| Front page | | Contents | | Previous | | Next |
Market information in life cycle assessment
4 Market-based system delimitation
4.1 Introduction
4.2 Scale and time horizon of the studied change
4.3 Market delimitation
4.4 Market trends
4.5 Production constraints
4.6 Suppliers/technologie s most sensitive to change
4.7 Environmental product declarations
4.8 Examples of the identification of affected processes
4.1 Introduction
The idea that market information is important in determining what processes to include in a product system was suggested already by Weidema (1993). Here it was suggested that the actual environmental impacts are most correctly modelled by using environmental data on the marginal technology, defined as the technology actually affected by a small change in demand (Weidema et al. 1999). As mentioned in footnote 10, we now refer to this technology simply as the “technology actually affected,” thus avoiding the term “marginal” as it may give rise to confusion due to its many different connotations in everyday-language. Also, compared to the procedure presented in Weidema et al. (1999), the procedure presented here is not only relevant for small (marginal) product substitutions, but has been generalised to cover also larger substitutions.
To build a model of a product system, it is natural to start with the process in which the reference flow occurs (see chapter 3). Each item in the reference flow is then linked to the next process both backwards and forwards in the life cycle. Backwards, the flow typically consists of intermediate products, components, ancillary inputs, and raw materials. Forwards, the flow may also consist of final products, products for reuse or recycling, and waste to treatment. To make it simple, we call all these flows “intermediate product flows”. Flows to the environment (environmental exchanges) are typically not included in the first description of a product system.
The purpose of the procedure presented here is to determine the process(es) that a specific intermediate product flow should be linked to, and which therefore should be included in the studied product system. It is for these processes that data on environmental exchanges are later to be collected. The overall uncertainty of a life cycle assessment will often be determined by what processes are included and excluded from the analysed product systems.
A product substitution (e.g. the choice of one chair design instead of another) will result in a change in demand for the intermediate products that enter into the process in which the substitution occurs (e.g. the steel and plastic components that are used by the chair manufacturer), and likewise in the demand for the further intermediate products backwards in the life cycle (e.g. the plastic raw materials). The procedure presented here identifies the processes that are expected to be affected by such a change in demand for a specific intermediate product.
A product substitution will also result in a change in supply of the intermediate products leaving the process in which the substitution occurs, and in supply of the further intermediate products forwards in the life cycle (e.g. the distribution, retail sale, use and disposal of the chair). To make the description less abstract, the explanatory text for the procedure only covers the situation where an intermediate product is followed backwards in the life cycle (identifying the effects of changes in demand). This is the most typical situation, since the functional unit is often determined in relation to the use phase, and most of the life cycle typically comes before this phase. However, the 5 steps of the procedure, the decision tree in figure 4.1, as well as the general concepts in the explanatory text, are also applicable when following an intermediate product flow forwards in the life cycle (identifying the effects of changes in supply). Examples of this are the investigations in section 4.8 of the consequences of a change in supply of dairy products and of waste treatment.
By the procedure presented here, one or more suppliers will be identified as being affected by a change in demand. The identified suppliers will typically use a specific technology and/or be located within a specific geographical region (since differences in market conditions and competitiveness typically depend on geographical and technological differences). The number of suppliers and the degree of detail of describing their technologies, depends on:
- the difference between the suppliers in terms of environmental impacts, since it may not always be necessary to distinguish between individual suppliers, when these use similar equipment and procedures,
- the scale and time horizon of the change, since large scale changes and changes over longer time spans may affect several separately identified suppliers or technologies, while for smaller and more temporary changes one specific supplier or technology may be identified as the one affected.
The implicit assumption of the presented procedure is that one or more suppliers have a fully elastic production and all other suppliers will not be affected by the changes in demand, i.e. having a fully inelastic production. If this assumption is regarded as too simple, the product system should include all suppliers that are expected to change, as well as all buyers that adjust their demand in response to changes in market price. This can be done either as separate scenarios or in the form of an average, weighted in proportion to the relative degree to which the processes are expected to be affected.
The procedure outlined in figure 4.1 consists of 5 steps:
Step 1: Identifying the scale and time horizon of the studied change Step 2: Market delimitation Step 3: Identifying the market trend Step 4: Identifying production constraints Step 5: Identifying the suppliers/technologies most sensitive to change
In the following sections, we will have a closer look at some of the theoretical issues involved in each procedural step. In section 4.8, we present a larger number of examples where the procedure has been applied in practice.
For the initial phases of a life cycle study, and for parts of the life cycle that are less important, the described procedure may be too elaborate and too demanding. Also, there may be situations where it is not possible to obtain the necessary market information. In these situations, the defaults in table 4.1 may be applied. The arguments for these defaults are given in the following sections.
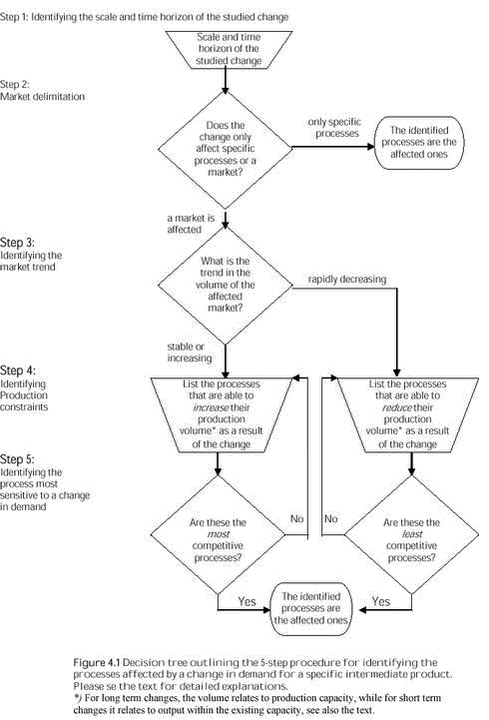
Click on the picture to see the html-version of: Figure 4.1
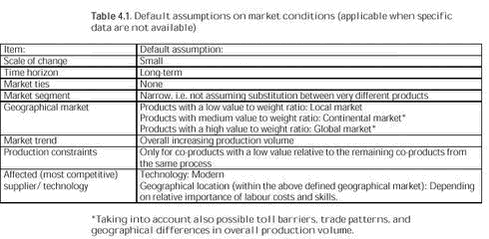
Click on the picture to see the html-version of: Table 4.1
4.2 Scale and time horizon of the studied change
As already pointed out in section 1.3, we distinguish between small (marginal) and large product substitutions (and changes in demand). For small substitutions, we further distinguish between short-term and long-term substitutions.
A product substitution is defined as small or marginal when it does not affect the determining parameters of the overall market situation, i.e. the direction of the trend in market volume and the constraints on and production costs of the involved products and technologies. The consequences of the substitution can thus be assumed linearly related to the size of the substitution and both an increase and a decrease in production volume will affect the same processes.
A product substitution is defined as large when it affects the determining parameters for the overall market situation, i.e. the direction of the trend in market volume and the constraints on and production costs of the involved products and technologies. The substitution may therefore in itself bring new suppliers, new markets, or even new products and technologies, into focus. It can therefore not be assumed linearly related to the size of the substitution and increases and decreases in the production volume may affect different processes. For large substitutions, it is therefore necessary to take the direction of change into account.
