| Front page | | Contents | | Previous | | Next |
Substitution of Cobalt Driers and Methyl Ethyl Ketoxime
2 Air-drying systems
Coatings, which are able to dry by oxidative cross-linking, are classified as air-drying or oxidative drying coatings.
Air-drying coating systems contain binders such as oils, alkyds and epoxy esters, which are all based on vegetable
oils or vegetable oil derivatives. On a volume basis alkyds are far the most important of the air-drying binders.
2.1 Vegetable oils
Vegetable oil molecules are glycerides, which are constituted of glycerol backbones combined with different fatty
acids. The majority of the molecules are triglycerides with only small proportions of mono- and diglycerides. The
fatty acids present in vegetable oils have varying hydrocarbon chain lengths even within the same oil. The chain of a
fatty acid does commonly contain an even number of carbon atoms ranging from 10 to 20 including the carbon
atom in the acid group (-COOH). The chemical structures of vegetable oils, glycerol and fatty acids are
schematically indicated in figure 2.1.
The fatty acids combined with glycerol determine the specific properties of vegetable oils and as the fatty acid
combination differs from one type of oil to another so do the properties.
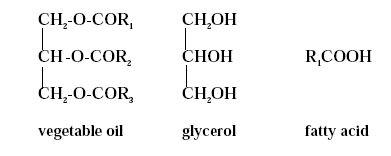
Figure 2.1 . A vegetable oil is a triglyceride, consisting of glycerol and fatty acids. The fatty acids are symbolised by R1, R2 and
R3 indicating that vegetable oil contains fatty acids with different chain length. The fatty acids can either be
saturated or unsaturated.
The fatty acids can either be saturated containing no double bonds or they can be unsaturated containing one or
more double bonds. The presence of double bonds makes the oils reactive as the double bonds are able to
polymerise (cross-link) when exposed to oxygen. This ability to cross-link makes unsaturated oils able to form a
solid, coherent and adherent film when spread on a surface and exposed to oxygen in the air.
The drying properties of oils depend on the degree of unsaturation. The more double bonds present in the oil the
better the drying properties. Oils are usually classified as drying, semi-drying or non-drying oils according to their
ability to dry when exposed to air. Over a period of time drying oils will form a tack free film, whereas semi-drying
oils form films that will never become completely tack free. Non-drying oils are unable to react to form a
cross-linked structure by oxidation as they mainly consist of saturated fatty acids, which have no drying properties.
The non-drying oil types or derivatives of non-drying oils are therefore not being used for air-drying binders.
Semi-drying oils, such as soybean oil, sunflower oil, tall oil or safflower oil contain acids with only one or two
double bonds. Semi-drying oils cannot be used unmodified in coatings. They are typically used for the manufacture
of air-drying binder such as alkyds and epoxy esters.
Drying oils are oils with a high degree of unsaturation, as they consist of glycerides of fatty acids containing two or
three double bonds. Linseed oil, tung oil, and oiticica oil are all classified as drying oils. Oils containing conjugated
unsaturated acid show a much higher reactivity and better drying properties than oils only containing
non-conjugated double bonds. Most of the oils are non-conjugated but tung oil and oiticica oil contain large
amounts of fatty acids with conjugated double bonds.
Drying oils, especially the refined ones, are able to form films in their unmodified form but only very slowly. In most
cases they are therefore modified to increase molecular weight and viscosity before using them in coatings to
improve as well drying time as the overall film forming properties. An increased initial molecular weight means that
less cross-linking is necessary to obtain a coherent film and therefore the drying time is reduced. The oils can be
modified in several ways either by thermal treatments, which polymerise the oil molecules, or by chemical reaction
polymerising the oil molecules with other compounds.
2.2 Drying mechanism
The drying mechanism for air-drying systems is described in general terms only as the drying mechanism of the
process is very complex. Although the principal reactions involved in the oxidative cross-linking are known, the
total mechanism is still not fully established. It is however accepted that the first steps in oxidative drying involve
hydroperoxide formation. This initial peroxide formation is followed by decomposition of peroxides to form free
radicals, which then initiate polymerisation, /2/3/4/. The chemical mechanisms presented are suggested in the open
literature and they are largely based on work with model compounds, which may not always be easily related to the
more complex polymer systems used in practice, /3/.
