energi ved hjælp af en redoxreaktion. Ved
afladning bevæger positive ioner sig fra én elektrode til en anden inden i batteriet, og for at udligne spændingsforskellen løber elektroner samtidigt fra den ene elektrode til den anden i en ekstern strømkreds.
De to elektroder er henholdsvis anoden (-), der bliver oxideret, og katoden (+), der bliver reduceret. Mediet der leder ionerne inden i batteriet kaldes elektrolytten.
Batterier opdeles som regel i to overordnede typer: Primærbatterier (engangsbatterier) og sekundærbatterier (genopladelige batterier).
2.1 Primære batterier
I primærbatterier - eller engangsbatterier - er den kemiske energi indbygget i cellen én gang for alle, og cellereaktionen kan kun forløbe i én retning. De mest almindelige primære batterier er alkaliske og
brunstensbatterier eller husholdningsbatterier, som disse typer også kaldes. Derudover er de mest anvendte lithiumbatterier og knapcellebatterier.
2.1.1 Brunstensbatterier
Hylstret, der også fungerer som anode, består af zink (se figur 2.1). Katoden består af en blanding af MnO2 (brunsten), carbon samt en binder, der holder sammen på blandingen. Elektrolytten er en vandig
opløsning af enten ZnCl2 eller NH4Cl. Centralt er placeret en kulstav, der fungerer som strømsamler. Derudover vil der være et lille indhold af andre metaller, plastik, pap og urenheder. Tidligere indeholdt
brunstensbatterier op til 100 ppm kviksølv, men i dag er det højst tilladte indhold 5 ppm (se afsnit 3.1.3).
Figur 2.2 viser fordelingen af indholdsstoffer. Indholdet kan dog variere noget for forskellige mærker, og efter hvornår batterierne er produceret. Den angivne fordeling skal derfor tages som udtryk for et
omtrentligt gennemsnit. Det ses at de væsentligste indholdsstoffer er mangandioxid, zink og jern.
Brunstensbatterier anvendes i lomme- og cykellygter, radioer, legetøj m.v.
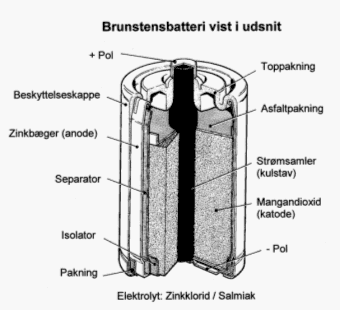
Figur 2.1. Skematisk opbygning af brunstensbatteri /1/
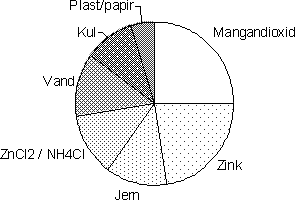
Figur 2.2. Brunstensbatteri. Gennemsnitlig fordeling af væsentlige indholdsstoffer /2/, /3/, /4/, /5/.
2.1.2 Alkaliske batterier
Hylstret består af stål og fungerer ikke som anode, og alkaliske batterier er i forhold til brunstensbatterier opbygget omvendt (se figur 2.3). Katoden består af et rør af sammenpresset MnO2, mens anoden
er placeret i midten, og er en blanding af zinkpulver og elektrolyt, der oftest er vandig KOH. Katoden består af zinkpulver og en messingstav (kobber-zink legering), der fungerer som strømsamler.
Derudover er der som ved brunstensbatterier også indhold af andre metaller, plastik, pap og urenheder. Alkaliske batterier var tidligere tilsat op til 10.000 ppm kviksølv, men må i dag ligesom
brunstensbatterierne ikke indeholde over 5 ppm.
Alkaliske batterier er kendetegnet ved en høj energitæthed og giver en lang driftstid ved kontinuerlig anvendelse i strømkrævende udstyr. Sammenlignet med brunstensbatterier har det også bedre
lavtemperaturegenskaber.
Figur 2.4 viser fordelingen af indholdsstoffer i alkaliske batterier. Indholdet kan dog variere noget for forskellige mærker og efter hvornår batterierne er produceret. Den angivne fordeling skal derfor tages
som udtryk for et omtrentligt gennemsnit. Det ses, som ved brunstensbatterier, at de væsentligste indholdsstoffer er mangandioxid, zink og jern.
De alkaliske batterier anvendes samme steder som brunstensbatterierne, men især i strømkrævende udstyr som f.eks. bærbare båndoptagere og cd-afspillere, kameraer m.v.
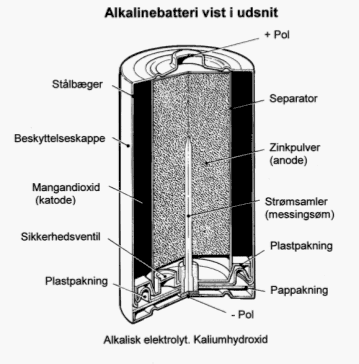
Figur 2.3. Alkalisk batteri /1/
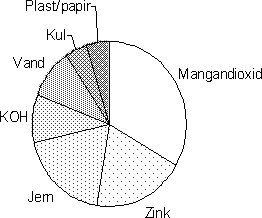
Figur 2.4. Alkalisk batteri. Gennemsnitlig fordeling af væsentligste indholdsstoffer /2/, /3/, /4/, /5/, /6/, /7/
2.1.3 Lithiumbatterier
I primære lithiumbatterier består anoden af lithium mens katoden kan bestå af uopløselige, faste forbindelser (f.eks. MnO2, FeS2 eller polycarbonfluorider), opløselige forbindelser (SO2) eller flydende
forbindelser (f.eks. SOCl2).
Elektrolytten er som regel lithiumsalte opløst i organiske opløsningsmidler.
Batterierne fremstilles både som knapceller og som cylindriske celler (se figur 2.5).
I figur 2.6 er angivet et eksempel på indholdet af stoffer i et lithiumbatteri med MnO2 som katode. Bemærk at de væsentligste indholdsstoffer er jern og MnO2, mens lithium kun udgør en mindre del.
Lithiumbatterierne er kendetegnet ved en høj energitæthed, og anvendes fortrinsvis i fotoudstyr, lommeregnere og lignende produkter med forholdsvis stort strømforbrug.
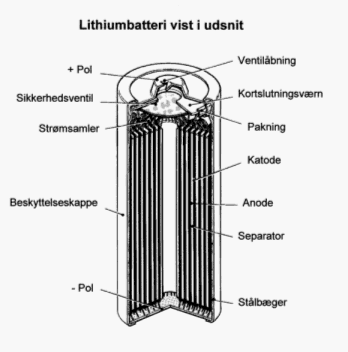
Figur 2.5. Cylindrisk lithiumbatteri /1/.
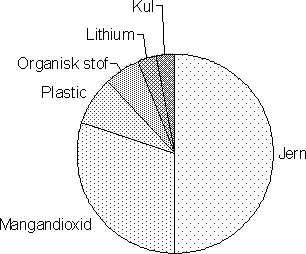
Figur 2.6. Lithiumbatteri. Eksempel på fordeling af indholdsstoffer i lithium-MnO2 type /2/
2.1.4 Knapceller
På grund af den store udvikling på markedet for miniature-elektronik, har knapcellebatterier fået en øget anvendelse. Knapcellerne er kendetegnet ved at være små, flade batterier på størrelse med knapper.
Knapcellerne findes i følgende kemiske systemer:
- kviksølvoxid. Den negative elektrode består af sintret zinkpulver og den positive elektrode af presset kviksølvoxid. Elektrolytten er kaliumhydroxid. Spændingen er meget konstant under afladningen.
Anvendes i fotografiapparater, pacemakere, høreapparater m.v.
- sølvoxid. Ligner kviksølvoxid cellen, men kviksølvoxid er erstattet af sølvoxiderne AgO eller AgO2. Indeholder desuden op til 2% kviksølv. Er på grund af sølvindholdet forholdsvis dyre at fremstille.
Anvendes i armbåndsure, høreapparater m.v.
- zink-luft. Den negative elektrode består af sintret zinkpulver. Elektrolytten er kaliumhydroxid, mens den positive elektrode består af aktivt kul, der optager og udnytter luftens ilt til oxidationsprocessen.
Anvendes meget i høreapparater.
Derudover findes der også alkaliske og lithium baserede knapceller.
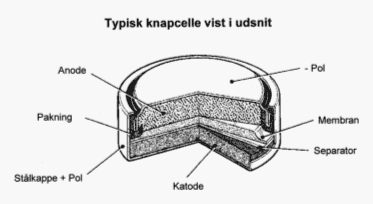
Figur 2.7. Opbygning af typisk knapcelle /1/
2.2 Sekundære batterier
I sekundære eller genopladelige batterier kan celleraktionen forløbe i begge retninger, hvorfor disse batterier kan tilføres energi fra en ekstern strømkilde således at de genoplades. De mest anvendte
systemer er blybatterier, nikkel-cadmium batterier, nikkel-metalhydrid batterier og lithiumbatterier.
2.2.1 Blybatterier/blyakkumulatorer
Blybatteriet eller blyakkumulatorer findes i mange versioner lige fra de velkendte startbatterier i biler, over traktionsbatterier i elektriske køretøjer til meget store stationære batterier i nødstrømsanlæg på
adskillige tusinde amperetimer.
I det opladede blybatteri udgør rent bly den negative elektrode og blyoverilte den positive. Under afladning omdannes begge elektroder til blysulfat. Elektrolytten, der er svovlsyre, indgår i den kemiske
proces, således at syrekoncentrationen falder under afladning. Blybatterier er kendetegnet ved lav energitæthed.
Langt den største anvendelse er som startbatteri i biler og motorcykler, men herudover anvendes de også til fritidsbrug i både, campingvogne m.v. Traktionsbatterier anvendes primært i elektriske
gaffeltrucks, mens de stationære batterier oftest benyttes som nødstrømsanlæg i forbindelse med f.eks. fyrtårne, telefoncentraler, sygehuse m.v.
2.2.2 Nikkel-cadmium batterier
I et opladet nikkel-cadmium batteri (NiCd-batteri) består den negative elektrode af rent cadmium og den positive elektrode af nikkeloxid. Elektrolytten består af en vandig opløsning af kaliumhydroxid, der
ikke indgår i den elektrokemiske reaktion.
Man skelner mellem åbne og lukkede NiCd-batterier. De åbne er store batterier, hvor det er muligt at aftappe elektrolytten, mens de lukkede er mindre hermetisk forseglede batterier.
Lukkede NiCd-batterier var de første genopladelige batterier, der kunne anvendes i transportable apparater (se figur 2.8). NiCd-batterier i samme størrelser som brunstens- og alkalibatterier erstattede
derfor i mange tilfælde disse, ligesom NiCd-batterierne blev anvendt i mobiltelefoner, bærbare computere, videokameraer, husholdningsapparater og håndholdt værktøj. Andre genopladelige batterityper har
dog efterhånden erstattet NiCd-batterierne. En undtagelse er dog i håndværktøj og lignende, og dette skyldes at NiCd-batterier har gode højbelastningsegenskaber og er relativt kuldestabile.
Åbne NiCd-batterier anvendes typisk hvor blyakkumulatorer er blevet vurderet til at aflade for hurtigt og til ikke at have tilstrækkelig kapacitet. Dette er specielt som nødstrømsanlæg på sygehuse, store
trafikanlæg m.v. samt i startmotorer i tog og fly. Endvidere anvendes de åbne NiCd-batterier i el-biler.
I figur 2.9 er vist et eksempel på det typiske indhold af stoffer i et Nikkel-cadmium batteri. Som det fremgår, er de væsentligste indholdsstoffer jern, nikkel og cadmium.
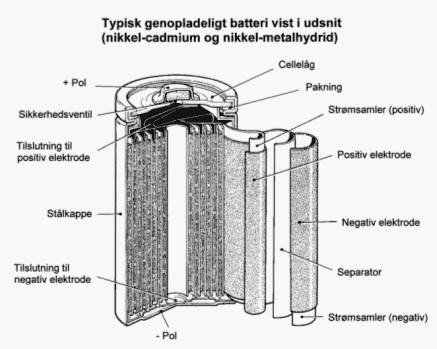
Figur 2.8. Genopladeligt batteri af cylindrisk type /1/
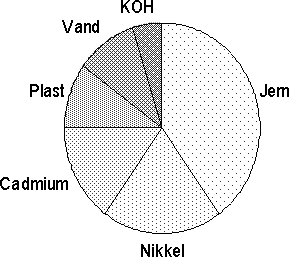
Figur 2.9. Eksempel på fordelingen af indholdsstoffer i Nikkel-cadmium batteri /2/, /3/, /8/
2.2.3 Nikkel-metalhydrid batterier
I nikkel-metalhydrid batteriet (NiMH-batteriet) består den positive elektrode, som i NiCd-batteriet, af nikkeloxid og elektrolytten af kaliumhydroxid.