Large changes are typically seen when introducing new technology or new regulation on a significant market, e.g. if all cars were to be made from polymers and carbon-fibres in stead of steel, which among other consequences would have the market for steel turning from increasing to decreasing. However, many small changes may accumulate to bring about a large change. Therefore, even in studies of small changes it may sometimes be relevant to apply an additional scenario with the possible larger changes that could be the result of accumulated small changes. For example, even in a life cycle assessment considering a shift to polymers and carbon fibres for a single producer of cars, it may be relevant to investigate the possible consequences of other car producers following suit.
However, the typical substitutions studied by life cycle assessment are (unfortunately) not of such significant size. As shown by Mattsson et al. 2001), even a change in electricity demand of 1 TWh can still be regarded as small (marginal), since it affects the same technologies as a change of 1 kWh, the effects thus being linearly related to the size of the substitution.
As a default, when there is no information available to justify that the studied substitution affects the determining parameters for the overall market situation, it is therefore advisable to assume that the studied change is small.
A short-term substitution affects only capacity utilisation, but not capacity itself. A long-term substitution affects also capital investment (installation of new machinery or phasing out of old machinery). Large substitutions will always affect capital investment. But even small substitutions can seldom be isolated to the short-term, since each individual short-term purchase decision will contribute to the accumulated trend in the market volume, which is the basis for decisions on capital investment (i.e. long term substitutions). This is obvious in markets with a short capital cycle (fast turnover of capital equipment, as e.g. in the electronics and polymer industries) and in free market situations (where market signals play a major role when planning capacity adjustments), but it is also true for markets with a long capital cycle (as e.g. in the building and paper industries). Thus, the isolated effects of short-term changes (i.e. effects within the existing production capacity) are only of interest in markets where no capital investment is planned (e.g. industries in decline), or where the market situation has little influence on capacity adjustments (i.e. monopolised or highly regulated markets, which may also be characterised by surplus capacity). An example of a substitution with a short-term effect only would be an isolated decision to remove heavy metals from the components of a product, which – all other things equal – would not involve capital investment in the metal industry, since heavy metals are already being phased out.
As a default, when specific information is not available, it may be assumed that the studied change is long-term, since this is the typical situation.
If a long-term substitution is planned and announced well in advance of its implementation (as e.g. the installation of a new pipeline), it may involve only long-term effects, i.e. effects from installation and production on newly installed capacity. But such planned decisions are the exception. Most long-term product substitutions will also lead to some immediate short-term effects, i.e. affecting the existing capacity, while at the same time affecting investments decisions and in the long run affecting the production from this newly installed technology. Since the technology affected in the short term will often be old technology (the least competitive technology which typically has a low capacity utilisation compared to newly installed technology) while the technology affected in the long term will often be new technology (at least in expanding markets), long-term product substitutions may thus often be seen to affect a mix of technologies (Mattsson et al. 2001). However, the short- term effect will typically be negligible compared to the long-term effect, simply because the long-term effect is typically more permanent, while the short-term effect is only lasting until the next capacity change.
Example:
In a factory, several production lines may exist, some using an older technology, which is more polluting and more expensive to run, and some with a new technology (less polluting, less costly to run). Short-term fluctuations in demand will affect the capacity utilisation of the production line with the older technology (since this is the most costly to run), while the line with the new technology will be utilised as much as possible, and will therefore not be affected. If the demand increases beyond what can be covered by the current capacity, new machinery will be installed, and here the factory may choose to install the newest technology even though it is more costly to acquire, or it may decide to buy a cheaper, but more polluting technology. Whatever the choice, this can be said to be the long-term result of the change in demand and the additional environmental exchanges from the factory are now those coming from the newly installed machinery. It is therefore these exchanges that it would be reasonable to ascribe to the change in demand. Once the new machinery has been installed, further changes in short-term demand will still affect the older technology (since this is still the most costly to run). It is important to understand that even though the short-term fluctuation constantly will affect the older technology in the short-term, it is the accumulated changes in the short-term demands that make up the long-term changes, which eventually lead to the installation of the new machinery. The long-term effect of the demand is therefore the additional exchanges from the newly installed technology, and the short-term effects can be seen as a mere background variation for this long-term effect. Thus, the long-term effect should also be guiding for decisions that at first sight appear short-term, such as individual purchase decisions, and the product declarations that support such decisions.
4.3 Market delimitation
In most situations, the intermediate product is demanded on a market with several potential suppliers/technologies, which are adequately different to merit a closer investigation as to which ones are actually affected by the change in demand. The potential suppliers/technologies must be identified in terms of those who (can be expected to) deliver to this market. The market in question is identified by the obligatory product properties and the geographical and temporal market boundaries, i.e. in parallel to the first two steps of the procedure described in chapter 3 (actually described already in section 2.1).
As a default, when no other information is available, narrow market segmentation may be applied, i.e. not assuming substitution among very different products, since this reduces the size of the possible error (assuming a wide market segment implies the inclusion of very different processes, compared to those within a narrower segment).
In the early presentation of this procedure (Weidema et al. 1999), the need for geographical delimitation of the market was not adequately described, which caused some confusion as to the correct delimitation of e.g. the aluminium market. Ekvall et al. (1998) assumed the existence of a European market for aluminium, implying that an additional demand for aluminium in Sweden would lead to an increase in European production capacity. In response to this, Nordheim (1999) pointed out that there is no such thing as regional markets for aluminium, i.e. that aluminium should be regarded as a global commodity, and the affected aluminium production therefore should be determined on a global market, while the electricity source for this aluminium production will be supplied from several regional electricity markets, one for each of the aluminium production sites where capacity will be adjusted, see also the elaboration on aluminium in section 4.8.
As a default for geographical segmentation, the value to weight ratio of the products may be applied, being properties that are practically always known and somewhat related to transport distances (see Weidema et al. 2003b), thus being indicative of geographical market boundaries. By assuming a local market for products with a low value to weight ratio, a continental market for products with medium value to weight ratio, and global markets for products with a high value to weight ratio, the possible error is minimised. Gielen (1998b) argue that for most bulk materials, Europe can be regarded as a closed economy. However, when available, knowledge should be applied regarding toll barriers, trade patterns, and geographical differences in overall production volume (such as for products that are only produced in certain locations or where price differences are large between different producing countries), since this can seriously affect the actual market boundaries.
In some situations, the whole procedure may be cut short here, namely when only one supplier is possible, or a group of specified suppliers can be identified as the ones affected. This is the case if:
- the decision-maker for the study is expecting to control or influence the production volume of a specified supplier or group of suppliers, e.g. by contract (see Kåberger & Karlsson 1998), or
- two or more companies are tied so closely together in a supply chain that the production volumes of the specific suppliers fluctuate with the demand of the specific customers.
Many examples can be found of the latter situation, especially:
- When products have a low price compared to their weight, so that transport costs prohibit all other than the local producers, as e.g. for the supply of straw for heat and power production, where only the farmers closest to the power plant will supply the straw. Other examples of this can be found in the forestry sector and the building- and glass-industries.
- When two or more companies are tied together by tradition, or when a supplier has developed its product to meet specific demands of the customer.
- When the choice of supplier is not subject to normal market conditions.
If a specific supplier (or group of suppliers) is identified as the one affected, it may be useful to justify that the production volume of this process is actually able to change. For this purpose, step 4 in the procedure (section 4.5) may be applied.