The simplest approach is to postulate oxygen attack at the site of the activated methylene, which is alpha to the
double bond (C=C) involving the formation of allylic radicals obtained by hydrogen abstraction. This gives rise to
peroxide formation. In the case of conjugated systems, such as tung oil, 1,4 cyclic peroxide is formed by oxygen
addition, /2/3/4/.
Once, a peroxide has been formed it dissociates into free radicals, which enable a series of further reactions to take
place. The peroxides decompose by dissociation of the O-O bonds leading to a variety of reaction products
including intermolecular linkage and a cross-linked film is obtained. The polymerisation mechanism for
non-conjugated fatty acids is presented below, /2/3/. The reactions are chain reactions which once started generate
more and more free radicals and peroxides leading to auto-oxidation, /5/. The overall effect of the reactions is that
the molecular size of the drying oil molecules is increased.
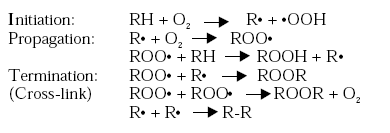
The termination reaction favours formation of polyperoxides, which subsequently decompose to polyethers. The
probability of chain termination is rather high for which reason the length of the polymerised chains is relatively
short, /2/3/. The rate of cross-linking does furthermore slow down as the cross-linking structure is built, due to
oxygen penetration of the coating film being increasingly inhibited /4/. The cross-linking reactions will though
continue very slowly within the dry coating film even years after application.
The process of oxidative polymerisation (cross-linking) is a rather slow process even for modified oil, as it normally
takes from twelve to thirty-six hours to form a tack free film, /4/. Organic metal compounds, driers, can accelerate
and modify these reactions. A coating that would take several days to dry will become tack free within a matter of
hours when the proper driers are present in the coating systems.
During oxidation, a great number of by-products are formed, notably ketones and aldehydes. These oxidative
by-products are responsible for the odour of oil containing systems, especially those containing drying oils or drying
oil derivatives.
2.3 Air-drying coating/binder types
To give an impression of the diversity of air-drying binders, different vegetable oils and binders that are commonly
used in air-drying coatings are described in brief in the following sections.
2.3.1 Vegetable oils
Vegetable oils have traditionally been used in a lot in paints, varnishes and printing inks because of their ability to
cross-link. The oils are though commonly modified before using them in coatings to improve their drying properties.
The most extensive use of vegetable oils within the coating industry is the manufacture of alkyd resins, ink vehicle
systems and other synthetic resins for air-drying coatings, /3/.
2.3.1.1 Refined oils
Raw vegetable oils produced by expression or solvent extraction contain variable amounts of non-glyceride
impurities, such as free fatty acids, phospholipids, carbohydrates, sterols etc. For many applications, e.g. alkyd
manufacture, these impurities are undesirable as they may affect the drying properties and pigment wetting
capabilities of the oil, /3/4/. Raw oils are therefore rarely used directly in coating formulations. They are usually
refined by treatment with acid or alkali to precipitate the impurities. As the refined oils also have a relatively slow
drying speed they are often modified either by thermal treatment or chemical modification, or by blending them with
synthetic resins, /3/.
2.3.1.2 Polymerised and oxidised oils
A partly polymerising or oxidising of vegetable oils leads to an increase in the molecular weight. The oil thus has an
increased initial molecular weight and fewer cross-links are required to form a coherent film. The drying time of the
coating is thereby reduced, /3/.
Isomerised oil is obtained by heating oil with an aqueous alkali solution hereby increasing the extent of conjugation
in unsaturated oils and making them more reactive and thereby improving their ability to cross-link when exposed to
oxygen in air.
Oils polymerised by heating without the presence of accelerators are called heat-polymerised oils, heat-bodied oils
or stand oils. Depending on the oil type the heating might be carried out in the presence of peroxides to improve the
cross-linking. The heating is continued until the viscosity has increased to the desired value, /5/. In the case of highly
conjugated oils the action of heat alone is sufficient to bring about a polymerisation. Even though the drying speed is
increased, stand oils do still have a rather slow drying speed but their levelling properties are improved, which is
also very important in many surface coating applications, /2/. Stand oils of drying oils can be used on their own in
coatings or they can be used for further processing, for instance alkyd production. If the oils are heated and
oxidised at the same time by blowing air through the oil they are called blown oils. The reaction may be catalysed
by the addition of metal driers, /3/4/.
