| Front page | | Contents | | Previous | | Next |
Market information in life cycle assessment
5 Method for handling co-products
5.1 Why system expansion is the preferred option for handling co-products
5.2 Theoretical model for system expansion
5.3 A procedure for handling co-products
5.4 Identifying a product as determining for the volume of the co-producing process
5.5 Treating intermediate processes
5.6 Waste or co-product?
5.7 Recycling
5.8 Services as co-products
5.9 Complex situations
5.10 Traditional co-product allocation as a special case of the presented procedure
5.11 Relation to the procedure of ISO 14041
15 When a process or product system in an LCA is related to more than one product, it presents a problem: how should its exchanges, such as the resources consumed and the releases generated, be partitioned and distributed over the multiple products?
The allocation of these multiple products, known as “co-products”, has been one of the most controversial issues in the development of the methodology for LCA, as it may significantly influence or even determine the result of the assessments. It has been seen as so central a procedure that it is often (even in the International Standards Organization standard on life cycle assessment, ISO14040) nick-named “allocation” as if it was the only allocation problem in LCA16.
Allocation is the partitioning and distribution of an item over several other items. Co-product allocation is the partitioning and distribution of the exchanges (e.g., inputs and outputs) of a multi-product process over its co-products. The co-product allocation problem is parallel to the cost allocation problem, which has been extensively treated in the economic literature (a review pertinent to LCA is provided by Frischknecht 1998). However, while cost allocation is primarily an accounting tool where the different methods can be said to have each their advantages and disadvantages from the view of different decision makers focusing either on issues internal to their business or on direct business-to-business relations. In contrast, LCA begs for a solution that models as closely as possible all the external consequences of a potential change in demand for one of the co-products.
The idea that co-product allocation can be avoided by system expansion has been put forward by Tillman et al. (1991) and Vigon et al. (1993) with respect to waste incineration, and more generally by Heintz & Baisnee (1992). System expansion is performed to maintain comparability of product systems in terms of product outputs, through balancing a change in output volume of a co-product that occurs only in one of the product systems, by adding an equivalent production in the other systems (or more elegantly and correctly by subtracting the equivalent production from the one system). For example, in the case of an LCA involving chlorine gas co-produced with sodium hydroxide used in another product system, the system is expanded with an alternative stand-alone production of sodium hydroxide, and the environmental releases and resource consumption of this alternative production is then subtracted from the system using the chlorine gas.
System expansion was given a prominent place in the procedure of ISO 14041, where it reads in section 6.5.3: “Step 1: Wherever possible, allocation shall be avoided by: 1) dividing the unit process to be allocated into two or more sub-processes and collecting the input and output data related to these sub-processes; 2) expanding the product system to include the additional functions related to the co-products…”.
Although avoiding allocation is seen as the preferable option, it has generally been regarded as impossible to expand the system in all cases. Therefore, other options have been maintained, especially the allocation according to the revenue or gross margin from the products, a procedure commonly applied in cost accounting (Huppes 1992). Older studies used simple physical allocation criteria such as the relative mass or exergy of the products, but these criteria have generally been discredited for lack of justification (Huppes & Schneider 1994), except in attributional, non-comparative LCAs, where they may still be used as a proxy for revenue.
The following four obstacles to system expansion can be seen as part of the reason why this option has not generally been applied as a way to avoid allocation:
- In attributional LCAs, there is typically no possibility for system expansion. Attributional studies typically seek to describe a status-quo situation, in which there are no changes in production volume. This obviously excludes the possibility of system expansion, because an expansion involves balancing a change in output volume of a co-product in one system with an equivalent change in the other systems to be compared, in order to maintain comparable product outputs from the systems. The distinction between attributional and consequential studies and its important consequences for the methodology (including the handling of co-products) has only recently been clarified (see section 1.2). It is still common to see attributional studies applied for decision support and a mix of methodologies and justifications without clear reference to the attributional or consequential nature of the study.
- It has been regarded as too difficult, too uncertain, or even impossible to identify which processes are affected when balancing a change in demand for (or supply of) a specific co-product.
- Because a system expansion may involve processes that also have multiple products, it has been suggested that there are situations where system expansion would be impossible because it would involve an unending regression.
- When a by-product does not substitute for another product, system expansion may be regarded as incompatible with the requirement that compared systems must have identical functions.
In this chapter, it is shown that allocation can (and shall) always be avoided in consequential LCAs. In attributional LCAs, it is not possible to express an imperative regarding what allocation procedure to apply, but avoiding allocation may still be an option. We reach this conclusion by demonstrating how to overcome the four obstacles listed above:
- By distinguishing clearly between attributional and consequential studies, it is possible to distinguish between the situations in which system expansion is both possible and mandatory (consequential studies) and the situations in which system expansion is irrelevant or at least optional (attributional studies).
- In chapter 4, it was shown that it is always possible, and seldom difficult, to identify the processes affected by a change in demand. The uncertainty of this determination, and the fundamental uncertainty of future market situations, are inherent to the method, but can be neither a theoretical nor a practical argument against system expansion.
- The problem of unending regression is eliminated by applying the method from chapter 4, which provides clear cut-off criteria (either a process is included or excluded from the studied system) and reduces the number of processes that may possibly be involved in a system expansion (for details, see section 5.8).
- It is shown that by-products practically always substitute for other products, and even when this may not be the case, the studied systems are still comparable.
In the following sections it is demonstrated how system expansion is performed, with a number of examples. Special emphasis is placed on issues that have earlier been in focus of the allocation debate: joint production of e.g. chlorine and sodium hydroxide, zinc and heavy metals; the handling of “near-to-waste” by-products; and credits for material recycling and downcycling. It is shown that all the different co-product situations can be covered by the same theoretical model and the same procedure. Separate sections deal with the issues of uncertainty, co-product allocation as a special case of system expansion, and comparison to the procedure of ISO 14041.
5.1 Why system expansion is the preferred option for handling co-products
To study correctly the effects of a potential product substitution in consequential, comparative LCAs, it is necessary that the studied product systems:
- are comparable, which means that they must provide the same functions, thus reflecting the substitution that is really expected to take place (Chapter 3),
- include all significant processes that are affected by the potential product substitution (Chapter 4).