Derimod er cadmium erstattet af en stang af en metallegering, der kan optage lagre og afgive brint af elektrokemisk vej. Opbygningen af den cylindriske type er vist i figur 2.8 mens opbygningen af et
flercellebatteri er vist i figur 2.10.
I figur 2.11 er vist et eksempel på fordelingen af indholdsstoffer, og det ses at de væsentligste er nikkel og jern.
NiMH-batterier har en høj energitæthed, og giver op til 50% længere driftstid end tilsvarende NiCd-typer. Endvidere har de ikke samme "memory-effekt" som NiCd-batterier, hvilket betyder at de nemmere
kan oplades uden at tage skade. Endelig indeholder NiMH-batteriet ikke det miljøskadelige cadmium, og det er derfor blevet et naturligt miljømæssigt alternativ til erstatning af NiCd-batterier i
mobiltelefoner, bærbare computere, videokameraer m.v.
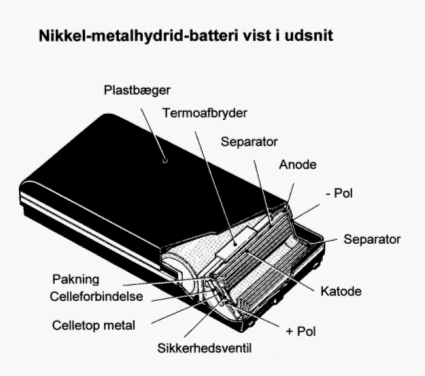
Figur 2.10. Opbygningen af flercelle Nikkel-metalhydrid batteri /1/
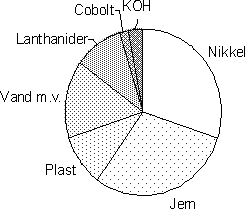
Figur 2.11. Eksempel på indholdet af stoffer i nikkelmetalhydrid batteri /8/
2.2.4 Lithium-ion batterier
Den nyeste anvendte teknologi inden for genopladelige batterier er lithium-ion batterier. Den negative elektrode består af kulstof og en strømsamler af kobber, mens den positive elektrode består af lagdelt
lithium-metaloxid og en strømsamler af aluminium. Metallet kan f.eks. være kobolt, nikkel eller mangan. Elektrolytten er en opløsning af lithiumsalt i blandinger af organiske opløsningsmidler.
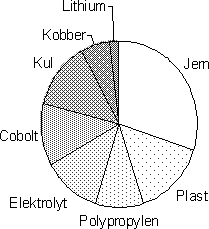
Figur 2.12. Eksempel på indholdet af stoffer i et lithiumbatteri med stålhylster /8/
Lithium-ion polymer batterier. Den seneste udvikling inden for lithium-batterier er lithium-ion polymer batterierne. Her er den flydende elektrolyt erstattet af en ion-ledende fast membran. Dette har bl.a.
den fordel, at man kan lave batterierne meget tynde og fleksible.
Lithium-ion batterier er det genopladelige batteri, der har den største energitæthed, og er derfor særlig velegnet til at strømforsyne bærbart udstyr, hvor laveste vægt/volumen og længst mulige driftstid ønskes,
f.eks. i mobiltelefoner, bærbare computere etc.
2.3 Kviksølv i brunstens- og alkalibatterier
På grund af den elektrokemiske proces sker der en udvikling af gas (brint) under udladningen af et zinkbaseret batteri. Hvis gasudviklingen sker ukontrolleret kan det være årsag til, at batteriet selvudlades
eller lækker. Tidligere tilsatte man kviksølv for at reducere og kontrollere denne gasudvikling, men overgangen til en ny batterikonstruktion med f.eks. en såkaldt "expanded can" muliggjorde fremstilling af
alkaliske batterier uden tilsætning af kviksølv og uden at give afkald på driftssikkerheden.
Før 1985 indeholdt alkaliske batterier således op til 10.000 ppm kviksølv, mens brunstensbatterier indeholdt op til 100 ppm kviksølv. På det tidspunkt igangsatte den europæiske batteri forening (EPBA) et
program for at nedsætte indholdet af kviksølv i batterier, og siden 1994 har EPBA's medlemmer udelukkende solgt såkaldte kviksølvfrie brunstens- og alkalibatterier i Europa /9/. Det vil i praksis sige, at
batterierne maksimalt indeholder 5 ppm kviksølv, da kviksølv kan optræde som urenhed i råvarerne. EPBA organiserer alle de væsentligste producenter af brunstens- og alkalibatterier i Europa, men da det
indtil 1. januar 2000, med visse undtagelser, var tilladt at importere og sælge alkalibatterier med op til 250 ppm kviksølv til EU-landene, kan en del importerede batterier fra før denne dato stadig indeholde
op til 250 ppm kviksølv.
1. januar 2000 blev det, som følge af et EU-direktiv, forbudt at importere og sælge alkaliske batterier med over 5 ppm kviksølv.
3 Status for batteriområdet i Danmark
3.1 Lovgivning og særlige ordninger
Indsamlingen af batterier reguleres af Affaldsbekendtgørelsen /10/. I listen over affald i bekendtgørelsen er batterier anført under:
16 06 00 |
Batterier og akkumulatorer |
16 06 01 00 |
fa |
Blyakkumulatorer |
16 06 02 00 |
fa |
NiCd batterier |
16 06 03 00 |
fa |
Kviksølv tørcellebatterier |
16 06 04 00 |
|
Alkaliske batterier |
16 06 05 00 |
|
Andre batterier og akkumulatorer |
16 06 06 00 |
fa |
Elektrolyt fra batterier og akkumulatorer |
NiCd-batterier, blyakkumulatorer og lithiumbatterier samt usorterede batterier klassificeres som farligt affald (fa), mens rene fraktioner af ikke tungmetalholdige batterier generelt ikke er farligt affald /11/.
Kviksølvfrie alkaliske og brunstensbatterier er således ikke farligt affald, og skal derfor ikke indsamles særskilt, men kan principielt bortskaffes via dagrenovationen. Miljøstyrelsen anbefaler dog, at man
afleverer batterierne til den kommunale indsamlingsordning, hvis man er i tvivl om batterierne indeholder farlige stoffer /12/.
For blyakkumulatorer og NiCd-batterier er der etableret særlige indsamlingsordninger.
3.1.1 Blyakkumulatorer
Indsamlingen af blyakkumulatorer er sikret gennem en aftale fra 1996 mellem miljøministeren og branchen, repræsenteret ved Foreningen til indsamling af blyakkumulatorer i Danmark, ReturBat.
Aftalen forpligter ReturBat til at indsamle alle blyakkumulatorer i Danmark, og den er suppleret af to bekendtgørelser, hvor den ene fastlægger betingelserne for indsamling og genanvendelse af
blyakkumulatorer /13/, mens den anden danner det finansielle grundlag /14/.
Ved denne aftale har ReturBat påtaget sig at forestå driften af ordningen, hvilket bl.a. indebærer registrering af indsamlere, der opfylder kravene i bekendtgørelsen, afregning og kontrol af tilskud til
indsamlere, beregning af indsamlingsprocent samt informationskampagner. Der ydes i henhold til bekendtgørelsen et tilskud på maksimalt 0,90 kr. pr. kg til indsamlere, der afleverer brugte akkumulatorer til
godkendte genanvendelsesanlæg.
Ordningen er finansieret ved et gebyr, der pålægges blyakkumulatorer, der fremstilles i eller importeres til Danmark.
Gebyret er for blyakkumulatorer:
indtil 100 Ah (personbilstyper) |
6 kr. pr. stk. |
over 100 Ah (lastbiltyper) |
12 kr. pr. stk. |
Andre |
9 kr. pr. kWh |
ReturBat får på baggrund af et godkendt budget overført midlerne fra Miljøstyrelsen til udbetaling af tilskud.
3.1.2 NiCd-batterier
I Danmark har der over en længere årrække været særlige indsamlingsordninger for NiCd-batterier. I starten af 90'erne og frem til 1995 blev indsamlingen varetaget på brancheinitiativ af Foreningen for
indsamling af genopladelige batterier.
I 1995 indførte Danmark en miljøafgift på lukkede NiCd-batterier /15, 17/, og afgiften føres tilbage gennem en godtgørelse for indsamlingen og genanvendelse af brugte NiCd-batterier /16, 18/.
Miljøstyrelsen overtog organiseringen og administrationen af ordningen, og formålet var at fremme indsamlingen og oparbejdning af NiCd-batterier. For at etablere sig som indsamlingsvirksomhed, skal man
registreres hos Miljøstyrelsen.
Afgiften udgør 6 kr. pr. stk. for løse celler og 36 kr. pr. pakke for sammenbyggede celler, mens godtgørelsen udgør 150 kr. pr. kg indsamlede NiCd-batterier, der afleveres til godkendt
genanvendelsesanlæg. Der er i perioden 2000-2001 budgetteret med 25,7 mio. kr. årligt /19/.
3.2 EU-direktiv
I 1999 udarbejdede EU et udkast til et direktivforslag vedrørende indsamling og behandling af alle batterier og akkumulatorer /30/. På grund af forskellige indvendinger mod udkastet har Kommissionen
imidlertid iværksat en udarbejdelse af et nyt udkast, men der foreligger på nuværende tidspunkt ikke noget om indholdet i dette.
3.3 Forbruget af batterier i Danmark
3.3.1 Primære batterier
Batteriforeningen i Danmark har opgivet, at der årligt bruges i alt ca. 77.000.000 stk. eller ca. 2.500 tons primære batterier i Danmark /1/.
Fordelingen på typer er angivet i tabel 3.1.
Type |
Antal stk. |
Vægt i tons |
Brunsten |
21.000.000 |
1.123 |
Alkaline |
42.000.000 |
1.297 |
Knapceller |
13.000.000 |
16 |
Foto-Lithium |
566.000 |
11 |
Lithium |
461.000 |
1 |
I alt |
77.000.000 |
2.449 |
Tabel 3.1. Forbrug af primære batterier i 2001 i Danmark /1/
Batteriforeningen anslår at 87% anvendes i husholdningerne mens 13% anvendes af virksomheder.
Mængderne kan være svære at anslå, da der sker import af en del batterier indsat i produkter. Disse batterier registreres ikke i importstatistikkerne.
3.3.2 Sekundære batterier
Forsyningen af åbne NiCd-batterier var i perioden 1995-1997 ca. 30 tons pr. år /20/.
Forbruget af lukkede NiCd-batterier er for 1996 skønnet til 218 - 328 tons /20/.
Forbruget af blyakkumulatorer er 15. - 16.000 tons pr. år /21/.
Det har ikke været muligt at skaffe oplysninger om forbruget af NiMH og lithiumbatterier.
3.4 Bortskaffede og indsamlede mængder i Danmark
I forbindelse med et indsamlingssystem er det ikke så vanskeligt at opbygge et system til registrering af den indsamlede mængde for de enkelte batterityper. Det vanskelige består i at vurdere
indsamlingsprocenten, hvilket er et mål for indsamlingssystemets effektivitet, og dermed et mål for hvor mange batterier, der bortskaffes uden om systemet.
Indsamlingsprocenten kan helt simpelt beregnes ved at tage forbruget af batterier i et bestemt år, vurdere middel-levetiden for disse batterier og sammenligne den forbrugte mængde med den indsamlede
mængde i året hvor batterierne er udtjente. Imidlertid skal der også tages hensyn til, hvad der kaldes "pulterkammereffekten" og "pipelineeffekten". Pulterkammereffekten er et udtryk for, at der er en tendens
til, at udtjente batterier opbevares et stykke tid inden de afleveres. Dette er især udtalt for husholdningsbatterier. Pipelineeffekten er den tid som batterierne er i indsamlingssystemet inden de registreres. Det
kan eksempelvis være tiden inden en boks til indsamling tømmes, opbevaring på mellemlager etc.
Middellevetiden, pulterkammereffekten og pipelineeffekten er størrelser, som det er meget vanskelig at beregne eksakt. Derfor bliver den beregnede indsamlingsprocent heller ikke eksakt, men et tal
behæftet med nogen usikkerhed.
Batterier er i Danmark blevet indsamlet på frivillig basis siden begyndelsen af 70'erne, men kommunerne har siden 1990 været forpligtiget til at indsamle de batterityper, der klassificeres som farlige. Dvs.
batterier med kviksølv, NiCd-batterier, blyakkumulatorer, lithiumbatterier og usorterede batterier. Rene fraktioner af f.eks. ikke tungmetalholdige batterier klassificeres ikke som farligt affald, og skal derfor
ikke indsamles separat.
I praksis betyder det, at der i de enkelte kommuner er etableret forskellige indsamlingsordninger. F.eks. ved opstilling af indsamlingsbokse i forretninger, skoler m.v., husstandsindsamling med miljøbiler,
indsamling på genbrugspladser og lignende.
Med det nuværende system er indsamlingsraten vurderet til omkring 50%, hvilket Miljøstyrelsen vurderer ikke er tilstrækkeligt /37/.