Boiled oils are produced from linseed oil using one or more driers. They are traditionally processed by controlled
oxidation of raw linseed oils where metallic driers are used to accelerate the cross-linking. The oils are called boiled
oils even though the cooking temperature is below the boiling and decomposition point. By proper control of the
reaction, boiled oils with a wide range of viscosities can be obtained. Boiled oils are usually used in oil paints,
enamels and oil-based primers. Today boiled oils are though often a simple blend of stand oils and driers, /6/7/.
2.3.1.3 Linseed oil
Linseed oil is one of the most widely used oils in air-drying coatings. Linseed oil contains a high proportion of
unsaturated linoleic and linolenic acids, which give the oil good air-drying properties. Linseed oil can be used on its
own in coatings, but it is extensively used for the production of air-drying alkyd resins and urethanated oils, /3/.
Coatings based on linseed oil tend to yellow with time, due to the presence of linolenic acid. The more linolenic acid
present the more prone will the dry coating film be to yellowing, especially in dark places. Coatings based on
linseed oils or linseed oil alkyds are therefore mainly for exterior use.
2.3.1.4 Tung oil (wood oil)
Around 80 % of the fatty acid content of tung oil is conjugated eleostearic acid, which gives tung oil rapid air-drying
properties. The surface drying of tung oil is actually so rapid that it often dries with a wrinkled surface, /6/. Tung oil
is therefore rarely used on its own. It is often used in combination with hard resins as phenolic resins, rosin esters or
alkyds in oil based printing inks.
2.3.1.5 Oiticica oil
Oiticica oil contains a high proportion of the conjugated licanic acid. The oil gives quick drying coating films with
good gloss and adhesion. The films are more brittle and have a greater tendency to yellow than those of tung oil and
therefore oiticica oil is often blended with soya bean oil to improve both colour and film flexibility. Oiticica oil is
used in printing inks that are required to dry on non-absorbent surfaces. It tends to be used interchangeably with
tung oil in ink formulations, /3/4/.
2.3.1.6 Dehydrated castor oil
Raw castor oil is a non-drying oil, but is possible to convert into an drying oil by removing the hydroxyl group from
the fatty acid together with a hydrogen atom from the neighbouring carbon atom. This yields conjugated fatty acids.
The reaction produces two isomers of linoleic acids, one non-conjugated and one conjugated in the ratio of about
3:1. The drying speed of dehydrated castor oil is somewhere in between the drying speed of semi-drying oils and
drying oils. Dehydrated castor oil is rarely used alone but is often used for the production of alkyds and epoxy ester
resins, /3/4/5/.
2.3.1.7 Soybean oil and sunflower oil
These oils are very similar in fatty acid composition and are often used interchangeably. They are semi-drying oils,
mainly used in their refined form and especially for alkyd manufacture, /3/. They have a pale colour, making them
suitable for use in white coating systems and varnishes, /4/.
2.3.1.8 Safflower oil
This oil contains a higher proportion of conjugated fatty acids than both soybean and sunflower oils and has better
drying characteristics, but still classified as semi-drying oil. Safflower is mainly used in its refined form and it is used
instead of soybean or sunflower oils where better drying is needed. Safflower oil does like sunflower and soybean
oil provides non-yellowing alkyds.
2.3.1.9 Tall oil
Tall oil is not a "true" vegetable oil as it is obtained as a by-product from wood pulp production, but as it contains
unsaturated fatty acids it is able to air-dry like vegetable oils. Tall oils are today widely used for the production of
alkyds.
2.3.2 Alkyd binders
Alkyd is one of the most used binder type within the European paint industry accounting for approximately 25 % of
the total amount of consumed binders and at present they hold a majority share of the world market for
non-aqueous binders, /1/3/.
Alkyd resins are short branched polyester chains containing fatty acids. They are condensation products of polyols,
polybasic acids and vegetable oils or fatty acids. The properties and nature of the final alkyd are dependant on the
quantity, type and nature of the modifying oil, fatty acid or acid anhydride used as well as the processing conditions.
The presence of the oil provides alkyd binders with good pigment wetting properties and when the oil is
unsaturated good air-drying properties are provided as well. The polyester chain gives hardness and durability to
the film and improved drying speed, /5/. Alkyds may be further modified by reacting urethane, styrene, vinyl toluene
or silicone groups into the alkyd binder to provide specific properties. Most widely used for the production of
air-drying alkyds are linseed oil, soybean oil, tall oil, tung oil, and safflower oil. Dehydrated castor oil, linoleic acid
and linolenic acid are also used in the production of alkyds, /4/.