The procedure can only be terminated here if the production volume of the specific suppliers is actually expected to change as a result of the studied product substitution, i.e. as a result of a change in demand for the intermediate product. If the change in demand is transferred on to other suppliers of the intermediate product, the production volume of the specific supplier will not change. This may be the case in spite of close relations between supplier and customer, even in spite of ownership relations or sole-supplier-status, i.e. it is not the closeness of the relation, which is important, but whether the overall production volume of the supplier is actually expected to be affected.
An example of this is in-house electricity production. If the in-house production fluctuates with in-house demand and thereby does not affect the production volume of the general electricity market, then the in-house production can be regarded as the affected electricity source for the in-house demand. However, if the in-house production takes place on normal market conditions, and the in-house production does not fluctuate with in-house demand (even when the company is closed), then the electricity supply for the in-house demand must be regarded as coming from the general electricity market, and not from the specific in-house production.
This also means that a consequential, market-based life cycle assessment will only give credit for - and incentive to - a shift to specific products or suppliers with environmentally more preferable technologies, e.g. "green electricity", when this shift is actually expected to lead to an increase in the capacity of the "green" technology. If the shift only pretends to be an improvement, and no change is expected in the composition of the overall output, no credit is given.
However, the effects of a shift may be delayed, so that the expected increase in the “green” technology will only appear after some time. For example, the production of ecological foods cannot react immediately to a change in consumer demand due to the time it takes to convert the production facilities to ecological production. In such instances, a demand for “green” products should still be credited for its long-term influence on the production capacity of the environmentally preferable technology.
Also, the effects of a shift may be indirect, via the political signal that it sends. For example, a constraint on a specific “green” product may be overcome, e.g. by political intervention or because a private company takes up the challenge, as a result of a consistent unsatisfied demand for this product. Likewise, a consumer boycott of a particular product may be followed up by political action or “voluntary” changes in company behaviour that limits the production beyond the effects of the boycott itself. More speculatively, it can be argued that the credit for a “green” product can be so valuable to the buyer that this alone could lead to a situation in which a constrained market for a “green” product is kept artificially sub-optimised (see Ekvall et al. 2001).
Since such indirect effects may be controversial and difficult to predict, it may be preferable to include them in separate scenarios. It should also be taken into account that such indirect effects are often “one-time-only” effects, e.g. political intervention that shifts a constraint from one level to another. After adjusting to the intervention, the situation finds a new equilibrium at the new level of the constraint.
As a default, when there is no information available to justify that a specific supplier (or group of suppliers) will be the one affected, it is advisable to assume that a market will be affected. This is the typical situation, and by this the burden of the proof rests on the companies having established such close market ties, and therefore have the best access to the information on these. The technology that will be affected at different suppliers may often be the same modern technology, even though they may currently have very different technologies installed (e.g. a company which has been in operation for a long time may be dominated by older production lines, while a factory that has recently entered into the market may on average have a more modern technology). In a consequential, market-based life cycle assessment, both suppliers will appear with the same modern technology, since this is what will be affected by a change in demand. Thus, the company with a longer history will not be punished for its historical investments, nor will the newcomer obtain any advantage from having avoided such a burden of history, as would have been the case if an average, attributional approach had been followed. Instead, the consequential approach will give credit for any supplier that makes an environmental improvement, no matter how good or bad his current situation.
This may raise the concern that such an approach will not give any incentive to the older factory to improve the more polluting parts of its current production equipment, since the factory is anyway judged only on the basis of its new installations. However, the older factory may actively utilise its larger improvement potential by linking investments in new capacity to improvements in its older production lines. Any company may in fact make such linking (cross-subsidising) of two separate productions; it is not necessary that the two production lines be inside the same company, as long as the link is binding and verifiable (e.g. contractual). To be credible, the existence of such links should preferably be verified by an independent third party.
An example of such linking, although with a different objective, namely to avoid that the premium from the sales of a “green” product cross-subsidises other less environmentally preferable productions, is that of naturemade-Star electricity: This label explicitly requires that the additional income from the premium on the labelled electricity is used to increase the environmentally preferable electricity production from renewable sources and to improve the environmental performance of the existing power plants (http://www.naturemade.org/d/zertifizierung/). Specifically for hydropower, the label requires (according to Frischknecht 2001) that the additional revenue, about 0.03 EUR per kWh, from selling labelled electricity, is used for (percentages from one specific utility, as example only):
- additional distribution and marketing for labelled electricity, directly & through local utilities (31%),
- a promotional model (Fördermodel), implying that per kWh naturemade-star hydro power, 0.025 kWh new naturemade-star renewable electricity (wind, biomass, photovoltaics) must be sold (47%),
- ecological improvements at the power plant (22%).
4.4 Market trends
Within the identified market, not all potential suppliers/technologies will actually be affected by a change in demand. For short-term changes (see also section 4.2), the affected suppliers will typically be the least competitive (often using older technology), since it is mostly these suppliers that have capacity available. For long-term changes, the affected suppliers depend on the overall market trend. In a market that decreases (at a higher pace than what can be covered by the decrease from regular, planned phasing out of capital equipment) the affected suppliers will typically be the least competitive. If the market is generally increasing (or decreasing at a rate less than the average replacement rate for the capital equipment), new capacity must be installed, typically involving a modern, competitive technology.
Therefore, it is important to identify the market trend (“Is the market increasing or decreasing?”) especially for long-term changes involving capacity adjustments.
It follows from the above distinction, that if the general market volume is decreasing at about the average replacement rate for the capital equipment, the effect of a change may shift back and forth between suppliers with very different technologies, which makes it necessary to make two separate scenarios. This may be relevant for a fairly large interval of trends in market volume, since the replacement rate for capital equipment is a relatively flexible parameter (planned decommissioning may be postponed for some time, e.g. by increasing maintenance). In general, the replacement rate for production equipment is determined as the inverse of the estimated lifetime of the equipment.
Note that it is the overall market trend, which is of interest, and not the direction of the specific demand studied. This is because - as long as the overall trend in the market is not affected – it is the same suppliers that will be affected by an increase in demand and a decrease in demand.
Example: In comparing paper and textile tablecloths, it is the same modern, competitive technology that will be affected in both the paper and the textile product system, even though a shift from paper to textile will lead to a reduction in demand for paper and an increase in demand for textile, and vice versa. This is because the reduction in demand for paper or textile resulting from the shift will not affect the overall market trend for paper and textile, which will still both be increasing. What will be affected is only the size of the increase, i.e. the amount of new technology that will be installed in the two systems.
Market trends are typically obtained by combining statistical data showing the past and current development of the market and different forecasts and scenarios (see also chapter 6). Sector forecasts are typically available from national and supranational authorities, while more product specific forecasts are available from industrial organisations.
As a default, when information on market trends is not available, an increasing market may be assumed, since this is – in spite of obvious exceptions - the general situation for most products, due to the general increase in population and wealth.
4.5 Production constraints
As already discussed in section 2.2, a supplier or an entire technology can be constrained in its ability to change its production volume in response to a change in demand, for one or more of the following reasons:
- Market failures, and regulatory or political constraints.
- Constraints in the availability of raw materials, waste treatment capacity, or other production factors.
- If the change in demand is for a co-product, and the production volume of the co-producing process determined by one or more of the other co-products. See section 5.4 for a precise procedure for identifying which co-products determine the production volume of a co-producing process.