Fra de indsamlede batterier udsorteres manuelt, af både private og kommunale affaldsfirmaer, blybatterier, NiCd-batterier, NiMH-batterier og knapceller til genanvendelse. Lithium-batterier udsorteres til
enten genanvendelse eller forbrænding/deponering. Den resterende fraktion, som herefter er en blanding af alkaliske og brunstensbatterier er stadig klassificeret som farligt affald, med mindre kviksølvholdige
alkalibatterier er sorteret fra. Dette lader sig dog vanskeligt gøre ved en manuel sortering. Alternativt kan batterierne sorteres i en alkali- og en brunstensfraktion, og herefter er det kun alkalifraktionen der
klassificeres som farligt affald. Brunstensfraktionen kan derfor deponeres på almindelige kontrollerede lossepladser.
Eneste slutmodtager i Danmark til blandede alkali- og brunstensbatterier samt alkalibatterier, der ikke er garanteret kviksølvfrie, er Kommunekemi a/s, hvor batterierne indstøbes i beton og deponeres på
specialdeponi. Alternativt skal batterierne eksporteres til oparbejdning i udlandet, men på grund af prisniveauet har denne mulighed dog ikke hidtil været brugt.
Kommunekemi har de seneste år modtaget følgende mængder:
|
1999 |
2000 |
Blandede batterier (alle typer) |
63 |
52 tons |
Blandede alkali/brunstensbatterier |
123 |
84 tons |
I forhold til en indsamlingsrate på 50% samt det samlede forbrug på ca. 1.300 tons alkali- og ca. 1.100 tons brunstensbatterier pr. år, er det således kun relativt beskedne mængder Kommunekemi
modtager.
Der kan være flere mulige forklaringer på dette:
- Indsamlingsraten er betydeligt mindre end 50%. Hvis raten var 50% skulle Kommunekemi modtage alene omkring 650 tons alkalibatterier om året til specialdeponering.
- Kviksølvholdige alkalibatterier frasorteres. De resterende alkalibatterier deponeres sammen med brunstensbatterierne på almindelige kontrollerede lossepladser, og kun de kviksølvholdige alkalibatterier
sendes til Kommunekemi.
- Usorterede alkalibatterier deponeres sammen med brunstensbatterier på almindelige kontrollerede lossepladser.
Det må antages, at praktisk taget alle de batterier der ikke indsamles, bortskaffes via dagrenovationen. De forbrændes således sammen med det øvrige husholdningsaffald på forbrændingsanlæggene.
Kviksølv, cadmium, bly og zink fra batterierne vil fordampe og belaste forbrændingsanlæggenes røggasrensningsanlæg, ligesom ressourcerne i batterierne vil gå tabt.
Regnes eksempelvis med at 50% af alkali-/brunstensbatterierne ender i forbrændingsanlæggene betyder det, at omkring 1.200 tons brunstens-/alkalibatterier forbrændes pr. år. Dette medfører en årlig
belastning af forbrændingsanlæggenes røggasrensningsanlæg med 240 tons zink, mens 120 tons jern og 300 tons mangan ender i slaggen.
Da vi ikke har ét system for indsamling af alle batterityper I Danmark, findes der ikke samlede opgørelser over hvor mange brunstens- og alkalibatterier der totalt indsamles om året, og det er derfor meget
vanskeligt at vurdere indsamlingsraten.
For bly- og NiCd-batterier, hvor der eksisterer specielle ordninger findes der dog data.
Blyakkumulatorer
I perioden fra 1994 til 1999 er der årligt blevet indsamlet 14.000 -15.300 tons blyakkumulatorer, og i 2000 blev der indsamlet ca. 15.600 tons /22/.
Indsamlingsprocenten er tæt på 100% /21/.
NiCd-batterier
I 1998 blev der indsamlet ca. 80 tons NiCd-batterier til genanvendelse, hvilket svarer til mindst 40% af de udtjente batterier. Den resterende batterimængde på et sted mellem 0 og 90 tons, svarende til 0 -
14 tons cadmium, vurderes at være bortskaffet via dagrenovationen til forbrænding/deponering /20/.
Miljøstyrelsen vurderer, at indsamlingsraten i 1998 har været ca. 70%, men anfører, at værdien er behæftet med nogen usikkerhed på grund af ”pulterkammer-” og ”pipelineeffekten” samt det øgede forbrug
af NiCd-batterier fra først i 90'erne /24/.
3.5 Udviklingstendenser
3.5.1 Primære batterier
Der er i øjeblikket ikke noget der tyder på, at forbrugsmønstret for de primære batterier vil ændre sig markant i forhold til det nuværende. Flere år fremover må det derfor forventes, at brunstens- og
alkalibatterier vil udgøre langt den overvejende del af de primære batterier der anvendes. Der er heller ikke noget der tyder på, at der i nær fremtid vil forsvinde eller opstå nye anvendelsesområder i forhold
til de nuværende, hvorfor den anvendte mængde også må forventes at holde sig nogenlunde konstant.
3.5.2 Sekundære batterier
Forbruget af små, sekundære batterier er gennem de seneste 5 år steget markant på grund af den øgede brug af bærbar elektronik, ligesom de typer af små, sekundære batterier der har været anvendt, har
ændret sig markant. Det forventes dog, at det samlede forbrug af små, sekundære batterier vil være relativt konstant over de næste 10 år, men de typer af batterier der anvendes vil ændre sig yderligere /23/.
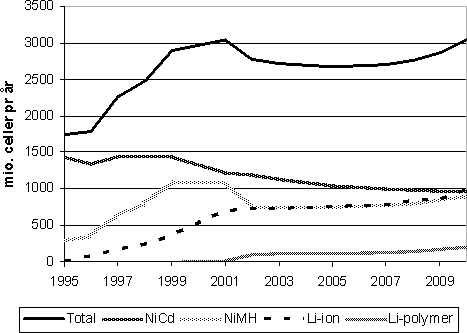
Figur 3.1. Den forventede markedsudvikling på verdensplan for små genopladelige batterier. Efter /23/
For bare 5 år siden var NiCd-batterierne det altdominerende genopladelige batteri, men i dag er der flere forskellige typer på markedet.
Gennem de senere år er der på verdensplan sket en stor stigning i anvendelsen af NiMH-batterier, således at disse til mange anvendelser, som f.eks. bærbare elektroniske apparater, har fortrængt
NiCd-batterier. Dette kan især tilskrives NiMH-batteriernes større energitæthed i forhold til NiCd-batterierne, samt de bedre miljøegenskaber fordi de ikke indeholder cadmium.
I Danmark er forbruget af NiCd-batterier ca. halveret fra 1995 til 2001, hvilket ses af at der i 1995 kom 45 mio. kr. ind fra afgifter, mens der i 2001 kun kom 20 mio. kr. ind /24/. Dette fald i forbruget kan
både tilskrives den tekniske udvikling og indførelsen af afgiften på NiCd-batterier i 1995.
Til trods for at der praktisk taget ikke mere anvendes NiCd-batterier til nyt elektronisk udstyr har forbruget af NiCd-batterier dog kun været svagt faldende. Det kan sandsynligvis tilskrives den øgede brug
af batteridrevet håndværktøj, hvor NiCd-batterier er de mest egnede i dag.
Hvis der på EU-plan gennemføres et forbud mod cadmium i batterier, vil dette naturligvis betyde et voldsomt fald i brugen af NiCd-batterier, og en stigning i de øvrige typer.
Lithiumbatterier har endnu større energitæthed end NiMH-batterier. Lithium-ion batteriet har gennem de seneste 5 år i stigende udstrækning været anvendt. Ligeledes ses der også en stigende anvendelse af
de nye lithium-polymer batterier.
Fremover må man derfor forvente et faldende forbrug af NiCd-batterier - måske til nul, et uændret eller måske faldende forbrug af NiMH-batterier, og et stigende forbrug af lihiumbatterier.
3.5.3 Brændselsceller
Brændselsceller er en energikilde, der arbejdes en del på at udvikle i dag. De bygger på et helt andet princip end batterier, men kan på samme måde som batterier anvendes som strømforsyning.
Brændselscellen er dog ikke i dag færdigudviklet til at kunne anvendes, hvor vi i dag anvender små batterier, men på længere sigt regner man med, at brændselscellen vil kunne erstatte batterier.
En brændselscelle virker som i et batteri ved at kemisk energi omdannes til elektrisk energi. Et batteri opbruges når det producerer el, og et sekundært batteri kan tilføres ny energi fra en ekstern strømkilde.
Den afgørende forskel til en brændselscelle er, at den kan producere el uden pauser så længe den får tilført brændsel i form af brint.
Princippet i en brændselscelle er, at brint, ved hjælp af en katalysator, spaltes i ioner og elektroner. Brintionerne vandrer gennem en membran fra anoden til katoden, mens elektronerne løber gennem en
ekstern strømkreds og producerer således en elektrisk strøm. Ved katoden forbinder brintionerne og elektronerne med atmosfærisk ilt, og der dannes vand.
Brinten, der anvendes som brændsel, kan fremstilles ud fra kulbrinter, f.eks. naturgas, methanol el. lignende i en såkaldt reformator, der kan være bygget sammen med brændselscellen.
Brændselsceller kan bygges op som større energiproducerende anlæg, hvor fordelene skulle være højere virkningsgrader i forhold til konventionelle anlæg, eller som små transportable celler til erstatning for
batterier. Der er dog nogen vej endnu før de små anlæg er færdigudviklet, mens der for de større stationære anlæg allerede findes demoanlæg på op til 5 MW /25/.
4 Kortlægning af eksisterende behandlingsteknologier
I de følgende afsnit er mulighederne for sortering og kendte metoder til oparbejdning af de forskellige batterier beskrevet. Ved oparbejdningsmetoderne er der især fokuseret på alkali- og brunstensbatterier.
4.1 Sortering
De indsamlede batterier vil være en blanding af alle batterityper samt andet affald, som uundgåeligt også vil havne blandt batterierne. I de fleste tilfælde foregår sorteringen af batterierne i typer manuelt, da
det har været vanskeligt at udvikle en teknik der såvel økonomisk som teknisk kan konkurrere med manuel sortering.
Imidlertid har der gennem de senere år flere steder været gennemført udvikling af udstyr til automatisk sortering.
Nye kviksølvfrie alkali- og brunstensbatterier produceret i EU er påført en UV-markør, der betyder at et automatisk sorteringsanlæg let kan genkende disse batterier ved belysning med UV-lys. Det varer
dog en del år endnu før alle de gamle kviksølvholdige batterier er ude af affaldsstrømmen, ligesom man ikke kan være sikker på at batterier importeret til EU er mærket med UV-markør.
4.1.1 Automatisk sortering hos Trienekens AG /26/
Et af de nyeste og mest moderne automatiske sorteringsanlæg i Europa er placeret hos Trienekens AG i Düsseldorf. Anlægget er besøgt i august 2000.
Batterisorteringsanlægget hos Trienekens repræsenterer 3. generation inden for automatiske sorteringsanlæg, og er en videreudvikling af det anlæg, som står hos firmaet S.N.A.M. i Lyon.
Batterierne kommer fra den tyske indsamlingsordning, der administreres af GRS-Batterien. Trienekens AG er et at de 3 tyske firmaer der har kontrakt med GRS-Batterien, og i kontrakten forudsættes det,
at firmaerne etablerer automatiske sorteringsanlæg.
4.1.1.1 Princip
Anlægget består af 2 afsnit: Første afsnit er en manuel/mekanisk sortering og er udviklet af Trienekens selv. Dele af det har de patent på. Andet afsnit er udviklet af Euro Bat Tri, der er et datterselskab af
S.N.A.M, og består af vægt-, Tri-Mag- og UV-sensorer.
Første afsnit.
Anlægget fødes ved at batterierne hældes i en fødekasse med en rist, der tilbageholder store batterier. Herefter kører de ud på et transportbånd, hvor firkantede Ni-Cd, Ni-MeH og lithium batterier samt
militærbatterier og affald sorteres fra manuelt. Dernæst sker der en størrelsessortering på et ristesystem således at knapceller tages fra, og øvrige batterier deles i en strøm med store og små batterier.
Knapcellerne sorteres efter størrelse, i tre fraktioner, i et separat si-system. Størrelsen er specifik for de forskellige typer (zink-kviksølvoxid, zink-sølvoxid og zink-luft), og er således nok til at dele dem i
typer. Virksomheden har to anlæg, hvor bl.a. de kviksølvholdige knapceller destilleres.
De to strømme af de øvrige batterier føres videre til en anordning, hvor flade og firkantede batterier sorteres fra. Dette sker på skråtstillede roterende plader, således at runde batterier ruller af, mens flade
bliver ført med pladen. Det er nødvendigt at fjerne de firkantede og flade batterier her, da de ikke passer ind i teknikken på andet afsnit af anlægget.
Andet afsnit.
Her er der 2 linier til henholdsvis store og små runde batterier. Batterierne transporteres på "polycord belts", en slags runde plastkabler med ½-1½ cm mellemrum, således at batteriet ligger mellem kablerne
og hviler på disse. Dette sikrer at batteriet fastholdes i samme position.