In general, these two conditions are not fulfilled by allocation. First, allocation typically involves a more or less arbitrary partitioning of the co-producing process over its co-products, without consideration of the extent to which a change in the amount of these co-products actually affects the functional output and other exchanges of the co-producing process. Secondly, allocation ignores the effects that a co-product may have on the further fate of the other co-products, i.e. displacement effects and additional treatment of the co-products before displacement takes place.
Thus, traditional co-product allocation only fulfils the above two conditions in those particular instances where the allocation factors are chosen to reflect the way the co-products actually affect the co-producing process and where there are no significant effects on the further fate of the other co-products. In such instances, allocation may be regarded as a special instance of system expansion, as described in section 5.10.
The above two conditions are fulfilled by system expansion, because any process, which will be affected by a change in the amount of co-products, is included in the studied product systems, and it is ensured that all systems yield comparable product outputs, by subtracting or balancing processes that do not occur in all of the compared systems (for details, see the procedure described in later sections). This is the rationale for preferring system expansion to allocation for handling co-products in prospective LCAs.
In a non-comparative, attributional LCA, the preference for system expansion (as in the ISO procedure) still leads to a reasonable result, when the study is understood as an analysis of hypothetical historical changes like: What would have happened if this product had not been introduced or if this product had been produced instead of this? In this case, historical market data can be used to calculate hypothetical system expansions and to show what the results would have been of a prospective LCA if it had been produced at that historical moment.
5.2 Theoretical model for system expansion
System expansion is illustrated in figure 5.1 showing a co-producing process with one determining co-product (product A); that is, a co-product that determines the production volume of that process. This is not necessarily the co-product of interest to the specific life cycle study. In figure 5.1, just one dependent co-product is shown, but in practice there may be any number of co-products.
That a product is determining for the production volume of a process is the same as saying that this process will be affected by a change in demand for this product, as identified by the procedure in chapter 4.
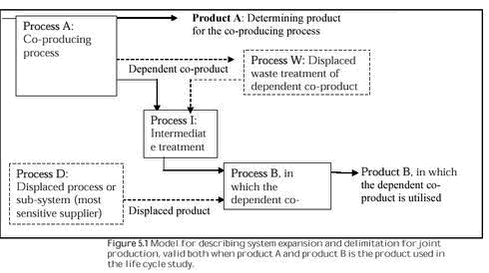
Click on the picture to see the html-version of: Figure 5.1
Performing a system expansion in relation to joint production is to answer the question: How will the production volume and exchanges of the processes in figure 5.1 be affected by a change in demand for the co-product that is used in the life cycle study?
Because the environmental exchanges are generally linked to the production volumes, the answer to this question will also provide a solution to the allocation issue. This question is equally relevant when the co-product used in the life cycle study is the determining product for the co-producing process (A) and when it is the product in which the dependent co-product is utilised (B).
A complete identification of changes in production volume as a function of change in demand would require an economic model for all the involved processes and product flows. The procedure presented here involves the simplifying assumption that a change in demand for a dependent co-product does not affect the production volume of the co-producing process17.
Under this assumption, the answer to the above question can be summarised in three rules18:
- The co-producing process shall be ascribed fully (100%) to the determining co-product for this process (product A). This follows logically from product A per definition being the co-product, which causes the changes in production volume of the co-producing process.
- Under the conditions that the dependent co-products are fully utilised, i.e. that they do not partly go to waste treatment, product A shall be credited for the processes that are displaced by the dependent co-products. The intermediate treatment shall be ascribed to product A. If there are differences between a dependent co-product and the product it displaces, and if these differences cause any changes in the further life cycles in which the dependent co-product is used, these changes shall likewise be ascribed to product A. This rule follows from the fact that – under the stated condition – both the volume of intermediate treatment and the amount of product which can be replaced, is determined by the amount of dependent co-product available, which again is determined by the change in production volume in the co-producing process, which is finally determined by the change in demand for product A. It follows from this rule that product B is ascribed neither any part of the co-producing system, nor any part of the intermediate treatment. When studying a change in demand for product B, this product shall be ascribed the change at the supplier most sensitive to a change in demand (identified by the procedure described in chapter 4), i.e. the same process, which is displaced by a change in demand for product A (but see also rule no. 3). If the condition stated in rule no. 2 (that the co-product is fully utilised in other processes) is not fulfilled, rule no. 3 applies.
- When a dependent co-product is not utilised fully (i.e. when part of it must be regarded as a waste), the intermediate treatment shall be ascribed to the product in which the dependent co-product is used (product B), while product B is credited for the avoided waste treatment of the dependent co-product. This follows from the volume of the intermediate treatment (and the displacement of waste treatment) in this situation being determined by how much is utilised in the receiving system, and not by how much is produced in the co-producing process. Another way of saying this is that in this situation, process I (the intermediate treatment) is that supplier to process B, which is most sensitive to a change in demand for product B.
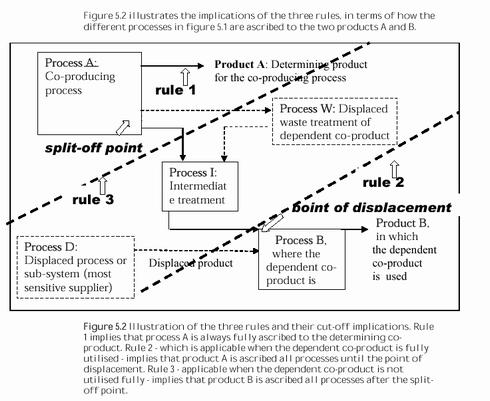 Click on the picture to see the html-version of: Figure 5.2
It may at first sight appear counter-intuitive that the intermediate process is ascribed to product A when product B utilises all of a dependent co-product, while the process is ascribed to product B when only part of the co-product is used in product B. This is a reflection and a good illustration of the difference between the (more intuitive?) attributional perspective that focus on the average behaviour (full utilisation or not) of the intermediate process rather than on the consequences of this full utilisation for the changes in the volume of the intermediate process when demand for product B changes, which is the focus of the consequential approach upon which the three rules are based.