See section 2.2 and 4.8 for examples.
The situation of a declining market, see section 4.4, can be regarded as a constraint on modern technology, since new capacity is not being installed, limiting competition to those suppliers already present.
As any other market condition, production constraints may change: over time, depending on location, and depending on the scale of change. Thus, it is important to note the conditions for which the constraints are valid. Especially, when studying long-term changes (the typical situation for life cycle assessments), it should be avoided that a process is excluded from further considerations because of constraints that only apply in the short term (in day-to-day operations, many constraints apply, e.g. in raw material availability and production capacity, that are irrelevant when considering long-term changes).
As a default, in case of missing information on production constraints, we recommend to assume that there are none. Unjustified exclusion of processes is thereby avoided. If a constrained process is thereby included, this will normally be discovered in the next step in the procedure (see section 4.6).
If all suppliers to a specific market segment are constrained, or if one or more production factors are not fully elastic, a change in demand will lead to a change in market price and a consequent adjustment in demand (i.e. a behavioural change). This adjustment will be accommodated by the customer(s)/application(s) most sensitive to changes in price, measured in terms of their demand elasticity (i.e. their relative change in demand in response to a change in price). This change must then be followed forward (downstream) in this lifecycle.
4.6 Suppliers/technologie s most sensitive to change
Among the unconstrained suppliers/technologies, some will be more sensitive to a change in demand than others.
As already discussed in section 4.4, the most sensitive supplier/technology depends on the temporal horizon (short-term/long-term) and the current market trend. For long-term changes in an increasing market, the most sensitive supplier/technology is identical to the most competitive, while in a rapidly decreasing market and for short-term changes, the most sensitive supplier/technology is the least competitive.
Competitiveness is typically determined by the production costs per unit. For capacity adjustments it is the expected production costs over long-term that matters. The distinction between constraints (section 4.5) and costs is not completely sharp, since some constraints may be translated into additional costs and some costs may be regarded as prohibitive and therefore in practice function as constraints. However, if not taken too strictly, the distinction is useful for practical decision-making. Also the definition of costs itself is not sharp, since concerns for flexibility (as a concern for future costs), environmental costs and other externalities – whether monetarised or not - may enter the decision-making process. When predicting the actual decisions with regard to changes in capacity or capacity utilisation, it is therefore necessary to include all those constraints and non-monetarised costs which are relevant to the decision makers, but on the other hand not such which are not going to influence the actual decisions. The kind of costs included may also vary depending on the interests of the decision makers, e.g. private investors may place less emphasis on environmental externalities than a public investor (Frischknecht 1998).
Thus, the most sensitive suppliers/technologies are determined from the production costs, while taking into account constraints and non-monetarised costs as perceived by those who decide about the change in capacity (long-term) or capacity utilisation (short-term). The important point is to model as closely as possible the actual decision making context.
As a default, when data cannot be obtained, it may be assumed that modern technology is the most competitive and the oldest applied technology is the least competitive. With respect to geographical location, it can be assumed that competitiveness is determined by the cost structure of the most important production factor (labour costs for labour intensive products, else energy and raw material costs). When comparing labour costs, local differences in productivity and labour skills should be taken into account.
4.7 Environmental product declarations
13As a specific application of environmental data from the product chain (life cycle data), there is some ambiguity in the way Environmental Product Declarations (EPDs) are viewed by the public and by experts in the field of labelling and declarations. On the one hand, EPDs are seen as declarations of the past environmental impact that the declared product has had up till the point of purchase, and sometimes including the expected use and disposal phases, but not specifically intended to indicate the expected environmental consequences of buying the declared product, in parallel to a declaration of contents, which does not indicate the expected composition of tomorrows product. On the other hand, EPDs are seen as a means for the customer to influence the environmental impacts of the purchased products, which exactly places a requirement on the EPD that it reflects the expected environmental consequences of buying the declared product compared to not buying it.
These two views on EPDs are not necessarily in conflict, since in some cases the environmental impacts from buying an additional unit of a product may be expected to be identical to the past environmental impacts caused by a unit of the same product. Intuitively, this expectation appears justified, since one would expect that buying an additional unit of the declared product would lead to an equivalent increase in production of this product by its immediate supplier, and in the long term an increase in the production capacity in the current supply chain. In many cases this may in fact be the case, and a declaration based on data from the current supply chain can then be regarded as both useful for the customer and beneficial for the environment.
However, two conditions must be fulfilled for the expectation to be true, namely: 1) that the production capacity in the supply chain is unconstrained (section 4.3), and 2) that the market is not declining (section 4.4).
In so far as these two conditions are not fulfilled, the inclusion of data from the current supply chain into the EPD may be seen as deceptive, as they may mislead the customer as to what are the actual consequences of the purchase. A few examples will illustrate the need for requiring the two conditions to be fulfilled before including data from the current supply chain into EPDs. Also, possible ways of avoiding misleading declarations are discussed in the following.
In Europe, some sources of electricity, notably hydropower and nuclear power, are subject to either physical or political constraints on their capacity. This implies that the production capacity cannot increase as a result of an increase in demand. An EPD based on current data for these sources of electricity will therefore obviously be an attribution of past environmental impacts rather than a reflection of the consequences of an additional demand. Therefore, such an EPD should be issued with an appropriate warning that it should not be applied in a comparison with EPDs of other sources of electricity in the context of a purchase decision aiming at choosing the electricity source leading to the lowest environmental impact.
In spite of this, there are examples of EPDs of hydropower presented to the public without such warnings, in a way that could lead the customer to think that they reflect the environmental consequences of buying the declared electricity. One such example is the EPD of hydro power electricity from the Lule river (SEMC 1999), which is published without any warnings on the limitations of its applicability, and even on a web-site where you can find statements such as: “Environmentally sound procurement is probably one of the most important applications of EPD‘s” and similar statements (http://www.environdec.com/eng/summary/key_issues.asp, latest visited 2001.08.15). Although not explicitly placed as an information for purchase decisions, e.g. in the context of increasing a customers purchase of “green electricity,” it still appears misleading to present the declarations without a specific warning that they should not be used for comparisons with other equivalent products. The Swiss naturemade-star label described at the end of section 4.3 demonstrates that there are other options available.
Besides physical and political constraints as in the above electricity example, constraints may also be found in relation to co-products, and the use of allocation procedures (as opposed to system expansion, see chapter 5) may therefore lead to similar misleading results as the ones shown in the above case. In fact, capacity constraints on specific raw materials or technologies are such a widespread feature in most supply chains, that the two above conditions are seldom fulfilled for all parts of a product chain. This means that in most cases where EPDs are based exclusively on data from the current supply chain, there is a risk that the declarations may be misleading14.