Herefter registreres forskellige parametre for batterierne. Vægten registreres ved at batteriet, ved hjælp af overbånds kabler, løftes og vejes. Vægten lagres i en PLC. Alle batterier over en vis vægt
frasorteres herefter, da de enten indeholder bly eller kviksølv.
Dernæst passerer batterierne en såkaldt Tri-Mag-sensor, hvor der induceres et magnetisk felt i batteriet og detektorceller måler responsen. Dataene lagres ligeledes i PLC'en, og sammenholdt med
vægtregistreringerne kan der skelnes mellem brunstens-, alkali- og NiCd-batterier. NiCd batterier sorteres fra. Til slut passerer brunstens- og alkalibatterierne en UV-sensor, der registrerer eventuelle
UV-markører på batterierne. Nye kviksølvfrie batterier påføres hos de væsentligste producenter i Europa denne UV-markør for at lette sorteringen.
Brunstens og alkalibatteriene sorteres således i fire fraktioner: to garanterede kviksølvfrie alkali- og brunstens-fraktioner og to alkali- og brunstensfraktioner, hvor der kan forekomme kviksølv.
Endelig vil der være en fraktion, der ikke kan genkendes af nogle af systemerne og den udsorteres til sidst i anlægget. I dag er den ca. 2%, men mængden formindskes løbende, idet data for de ikke
genkendelige batterier efterfølgende lægges ind i systemet.
I alt sorteres i 11 fraktioner.
Vægt- og Tri-Mag-sensorerne er den mest kritiske del af systemet med hensyn til nøjagtighed og hastighed, mens UV-sensorerne er langt det hurtigste og mest stabile sensorsystem. Det samlede system kan
detektere 5-8 celler pr. sek.
4.1.1.2 Kvalitet.
Renheden af de enkelte fraktioner er bedre end ved manuel sortering. Med undtagelse af lithiumfraktionen er renheden over 99%. For lithiumfraktionen er den omkring 96%
4.1.1.3 Kapacitet.
Første afsnit: |
10.000 tons/år |
|
Andet afsnit: |
5.000 tons/år |
1 tons/time |
Der regnes med 5 tons/skift
Der regnes med en sortering af 2.500 tons batterier i 2000. Der arbejdes p.t. i 2 skift.
Prisen for sortering er ca. 1,50 kr. pr. kg
4.1.2 Automatisk sortering hos Uni-cyc GmbH (SORBAREC) /35, 36/
Hos firmaet Uni-cyc GmbH i Bremerhaven er der etableret et automatisk sorteringsanlæg kaldet SORBAREC. Anlægget anvender, som det første i verden, røntgen-gennemlysning til at identificere de
forskellige batterityper.
Først er der en manuel indgangskontrol af batterierne, hvor andet affald og store batterier sorteres fra. Herefter sker der en mekanisk sortering efter størrelse på en sigte, så batterierne opdeles i 5 fraktioner.
Knapceller og batterier med en diameter over 35 mm tages fra, mens de øvrige tre fraktioner, der udgør omkring 85%, går videre til røntgen-linien. Her bliver der taget et røntgenbillede, hvor gråtoningen er
forskellig på grund af metallernes forskellige evne til at absorbere røntgenstråler. Yderligere er der en UV-detektor, der kan udsortere kviksølvfrie batterier, der er UV-mærket.
Anlægget har en kapacitet på ca. 1 tons pr. time og kan sortere 12 batterier pr. sekund. Renheden af de sorterede fraktioner angives til at være over 99,75 %.
Prisen for sorteringen er opgivet til 1 - 1,50 kr. pr. kg.
4.2 Behandlingsteknologier
4.2.1 Blybatterier/blyakkumulatorer /21, 22/
Blyakkumulatorer fra biler og lignende indsamles i Danmark af foreningen ReturBat. Praktisk taget alle de indsamlede akkumulatorer behandles hos smelteværket, Boliden Bergsöe i Landskrona.
Akkumulatorerne leveres til smelteværket inklusive syre, og første trin er udtømning af syren. Denne opsamles, renses og neutraliseres, hvorefter den ledes ud i Øresund.
Efter tømning knuses akkumulatorerne, og det sønderdelte materiale blandes med koks og slaggedannerne jern, kalk og sand, hvorefter det hele føres til smelteovnene. Rester af svovlsyre fra de knuste
akkumulatorer bindes til jern i slaggen. Under processen forbrændes alle de organiske materialer, mens blyet smelter og kan aftappes. Herefter raffineres blyet, og anvendes til fremstilling af nye
akkumulatorer.
4.2.2 NiCd-batterier
I Europa er der identificeret 3 firmaer, der så vidt vides behandler alle de NiCd-batterier, der indsamles i Vesteuropa:
S.N.A.M. , Frankrig
SAFT NIFE AB, Oskarshamn, Sverige
ACCUREC GmbH, Tyskland
Disse virksomheder behandler til sammen ca. 8.000 tons NiCd-batterier pr. år, og princippet alle tre virksomheder benytter sig af, er en opvarmning af batterierne, således at cadmium destillerer af.
Industrielle batterier skilles ad og de negative plader, der indeholder cadmium, opvarmes hvorved cadmium fordamper og efterfølgende kondenseres. Små lukkede NiCd-batterier kan pyrolyseres, således
at plast og andet organisk materiale nedbrydes inden destillationen.
Det tilbageblevne stål/nikkelblanding kan herefter videreforarbejdes og anvendes til jern-nikkel legeringer.
4.2.3 NiMH-batterier
NiMH-batterier kan bl.a. behandles hos S.N.A.M. i Frankrig og hos NIREC - Nickel Recycling GmbH i Tyskland.
Hos NIREC sker behandlingen på den måde, at batterierne gennem en vakuumsluse tilføres en shredder, hvor batterierne neddeles under vakuum. Derved frigives der brint, der kontinuerligt fjernes fra
kammeret. Herefter sorteres kunststofdele fra, og tilbage haves et produkt med højt indhold af nikkel. Dette kan efter en yderligere bearbejdning anvendes som legeringsmiddel ved stålfremstilling.
4.2.4 Lithiumbatterier
Lithiumbatterier er forholdsvis nye på markedet og bl.a. derfor, er der ikke så mange oparbejdningsmuligheder i dag.
Et af problemerne ved oparbejdning af primære lithiumbatterier er, at de indeholder metallisk lithium, der kan reagere eksplosivt ved kontakt med fugtig luft. Det amerikanske firma ToxCo, Inc. har derfor
udviklet en metode, hvor både primære og sekundære lithiumbatterier kan oparbejdes, og er i dag verdens største lithiumbatteri-oparbejder i dag.
Ved ToxCo processen nedfryses de primære batterier i flydende nitrogen til -195 °C, hvorved lithiums reaktivitet reduceres meget betydeligt. Herefter neddeles batterierne nedsænket i en opløsning af
kaustisk lithiumhydroxid. Friktionsvarmen gør, at batteridelene tørrer, og lithium vil reagere med den vandige opløsning og bl.a. danne lithiumhydroxid, lithiumsulfater og lithiumcarbonater. Samtidig dannes
der hydrogen, der kontrolleret afbrændes på overfladen af badet. Herefter frasepareres de faste metaldele ligesom plastik og papir, der flyder ovenpå, tages fra. Kulstof og andet slam filtreres ud af
opløsningen, og ved tilsætning af natriumcarbonate udfælder lithiumcarbonat som et hvidt fast stof, der også kan filtreres fra.
Sekundære lithiumbatterier behandles på en tilsvarende måde, men det værdifulde cobalt oparbejdes også fra disse batterier /27/.
I Europa er der kendskab til tre processer til oparbejdning af lithiumbatterier hos:
- AEA Technology Batteries, England
- ACCUREC, Tyskland
- S.N.A.M. Frankrig
Disse teknikker er dog ikke fuldt udviklede til fuldskalaanlæg endnu.
Teknikken udviklet af AEA Technology Batteries bygger på en neddeling af batterierne i en inert tør atmosfære, således at reaktioner med metallisk lithium undgås. Herefter separeres elektrolytten og kan
evt. genanvendes. Elektroderne opløses i det samme opløsningsmiddel som anvendes ved fremstillingen af elektroderne. Herved kan plastik, stål, kobber m.v. tages fra, og de resterende elektrodepartikler er
lithium cobalt oxid og forskellige typer af carbon. Efterfølgende kan cobalt reduceres til cobalt(II)oxid ved elektrolyse hvorved der desuden dannes lithiumhydroxid. Cobalt(II)oxid og kulstof frafiltreres
opløsningen af lithiumhydroxid, og det faste stof separeres i cobalt(II)oxid og kulpulver /28/.
Hos S.N.A.M. behandles sekundære lithiumbatterier i et pilotanlæg ved hjælp af pyrolyse efterfulgt af en neddeling. Fra de neddelte batterier fjernes jern med en magnet, mens kobber og aluminium sigtes fra
den fine fraktion med lithium, cobalt og kul. Fra den fine fraktion kan cobalt efterfølgende oparbejdes /2, 8/.
4.2.5 Knapceller
Kviksølvholdige knapceller kan behandles ved at destillere kviksølv af. Dette gøres som regel ved at anbringe knapceller og evt. andet kviksølvholdigt affald i en destillationsbeholder, som herefter opvarmes.
Derved vil kviksølv fordampe, og dampene kan efterfølgende kondenseres som metallisk kviksølv med en renhedsgrad på over 99,9% Processen er således relativ enkel, men på grund af kviksølvs lave
damptryk og høje giftighed stiller processen høje krav til tætheden af anlægget.
Der findes flere virksomheder i Europa der udfører destillation af kviksølv fra batterier. Som eksempler kan her nævnes:
Batrec, Schweiz
Citron, Frankrig
NQR, Tyskland
Trienekens, Tyskland
4.2.6 Alkali- og brunstensbatterier
I dag, hvor der i Danmark ikke er en obligatorisk ordning, hvor alkali- og brunstensbatterier indsamles separat, bortskaffes langt de fleste af disse via dagrenovationen. Dette betyder at batterierne i stort
omfang ender i husholdningsforbrændingsanlæggene, hvor plast, papir og kul vil forbrændes, mens stål og mangan vil ende i slaggen og zink i flyveasken. Eventuelt kviksølv renses fra i røggasrensningen. Alle
ressourcerne går tabt ved denne løsning.
Hvis alkali- og brunstensbatterier blev indsamlet separat, ville der i dag principielt være tre muligheder for behandling:
- Deponering
- Oparbejdning i metalindustrien
- Oparbejdning i specialanlæg
Deponering er den væsentligste løsning der anvendes i dag for de alkali- og brunstensbatterier der indsamles i Danmark. Batterier uden kviksølv kan deponeres på almindelige kontrollerede lossepladser,
mens kviksølvholdige batterier er farligt affald og skal derfor deponeres på specialdepot.
De alkali- og brunstensbatterier som Kommunekemi modtager deponeres på Kommunekemis specialdepot ved Klintholm, hvor de indstøbes i beton for at immobilisere eventuelt kviksølv.
Ved en oparbejdningsløsning er det muligt at oparbejde batterierne i metalindustrien, hvor de kan indgå som en del af råmaterialet, eller i specialanlæg der er specielt konstrueret til behandling af batterier. I
tabel 4.1 er vist en oversigt over forskellige anlæg og processer der kan anvendes til oparbejdning, og i de følgende afsnit er der nærmere beskrivelse af de enkelte processer.
Genanvendelse
Produkter
Prisniveau for behandling
Metalindustrien
Stålværker
35-40%
Jern og zink genanvendes
Kullet bidrager i stålet eller som brændsel
Mangan går i slaggen
Jern indgår i stålet
Zink i flyveasken, der oparbejdes
Under 5 kr./kg
Waelzovn
20-25 %
Kun zink genanvendes.
Kul forbrændes
Støv med 65% zinkoxid til oparbejdning
Under 5 kr./kg
Zinksmelteovn
20-25 %
Kun zink genanvendes
Zink
(>99,99 % ren)
Under 5 kr./kg
Specialprocesser
Citron
60-70%
Jern, zink og mangan genanvendes
Kul anvendes som reduktionsmiddel/brændsel
Zinkoxidkoncentrat og manganoxid til oparbejdning
Stålskrot til oparbejdning
Kviksølv
5-10 kr./kg
Batrec
60-70%
Jern, zink og mangan genanvendes
Kul anvendes som reduktionsmiddel/brændsel
Ferromangan
Zink (99% ren)
Kviksølv (>99,99%)
Over 10 kr./kg
VALDI
60-70%
Jern, zink og mangan genanvendes
Kul anvendes som reduktionsmiddel/brændsel
Ferromangan
Støv med kviksølv og ca. 80% zinkoxid til oparbejdning
5-10 kr./kg
Ebs
60-70%
Jern, zink og mangan genanvendes
Kul anvendes som brændsel
Støv med jern (10%), zink (40%) og mangan(30%) til oparbejdning
Jernskrot til oparbejdning
5-10 kr./kg
Revatech /Erachem
60-70%
Jern, zink og mangan genanvendes
Stål og zinkskrot til genanvendelse
Pasta med zink og mangan til oparbejdning
?