5.3 A procedure for handling co-products
Figure 5.3 presents a procedure for handling co-products in the form of a flow-chart. An initial distinction can be made between joint production, where the relative output volume of the co-products is fixed, and combined production with independently variable output volumes (Huppes 1992). For the latter type of production, allocation can be avoided simply by modeling directly the consequences of a change in the output of the co-product of interest (that which is used in the product system under study) without change in the output of the other co-products. This situation is dealt with in step 1 of the procedure. The remaining part of the procedure (steps 2 to 4) deals with the situation of joint production where allocation can only be avoided through system expansion.
For combined production, a physical parameter can generally be identified, which - in a given situation – is the limiting parameter for the co-production. It is the contribution of the co-product of interest to this parameter, which determines the consequences of the studied change. In the guideline (Weidema 2003), two examples are provided of this: treated surface area of product plus border area in a combined surface treatment, and weight or volume in different situations of combined transport. Here we add an example of a combined freezer/refrigerator and the classical example of combined treatment of several wastes in the same treatment plant (e.g. landfill or incinerator):
Example: Refrigerators and freezers are often built as combined equipment to reduce the heat loss, and take advantage of savings in insulation and casing. An additional need for refrigerator space may be covered by adding a separate refrigerator, but more rationally the existing combined option may be substituted by another combined option in which the refrigerator space is larger relative to the freezer space. Here we assume that the old equipment is anyway up for replacement or can be utilized in another context, since the old equipment should else be included in the calculation. The energy requirement of the marginal refrigerator space can be determined from comparing the two options, or more generally by identifying the relevant physical parameter that determines the relative energy consumption. Also here, the physical parameter can be identified as the co-called “temperature C), adjusted volume”, which can be calculated as: Vadj = Vc* (tr- tc)/(tr– 5°C) where Vc is the volume of the compartment, tr, the room temperature, tc the temperature of the compartment, and 5°C is the reference temperature. Thus, it is the contribution to Vadj that determines the energy requirement of the additional refrigerator space.
Example: In combined waste treatment, many emissions depend on the composition of the incoming waste. For example, the emissions of cadmium will be in proportion to the amount of cadmium in the incoming waste. Thus, adding a cadmium-containing item will increase the emissions of cadmium by this amount. The same straightforward logic applies to the creation of incineration ashes, which depends on the ash content of the different incoming wastes. However, some emissions are not dependent on the composition of the incoming waste. Classical examples from incineration are NOx, which is formed in the combustion chamber, and dioxins, which are formed mainly in the ”exhaust cleaning” processes. The formation of NOx depends mainly on the combustion temperature, and while the formation of dioxins has some connection to the occurrence of elements like carbon and chlorine, many other elements act as catalysts in the process. In principle, it is possible to add different kinds of waste and measure the change in formation of NOx and dioxins, thus reaching an understanding of the relations between the type of waste and the emissions. However, as long as the chemical reactions and their determining parameters are not fully understood it is most reasonable to assume that the emissions of NOx and dioxins will change in proportion to the overall limiting parameter of the combustion process. Waste incinerator capacity is generally limited by the weight of incoming waste, which means that the emissions of NOx and dioxins should change in proportion to the weight of the treated waste.
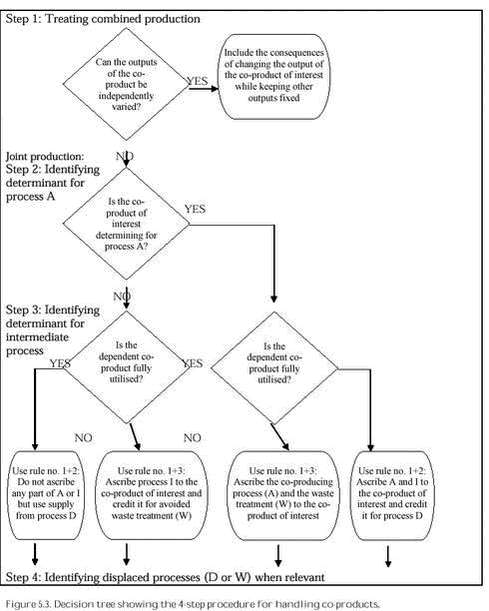
Click on the picture to see the html-version of: Figure 5.3
The limiting production parameter may depend on the original situation. Therefore, it is essential to describe both the original situation in terms of the relative outputs of the co-products before the studied change, and the production parameters that in this situation are determining the changes in the exchanges of the combined production. This is even more obvious when the output of the co-products can only be varied within certain limits, that is, when the production cannot be separated completely. In many production processes where one raw material is used to produce several outputs, the production parameters can be adjusted to give different relative yields of the co-products, but only within certain limits. When operating close to such a limit, the consequences of the studied change may be ambiguous, and this should be reflected in the modeling and its results.
Example:
In oil refining, the output of bitumen (asphalt) varies between 7% and 79% depending on the origin of the raw oil. Thus, for each individual raw oil type, the output of bitumen is not variable, but for refineries as a whole, there is some flexibility to meet changes in the demand for bitumen, as long as the demand as a whole does not fall below 7% of the demand for the remaining refinery products. If the demand falls below this limit, bitumen could become a waste product (although some of it can be reprocessed for combustion purposes in the form of tar-sand and orimulsion), and this alternative situation should then be modelled in the LCA.
Example:
On a milk farm, the outputs of milk and meat can be individually varied within certain limits. The milk output can be regulated e.g. by changing the fodder composition, and the amount of meat output can be regulated through the rate of replacement of the milking cows. However, there are both physical limits to the maximum milk yield per animal and the minimum replacement rate. The output of meat will be determined by the replacement rate, which gives the desired milk production, not by the demand for meat. Thus, an additional output of meat can only be obtained by increasing the amount of calves raised for meat, an additional production not originally included when studying a milk producing system.
As already suggested by the last example, some productions may appear as allowing individual variation in output, but when subjected to a closer analysis it is only possible to keep the output of the other co-products constant by adjusting sub-processes not involved in the original production. Thus, what appears at the superficial level to be a case of individually variable co-products may in fact be a joint production requiring a system expansion (steps 2-4 of the procedure, see below).