In Europe, the market for ammonia is declining, mainly due to political constraints on the use of nitrogen fertiliser for environmental reasons (see section 4.8). The variations in environmental impacts of ammonia production may be illustrated by the differences in energy consumption per ton of ammonia between a modern combined plant in Western Europe, at 29 GJ/ton (EFMA 2000), and an old plant in Eastern Europe producing at 48 GJ/ton (Patyk & Reinhardt 1997). Considering an EPD on a nitrogen fertiliser produced on the basis of supplies from the modern plant, the inclusion of environmental data from this immediate supplier would not reflect the environmental consequences of buying the declared product. Since the market is declining, no new capacity is being installed, and the purchase of the declared product therefore does not lead to increase in production capacity for this environmentally preferable product, but rather to postponing the decommissioning of an old plant with poor environmental performance. In fact, the declining market may be seen as a special kind of the constraints on increases in production capacity that we encountered in the electricity example. Thus, to bring the declaration in accordance with reality, i.e. to reflect the consequences of the purchase of additional nitrogen fertiliser, the EPD would have to include the environmental data for the old Eastern European plants that would actually be affected by the purchase decision. To avoid this situation, there is another option for the producer of nitrogen fertiliser: To bring the reality in accordance with the declaration. This could be done by creating a separate market for “green” ammonia, i.e. ammonia from modern plants with low energy consumption, etc. If the producer of nitrogen fertiliser placed a requirement on the ammonia supplier(s) to increase the production capacity in proportion to the sale of declared ammonia (somewhat in parallel to the promotional model described above for electricity), the consequences would be that decommissioning of old plants in Eastern Europe would be speeded up, and the declared ammonia would now really be produced on a modern plant, the data for which could then be safely used in the EPD
In conclusion, there are three ways to avoid the problem of misleading EPDs due to system boundary choices:
- Issue the declaration with a warning: The EPDs can be issued with a warning that they should not be used for comparisons with other equivalent products. However, this would then not provide any decision support to the customers.
- Bring the declaration in accordance with reality: The EPDs can be produced under the application of system boundaries that reflect the consequences of the purchase decision, i.e. market-based modelling.
- Bring reality in accordance with the declaration: The constraints on production capacity can be overcome, e.g. by creating a separate market for the environmentally preferable products, or by a promotional model (as illustrated by naturemade-star), so that the immediate supplier providing the data for the EPD also becomes the supplier affected by the purchase decision.
It should be noted that the background for an EPD based on market-based modelling might be more difficult to communicate to the consumer, since the market-based product system is less intuitively (physically) connected to the product. For example, the overall volume of milk production being constrained by quotas (as is the case in Europe) means that a purchase of 1 litre of milk does not lead to more production of milk, but to less sales of milk for the least profitable application (typically milk powder). Thus, a market-based EPD would not include the agricultural production, since this cannot be changed by the purchase of the declared product. Nevertheless, the consumer may wonder: “This litre of milk I have in my hand must have come out of a cow. Why is the cow not part of the life cycle?” It may be difficult to communicate that buying the milk just means that someone else will not be able to buy it, but that its production remains unchanged. This is further complicated by the fact that the consumer may actually influence the agricultural production even when the overall production volume is constrained, namely by buying ecolabelled (ecological) milk. Such a purchase will (eventually) lead to more production of ecological milk and less production of non-ecolabelled milk for milk powder, which means that a market-based EPD of ecological milk would include the difference between the ecological and non-ecological agricultural production.
4.8 Examples of the identification of affected processes
We have applied the above procedure to a number of products, to show the different variations and to demonstrate the practicability of the procedure. The procedure has been applied in different degrees of detail, thus also reflecting that the same degree of detail is not always necessary. The degree of detail required in a specific study will depend on the importance of the specific process in that study and the degree of difference between the possible processes.
It can be seen from the examples that the affected suppliers/technologies are often very different from the corresponding average supplying the market. Thus, only in exceptional cases can average data be used as proxy data, when market-based data are not available. This may e.g. be the case when the market in question is supplied exclusively by one main, slowly developing technology. In most other situations, it is preferable to make one or more estimates of the affected process, based on the available data. If you have data for a market average, the market range may be estimated (see Weidema et al. 2003b) and the affected process can then be assumed to be at one of the ends of this range, depending on realistic assumptions with respect to the items listed in table 4.1. When relevant, several alternative scenarios should be included to reflect the limits of knowledge.
The examples provided below are listed in increasing order after their NACE-code. References are provided for each step in the procedure. Unless otherwise stated, the identification is valid for small (marginal), long-term changes in the years 2000-2010. Some examples have been worked out in 1998 and have not been updated since, although more recent data than cited is likely to be available at the time of print. In general, the examples should be used with care, as they are intended primarily to illustrate the principles of the procedure, not as final conclusions or default data.
When applicable, specific data for modern technologies in Europe may be available in the form of reference documents from the European IPPC Bureau (http://eippcb.jrc.es).
Agricultural crops in general (NACE 01.1) Market ties: - Market segment: - Geographical market: EU, due to border tariffs Market trend: Increase (FAOSTAT) Production constraints: Limits on fertiliser per ha in some areas. Some crops are regulated by quotas ( Affected supplier/technology: Current suppliers, adjusting yield per ha by using additional fertiliser. When this is not possible, or for larger changes, the crop that will be affected in Europe is barley, since this is the crop with the lowest gross margin (Danmarks Statistik 1992, 1997a). This is confirmed by the expectations of the European Commission (1997c) that the crop most affected by changes in the amount of set-aside area is barley. The change in production of barley will then cause adjustments in productivity of other cereals, which can substitute as fodder, notably wheat and maize. The marginal production of wheat will under these assumptions take place in a grain-dominated rotation on mineral soils, since this is where the marginal cost of increasing the yield of winter wheat by the use of increased nitrogen-fertilisation is the lowest (Statens Planteavlsforsøg 1997).
Fodder protein (NACE 01.11)
Market ties:- Market segment:- Geographical market: Global Market trend: Increase Production constraints: Soy bean import from USA temporarily hampered by disagreements over genetically modified crops. Protein by-products from industry constrained by demand for the main products. Affected supplier/technology: Soy bean (USA or Brazil). This conclusion is based on calculations (by Mikkel Overvad of DLG fodder wholesalers) using the linear programming tool “Bestmix” applying current prices and constrained supplies of food industry by-products. This can be explained by the fact that soybean is the only protein crop (aside from grains) for which the protein is the main product. Some substitution between grain and protein concentrates is possible, as determined by their relative prices. However, within the next 10 years, the price of soybeans is expected to be well below the price of grain.
Fodder energy (NACE 01.11)
Market ties:- Market segment: Energy rich part of the diet (basic energy requirement will be covered by roughage). Geographical market: Global Market trend: Increase Production constraints: None. Affected supplier/technology: Wheat (or barley, see above). This conclusion is supported by calculations (by Mikkel Overvad of DLG fodder wholesalers) using the linear programming tool “Bestmix” applying current prices and constrained supplies of food industry by-products.
Meat (NACE 01.2)
Market ties:- Market segment: Not requiring meat from a specific type of animal (typically for minced meat). Geographical market: Europe Market trend: Increase Production constraints: Meat from milking cows constrained by determining by-product (milk). Affected supplier/technology: Pork production (as production costs are lower than for beef cattle).
Wood for fuel (NACE 02.01)
Market ties:- Market segment: The supply and demand of wood is not as strongly connected as for many other materials, because of the long production time. Fuelwood is usually the by-product of construction wood, produced by premature thinning-operations of the wood-stands. Fuelwood can be produced from wood-diameters as small as 5-6 cm. The smallest parts are defined as wood residues, since they have no alternative, commercial use. Diameters from 10-11 cm can be sold for production of pulp. Geographical market: Local Market trend: Increasing, but decreasing compared to the expected supply of small dimensioned wood (FAO 1999), which means that the alternative fate for the small-dimensioned wood is to be left to decompose in the forest ecosystem. Production constraints: None Affected supplier/technology: Local wood-residues
Wood for pulp (NACE 02.01)
Market ties:- Market segment:- Geographical market: Regional Market trend: Increase Production constraints: None Affected supplier/technology: Local small-dimensioned wood (diameters from 10-11 cm upwards).