Euro Dieuze Industrie
50-70%
Zink, mangan og måske jern genanvendes
?
Zimaval Technologies
60-70%
Benytter tilsyneladende samme teknik som Revatech / Erachem
?
Tabel 4.1. Oversigt over kortlagte processer til behandling af alkali- og brunstensbatterier
4.2.6.1 Oparbejdning i metalindustrien
Oparbejdning af alkali- og brunstensbatterier i metalindustrien er en løsning, som især den europæiske batteriorganisation, EPBA mener, bør fremmes. I metalindustrien er der mulighed for oparbejdning i
flere forskellige typer af industrier:
- I lysbueovne (EAF) på stålværker
- I Waelz-ovne til oparbejdning af stålværksstøv med zink
- I zinksmelteovne
- Ved fremstilling af ferromangan
- Ved jernfremstilling i højovne
Batterierne tilsættes som en delstrøm til råmaterialet, og et af problemerne ved dette er, at de kan kontaminere slutproduktet med uønskede stoffer. Ligeledes producerer disse termiske processer store
røggasmængder, og kritikerne fremhæver at eventuelt kviksølv, cadmium eller dannede dioxiner fra batterierne blot fortyndes væk. Der er således både et kvalitets- og miljømæssigt aspekt, der skal tages
højde for.
Ved oparbejdning i metalindustrien stilles der af miljøhensyn generelt krav om at batterierne maksimalt må indeholde 5-20 ppm kviksølv og maksimalt 5% organisk materiale (plastik etc.).
Oparbejdning i stålværker (lysbueovn)
Ved en oparbejdning i stålværkernes lysbueovne tilsættes batterierne sammen med stålskrot. Herved vil jernet i batterierne blive genanvendt i det færdige stål. Zinken vil fordampe og blive oxideret til
zinkoxid, der opsamles i værkets røggasrensningssystem. Mangandioxid kan ikke reduceres i det smeltede stål, men vil i stedet flyde med op i slaggen. Mangandioxid fra batterier kan således ikke erstatte
den mangan der tilsættes ved stålproduktion. Organisk materiale og kul vil forbrændes ved processen.
Zinkstøv fra stålværker sendes som regel til oparbejdning i zinkværker (f.eks. Waelzovne), hvorved der også sker genbrug af zinken fra batterierne. Genanvendelsesprocenten vil således være noget større.
En af de kvalitetsmæssige indvendinger imod at anvende batterier i stålindustrien er batteriernes indhold af kobber, da kobber i stålet har en negativ indflydelse på kvaliteten. Hvorvidt stålværkerne kan
modtage batterier afhænger altså af hvilken stålkvalitet der fremstilles på de enkelte stålværker.
Miljømæssigt har det været anført, at der til trods for forbuddet mod et indhold af kviksølv på mere end 5 ppm i batterier, der fremstilles eller importeres til EU, stadig vil forekomme kviksølvholdige batterier
i affaldsstrømmen. Stålværkerne har normalt ikke udstyr til at rense afkastluften for kviksølv, men på grund af de store luftmængder vil der ske en fortynding af denne kviksølvmængde, således at mængden
der udledes vil synes meget lille. Cadmium fra NiCd-batterier der fejlagtigt ikke er sorteret fra, vil ligeledes emitteres.
Endelig har det været anført, at batteriernes indhold af organisk materiale kan være en kilde til dioxindannelse i stålværkerne.
Eksempler på stålværker i Europa der i dag har godkendelser og modtager batterier er:
- Nedstaal B.V., Holland
- Nervacero S.A., Spanien
- ASW Sherness Steel Ltd., England (kun test)
Waelz-ovn
Waelz-ovne benyttes især til oparbejdning af zinkholdigt støv fra stålværker, men processen kan også anvendes til andet zinkholdigt affald som batterier.
Waelz-processen går i korte træk ud på at opkoncentrere zinken ved at fordampe og oxidere zinken i affaldet og efterfølgende fange det zinkholdige støv i et filter.
Processen udføres i en Waelzovn - en ca. 40 m lang rotérovn - hvor det zinkholdige affald blandet med koks indføres i den ene ende (øverst), mens luft indblæses i den anden ende (nederst). Slaggen vil
således falde ud i den samme ende, som der indblæses luft. Undervejs i rotérovnen vil zinken fordampe og oxideres til zinkoxid, der føres med røggassen ud i samme ende som affaldet fyres ind i ovnen.
Røggassen og affaldsstrømmen er altså modsatrettede, hvilket bevirker at man gennem ovnen får en stigende opvarmning af affaldet.
Røggassen nedkøles kraftigt umiddelbart efter rotérovnen for at undgå dioxindannelse, hvorefter støvet med zinkoxid fjernes i et elektrofilter. Efterfølgende renses røggassen yderligere i filtre inden den ledes
ud.
Zinkstøvet, der kaldes Waelz-oxid, har et zinkindhold på ca. 65%, og sælges videre til zinkværker til yderligere oparbejdning /29/.
Batterier kan tilsættes som en delstrøm i det øvrige affald, og herved vil zinken fra batterierne kunne genvindes sammen med zink fra det øvrige affald. Organisk materiale og kul vil forbrændes, mens mangan
og jern vil blive tilbageholdt i slaggen, der eventuelt kan anvendes som fyld i forbindelse med anlægsarbejder. Ved processen er det således kun zink, der i egentlig forstand genanvendes.
Eksempel på en virksomhed i Europa der oparbejder batterier i Waelzovn er
- B.U.S. Berzelius Umwelt-Service AG, Tyskland.
Oparbejdning i zinksmelteovn
Batterier kan også oparbejdes i en zinksmelteovn - Imperial Smelting Process (ISP). Processen er udviklet til oparbejdning af zink og bly fra affaldsprodukter. Materialerne presses først til briketter,
hvorefter de sammen med koks indfødes i en skaktovn. Her opvarmes de til over 1.000 °C, hvorved slagge og metallisk bly kan aftappes i bunden, mens zink fordamper som metaldampe. Organisk
materiale og kul forbrændes i ovnen, og bidrager således til opvarmningen. Zinkdampene kondenseres efterfølgende som metal i en såkaldt bly "splash" kondensor. Princippet er, at flydende bly sprøjtes ind i
den varme gas, hvorved zink udkondenserer. Den flydende bly og zink fasedeler, hvorved zink kan tages fra og blyet kan genanvendes i kondensatoren. Efter separation og raffinering fås zink med en renhed
på mere end 99,990%
Ved anvendelse af batterier som fødemateriale er det, ligesom ved oparbejdning i Waelzovn, kun zinken fra batterierne der går til egentlig genanvendelse.
4.2.6.2 Oparbejdning i specialanlæg
Ved oparbejdning i specialanlæg forstås her anlæg, der er specielt udviklet med henblik på at oparbejde batterier i en separat proces. Der er ikke nogen klar skillelinie mellem processer, der kan henføres til
metalindustrien og specialprocesser, da mange af specialprocesserne bygger på i forvejen kendt teknologi fra metalindustrien.
Specialprocesserne kan opdeles i:
- Termiske processer
- Hydrokemiske processer
De termiske processer er langt de mest udbredte, men der findes enkelte firmaer i Europa der arbejder med hydrokemiske processer.
I det efterfølgende er der en kortere beskrivelse af de anlæg, der er identificeret i Europa. Nogle udvalgte anlæg er besøgt og analyseret mere indgående, og der er for disse en mere detaljeret beskrivelse i
bilag 1
Citron SA, Frankrig
Anlægget har en potentiel kapacitet på 130.000 tons pr. år, og kan behandle forskelligt tungmetalholdigt affald, herunder batterier med kviksølv. Der behandles pt. ca. 50.000 tons årligt, hvoraf batterier kun
udgør en mindre del. Det centrale i anlægget er den såkaldte Oxyreducer, hvor batterierne indfødes. Her opvarmes de til 1.000 - 1.200 °C ved hjælp af naturgasbrændere et stykke over affaldet. I bunden af
ovnen, hvor affaldet ligger, er der en reducerende atmosfære, således at metaloxider og -hydroxider reduceres, mens organiske dele pyrolyseres. Metaller som Zn, Pb, Cd og Hg med lavt
fordampningspunkt fordamper, og med undtagelse af Hg vil de re-oxideres når de når op i gasflammen.
Dette betyder at metallerne, med undtagelse af Hg, vil forlade ovnen som fine partikler. I et såkaldt gravitationskammer, hvor gashastigheden nedsættes på grund af kammerets størrelse vil partiklerne falde til
bunds, og kan tages ud. Hg og salte vil fortsætte med gassen, og renses ud i gasrensesystemet.
Fra gravitationskammeret fås således et pulverprodukt med et højt indhold af zinkoxid. Pulveret kan afsættes til yderligere oparbejdning, og en fordel ved processen er det lave indhold af chlorid i pulveret.
Kviksølv udkondenseres fra røggassen, og der fremstilles herved 99,995% rent kviksølv. Anlægget er nærmere beskrevet i bilag 1 A.
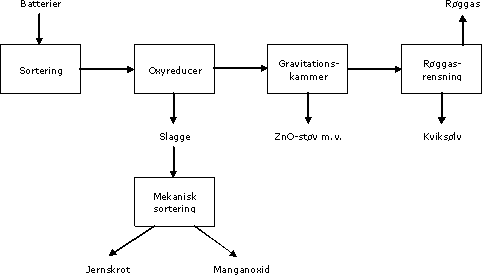
Figur 4.1. Citron SA. Skematisk procesdiagram.
Batrec Industrie AG, Schweiz
Dette anlæg med en årlig kapacitet på 3.000 tons, er specielt designet til behandling af batterier med kviksølv, og består først af en pyrolyse af batterierne ved ca. 600 °C. Herved pyrolyseres organisk
materiale og kviksølv fordamper. Batterierne overføres herefter til en induktions-smelteovn, hvor de opvarmes til 1.500 °C. Herved dannes der en slagge af ikke reducerbare metaller, en smelte af jern og
mangan (ferromangan) og en gas med zink på dampform. Gassen overføres til en splash-kondensor, hvor zinken kondenseres og aftappes i en renhed på 99%
Gassen fra pyrolysatoren renses for kviksølv, der efterfølgende destilleres til en renhed på 99,995%
Processen har en meget høj genanvendelsesgrad, idet praktisk taget alle metallerne oparbejdes. Anlægget er nærmere beskrevet i bilag 1 B.
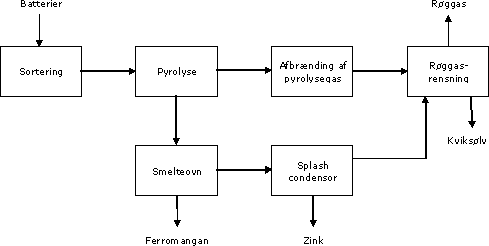
Figur 4.2. Batrec Industrie AG. Skematisk procesdiagram.
VALDI, Frankrig
Anlægget har en årlig kapacitet på 6.000 tons batterier med maksimalt 500 ppm kviksølv.
Batterierne tilføres en lysbueovn, hvor de smeltes i et stålbad ved ca. 1.600 °C. Herved vil jern og mangan indgå i en legering med stålbadet. Der tilføres samtidig forskellige additiver for at reducere MnO2 i
batterierne og for at neutralisere den udviklede gas. Ferromangan-legeringen aftappes og udstøbes i barrer der sælges.
Zink fra batterierne vil fordampe og efterfølgende oxideres i ovnen. Ligeledes vil kviksølv og salte fordampe, og under transporten til det efterfølgende filter vil kviksølvet reagere med zinken og danne en
stabil amalgamforbindelse. For at modvirke dannelse af dioxiner chokkøles gassen umiddelbart efter ovnen, og der tilsættes aktivt kul. I et posefilter udtages støvet fra gassen, og dette støv indeholder
75-86% zinkoxid og op til 0,06% kviksølv.
Zinkstøvet sendes til hydrokemisk oparbejdning hos et firma i Belgien, der også udvinder kviksølvet.
Ved processen sker der således en genanvendelse af både jern, mangan, zink og kviksølv fra batterierne. Anlægget er nærmere beskrevet i bilag 1 C.
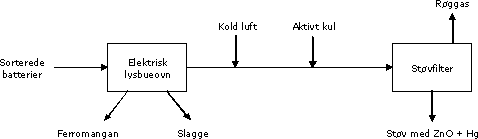
Figur 4.3. VALDI. Skematisk procesdiagram.
Entsorgungsbereich Simmering, EbS, Østrig
Anlægget har en kapacitet på 3.000 tons batterier pr. år, og er designet specielt til kviksølvholdige batterier indsamlet i Østrig.