Example: If an oil refinery is regarded as a black box, the outputs of different fuels, olefins and other refinery fractions may be individually varied, so that practically any desired relation between the outputs can be obtained. The only fixed fractions are refinery gas and bitumen. However, when having access to data for the individual processes within the refinery, it becomes clear that this flexibility in outputs is achieved by allowing simultaneous changes in a large number of individual processes. Looking specifically at the major olefins: ethylene and propylene, the main production route is steam-cracking which yields ethylene in a relatively high proportion. The specific proportion is fixed for each raw material, so that the relative outputs of the twoolefins can be varied by shifting between a raw material that yield practically only ethylene (ethane) and those raw materials (LPG, naphtha, and gas oil) that yield increasingly larger proportions of propylene yields (42, 53 and 61% of the ethylene yield respectively). However, also another production route exists that yields more propylene than ethylene. This secondary route uses the off-gases from fluid catalytic cracking (FCC). Thus, a change in the demand for one of the two products may cause either a shift in raw materials for steam cracking or a shift in volumes between steam cracking and FCC offgas-cleaning, until a new balance is found that satisfies the current demand. Which of these options will be chosen depends on the price relations between the options, and the constraints on raw material availability and the demand for the other co-products (the mentioned raw materials also yield increasing outputs of C4 and BTX fractions along with the increase in propylene). The described changes can be modelled as a system expansion within the refinery, as shown in Weidema (2003).
5.4 Identifying a product as determining for the volume of the co-producing process
When the output of the co-products cannot be independently varied, a change in demand for one of the co-products may or may not lead to an increase in the production volume of the co-producing process. This depends on whether the co-product in question is determining for the production volume or not.
Identifying a product from a joint production (to keep it short, such a co-product will simply be called a joint product in the remaining part of this section) as determining for the production volume of the co-producing process is the same as showing that the co-producing process will be affected by a change in demand for this specific co-product (which we will then call a determining co-product for short). When the co-producing process is identified as the affected process by using the procedure in chapter 4, we have in fact at the same time identified the co-product under study as being a determining co-product.
For a co-product, the crucial point in the procedure in chapter 4 is the identification of the other co-products as a production constraint. The production volume of the co-producing process is constrained by the demand for the determining joint product(s). Independently variable (combined) co-products cannot provide a constraint and may be simultaneously determining (as described in the previous step).
In this section, it is explained:
- how to identify the determining co-product,
- why there is typically only one of the joint products that is determining the production volume of the co-producing process at one given moment,
- why the determining co-product is not necessarily the co-product, which yields the largest economic value to the process, and
- why the determining co-product is not necessarily the co-product, which has the largest change in demand.
The overall production volume of a co-producing process is typically determined by the combined revenue from all the co-products, since production of an additional unit will be profitable as long as the total marginal revenue exceeds or equals the marginal production costs. As a starting point, this also implies that any change in revenue for any co-product may affect the production volume. Thus, to identify a joint product as determining, it is adequate to document that a change in demand for the joint product leads to a change in revenue for the co-producing process.
However, as already discussed in section 2.4, the default assumption in life cycle assessment is that suppliers are price-takers and the long-term market price of a co-product is therefore typically determined by the long-term marginal production costs of the alternative production route for this co-product, if such an alternative route exists. As long as the price of a joint product and thus its contribution to the overall revenue of the co-producing process is determined by its alternative production route, a change in demand for this co-product will not lead to a change in its (long-term) price and there will be no change in its contribution to the overall (long-term) revenue of the co-producing process.
Thus, there is typically only one of the joint products that is determining at any given moment. This understanding can be further elaborated into the following two conditions:
To be a determining co-product, a joint product (or a combination of joint products in which the co-product takes part) shall:
- provide an economic revenue that is in itself adequate reason for changing the production volume
and
- have a larger market trend (change in overall demand) than any other joint product or combination of joint products that fulfil the first condition (taking into account the relative outputs of the co-products). The reason for this is that the joint product (or combination) with the largest market trend provides a constraint on the ability of the other joint products to influence the production volume of the co-producing process. Note that within a combination of joint products, the co-product with the smallest market trend is determining the ability of the combination to influence the production volume.
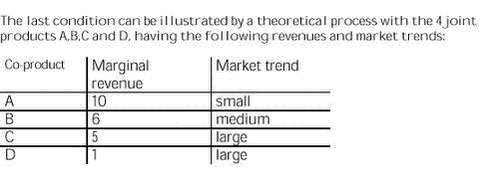
Click on the picture to see the html-version of: Figure
Note that the stated market trends and revenues are relative to the normalised output volumes of the co-producing process, which means that differences in the actual physical quantities have already been eliminated. At a marginal production cost for the co-producing process of 9, only one co-product (A) can provide adequate revenue to change the production volume alone. Product C cannot alone influence the production volume, in spite of the large market trend for this product. However, the combination B and C also fulfil the condition of providing adequate revenue. The possible influence on the production volume from this combination is determined by the smallest of the market trends of the products in the combination. This is the medium trend of product B. Because this is still larger than the trend of product A, product B becomes the co-product that determines the production volume.
Condition ii) above implies that if more than one joint product or combination of joint products fulfil condition i), then only that joint product or combination which has the relatively largest change in overall demand (market trend) is actually determining. This again emphasises that as long as alternative production routes exist for the joint products, there is only one of the joint products that can be determining for the production volume at any given moment.
Example:
Approximately 90% of all primary cadmium is a co-product of zinc extraction. Mercury, lead, and sulfur are also produced as co-products of zinc extraction. The demand for zinc is increasing moderately (Henstock 1996) while the demand for the heavy metals cadmium, mercury, and lead is stagnating mainly due to environmental regulations. The supply of cadmium from compulsory take-back and recycling of cadmium-containing products means that some primary cadmium is currently deposited (landfilled) and the same situation can be expected in the future for the other heavy metals. Sulfur is increasingly produced from desulfurisation of flue gases from refineries, power plants and other similar facilities. In Europe, there is no longer primary production of sulfur (Gielen 1997). Thus, it should be clear that only changes in demand for zinc can be determining for the primary zinc extraction.