Crude oil (NACE 11.1)
Market ties:- Market segment:- Geographical market: Global Market trend: Increase Production constraints: None Affected supplier/technology: Heavy crude from Venezuela or Middle East, as they are the most competitive sources (those with the lowest extraction costs), and therefore are expected to increase their share in the global supply from 30% in 1991 to 45-57% in year 2010 (IEA 1994).
Aluminium (NACE 13.2)
Market ties:- Market segment:- Geographical market: Global (Schwarz 2000) Market trend: Increase (Schwarz 2000) Production constraints: None Affected supplier/technology: Hall-Heroult with pre-baked anodes and point feeders (Gielen 1998a, Schwarz 2000). Separate electricity market: The aluminium production is unusual in being so electricity demanding that the localisation of the production plants is to a large extent determined by the availability of cheap sources of electricity. Thus, new smelters are typically placed in areas with unutilised hydropower and unutilised natural gas which is currently flared in connection to oil extraction. For example, recent expansion in smelter capacity has taken place or is planned in Iceland (hydropower and geothermic energy) and in Africa and the Middle East (hydropower and waste natural gas from oil extraction). Both the historical statistics published by the International Primary Aluminum Institute, and the projections for 2004 (Aluminum Association 1999) show that the high share of hydropower (56%) for primary aluminium production is surprisingly stable over time. Out of the publicly announced new plants, 57% is expected to be based on hydropower, 14% on natural gas and only 29% on coal (Aluminum Association 1999). Thus, the overweight of hydropower that has been prevailing in the average attributional-LCA data for aluminium production will also be the result of a market-based LCA-data for aluminium; see also modelling by Schwarz (2000).
Copper (NACE 13.2)
Market ties:- Market segment:- Geographical market: Global Market trend: Increase (USGS 1999, 2001) Production constraints: Pyrometallurgy constrained to sulfide ores and copper scrap. Some hydrometallurgical processes are also constrained to specific ore types. Affected supplier/technology: Modern, raw material flexible (Caspersen 1998): Most recent plants built have been with solvent-extraction-electrowinning (a hydrometallurgical process) and 30% of new plants are expected to be of this type. Of the pyrometallurgical processes, for sulfide ores, the cheapest and most flexible technology that give an adequate quality is INCO/Outokumpu flash smelting with an energy consumption below 8.4 MJ/kg Cu. The Noranda process may compete in terms of energy consumption, but gives a lower quality and leaves more copper in slag.
Cadmium, Mercury, Lead (NACE 13.2)
Market ties:- Market segment:- Geographical market: Virgin material global; recycled material regional Market trend: Decrease for cadmium and mercury (USGS 2001). For lead, the consumption increases, but mine production is stable or decreases as lead recycling is growing (ILZSG 2001). All three metals are co-products from polymetallic mines (zinc, gold, silver, copper) where demand for the co-product determines the output. Production constraints: None Affected supplier/technology: Waste deposits.
Vegetable fat (NACE 15.4)
Market ties:- Market segment: No specific fatty acid composition requested. Geographical market: Global Market trend: Increase (FAPRI 2000) Production constraints: Soy oil constrained by demand for its co-product soy protein. Affected supplier/technology: Rapeseed (canola) oil from EU or Canada (Vis 1998, European Commission 1997c, FAPRI 2000).
Dairy products (NACE 15.5)
Market ties: Suppliers are often bound by contract to a specific dairy. Market segment- Geographical market: Europe Market trend: Small increase in Europe (European Commission 1997d), stable in Denmark (Fødevareministeriet 1996). Production constraints: Milk production is constrained by quotas (European Commission 1997d), which means that the overall production volume is not sensitive to changes in demand. Thus, a change in demand will affect that application of milk, which is most sensitive to changes in supply. Affected outlet/technology: Skimmed milk powder and butter, being the outlets with the lowest profit margin (Skak Jensen 2001). The underlying cause for this is that these products do not demand sophisticated skills or technology and are therefore produced many places. Furthermore, these products store well and are subject to EU interventions. A change in supply of skimmed milk 72 powder and butter are not expected to lead to substitutions on the world market, since the consumption will be regulated through adjustments in prices. It should be noted that purchase of ecolabelled (ecological) milk will (eventually) lead to more production of ecological milk and less production of non-ecolabelled milk for milk powder and butter, while the purchase of non-ecolabelled milk just leads to less non-ecolabelled milk powder and butter. The net effect of choosing between labelled and nonlabelled milk is thus the difference between the two forms of agricultural production.
Wood and products of wood (NACE 20)
Market ties:- Market segment:- Geographical market: Depending on product requirement. Market trend: Increase Production constraints: None Affected supplier/technology: Modern, often local: Drying plants with variable speed heat pumps (Hekkert & Worrell 1998).
Pulp, paper, board (NACE 21.2)
Market ties:- Market segment:- Geographical market: Local to regional, due to low value compared to weight. (Jordbrugsdirektoratet 1994, Danmarks Statistik 1997b, Lind 1998, and the references under ”market trend”). Market trend: Increase (Joint ECE/FAO Agriculture and Timber Division 1996, FAO 1998, FAO 1999). Production constraints: Recycled fibres constrained by availability. Affected supplier/technology: Local, modern, based on softwood and light hardwood. The different pulping technologies have different demands for the raw material, depending on the amount of resin and the type of fibres (Tsuomis 1991, Bergstedt 1994). The neutralsulfite-process and the alkaline-process are best suited for broadleaved species; the alkaline-process can alternatively use straw. The sulfite- and the sulfate-processes can both use spruce and light broadleaves, and the sulfate-process can use pine too. Because of economy of scale, new plants are rarely built in Scandinavia or Germany (Karlson 1998) and instead existing plants are enlarged to meet the increased demand. Of historical reasons most paper plants in Germany use the sulfite-process, whereas most plants in Sweden use the sulfate-process. Since many of the trees in the new, fast-growing plantations in New Zealand and Asia consist of pine, for which the sulfate-process is best suited, this technology will most likely prevail for new plants in these areas.
Propylene (NACE 23.2)
Market ties:- Market segment:- Geographical market: EU Market trend: Increase Production constraints: Output of propylene from steamcracking constrained by relatively slower growth in demand for the co-product ethylene (Joosten 1998). Affected supplier/technology: Fluid catalytic cracking off-gas cleaning (Joosten 1998).
Ethylene (NACE 23.2)
Market ties:- Market segment:- Geographical market: EU Market trend: Stable to increase Production constraints: None Affected supplier/technology: Steam cracking of LPG or gas oil (Gielen et al. 1996).
Chlorine (NACE 24.13)
Market ties:- Market segment:- Geographical market: Europe Market trend: Decrease (van Santen 1998b) Production constraints: None Affected supplier/technology: Old technology (mercury process).
Chlorine (NACE 24.13)
Market ties:- Market segment:- Geographical market: World, except Europe Market trend: Increase (van Santen 1998b) Production constraints: None Affected supplier/technology: New technology (ion exchange membrane process).