Batterierne indfyres i en rotérovn, hvor de opvarmes til 600 °C. Herved åbner batterierne sig og kviksølv vil fordampe, mens organiske dele vil forbrændes. Røggassen afkøles efterfølgende og ledes igennem
en vådscrubber med NaOH, hvor kviksølv vaskes ud. Vaskevandet behandles kemisk således at kviksølvet fældes og det rensede vand udledes til Donau.
Røggassen fra skrubberen ledes til EbS' øvrige forbrændingsanlæg til forbrænding af farligt affald, således at røggasrensningen herfra sikrer at EU's emissionskrav er overholdt.
De "afgiftede" batterier udledes fra ovnen ved hjælp af en vandkølet snegl til en shredder. Efter shredningen deles materialet i en fin (< 1 mm) og en grov fraktion. Den fine fraktion, der indeholder en stor
mængde zink og mangan sendes til oparbejdning i metalindustrien, mens den jernholdige separeres fra den grove fraktion ved hjælp af en magnetseparation. Både den ikke jernholdige fraktion, der
indeholder en del kobber, og jernfraktionen sendes til oparbejdning i metalindustrien. Det har ikke været muligt at få detaljerede oplysninger om hvordan metallerne oparbejdes i metalindustrien, men på
baggrund af den separation der sker hos EbS må der forventes en høj grad af genanvendelse. Anlægget er nærmere beskrevet i bilag 1 D.
Klik her for at se Figur 4.4.
Figur 4.4. Entsorgungsbereich Simmering, EbS,. Skematisk procesdiagram.
Revatech - Erachem Europe, Belgien
Processen hos de to belgiske firmaer Revatech og Erachem Europe er designet til at behandle kviksølvholdige batterier mekanisk og hydrokemisk.
Ravatech står for den mekaniske behandling, mens Erachem Europe fra Revatech modtager et mellemprodukt og behandler dette hydrokemisk.
Kapaciteten hos Revatech er 3.000 - 4.000 tons batterier pr. år.
Processen starter hos Revatech med en mekanisk behandling, hvor batterierne knuses. Restenergien i batterierne gør, at der udvikles varme ved knusningen, hvilket betyder afdampning af kviksølv. Luft,
afsuget fra knusningen, ledes gennem et kulfilter. Plastik og metaldele (stål og zink) fjernes og plasticdelen sendes til cementindustrien, hvor energiindholdet udnyttes, mens metaldelen sendes til oparbejdning i
metalindustrien.
Den resterende del af batterierne udgør ca. 2/3 af vægten og benævnes som "black mass" på grund af den sorte farve. Denne del sendes til Erachem Europe og behandles hydrokemisk. Der startes med en
alkalisk vask for at fjerne elektrolytten efterfulgt af en filtrering. Spildevandet med elektrolytten renses og udledes, mens resten behandles med svovlsyre og additiver og filtreres, således at der fremstilles en
blanding af ZnSO4 og MnSO4, og en fast restfraktion der deponeres.
Dobbeltsulfatblandingen oprenses yderligere, idet den indeholder op til 500 ppm kviksølv samt nikkel, cadmium og andre urenheder. Herefter kan der fremstilles og sælges forskellige salte og oxider af
mangan og zink.
Ved processen er der en udnyttelse af jern, zink og mangan i batterierne, og Revatech angiver genanvendelsesgraden til 70%
Klik her for at se Figur 4.5.
Figur 4.5. Revatech – Erachem. Skematisk procesdiagram.
Euro Dieuze Industrie, Frankrig
Euro Dieuze Industrie, der ejes af det franske Vivendi, behandler batterier ved en mekanisk/hydrokemisk proces. Det har ikke været muligt at få oplysninger direkte fra virksomheden om deres proces,
hvorfor beskrivelsen bygger på andenhånds oplysninger. Processen minder tilsyneladende om processen hos Revatech/Erachem Europe.
Først neddeles batterierne mekanisk, hvorefter pulver og metal/plastik adskilles ved sigtning. Metallet består især af stål og zink. Pulveret behandles med svovlsyre, hvorefter kulstof frafiltreres. Filtratet, der
indeholder opløst zink og mangan, behandles således at kviksølv udfældes, hvorefter der fremstilles mangan- og sulfatforbindelser til salg.
Zimaval Technologies, Frankrig
Zimaval har en kapacitet på behandling af 4.000 tons batterier årligt, og processen bygger på den samme teknik som hos Revatech, der tilsyneladende også har en aktieandel i Zimaval. Det har ikke været
muligt at fremskaffe flere oplysninger om processen.
4.3 Vurdering af behandlingsteknologierne
Som det fremgår af forrige afsnit, er der med hensyn til alkali- og brunstensbatterier, mulighed for at oparbejde dem som en delstrøm i metalindustrien eller i specialiserede anlæg.
Generelt er priserne de laveste ved oparbejdning i metalindustrien, men til gengæld er genanvendelsesprocenten også lavere. Ofte er det kun zinken der oparbejdes til egentlig genanvendelse, hvilket giver en
genanvendelsesgrad på op til 25%. På stålværkerne er det dog jerndelen der genanvendes direkte og zinken genanvendes ved efterfølgende oparbejdning af flyveasken. På stålværkerne kan således opnås
en genanvendelsesgrad på op til 40% /34/.
Et andet problem, der har været nævnt ved behandling i metalindustrien er, at disse anlæg generelt ikke har røgrensningsudstyr til at fange cadmium og bly fra fejlsorterede batterier og kviksølv fra gamle
alkalibatterier. Endvidere kan der fra batteriernes organiske dele (plastik etc.) dannes dioxiner under forbrændingen, og normalt har anlæggene ikke udstyr til at rense for dette. Ved emissionsmålinger på
anlæggene vil det dog ofte ikke være muligt at måle en øget emission i røggassen, hvilket kan skyldes at den evt. øgede emission fortyndes bort i den store røggasmængde.
Eneste mulighed for behandling i metalindustrien i Danmark er Det Danske Stålvalseværk A/S. Her har man dog af kvalitetsmæssige årsager ikke hidtil haft mulighed for at modtage batterier, da bl.a.
kobberindholdet overstiger den mængde som værket kan acceptere. Hvis batterierne skal oparbejdes i metalindustrien, er man således nødt til at sende dem til udlandet. Herved bliver der ud over udgifterne
til behandling også en transportudgift, der naturligvis afhænger af den aktuelle afstand.
Som nævnt er behandlingen på de specialiserede anlæg dyrere, men til gengæld er genanvendelsesgraden også op til 70%. Endvidere er nogle af anlæggene specielt designet til at behandle kviksølvholdige
batterier, og samtidig tage hånd om f.eks. cadmium og bly fra fejlsorterede batterier.
Inden for specialanlæggene er der stor forskel på de produkter der fremstilles, og i hvor høj grad der skal ske en yderligere oparbejdning på andre anlæg efterfølgende.
Hos f.eks. Batrec fremstilles der udelukkende salgbare produkter, der kan anvendes uden yderligere oparbejdning. Hos de øvrige anlæg skal en større eller mindre del af produkterne - specielt zink - sendes
til yderligere oparbejdning inden de bliver anvendelige.
Kort kan det konkluderes, at fordelen ved oparbejdning i metalindustrien er de lave omkostninger, mens oparbejdningsgraden er højere i de specialiserede anlæg. Endvidere er disse også i højere grad
indrettet til at kunne håndtere evt. kviksølv, cadmium og dioxiner/furaner.
I afsnit 4.2.6 er i tabel 4.1 vist en oversigt over genanvendelsesgrad og prisniveau for de undersøgte processer.
5 Dansk løsning
Der findes ikke i dag en behandlingsløsning i Danmark. Hvis alle batterier i Danmark skal indsamles separat, er der tre muligheder, hvis batterierne behandles:
- Eksport til udenlandske anlæg
- Etablering af behandlingsanlæg i Danmark
- Forbehandling af batterierne i Danmark og efterfølgende eksport til udenlandske anlæg
På grund af den forholdsvise lille mængde, der potentielt vil kunne indsamles i Danmark, vurderes der ikke at være basis for et egentligt behandlingsanlæg her, med mindre der også importeres batterier fra
udlandet.
En mulig løsning for oparbejdning af batterier indsamlet i Danmark kan være:
- Afgiftning af batterierne på dansk anlæg
- Endelig oparbejdning i udlandet
Ved en afgiftning menes, at plastik og lignende samt evt. kviksølv, cadmium og bly fjernes fra batterierne i et specielt anlæg. Dette kan gøres enten ved pyrolyse eller forbrænding af batterierne. Herefter
volder batterierne ikke emissionsmæssige problemer i metalindustrien, og kan således umiddelbart behandles her.
Ønskes imidlertid en højere genanvendelsesprocent, er det nødvendigt efter afgiftningen at neddele batterierne, sortere materialet i fraktioner, og sende disse til specialiserede oparbejdere. Faktisk som det
gøres på Ebs' anlæg i Østrig.
I fase 2 af dette projekt arbejdes derfor videre på, ved praktiske forsøg, at undersøge en model hvor der først foretages en pyrolyse af batterierne, hvorved organisk materiale og kviksølv fjernes. Herefter
undersøges det om der er en fordel i at behandle batterierne yderligere ved fraktionering, eller om det er mest hensigtsmæssigt at sende dem direkte til genbrug i metalindustrien. Dette afhænger som nævnt
også af hvor høj genanvendelsesprocent der ønskes. Eksempelvis er det ved en behandling i metalindustrien ikke muligt at opnå en genanvendelsesprocent på de 55 der er angivet i det gamle udkast til EU's
direktivforslag.
Et alternativ til pyrolyse kan være forbrænding i en lille rotérovn efter det princip der benyttes på Ebs' anlæg i Østrig. Pyrolyseforsøgene sammenlignes derfor med forbrændingsløsningen.
6 Referencer og litteratur
- BatteriForeningens hjemmeside (2001). www.batteri.dk
- Fricke, J. L. & Knudsen, N. (2001). „Entsorgung verbrauchter Gerätebatterien.“ Stiftung Gemeinsames Rücknahmesystem Batterien, Hamburg.
- European Portable Battery Association, EPBA (1997). Product Information
- DURACELL Batteries (1998)
- Krebs, A. (2001). “The Future Way for Batery Recycling - BATREC Recycling System“. International Congress for Battery Recycling. Montreux, Switzerland, May 2-4, 2001.
- Helgesson, C.I. & Lindén, R. (1999). ”Metallurgical and Ecological Aspects on Using Recycled General Purpose Batteries in Steel Making.” Proceedings of the 5th International Battery Recycling Congress. Deauville, France, September 27-29, 1999.
- Søndergaard, J. (2001). Alkaline batteries A/S. Thisted. Personlige oplysninger.
- David, J. (2001). “Can We Recycle 70% of the Components of the Nikkel Metal Hydride and Lithium-Ion Batteries?”. International Congress for Battery Recycling. Montreux, Switzerland, May 2-4, 2001.
- European Portable Battery Association, EPBA (2001). Hjemmeside: www.epba-europe.org
- Bekendtgørelse om affald. Bek. nr. 619 af 27. juni 2000. Miljø- og Energiministeriet.
- Affald 21. Regeringens affaldsplan 1998-2004. Miljø- og Energiministeriet 1999.
- Nielsen, A. (2003). Miljøstyrelsen. Personlige oplysninger.
- Bekendtgørelse om tilskud til indsamling og genanvendelse af blyakkumulatorer. Bek. nr. 1060 af 4.december 2000. Miljø- og Energiministeriet.
- Bekendtgørelse om gebyrer på blyakkumulatorer. Bek. nr. 1061 af 4. december 2000. Miljø- og Energiministeriet.
- Lov om afgift af blyakkumulatorer og hermetisk forseglede nikkel-cadmium-akkumulatorer. Lov nr. 414 af 14. juni 1995.
- Lov om godtgørelse i forbindelse med indsamling af blyakkumulatorer og hermetisk forseglede nikkel-cadmium-akkumulatorer. Lov nr. 404 af 14. juni 2000.
- Bekendtgørelse af lov om afgift af hermetisk forseglede nikkel-cadmium-akkumulatorer (lukkede nikkel-cadmium batterier). Lbk. nr. 561 af 3. august 1998.
- Bekendtgørelse af lov om godtgørelse i forbindelse med indsamling af hermetisk forseglede nikkel-cadmium-akkumulatorer (lukkede nikkel-cadmium-batteier). Lbk. nr. 547 af 30. maj 2000.
- Miljøstyrelsen (2001). Indsamlingsordning for nikkel-cadmium-batterier. Opdateret 20. november 2001. Miljøstyrelsens hjemmeside: www.mst.dk.
- Drivsholm, T. (2000). Massestrømsanalyse for cadmium. Miljøprojekt nr. 557. Udført af COWI A/S for Miljøstyrelsen.
- Lildballe, E. (2001). ReturBat, Foreningen til indsamling af blyakkumulatorer i Danmark. Personlige oplysninger.