Example: The joint production of chlorine and sodium hydroxide is one of the classical examples of allocation problems. The chloralkali process yields three co-products: 2NaCl +2H2O ⇒ 2NaOH + Cl2 + H2 Hydrogen is produced in relatively small quantities (27 g for every kg of chlorine) providing approximately 3% of the world market for hydrogen. The main production route for hydrogen is steam reforming of natural gas and this will probably also be the preferred process to meet an increase in demand for hydrogen. As hydrogen does not fulfil the first condition, it cannot be the determining co-product. In addition, it can be noted that the value of the hydrogen is approximately 5% of the total income for the chloralkali process, which means that is does not fulfil the last condition either. In practice, the chloralkali process is the exclusive production route for chlorine, which cannot be easily stored and is typically sold locally. Sodium hydroxide is a more flexible product that can be stored and transported over long distances. Sodium hydroxide can be substituted by soda ash directly or by sodium hydroxide produced by caustification of soda ash, thus providing both a floor and a ceiling on the price of this co-product (van Santen 1998a). Chlorine and sodium hydroxide are produced in approximately equal quantities by the chloralkali process and their share in the total income for the process is approximately the same. However, during the last 10 years there has only been one short period in 1990/1991 where the price of sodium hydroxide was so high that it could by itself provide adequate revenue to change the production volume (Beal 1995). Based on this analysis of the market situation, it is concluded that long-term decisions on capacity adjustments are based on the existence of local, stable demands for chlorine, making chlorine the determining co-product for the chloralkali process when applied in LCAs with a long time horizon. However, for some studies with a short time horizon, it may be relevant to regard sodium hydroxide as the determining co-product for the utilisation of the existing chloralkali capacity, in periods when the demand/price of sodium hydroxide is high. However, this situation is not likely to persist for longer periods, because of the existence of alternative production routes and substitutes for sodium hydroxide.
For joint products that do not have any relevant alternative production routes, their prices will adjust so that all the joint products have the same normalised market trend, since only then the market will be cleared. In this situation, a change in demand for one of the joint products will influence the production volume of the joint production in proportion to its share in the gross margin of the joint production. This is equivalent to the result of an economic allocation. However, the resulting change in output of the other joint products influences their further downstream lifecycles, including their consumption and disposal phases, and thus requires the inclusion of the processes affected. This latter aspect of system expansion is ignored in a pure economic allocation of the joint production (see also section 5.10).
Example:
In pork production, the slaughtered pig is the basis for a large number of co-products. Independent variation among co-products is limited, although some flexibility exists, notably in the share of minced meat. All co-products must therefore be regarded as joint, and with some minor exceptions no alternative production routes exist. Thus, the pork market is governed solely by the output from the abattoirs and all prices are continuously adjusted so that all products are sold. Market trends are therefore aligned so that all joint products are simultaneously determining for the production volume. A change in demand for one specific part of the pig, e.g. tenderloin, will therefore influence the volume of production in proportion to the gross margin obtained for this part, relative to the average gross margin, equivalent to the result of an economic allocation. Since there are no alternative production routes, this change in production volume in turn affects the output, pricing and consequent consumption of all other parts of the pig.
The above theoretical illustration with the 4 joint products A,B,C, and D, also shows that the determining co-product is not necessarily the co-product that yields the largest revenue to the process (although this will often be the case), and that the determining co-product is not necessarily the co-product that is having the largest increase (or decrease) in demand.
It should be obvious that the two conditions above, and thus the determining co-product, may change over time, depending on location and the scale of change. Thus, it is always important to note the preconditions under which a given co-product has been identified as determining. When in doubt, or when conditions vary within the studied scale or geographical or temporal horizon, two or more alternative scenarios should be modelled.
5.5 Treating intermediate processes
The intermediate processes are those processes that take place between the split-off point where a dependent co-product leaves the processing route of the determining co-product and the point of displacement where the dependent co-product can displace another product (see also figure 5.2). While it is always relevant to determine the split-off point, it is only relevant to determine a point of displacement when the dependent co-product is utilised fully in other processes and actually displaces other products there.
The determining co-product for the intermediate processes is identified by investigating whether the condition of rule no. 2 (section 5.2) is fulfilled or not, i.e. whether the dependent co-product is utilised fully in other processes.
If the condition is fulfilled, the volume of intermediate treatment (and the amount of product being displaced) depends on the product volume of dependent co-product. Since the co-products cannot be independently varied, this volume is fixed by the determining product of the co-producing process. A change in demand for the dependent co-product will not lead to any change in the intermediate treatment (exactly because it is not determining, i.e. it cannot affect the volume of the co-producing process). Thus, the intermediate treatment and the co-producing process have the same determining product, and (as stated by rule no. 2) the intermediate process shall be fully ascribed to this product.
Example:
Cement may contain up to 40% of fly ash (a co-product from combustion processes), thus replacing the energy intensive raw material clinker. In most countries, all fly ash produced is fully utilised because of the obvious energy advantage. In this situation, the amount of fly ash used depends on the supply, i.e. on the volume of the combustion process producing the fly ash. Thus, this combustion process is ascribed the intermediate treatment (drying and transport) while being credited for the displaced clinker production.
Since in this situation, where the dependent co-product is fully utilised, it is the determining product for the co-producing process that also determines the amount of product being displaced, this product shall also be ascribed other possible changes resulting from the displacement. This applies to the changes in the alternative raw material supply, as in the example above, where the determining product for the co-producing process is ascribed (credited for) the changes in the displaced process, but also to such changes in the further life cycle of the dependent co-product that are a consequence of differences between the dependent co-products and the products they displace.
Example:
Compared to the displaced product, the dependent co-product may be of a different (typically lower) quality than the displaced product. This is often of no importance to the user (else the substitution would not have been accepted) but sometimes it may lead to an additional need for maintenance or other supplementary activities. These additional activities shall be ascribed to the determining product for the co-producing process.
Example: Compared to the displaced raw material, the dependent co-product may contain a contamination, e.g. of heavy metals, which gives it a different performance during the final waste treatment of the product in which the dependent co-product is used. The difference in waste treatment and/or in environmental exchanges form the waste treatment shall be ascribed to the determining product for the co-producing process.