Sodium hydroxide (NACE 24.13)
Market ties:- Market segment:- Geographical market: World Market trend: Increase (van Santen 1998a) Production constraints: Relatively lower growth in demand for chlorine provides a constraint on supply from chlor-alkali process. Affected supplier/technology: Soda ash or sodium hydroxide from caustification of soda ash (van Santen 1998a).
Ammonia (NACE 24.15)
Market ties:- Market segment:- Geographical market: Europe Market trend: Decrease. Surplus capacity in Eastern Europe. Production constraints: None Affected supplier/technology: Since energy is one of the main cost factors for producing fertiliser, it can be assumed that the least economic efficient plants have the highest energy consumption. The affected supplier can therefore be estimated to be an older plant in Eastern Europe with an energy consumption above 43 MJ/kg N, which is the highest national average energy consumption for the fertiliser industry in Europe (Worell et al. 1994, Patyk & Reinhardt 1997).
Fertiliser, in general (NACE 24.15)
Market ties:- Market segment:- Geographical market: Europe Market trend: The global consumption of mineral fertiliser has shown a steady increase over the past decades (FAOSTAT), but the European market has experienced a decrease in the consumption of fertilizer due to environmental restrictions. The European Fertilizer Manufacturers Association (EFMA 1997, EFMA s.d.) forecasts that these trends will continue. Production constraints: Supply of animal manure is constrained by the animal production being determined by other factors (the demand for other animal products, production quotas). Affected supplier/technology: Artificial fertiliser. Plants producing mineral N-fertiliser can be based upon a variety of different technological and chemical processes (IFA, 1998). However, roughly they can be divided into two categories: plants based on imported ammonia or plants with a combined production of ammonia and fertiliser. The combined plants are typically found where the resource of natural gas is abundant, e.g. Norway. The combined plants have significant technical and economic advantage, since they avoid a process of transport and can use the CO2-emission as input in the production (Engstrøm 1998). Therefore the affected supplier (in the declining market) can be identified as one without own production of ammonia.
Rubber (NACE 25.1)
Market ties:- Market segment:- Geographical market: Global Market trend: Increase Production constraints: None. Affected supplier/technology: Synthetic rubber from modern plants (Hekkert & Worrell 1998)
Bricks (NACE 26.4)
Market ties:- Market segment:- Geographical market: Local Market trend: Decrease Production constraints: None Affected supplier/technology: Oldest local tunnel kiln.
Cement clinker (NACE 26.5)
Market ties:- Market segment:- Geographical market: Local Market trend: Decrease Production constraints: Technology is raw material dependent. Affected supplier/technology: Wet process in Denmark, since raw materials contain more than 20% water. Dry process in general.
Cement (NACE 26.5)
Market ties:- Market segment:- Geographical market: Local Market trend: Decrease Production constraints: Fly ash cements etc. constrained by raw material availability. Affected supplier/technology: Portland. Older, local plants.
Steel (NACE 27.1)
Market ties:- Market segment:-
Geographical market: Europe Market trend: Increase. Trade statistics and forecasts are available from the International Iron and Steel Institute (http://www.worldsteel.org/) and World Steel Dynamics (http://www.worldsteeldynamics.com/).
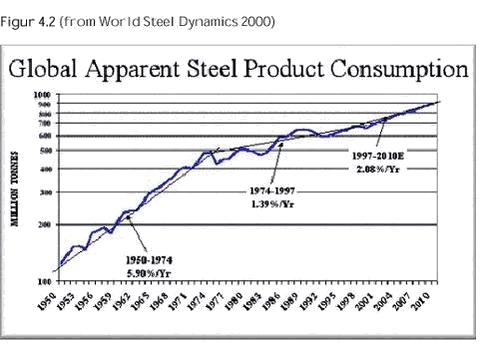
Click on the picture to see the html-version of: Figure 4.2
Despite an increasing global trend, the European production of steel is stagnating, however not below the replacement rate of capital equipment. Production constraints: Electric Arc Furnace technology constrained by availability of its main raw material (steel scrap). Affected supplier/technology: Modern Basic Oxygen Furnace technology (Gielen & van Dril 1997).
Grid electricity (NACE 40.1)
Market ties:- Market segment: Base load Geographical market: Central Europe Market trend: Increase (Eurostat 1997b, OECD 1997, European Commission 1996) Production constraints: Nuclear and hydro based power politically constrained (European Commission 1995b, 1996, 1997a). Co-generating technology limited by the local demand for heat. The installation of co-generation is independent from the choice of technology for the general electricity market. Wind power is currently expanding its market share, but the development is still constrained by the availability of technical knowledge. In most of EU, lignite based power plants are no longer built due to emission quotas, especially the SO2, NOX and CO2 targets. An exception may be Greece, where lignite power plants produce most of the electricity supply without indication of decline (Eurostat 1997a). Affected supplier/technology: Coal-based technology. This conclusion is based on the calculation of production costs shown in the table below. The production costs are composed of operation and maintenance costs, fuel costs and depreciation and interest on capital goods. Operation and maintenance costs and capital goods are taken from Energistyrelsen (1995) and data on fuel costs are from Larsen (1997). The calculations are made for proven technologies, relevant for new plants. The results are verified with data published by Hammar (1997). Calculations have been made for such technologies only, which may have a potential to be the marginal electricity source following the considerations in the above sections. Due to fluctuation in demand, power plants operate on average at less than full capacity. In the calculations, 50% capacity utilisation is assumed. The efficiencies of the plants are for electricity production only, since co-production of heat is not relevant for a marginal power plant, for reasons stated above.
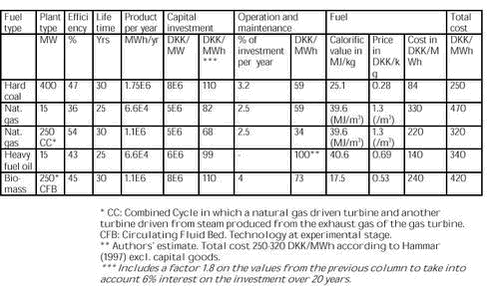
Click on the picture to see the html-version of: Figure
The calculation is most sensitive for the fuel costs, where the gas price may be set too high in the above calculations. Furthermore, due to the lower capital costs required, gas fired plants may also be the preferred technology under periods of high interest rates and insecurity. The current deregulation also favors technologies with low investment costs, as has been seen after the deregulation in the U.K. (DTI 1998). Furthermore gas fired plants better fulfil the requirements of the electricity networks for ability to adjust output quickly on a minute-to-minute basis (Dienhart et al. 1999). Therefore, it may be recommended to apply gas-fired technology in a sensitivity analysis.
Grid electricity (NACE 40.1)
Market ties:- Market segment: Base load Geographical market: Nordic countries Market trend: Increase Production constraints: As above + emission limits for SO2, NOx (and CO2) that do not leave room for much expansion of coal based power plants. Surplus coal based capacity. Affected supplier/technology: Coal-based technology within existing capacity likely to cover demand for next 10 years. Any new power plants planned are natural gas fired (Nordel 1996). This is also confirmed by a recent study based on a dynamic model of the Nordic electricity system (Mattsson et al. 2001).