- ReturBat (2001). Hjemmeside: www.returbat.dk
- Scrosati, B. (2001). ”Portable Lithium Batteries: Technology & Market”. International Congress for Battery Recycling. Montreux, Switzerland, May 2-4, 2001.
- Rahbek, L. (2001). Miljøstyrelsen. Personlige oplysninger.
- IngeniørenNet (2001). ”Topsøe tjener penge på brændselsceller”, ”Dansk produktion af brændselsceller”, ”En miljøvenlig lille celle”
- Werth-Kreienberg, C. (2000). Trienekens AG. Personlige oplysninger.
- Ganivet, C. (1999). “6 Years Experience in Lithium battery recycling“. Proceedings of the 5th International Battery Recycling Congress. Deauville, France, September 27-29, 1999.
- Lain, M.J. (1999). “Recycling of Lithium Cells and Batteries”. Proceedings of the 5th International Battery Recycling Congress. Deauville, France, September 27-29, 1999.
- Schmidt, P. og Ribke, W. (2001). B.U.S. Commercial Services GmbH. Personlige oplysninger.
- Draft Proposal for a EUROPEAN PARLIAMENT AND COUNCIL DIRECTIVE../…;/EC of .. …;…; …;. on batteries and accumulators. April 1999.
- -
- -
- -
- Watson, N. J. (1998). Recycling in the metals industry. Duracell Batteries.
- Rausch, S. (2001). SORBAREC-X-ray- Technology for Sorting of Spent Batteries. International Congress for Battery Recycling. Montreux, Switzerland, May 2-4, 2001.
- Rentz, O., Engels, B. og Schultmann, F. (2001). Untersuchung von Batteriverwertungsverfahren und anlagen hinsichtlich ökologisher und ökonomischer Relevanz unter besonderer Berücksichtigung des Cadmiumproblems. Deutsch-Französisches Institut für Umweltforschung, Karlsruhe.
- Rahbek, L. (1999). “Present and future collection of batteries in Denmark”. Proceedings of the 5th International Battery Recycling Congress. Deauville, France, September 27-29, 1999.
Anden anvendt litteratur
- Vincent, C.A. & Scrosati, B. (1997). Modern Batteries. An Introduction to Electrochemical Power Sources. Arnold, London.
- Berndt, D. (1997). Maintenance-Free Batteries. A Handbook of Battery Technology. Second Edition. Research Studies Press Ltd., Somerset.
Bilag Beskrivelse af anlæg
Bilag 1 A: CITRON SA
Bilag 1 B: Batrec Industrie AG
Bilag 1 C: VALDI
Bilag 1 D: Entsorgungsbereich Simmering, EbS
Bilag 1A
CITRON SA
Anlægget er besøgt i marts 2001.
Beliggenhed
Rogerville ved Le Havre i Frankrig. Ca. 1.200 km fra den danske grænse mod Tyskland.
Anlæggets formål
Anlægget er designet til at behandle forskelligt tungmetalholdigt affald i kampagner, herunder brugte brunstens- og alkalibatterier. Batterier udgør i dag kun en mindre del af det behandlede affald. Ved
behandlingen produceres zinkoxid, kviksølv og andre metalkoncentrater, der afsættes til videreforarbejdning i metalindustrien.
Baggrund
CITRON AG blev grundlagt i Schweiz 1991.
Efter drift af et pilotanlæg med en kapacitet på 1.000 tons pr. år blev det industrielle anlæg i Rogerville sat i drift i august 1999. Dette anlæg ejes og drives af CITRON SA, France.
CITRON SA, France er et datterselskab af CITRON Holding AG med minoritet ejerskab af ALSTOM og SOHGEPAR. CITRON Holding AG er noteret på den schweiziske børs, og hovedaktionærerne
omfatter banker, forsikringsselskaber m.v.
Der er ca. 100 ansatte i firmaet.
Kapacitet
Anlægget har en potentiel kapacitet på 130.000 tons affald pr. år. Der behandles i dag omkring 50.000 tons pr. år.
Procesbeskrivelse
De forskellige affaldstyper opbevares i en lagerhal, hvorfra de via et transportsystem indfødes til selve behandlingsanlægget. Blandede batterier håndsorteres, således at typer som NiCd- og blybatterier
sendes til andre behandlere.
Oxyreducer
Det centrale i anlægget er den såkaldte Oxyreducer, som er et modificeret ringkammer ovn med en diameter på 20 meter. Ovnbunden, hvor affaldet/ batterierne danner et tyndt lag på 6-8 cm, roterer med
ca. en omgang i timen. Affaldet følger med ca. 3/4 omgang, således at opholdstiden bliver ca. 45 minutter. Affaldet varmes op til 1.000 - 1.200 °C ved hjælp af 6 naturgasbrændere placeret et stykke over
affaldet hele vejen rundt i ovnen. I bunden af ovnen, hvor affaldet ligger, bliver der herved en reducerende atmosfære (iltunderskud), således at der sker en pyrolyse af det organiske materiale. Den dannede
kulmoNOxid oxideres til kuldioxid i brændernes brændzone før det forlader ovnen.
Den reducerende atmosfære i affaldet gør, at metaloxider og -hydroxider i affaldet reduceres, og metaller med lavt kogepunkt som zink, bly, cadmium og kviksølv vil fordampe. I gasfasen vil de, med
undtagelse af kviksølv, oxideres inden de forlader ovnen.
Gravitationskammer
Med undtagelse af kviksølv vil metaloxiderne forlade ovnen som små faste partikler. Disse fanges i et såkaldt gravitationskammer, hvor gashastigheden på grund af kammerets størrelse nedsættes, hvorved
metaloxiderne på grund af tyngdekraften vil falde ned i bunden af kammeret, hvorfra de kan udtages. Temperaturen i kammeret er omkring 1.150 °C, og på grund af denne temperatur vil kviksølv ikke
kondensere, men vil blive ledt med gassen videre. Ligeledes vil salte, specielt chlorid, ikke blive blandet med zinkoxiden. Dette er angiveligt en fordel ved processen, frem for den zinkoxid der fremstilles ved
en Waelzproces, hvor man ofte er nødt til at fjerne chlor efterfølgende.
Røggasrensning
Røggassen renses efterfølgende i et vådt, flertrins gasrensesystem, bestående af to quenchere, hvor gastemperaturen sænkes til 55 °C, et vådt elektrofilter og en basisk scrubber. Det meste kviksølv
kondenseres og fjernes som metal ud af sumpen i den første quencher. Det resterende kviksølv fjernes i den anden quencher, det våde elektrofilter og scrubbersystemet. Til slut ledes røggassen gennem et
aktivt kulfilter for at fjerne eventuelle dioxiner.
Slammet der udtages fra røggasrensningen behandles først i en reaktor, hvor det opvarmes til 550 °C. I den efterfølgende dekanter adskilles strømmen fra reaktoren i tre fraktioner: vand, slam og 99,995%
ren kviksølv.
Slammet presses i en filterpresse, og efter en eventuel destillering for yderligere kviksølv sendes slammet tilbage til ovnen. Vandet fra filterpressen ledes sammen med vandet fra dekanteren til en
bundfældningstank, og efter en kontrol af om emissionsgrænserne er overholdt, ledes vandet ud i havet. Slam fra bundfældningsbassinet ledes til filterpressen.
Slaggen fra Oxyreduceren
De metaller og øvrige produkter der ikke fordamper fra Oxyreduceren tages ud gennem et vandbad. Herefter sorteres restprodukterne mekanisk ved forskellige teknikker: Shredding, efter størrelse,
magnetisk og med Eddy Current magnet.
Klik her for at se anlæg
Behandling af batterier
Anlægget kan behandle brunstens- og alkalibatterier, og er ikke følsomt over for kviksølv eller plastik i de behandlede batterier.
Batterierne sorteres først manuelt hvorved batterier som NiCd, bly m.v. frasorteres.
I Oxyreduceren forbrændes det organiske indhold i batterierne. Den totale opholdstid i den oxiderende zone opgives til mere end 4 sekunder.
Kviksølv fra batterierne fordamper i Oxyreduceren og kondenseres som beskrevet tidligere.
Zink, der udgør en betydelig del i batterierne, fordamper sammen med eventuel cadmium og bly i Oxyreduceren, men i forbrændingszonen oxideres de til metaloxider, der udtages i gravitationskammeret.
Hovedproduktet fra gravitationskammeret er zinkoxid, og eventuelle NiCd- eller blybatterier i de indfødte batterier vil derfor betyde, at cadmium- og blyoxider vil optræde som urenheder i den
koncentrerede zinkoxid.
Metaller som jern, mangan, nikkel, chrom og kobber vil ikke fordampe i Oxyreduceren, og tages ud sammen med slaggen, der fra batterier består af jernskrot, kulelektroder og mangaNOxid. På grund af
mangans egenskaber samt ilt og temperaturmæssige forhold i bunden af oxyreduceren vil mangan ikke reduceres.
Jerndelen frasorteres ved hjælp af en magnet, mens mangaNOxid, der er et fint pulver, adskilles fra kulelektroderne ved sigtning. Kulelektroderne knuses og anvendes som reduktionsmiddel i Oxyreduceren,
mens jern og mangaNOxid afsættes til genanvendelse.
Massebalance
1000 kg batterier |
kg |
|
Plastic og andet |
65 |
Forbrændes under processen og ender som CO2 |
Vand |
120 |
Indgår i spildevandsbehandlingen / fordamper |
Salte |
40 |
C-elektroder |
90 |
Knuses og anvendes i processen |
Stålskrot |
180 |
Afsættes til oparbejdning |
MnO |
350 |
ZnO-koncentrat |
180 |
Kviksølv |
0,2 |
Emissioner
For 1.000 kg batterier:
Røggas: |
Mængde: |
7.000 m³ |
|
NOx: |
0,7 kg |
100 mg/m³ |
|
SOx: |
< 0,1 kg |
< 15 mg/m³ |
|
Støv: |
0,03 kg |
< 5 mg/m³ |
|
Zn: |
8 g |
1,1 mg/m³ |
|
HCl |
8 g |
1,1 mg/m³ |
|
Cd |
0,1 g |
< 15 mg/m³ |
|
Hg |
0,06 g |
< 10 mg/m³ |
|
|
|
Spildevand: |
Mængde: |
1,7 m³ |
|
Cl |
15 kg |
8,8 kg/m³ |
|
Zn |
0,3 kg |
< 200 g/m³ |
|
Cd |
0,03 kg |
< 20 g/m³ |
|
MES |
25 g |
15 g/m³ |
|
Hg |
0,01 g |
6 mg/m³ |
Spildevandet udledes, efter kontrol af om udledningskriterierne er overholdt, batchvis direkte i flodmundingen, hvorfra det føres til havet.
Affald: Det oplyses fra CITRON, at der ikke opstår affald i forbindelse med behandlingen af batterier.
Energiforbrug og vandforbrug
For 1.000 kg batterier:
Vand: |
3,3 m³ |
Elektricitet |
150 kWh |
Naturgas |
85 Nm³ |
Behandlingspris
6.000 - 8.000 DKK pr. tons
Bilag 1B
Batrec Industrie AG
Anlægget er besøgt i marts og august 2000.
Beliggenhed
Wimmis i Schweiz. Ca. 1.100 km fra den danske grænse mod Tyskland.
Anlæggets formål
Anlæggets er designet specielt til behandling af brunstens- og alkalibatterier med indhold af kviksølv. Derudover behandles også andet kviksølvholdigt affald i separate destillationsprocesser, ligesom Batrec
står for indsamlingen af batterier i Schweiz.
Baggrund
Batrec blev grundlagt i 1989 med det formål at bortskaffe brugte batterier i Schweiz. Det blev besluttet at basere anlægget på en proces udviklet af Sumitomo Heavy Industries, og i 1992 var anlægget klar
til opstart. 1½ år efter i 1994 var anlægget oppe på den forventede driftskapacitet.
I 1999 fusionerede Batrec AG med Rycymet SA og blev til Batrec Industrie AG. De vigtigste aktionærer er den schweiziske stat, myndighederne i flere schweiziske kantoner, det schweiziske postvæsen,
m.fl.
Firmaet har ca. 50 ansatte.
Kapacitet
Anlægget har en kapacitet på 3.000 tons batterier pr. år. Batrec er i gang med en udvidelse, således at kapaciteten udvides til ca. 4.500 tons pr. år.
Procesbeskrivelse
Batterierne modtages blandet, og de sorteres inden behandlingen manuelt. Lithium-, NiCd-, NiMH-batterier m.fl. frasorteres, således at der opnås en renhed af brunstens-, alkalibatterier og knapceller på
omkring 98%. NiCd- og NiMH-batterier sendes til oparbejdning andre steder, mens den øvrige fraktion behandles på Batrecs anlæg.