If, in the described situation where the dependent co-product is fully utilised, no point of displacement can be found, i.e. if the dependent co-product cannot immediately displace another product, the entire life cycle of the product in which the dependent co-product is used can be regarded as belonging to the intermediate treatment. Alternatively, it can be regarded as an alternative (but not necessarily more environmentally benign) waste treatment for the co-producing process. Both of these perspectives implies that the volume of the product in which the dependent co-product is used depends on the supply from the co-producing process, and that all processes in the life cycles for both the determining and the dependent co-products are to be ascribed to the determining product for the co-producing process. As the dependent co-product has a function (else it would be a waste) the resulting product system is strictly speaking still a system with more than one function. In spite of this, it is comparable to other product systems that solely yield the determining product. These other product systems shall not be expanded with the additional function (the one yielded by the dependent co-product) since this function is solely caused by the existence of the dependent product and not by any external demand19.
Example:
Some discarded materials or worn-out products may be sold on a secondary market or reprocessed to fulfil some kind of leisure or luxury function, not necessarily replacing any other products, but simply implying an extra consumption. The reprocessing and use of these co-products shall be ascribed to the product system in which they originate. It should be noted that the price obtained for the (reprocessed) co-products will be taken from a consumer budget and can therefore not be used for other purchases. This may be regarded as a displacement of the marginal consumer spending, for which rules no. 2 or 3 (section 5.2) would apply.
If the condition of full utilisation is not fulfilled, it means that part of the dependent co-product is treated as a waste. In this situation, the volume of the intermediate treatment (and the displacement of waste treatment) is determined by how much is utilised in the receiving system, and not by how much is produced in the co-producing process. Thus, the product in which the dependent co-product is used, is determining the volume of the intermediate processes and shall be ascribed these (while being credited for the avoided waste treatment), as stated by rule no. 3 (section 5.2).
Example:
Use of the co-product fly ash as additive to cement is limited by a lack of standards for blended cements in countries with a relatively low amount of fly ash production (like Ireland and in Latin America). Also traditions and building codes for strength testing may limit the market for blended cements. In these situations, part of the fly ash may be deposited. Thus, a change in demand for blended cements may lead to more fly ash being used, and a displacement of the waste depositing. Thus, the blended cements should be ascribed the intermediate treatment and credited for the displaced waste treatment.
Example:
In the joint production of zinc and heavy metals, some primary cadmium is currently deposited and the same situation can be expected in the future for the other co-products from zinc extraction: mercury, lead, and sulfur. Thus, in this situation the product using these co-products should be ascribed the intermediate treatment, while being credited for the displaced waste treatment.
As illustrated by the examples, whether a co-product is utilised fully and whether it displaces other products, depend on market conditions that may change:
- over time,
- depending on location, and
- depending on the scale of change.
Thus, it is important always to note the conditions under which the determinant for the intermediate processes has been identified.
If the investigated change is of such a size that it in itself changes the conditions for the system expansion, i.e. changes which product is determining or whether the dependent co-product is utilised fully, the system expansion shall be calculated on the basis of the resulting conditions after the change.
The information needed to determine whether a dependent co-product is fully utilised are obtained from market and waste statistics and market studies, often available in-house in the involved industries. If it is uncertain whether this condition is fulfilled, it may be necessary to apply different scenarios to reflect the limited knowledge.
5.6 Waste or co-product?
In previously presented allocation procedures, it was important to distinguish between wastes and co-products, because the exchanges of the co-producing process should be allocated over the co-products, but not over the wastes and emissions. Waste is often defined in vague terms as ’outputs that need further treatment’ (see e.g., Frischknecht 1994) or ’outputs that the holder discards or intends to or is required to discard’ (EEC 1991) supported by exemplary or authoritative listings (e.g., the European Waste Catalogue 1994). In a more stringent way, waste can be defined as economic inputs and outputs (as opposed to inputs and outputs from and to the environment) with a value equal to or lower than zero (see e.g., Huppes 1994).
In the procedure presented here, the distinction between wastes and co-products is not important. If in doubt whether an output is a waste or a co-product, the output can be regarded as a dependent co-product and passed through the procedure. It will then fall under either rule 2 (the treatment of wastes that do not displace any other products would then be classified as an intermediate treatment and ascribed to the determining product for the co-producing process, just as a waste treatment would normally) or rule 3 (for “near-to-wastes” that are not fully utilised) of section 5.2. If a waste in the economic sense, i.e. an output without economic value to the process that produces it, displaces another product, the “waste treatment” is in fact a recycling, and rules 2 or 3 should therefore be applied in order to model correctly the consequences of this “waste treatment”.
Thus, from the procedure presented here, a novel definition of waste may therefore be derived: A waste is a dependent output that does not displace any other product. This definition is in line with the intention of the definition in the European Waste Directive (EEC 1991) but gives a more precise distinction.
5.7 Recycling
Recycling has been regarded as presenting distinct allocation problems needing a separate treatment (for a number of articles on this topic, see Huppes & Schneider 1994). Examples of specific allocation procedures developed to handle recycling situations are the 50/50 rule (Ekvall 1994) and the material grade model (Wenzel 1998, Werner & Richter 2000).
However, the procedure presented earlier in this chapter is applicable for recycling, as for any other situation in which the same processes are shared by several products.
In the recycling situation, it is not difficult to identify the determining process for the primary life cycle. This is obviously the product of this life cycle, not the scrap.
The central issue is what determines the recycling rate and thus the degree to which the scrap is utilised in the secondary life cycle.
In an expanding market for the scrap product, such as is the case for most metals, all scrap collected will be used. In this situation, a change in the volume of the primary life cycle will lead to a change in the amount of scrap available for collection, and a change in the amount collected, and a change in the amount of scrap utilised in secondary life cycles, and thus in the displacement of “virgin” production (i.e. following rule 2 of section 5.2). A change in the volume of the secondary life cycle will not be able to influence the amount of scrap utilised, because it is already utilised fully. Thus, the change in the volume of the secondary life cycle must be covered by a change in “virgin” production (i.e. still following rule 2). However, it should be noted that a change in demand for scrap products may have indirect effects in the form of political intervention, reinforcing the signal sent by the change in demand, as also described in section 4.3. Such indirect effects are possible when significant quantities of scrap are available for collection, in addition to the amount already collected, and the costs of the additional collection is comparable to the costs of extracting “virgin” material. Such indirect effects should be described in separate scenarios, since they depend on political decisions that are difficult to predict.