Grid electricity (NACE 40.1)
Market ties:- Market segment: Base load Geographical market: Greece Market trend: Increase Production constraints: Nuclear and hydro power politically constrained Affected supplier/technology: Lignite-based technology
Water supply (NACE 41.00)
Market ties: Drinking water is supplied through a regional water supply. In Copenhagen, the extraction of groundwater is politically controlled by the counties, but within this constraint, the Copenhagen Water Supply choose between a variety of technologies. Market segment: Like electricity, water consumption fluctuates on a daily and yearly basis, but because of storage capacity in ground water basins and water towers, the market is not temporally segmented, except for very dry periods where the base load supply may be supplemented by cleaned surface water. In principle, tap water and secondary water may be distinguished, but requires separate piping, which makes the latter prohibitively costly in most applications (see below). Geographical market: Greater Copenhagen. Market trend: Increasing relative to the decrease in supply capacity from current technology, which is pumping of naturally generated ground water (Miljø- og Energiministeriet 1998). Therefore new technology (most preferred, unconstrained technology) must be installed. Production constraints: Extraction of naturally generated ground water is presently the most used technology, and in the Copenhagen area ground water accounts for 94-99% of the water supply each year (Passow 1998). This technology is constrained by the renewal rate of high quality ground water. In the Copenhagen area as much as 2.5 times the sustainable amount is pumped (Albrechtsen et al. 1998) and in many regions the resource is threatened by percolations from industry, agriculture and gardens. Ground water only needs a few cleaning operations: filtering, aeration, oxidation etc. Water of poorer qualities (polluted ground water and surface water) can be cleaned to an acceptable quality through different chemical processes. The capacity is however, still very little used, partly because the cleaning process involves chlorination, a process leaving an off-taste. Presently this is not considered politically acceptable for base load supply. Ground water can be artificially produced when surface water is irrigated on fields. This technology is called infiltration, and can utilise much poorer qualities of surface water, since e.g. organic compounds are effectively filtered by the soil. A pilot plant made by the Copenhagen Water Supply and the Technical University of Denmark shows very positive results (Gardarsson 1997), and the Copenhagen Water Supply assumes it is a matter of short time before more infiltration-fields are established (Passow 1998). This technology may eventually become constrained by its area requirement. Rainwater can be collected from roofs of buildings. The Danish Ministry of Environment and Energy estimates the potential to 2.3 E08 m3 of water. This potential is almost unused, and the amounts are led through the sewerage system together with wastewater. The rainwater cannot be used directly for drinking, but must either be cleaned or only used for washing machines and toilets. The existing plants are local, supplying the house beneath the roof, and mostly the quality problem is overcome by installation of a separate pipe system in the house. The technology is most relevant for single-family houses, where the roof area is relatively bigger and the pipes easier to change than in apartment houses. The technologies mentioned so far are all ultimately constrained by the overall amount of water supplied by local precipitation. When encountering this constraint we are left with two options: Long distance transport and desalination, both practically unconstrained. In Copenhagen, the uses of these technical possibilities are constrained by the political goal to keep the water supply on a local basis (Lund 1993, Sydvatten 1998). Affected supplier/technology: Production costs have been obtained for Copenhagen (see table) and may not apply globally. However, the factors influencing the productions costs are likely to be universally valid. From the table, the most likely technology affected in the Copenhagen situation is artificial ground water production. If this technology becomes constrained by the amount of land available for the infiltration process, the decision makers have to make a trade-off between price and quality standards. If price is most important the new technology will be cleaning of local surface water, and if more production volume is needed the desalination process or cleaning of polluted ground water can be taken into use. Cleaning costs (or alternative piping for rain water) may run very high - even higher than the costs of desalination - depending on the degree of pollution. If quality requirements are more important than the price, or when local water sources fail, long distance transport becomes relevant. For the Danish capital there is adequate amounts available in a large lake in Sweden, only 100 km away, although part of the pipeline will be underwater in the sound dividing Denmark and Sweden. For countries where the transportation distance is longer or more difficult, desalination is the ultimate option. Due to recent advances in desalination technology, the price is no longer prohibitive and often competitive to chemical treatment of polluted water or collection of rainwater. For industrial use, desalination may even be the cheapest option, since water taxes may be avoided (Hinge & Salemsen 1996). As long as the demand of water can be met from other sources, collection of rainwater is irrelevant because of the prohibitively high price.
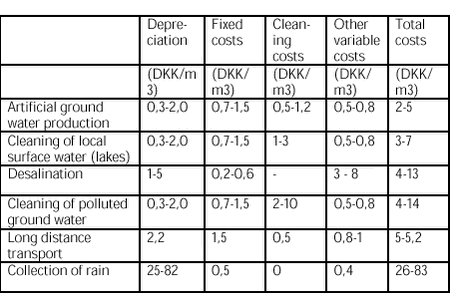
Click on the picture to see the html-version of: Figure
Data on depreciation are provided by a private drilling-firm and the statistics of the Danish Water Works Association (VandSchmidt 1998, Danske Vandværkers Forening 1997). Fixed costs, cleaning and other variable costs are estimated from a technical report on ground water valuation and personal communication with employees at the Copenhagen Water Supply (COWIconsult 1995, Passow 1998, Als 1998). Cleaning of surface water costs 1-2 DKr, while the costs for cleaning polluted ground water can vary considerably depending on the actual quality. These data are from Kemp & Lauritsen (1995) and two local water works (Regnemark Waterworks 1998, Gentofte Waterworks 1998). Artificial production of ground water through infiltration gives additional costs for irrigation and land use. Data on infiltration costs for artificial ground water production is supplied from the pilot plant of the Copenhagen Water Supply and the Technical University of Denmark (Gardasson et al. 1997). Desalination costs are estimated on basis of Ribeiro (1996). If water is to be transported from water works in other geographical regions, there will be additional costs for construction and maintenance of a pipeline and costs for pumping. These costs can vary considerably depending on the nature of the subsoil, the needed capacity and the slope of the distance. Construction costs alone can vary from a mere 140 DKK/meter to 13.000 DKK/meter. Data here are based upon an internal calculations performed by the Water Supply of Copenhagen to assess the possibility of supplying water to Copenhagen from a distance of approximately 100 km from a Swedish lake (Lund 1993) with standard costs for maintenance (COWIconsult 1995) and operating costs roughly estimated by Sydvatten (1998). The cost of collecting rainwater from roofs is estimated by Albrechtsen et al. (1998). Most of the investment for collection of rain is for changing the piping, and the cost depends very much on the type of house. An alternative to changing the pipes is to filter and clean the rainwater, but the cost for this is estimated to be higher, mostly because of control-costs.
Waste treatment (NACE 90.00)
Market ties:- Market segment: Non-separated household wastes. Geographical market: Local (Europe outside Denmark). Market trend: Increase Production constraints: In Denmark, legislation prohibits landfilling of combustible waste. Outside Denmark, waste incineration capacity is fully utilised, although expanding (Ekvall & Finnveden 1998). Affected supplier/technology: Landfilling (Ekvall & Finnveden 1998).
____________________________________________________________ 13 This section is adapted from a presentation to the 9th SETAC Europe LCA Case Studies Symposium (Weidema 2001b) 14 While this section deals mainly with environmental product declarations, the arguments and conclusions are equally valid for environmental labelling in general.
| Front page | | Contents | | Previous | | Next | | Top |
|