Batrecs proces består i princippet af 3 trin:
Pyrolyse
Batterierne indfødes via en sluse til en pyrolysator, hvor organiske komponenter pyrolyseres, mens vand og kviksølv afdampes ved 650 grader. Pyrolysegassen afbrændes ved 1.000 °C og afkøles herefter
øjeblikkelig til 60°C i en quench for at undgå dioxindannelse. Pyrolysatoren opvarmes ved hjælp af varm gas. Det er nødvendigt med en opholdstid på ca. 4 timer for at være sikker på, at batterierne opnår
den ønskede temperatur på 650 °C.
Smelteovn
De pyrolyserede batterier overføres til en induktions-smelteovn hvor de opvarmes til 1.500 °C. Herved dannes der en slagge af ikke reducerbare metaller, en smelte af jern og mangan (ferromangan), og en
gas med zink på dampform. Gassen overføres til en såkaldt splashkondensor, hvor zinken kondenseres.
Ferromanganen der består af ca. 40% mangan og 60% jern aftappes flydende fra smelteovnen, og udstøbes i halvkugler på størrelse med tennisbolde. Dette produkt afsættes til jernstøberier.
480 °C varm flydende zink aftappes fra splash-kondensoren, og udstøbes i barrer med en renhed på 99% Barrerne afsættes til metalindustrien.
I smelteovnen omsættes kulstoffet i batterierne til CO, der efter udledning fra splash-kondensoren vaskes og afbrændes således at det anvendes til opvarmning af pyrolysatoren.
Gasrensning
Pyrolysegassen afbrændes som nævnt ved 1.000 °C. Efterfølgende behandles gassen i en traditionel, våd røggasrensning. Herved udkondenseres kviksølv i slammet, hvorfra det genvindes ved en
destillationsproces. Herved fås 99,995% rent kviksølv, der afsættes til metalindustrien.
Massebalance
1.000 kg batterier |
kg |
|
Plastic, papir m.v. Carbon |
50 - 100
50 - 100 |
Forbrændes under processen og ender som CO2 |
Vand Salte |
50 - 100
50 - 100 |
Indgår i spildevandsbehandlingen |
Slagge (metaloxider) |
ca. 50 |
Deponi |
Ferromangan Zink Kviksølv |
ca. 390
ca. 200 ca. 1,5 |
Afsættes til metalindustrien |
Emissioner
For 1.000 kg batterier:
Røggas: |
Mængde: |
ca. 1.100 Nm³ |
NOx: |
0,5 kg |
133 mg/Nm³ |
SOx: |
< 0,1 g |
< 0,1 mg/Nm³ |
Støv: |
< 1 g |
0,5 mg/Nm³ |
Zn: |
0,03 g |
0,025 mg/Nm³ |
HCl: |
0,8 g |
0,08 mg/Nm³ |
Cd: |
1,4 mg |
0,001 mg/Nm³ |
Hg: |
16 mg |
0,014 mg/Nm³ |
|
Spildevand: |
Mængde |
1,4 m³ |
Cl: |
Zn: |
170 g |
0,12 mg/l |
Cd: |
10 g |
0,007 mg/l |
Hg: |
1,1 g |
0,0008 mg/l |
Pb: |
100 g |
0,07 mg/l |
Cu: |
270 g |
0,19 mg/l |
Cyanid: |
6 mg |
0,004 mg/l |
Spildevandet ledes efter analyse til det offentlige spildevandssystem.
Energi- og vandforbrug
For 1.000 kg batterier:
Vand: |
5,3 m³ (heraf er 3,7 m³ kølevand) |
Olie: |
10 kg |
Elektricitet: |
1.450 kWh |
Behandlingspris
Kostprisen for behandling er opgivet til ca. 15.000 DKK pr tons
Bilag 1C
VALDI
Anlægget er besøgt i juni 2001
Beliggenhed
Feurs i nærheden af Lyon, Frankrig. Ca. 1.400 km fra den danske grænse mod Tyskland.
Anlæggets formål
VALDIs hovedaktiviteter er, ud fra metalholdige restprodukter, fremstilling af jernlegeringer til rustfrit stål og andet specialstål. Brugte brunstens- og alkalibatterier med op til 500 ppm kviksølv udgør en del
af det affald der modtages. Der fremstilles ved behandlingen ferromangan, der afsættes til stålindustrien, og et zinkholdigt produkt der afsættes til oparbejdning.
Baggrund
VALDI startede med at teste mulighederne for oparbejdning af batterier i 1994, og i 1996 blev det besluttet at industrialisere processen.
VALDI har produktion to steder i Frankrig: Feurs og Le Palais. Det er kun i Feurs der behandles batterier.
Virksomheden ejes af de franske firmaer AFE og TREDI. AFE er en gruppe af metalstøberier mens TREDI er et affaldsbehandlingsfirma.
VALDI Feurs har ca. 60 ansatte.
Kapacitet
Anlægget har en kapacitet for batterier på 6.000 tons pr år. I 2000 blev behandlet 2.000 - 2.500 tons.
Procesbeskrivelse
De batterier der modtages hos VALDI i Feurs er sorteret, således at det kun er brunstens- og alkalibatterier med højst 500 ppm kviksølv.
Batterierne tilføres kontinuert ved hjælp af et transportsystem til en elektrisk lysbueovn. Der startes på et smeltet stålbad på ca. 1.600 °C, hvor jern og mangan fra batterierne vil smelte og indgå i en legering
med stålbadet. Der tilføres samtidig forskellige additiver for at reducere MnO2 i batterierne og for at neutralisere den udviklede gas.
Det smeltede jern og mangan danner en legering, der aftappes og udstøbes i ferromangan barrer, der sælges.
Derudover dannes der en slagge med aluminium-, silicium- og jerNOxider. Jernindholdet i slaggen udnyttes af AFE METAL ved smeltning. Organisk indhold og kulstof fra batterierne vil forbrændes til CO2.
Zink i batterierne vil fordampe og efterfølgende oxideres til zinkoxid i ovnen. Ligeledes vil kviksølv og salte fordampe. Under transporten til det efterfølgende filter vil kviksølvet reagere med zinken og danne
stabil amalgamforbindelse.
Umiddelbart efter at gassen forlader ovnen køles den ned fra 1.100 til 200 °C ved at indblæse kold luft. Dette gøres for at modvirke dannelse af dioxiner. Gassens indhold af calciumhydroxid og andre
alkaliske stoffer sørger for at chlor og svovl i gassen neutraliseres. Som en yderligere sikkerhed tilsættes der løbende aktivt kul til gasstrømmen, for at binde kviksølv ved eventuelle peaks.
Gassen transporteres flere hundrede meter i et rør frem til, hvor støvet udtages i et posefilter. Den rensede gas udledes herefter fra toppen af filteret i 7-8 meters højde. Støvet opsamles i bigbags, og
indeholder 75-85% zinkoxid og op til 0,06% kviksølv.
Støvet afsættes til Jean Goldschmidt International s.a. i Belgien, der oparbejder støvet ved hjælp af hydrometallurgi. Støvet blandes med andre biprodukter med zink og bly, og der tilsættes svovlsyre.
Herved dannes zinksulfat af ca. 90% af zinken og et uopløseligt koncentrat med bly, kviksølv og resten af zinken. Koncentratet sendes til oparbejdning i blyindustrien, hvor blyindholdet oparbejdes ved hjælp
af pyrometallurgi. Herved vil kviksølvet fordampe, men kan efterfølgende kondenseres. Goldschmidt angiver at effektiviteten af kviksølvgenvindingen er mere end 95%
Massebalance
1.000 kg batterier |
kg |
|
Plastic, papir m.v. Carbon |
80
75 |
Forbrændes under processen og ender som CO2 |
Vand |
|
Fordamper |
Slagge
heraf Mn
Fe |
300
40 10 |
Sendes til oparbejdning |
Ferromangan |
350 |
Afsættes til støberier |
Støv
heraf Zn
Hg |
350
190 0,2 |
Sendes til oparbejdning |
Emissioner
For 1.000 kg batterier:
(Der regnes med en kapacitet på 675 kg pr. time)
Røggas: |
Mængde: |
ca. 110.000 Nm³ |
NOx: |
mg/Nm³ |
SOx: |
g |
mg/Nm³ |
Støv: |
< 110 g |
< 1 mg/Nm³ |
Zn: |
20 g |
0,186 mg/Nm³ |
HCl: |
g |
mg/Nm³ |
Cd: |
3,3 mg |
0,00003 mg/Nm³ |
Hg: |
330 mg |
0,003 mg/Nm³ |
Der udledes ikke spildevand fra processen.
Energiforbrug
For 1.000 kg batterier:
Elektricitet |
1.050 kWh |
Naturgas |
0,5 Nm³ |
Behandlingspris
5,00 - 6,50 kr. pr. tons (afhængig af mængden)
Bilag 1D
Entsorgungsbereich Simmering, Ebs
Chemcontrol a/s har leveret den termiske del til anlægget, og den følgende beskrivelse bygger på oplysninger fra Chemcontrol a/s.
Beliggenhed
Wien i Østrig. Ca. 1.300 km fra den danske grænse mod Tyskland.
Anlæggets formål
Anlægget er designet til at behandle kviksølvholdige brunstens- og alkalibatterier.
Baggrund
I Østrig diskuterede man to typer af behandlinger af udtjente batterier. Den ene, og simple, var indsamling og deponering i saltminer i det sydlige Østrig. Den anden var en termisk behandling med henblik på
affaldsminimering og materialegenanvendelse.
Efter en lang debat i Østrig blev det besluttet at anvende den termiske behandling.
Som udgangspunkt var hovedformålet med anlægget at neddele batterierne, afdampe kviksølvet fra batterierne ved at opvarme dem til 600 °C i en rotérovn samt efterfølgende at kondensere kviksølvet ud af
røggassen ved at køle denne til 25 °C.
Ovennævnte proces gav en del driftsmæssige problemer med bl.a. store støvmængder til følge. Ligeledes viste det sig svært at afsætte kviksølvet, hvorfor processen blev modificeret til den i dag beskrevne.
Chemtec Ensorgungssysteme & Consulting GmbH er den formelle ejer af behandlingsanlægget. Chemtec ejes af tre selskaber inden for affaldsbranchen i Østrig.
Kapacitet
Anlægget har en kapacitet på 500 kg/h svarende til 3.000 tons pr. år. Det svarer meget godt til, hvad der indsamles af batterier i Østrig i dag.
Procesbeskrivelse
Batterierne sorteres manuelt således at NiCd-, lithium- og NiMH-batterier sorteres fra.
Alkali- og brunstensbatterierne fødes til en rotérovn, hvor de opvarmes til en temperatur på 650 °C ved hjælp af en oliebrænder placeret i fyrfronten. Den høje temperatur medfører at batterierne "åbnes", og
de let fordampelige tungmetaller som kviksølv damper af, mens plastik og papir afbrændes.
Efter opvarmningen udledes batterierne fra rotérovnen via en vandkølet snegl og et transportbånd til en shredder, hvor restdelen shreddes. Den shreddede del deles via en sigte i en fin og en grov fraktion.
Den fine fraktion (< 1 mm), der udgør ca. halvdelen af batterivægten og indeholder omkring 40% zink og 30% mangan sendes til oparbejdning i metalindustrien, mens den grove fraktion går gennem en
magnetseparator, hvor jern separeres fra ikke-jern materiale. Begge de sidstnævnte fraktioner sendes ligeledes til metalindustrien.
Røggassen fra rotérovnen ledes gennem et efterforbrændingskammer, hvorefter røggassens hovedpart af støv/partikler fjernes i en cyklon. Røggassen nedkøles herefter i en luft-gas varmeveksler, før den
ledes igennem en vådskrubber. I skrubberen vaskes gassen med en vandig opløsning af NaOH, hvorved gassens indhold af chlor, støv og tungmetaller fjernes.
Vaskevandet behandles ved en kemisk fældning i EbS' anlæg til behandling af øvrigt uorganisk affald. Herved udfældes kviksølv i filterkagen, der afhængigt af indholdet af organisk stof, enten deponeres
direkte eller afbrændes i EbS' øvrige forbrændingsanlæg. Vandet fra fældningen ledes, efter en biologisk rensning, ud i floden Donau.
Røggassen fra skrubberen ledes til EbS' øvrige forbrændingsanlæg, og derfra videre gennem røggasrensningsanlægget i forbindelse med dette.
Massebalance
1000 kg batterier |
kg |
|
Fin fraktion
heraf Fe
Zn
Mn |
520
56 204 172 |
Sendes til oparbejdning i metalindustrien |
Ikke-jern fraktion
heraf (C, H, N, O) |
77
56 |
Sendes til metalindustrien |
Jern fraktion |
75 |
Sendes til metalindustrien |
Flyveaske |
8 |
Deponeres |
Vaskevand
heraf Hg |
3
0,22 |
Metaller fældes og vandet udledes i Donau. Filterkagen deponeres. |
Røggas |
316 |
Sendes til EbS' forbrændingsanlæg |
Energiforbrug
For 1.000 kg batterier:
Elektricitet |
140 kWh |
Olie |
200 kg |
Behandlingspris
ca. 7.700 kr. pr. tons
| Til Top | | Forside |
|