Alkyds are classified as drying, semi-drying or non-drying dependent on the oil type used for manufacturing the
alkyd. Alkyds containing more than 55 % w/w of oils are called long oil alkyds. Alkyds with oil content ranging
from 45-55 % w/w are classified as medium oil alkyds whereas short oil alkyds contain less than 45 % w/w of
vegetable oil, /3/4/7/. Short oil types dry fast by solvent evaporation but show limited cross-linking. Long oil alkyds
dry slower, but their final durability is much better due to better cross-linking, /2/. Air-drying alkyds do therefore
usually have an oil length greater than 45%, /5/.
The molecular weight of an alkyd is considerably higher than that of a vegetable oil, which means that fewer
cross-links are required before a coherent film is formed. Alkyd binders do therefore dry much more rapidly than
the corresponding vegetable oils. Addition of driers is though still needed to obtain a drying time, which is
acceptable for commercial coating systems.
Alkyds are very versatile in use and can be used in several coating types such as paints, enamels, stains, varnishes,
lacquers and printing inks. They can be utilised in a variety of applications both in decorative, industrial and
speciality coatings. Oil inks are formulated almost exclusively from long oil alkyds, /3/.
2.3.2.1 High solids paints
Alkyd binders for high solids paints are similar to those for conventional organic solvent-borne systems but they
have a lower molecular weight. This makes it possible to formulate systems containing less amounts of volatile
organic solvents and yet having appropriate viscosity. Solvent free high solids systems can be formulated by using
reactive diluents.
2.3.2.2 Waterborne systems
Alkyd binders for waterborne systems are made either by converting the resin into an emulsion with the use of
emulsifiers or by incorporating water-soluble and cross-linking groups in the binder; e.g. carboxyl groups
neutralised with ammonia or reactive amines, /2/.
2.3.2.3 Modified Alkyd Resins
Alkyds can be modified to have properties ranging from fast drying hard coatings to slow drying, soft and flexible
films, /3/. The properties of alkyds are relatively easy tailored to specific needs, as there are several parameters
available for adjustments (chain length of fatty acids, degree of unsaturation, number of free OH groups, branching
etc.).
Modified alkyds are made by grafting vinyl monomers (styrene, vinyl toluene, methacrylates etc.), by radical
mechanism onto unsaturated sites of the resin or by reacting free hydroxyl groups with silicone and isocyanates
(urethane alkyds), /2/. Modified alkyds are widely used in applications where higher weather ability and durability,
faster drying and higher gloss are desired than in conventional alkyd coatings, /1/. The higher average initial
molecular weight in the modified alkyds means an improved speed of drying. This especially accounts the surface
drying as the through-drying might take longer time due to the reduced levels of unsaturation in the alkyd, caused by
the copolymerisation, /3/. The modified alkyds are primarily used in industrial coatings.
Polyamide modified alkyd resins (thixotropic alkyds) are made by chemical reaction with specially designed
polyamide resins. This results in a jelly-like structured material, which breaks down under shear to a free flowing
liquid. Once the shear is removed the resin re-sets to a jelly. These resins form the basis of non-drip or thixotropic
paints. They are frequently used as blends, with unmodified alkyds or urethane modified alkyds, to impart structure.
They are used in air-drying decorative paints, where their rheological properties make them attractive to users of
do-it-yourself products, /3/.
2.3.3 Epoxy ester
The majority of epoxy ester resins are reaction products of an epoxy resin and a vegetable fatty acid combining the
ease of handling of alkyds with some of the film properties of epoxy paint. Like alkyds, epoxy esters are
characterised by oil length and oil type. All vegetable oils and fatty acids common to alkyd manufacture are also
used in epoxy ester manufacture. Both air-drying and stoving types of epoxy esters are used commercially, /7/.
Although epoxy esters have similarities with conventional alkyds, they generally offer films with better colour,
flexibility, adhesion and chemical resistance. Epoxy esters are less versatile in use than alkyds and more expensive,
/7/.
| Front page | | Contents | | Previous | | Next | | Top |
Version 1.0 December 2003, © Danish Environmental Protection Agency
|