In immature markets, the recycling might be below the economic optimum due to capacity constraints. In this situation, neither using nor supplying scrap will affect the recycling rate. An increase in demand will thus affect “virgin” supply, while an increase in supply to recycling will increase waste deposits. Only a specific action to remove the capacity constraints on recycling will effectively increase recycling. Also in this situation, a specific demand for scrap products may have long-term indirect effects that may be modelled in separate scenarios, as noted in the previous paragraph.
In a shrinking market, as we see for cadmium and some other heavy metals, some of the available material is being deposited, because there is not an adequate demand. A change in volume of the primary life cycle will only lead to a change in the amount of material to be deposited, whereas a change in the volume of the secondary life cycle will lead to a change in the amount being recycled, and thus indirectly also to a change in the amount being deposited (i.e. following rule 3 of section 5.2). It is interesting to note that in the case of cadmium (and possibly other heavy metals) the amount of recycling is fixed by environmental regulation, which means that it is “virgin” cadmium (as a by-product from zinc production) that is deposited, whereas in other situations it can be expected that it is the scrap material that would not be collected.
It may be argued that the studied changes in either the primary or secondary life cycle may also have a secondary effect on the market prices, and that this would equally affect the price of the primary product and of the collected scrap. This was the background for the so-called 50/50-rule suggested by Ekvall (1994) under the assumption that the supply elasticities of the “virgin” production and scrap were equal (i.e. that they would react to a price change with the same change in volume). Actually, the price elasticities are not equal (Ekvall 1999), and at the high recycling rates that exist in free markets with low entry costs (where the value of scrap is determined by the marginal cost of “virgin” production), the resulting volume change in collection is likely to be much less (probably often negligible) compared to the change in “virgin” production. This would support the above conclusion of applying rule 2 in the situation of expanding markets. Also in the case of a moderately shrinking market, where the supply from “virgin” production still plays a role, the difference in supply elasticities would imply that the “virgin” production will be affected most. However, in a rapidly shrinking market, the scrap can cover the entire demand and virgin supply would not be relevant. In this situation, a small change in volume of the secondary life cycle would only be able to affect the scrap collection, which is in line with our above conclusion of applying rule 3 in case of shrinking markets.
One of the reasons that recycling has been thought to demand a separate allocation procedure has been that - when the recycling rate is below its environmental optimum - both the user of scrap materials and the supplier of scrap may need an incentive to increase recycling, and that it is therefore important that the environmental advantage of increased use of recycled materials is distributed over the actors in the way that actually stimulates an increase the recycling rate. Furthermore, as the same material may be used over and over again in several consecutive life cycles, it has been seen as “unfair” if only the first or the last life cycle should carry the burdens of extraction and waste treatment.
The procedure presented here provides a clear cut-off between the individual life cycles, determined by whether there is an inflow of “virgin” material or not. In an expanding market, all life cycles affect the amount of “virgin” material extraction, and only the production that ensures an increase in the collection (by providing more material for recycling, or by specifically increasing recycling capacity, either technically, by economic support in parallel to the option of cross-subsidising suggested in section 4.3, or by stimulating political intervention) will be credited for the resulting increase in recycling (displacement of “virgin” extraction and decrease in waste handling). In a decreasing market without “virgin” inflow, all life cycles that utilise scrap products will be credited for the resulting increase in recycling (decrease in waste handling), and no life cycle will be credited for supplying additional material to recycling (since this would just mean that an equivalent amount would require waste treatment elsewhere). In this way, the procedure does not provide support for general incentives for using or supplying scrap, but provides an incentive for using scrap when the market for the material in question is decreasing, and for supplying scrap when the market is expanding, which is exactly what is needed to increase recycling in these two respective situations. When the recycling rate is below its environmental optimum, the procedure furthermore gives credit for specific actions that increase recycling capacity.
In some situations, the recycled material cannot displace “virgin” material, either because its technical properties have been reduced (e.g., paper fibres that become shorter for each recycling, so that after approximately six cycles they are so short that they must be discarded), or because it has been contaminated (e.g. copper in iron scrap, and silicon alloys of aluminium that cannot be recycled with the ordinary aluminium scrap). In these cases, sometimes described as downcycling, several distinct markets may exist for different qualities of recycled material, and the displacements that will occur will be determined by the supply and demand on these markets. If a demand for a specific scrap quality is not satisfied completely, scrap of higher quality or virgin material may be used, while scrap of lower quality cannot be used. When upstream processes deliver more scrap than the capacity of its downstream markets, some of the scrap will not be used. Thus:
- A change in demand for a specific scrap quality will affect the next upstream, unused supply and will displace waste there. If all upstream supplies are used fully, it will affect “virgin” production.
- A change in supply of a specific scrap quality will affect the next downstream, unsatisfied demand. If no downstream markets have unsatisfied demands, the scrap produced will not be used, thus affecting the immediate waste treatment.
A change in demand for a specific product, produced with scrap material, will cause both of the above.
In the case of contamination of virgin material, it should be noted that it is not only the current market situation that must be considered, but rather a very long-term market situation. As long as the current demand for scrap qualities is larger than the supply, all the contaminated scrap will be used and will displace “virgin” material. The contamination will be diluted due to the constant inflow of virgin material. However, at some stage in the future the scrap markets may become saturated, so that the contamination becomes a limitation for the recycling (this is already happening with copper contamination in iron scrap). The current contamination may thus lead to a future need for waste treatment of the contaminated material, or at least to a different displacement than on the current market (see e.g. Kakudate et al. 2000, Holmberg et al. 2001). It is this future market situation that should be used to determine what processes to include in the system expansion, since the immediate displacement of “virgin” material is only a temporary postponement of the necessary supply of “virgin” material in the future situation, when the contaminated material can no longer be used. The need to take into account these future effects is included in the third sentence of rule no. 2 of Box 3: “If there are differences between a dependent co-product and the product it displaces, and if these differences cause any changes in the further life cycles in which the co-product is used, these changes shall likewise be ascribed to product A.”
