| Forside | | Indhold | | Forrige | | Næste |
Affaldsminimering i støberi- og maskinindustrien
Summary and conclusions
Iron foundry makes a fortune on waste
During the last four years, Vald. Birn A/S, the largest iron foundry in Northern Europe, has made an extraordinary effort to reduce the quantities of waste by testing new techniques for recovery of resources
that otherwise are expensive to purchase or dispose of. At the same time, Vald. Birn A/S has carried out a series of workshops together with KPMG with the purpose of highlighting the employees' own
ideas for waste reduction, and it has turned out that their ideas were worth a fortune.
"Background and purpose"
The project "Waste reduction within the foundry and machine industry" was financed by Perspektivpuljen through the Danish Environmental Protection Agency's programme for clean products.
The foundry industry outweighs many other industries in the waste statistics, and in year 2000, Vald. Birn A/S disposed of approx. 22,000 tonnes of waste. The purpose of the project was to analyse the
possibilities of waste reduction from selected waste fractions within the foundry and machine industry through recycling a large part of the waste from the production processes for internal use and by
reducing overall waste quantities in general.
Vald. Birn A/S took the initiative to achieve waste reductions partly through developing and testing new technologies, and partly through involving and training employees to identify and promote new
improvement ideas.
"Survey"
Three technical pilot projects were launched. A programme was also launched on involvement of employees through training and changing their attitudes so they regard waste as a loss for the company and
bring forward their own ideas to recycle the waste in the production process.
The purpose of the technical pilot projects was to test whether the following ideas could be feasible:
- Separation of foundry sand as this waste product holds a high content of coal dust and clay particles that can be added to the foundry sand again through recovery of the extracted, dead material, thus
reducing the requirement for new coal and clay.
- Demolition of sand cores that are scraped due to damage etc. and adding these as new core sand in small amounts.
- Significant extension of the life time of cooling lubricant through establishment of a central handling and maintenance unit, thus reducing the requirement for cooling lubricant.
The main conclusions of the project were:
- The tests with application of a Trenso separation table for segregation of bentonite from dead foundry sand does not work optimally, for which reason Vald. Birn A/S will not go on with this
technology.
- Tests with recovery of core sand from demolition of discharged core scrap have been a success. Tests have been carried out with addition of up to 7% of recycling core sand in new sand without
affecting the strength or quality of the mould. An upper limit for addition of recycle sand has not been tested. The potential is that all unsmoked cores can be recycled.
- Tests with a central unit for maintenance of cooling lubricant have proven a success. The result has been an extension of the life of the cooling lubricant by a factor of four, corresponding to a reduced
consumption and quantity of cooling lubricant for scrap of 75%. At the same time, the number of man-hours required for maintenance was reduced correspondingly.
- Tests with involvement of employees for waste reduction have been a success. The participants have been strongly committed, and their ideas have helped reduce the figures in the waste statistics. As
an example, the employees came up with an idea for a sorting unit and have documented the loss of sand at the production lines via photos resulting in that the C and M fraction together has been
reduced from 49 to 25 kg/tonne tapped iron.
By carrying out the pilot projects as well as involving the employees and their ideas, Vald. Birn A/S has achieved a reduction in waste per tonne tapped iron of 14% which corresponds to 36 kg/tonne
tapped iron. For the quantity of tapped iron in 2004, this results in a reduction of 3,215 tonne waste.
Based on Vald. Birn A/S' waste disposal prices in 2004, the above reduction in waste corresponds to a saving of DKK 1.1 million. The value of the increased recycling ratio achieved in the same period
(from 72% to 97%) has not been included, which makes the waste disposal significantly cheaper for certain fractions.
If we assume that the reduced quantity of waste replaces corresponding repurchase of raw materials, the saving amounts to DKK 1.3 million.
All in all, an estimated yearly saving of DKK 2.5 million is achieved on solid waste. In addition, there will be the savings from implementation of the central KSM unit in the machine shop, which is expected
to amount to DKK 1 million yearly, when the unit is fully developed.
If the effort is compared to the reduction in quantity of scrapped clay-bound moulding sand, a 15% reduction has been achieved for these fractions. If this result is extended to Denmark as a whole, where
Støberiforeningen (a Danish association of foundries) estimates that 60-70,000 tonnes clay-bound core sand are scrapped by the foundry industry, this corresponds to a possible waste reduction of
9-10,500
tonnes per year nationwide.
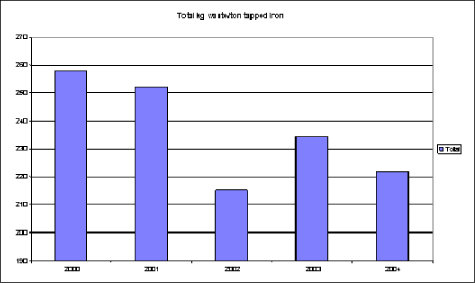
Project results
The tests of clay and coal recovery from filters in the sand towers show that the planned technique with vibration over a Trenso separation table cannot meet the requirements for separation of particles in the
requested grain size. The tests performed gave a 40% recovery of the potential, but the uncertainty in the test runs was too great. Vald. Birn A/S expects to find other technical solutions.
The test with demolition of core scrap and addition of new core sand in small quantities turned out to be a success. 99% of the core scrap demolished could be added as new sand, and tests were performed
where up to 7% addition of core sand did not cause production or quality problems. At the end of the project, approx. 5 tonnes of core scrap per week were recovered, corresponding to approx. 200
tonnes per year and Vald. Birn A/S anticipates being capable of increasing this quantity.
Setting up a central unit for handling and maintenance of cooling lubricants has turned out to work very satisfactorily. At the end of the project, three salvaging machines were linked to the unit and the life
time of the cooling lubricants had been extended from approx. two to nine months, leading to an approx. 75% saving on purchase and disposal of cooling lubricants. At the same time, it was stated that the
operation of the unit required fewer man-hours and machine stops for cleaning and maintenance.
The workshops for training and working with change of employee attitudes so that they regard waste as a loss for Vald. Birn A/S were very successful. Listening to the employees' ideas in respect of waste
reduction and recovery of waste in the production process yielded great results.
A visible result is the development in the quantity of sand on the floor along the seven production lines. The sand is removed by the cleaning team by means of a central aspirator unit. After the cleaning team
had focused on where the aspirator was used the most, they documented it via photos and the repair team is now capable of setting priority for work during the weekend. From having to vacuum 27 kg per
tonne tapped iron in 2000, the team now only vacuums 19 kg per tonne tapped iron.
"Other sources": www.birn.dk www.kpmg.dk
| Forside | | Indhold | | Forrige | | Næste | | Top |
Version 1.0 Februar 2006, © Miljøstyrelsen.
|