For materials where the technical properties are reduced on recycling, each additional life cycle will imply a change in the quality of the material in the recycling pools, influencing the requirements for supplies of “virgin” material to the pools. The need for new material may be caused e.g. by degradation of fibres or polymers, as can be seen with paper or plastics. Thereby, the change in material quality may also be expressed as a change in the ability of the material to displace “virgin” material. A life cycle that delivers as much material to recycling as it receives will cause a change in material quality equivalent to the amount of “virgin” material supply that is needed to compensate for the reduction in technical properties. When less material is sent to recycling than what is received (i.e. when material is sent to waste treatment), the change in requirements for supplies of “virgin” material to the recycling pool (the change in displacement ability) will depend on the actual quality of the material that is thereby leaving the recycling systems. The quality (the ability to displace “virgin” material) can be estimated specifically by the physical properties or be calculated theoretically from the average recycling rate in the specific recycling pool, since the material quality will be reverse proportional to the recycling rate (with a low recycling rate the supplies of “virgin” material will be relatively large, which gives a relatively high material quality in the recycling pool – and opposite with a high recycling rate).
The EDIP’97-method (Wenzel et al. 1997) applies a factor, called the grade loss, to express the loss of grade or material quality on recycling. This grade loss is used as an allocation factor, in that every life cycle using the material is burdened with this fraction of the primary material production. The grade loss is calculated as the percentage of virgin material that must be introduced on recycling. Therefore, in terms of system expansion, the grade loss is equivalent to the difference between the amount used in a lifecycle and the amount displaced by the recycling from this life cycle, expressed in percentage of the amount used, i.e. the change in displacement ability as explained in the previous paragraph. Thus, given the same information on displacement, the EDIP‘97-procedure will lead to the same result as the procedure presented here. Note, however, that he EDIP’97-method does not take into account the situation where the recycling pools are not utilised fully, which implies e.g. that in EDIP’97 the recycling process is always ascribed to the preceding life cycle.
Example:
In paper recycling, it may be assumed that paper fibres can only be used on average 6 times since the fibres become shorter and eventually must be discarded, so that each life cycle will imply an average loss of 17% of the “virgin” material. In EDIP’97-terminology this is expressed by a grade loss for paper of 0.17 per use, which means that a life cycle that receives 1 ton of recycled paper and after use sends 1 ton to recycling should be ascribed 17% of the exchanges from the primary production of 1 ton of paper and 17% of the exchanges from disposal of 1 ton of discarded fibres. In the terminology of system expansion, the life cycle that receives 1 ton of recycled paper (under the condition of full utilisation of the specific recycling pool and that “virgin” paper is displaced in the proportion 1 to 1) shall be ascribed a consumption of 1 ton of “virgin” paper, and – when 1 ton is sent to recycling after use – be ascribed the waste treatment from this (the scrapping of 170 kg discarded fibres) and be credited for the displacement ability of this after one life cycle (830 kg primary production; again under the condition of full utilisation of the recycling pool). The result is that this life cycle is ascribed 170 kg primary production and 170 kg waste treatment, exactly equivalent to the 17% of the used amount of 1 ton prescribed by the EDIP’97-method. When less material is sent to recycling than what is received, or when the receiving market is saturated, less “virgin” material is displaced, depending on the material quality in the lost material, for example the displacement ability of recycled newsprint in Denmark in 1995 could be estimated to be 50% (based on a realised recycling rate of 65%) and for corrugated board with a recycling rate of 75% the displacement ability will be approximately 32% (meaning that for each time 1 ton of corrugated board is sent to waste treatment, the requirement for “virgin” material in the recycling pool is increased with 320 kg). The displacement ability is directly corresponding to the concept of “residual material grade of scrap” in the EDIP’97-method.
5.8 Services as co-products
The situation where the co-products are services (e.g., waste treatment or transport) has also been regarded as presenting distinct allocation problems, also known as multi-input allocation because the co-products are typically related to physical inputs to the process (e.g., the waste to be treated, or the goods to be transported).
In the procedure presented here, the same method is used for service products as for material products (goods). The typical examples used are combined transport and combined waste treatment. It appears that most service outputs supplied to multiple product systems can be independently varied, and therefore treated already by step 1 of the procedure (see figure 5.3). However, we have been able to find at least one example of a joint waste treatment service that requires the use of system expansion (joint neutralisation of waste acids and bases):
Example:
The neutralisation of waste liquids with extreme pH-values can be done by proportional mixing, where one waste neutralises the other. The waste-based neutralisation process thus supplies two services: Waste-based acid neutralisation and waste-based alkali neutralisation. If the two wastes are not available in the right proportions, the amount of waste-based neutralisation is determined by the least available waste. If there is more alkali than acid waste available, the remaining alkali waste must be neutralised by “virgin” acid. In this situation, an additional demand for acid neutralisation (the determining product) will lead to additional waste-based alkali neutralisation, displacing alkali neutralisation by “virgin” acid. An additional demand for alkali neutralisation (the non-determining product) must be satisfied by neutralisation by “virgin” acid (since all waste acid has already been used).
Secondary functions of forestry and agriculture, such as maintaining rural income and maintenance of landscapes for recreation, may also be used as examples of service co-products that can be treated by the procedure in complete parallel to physical products. As the name implies, these functions are typically secondary compared to the production of physical products. Thus, the secondary functions may be regarded as non-determining co-products, while the physical product (e.g. wheat or wood) is typically the determining product. The demand for the physical product can change either as a result of changes in the market or changes in crop specific subsidies. In both cases, the fulfilment of the secondary functions is affected (e.g. causing changes in rural income or landscape maintenance compared to the desired output of these functions). This change may or may not be counteracted by alternative measures, but can in both situations be covered by rule no. 2 of section 5.2. The affected alternative measure (i.e. the most sensitive measure for supporting rural income or for landscape maintenance, respectively) depends on the current policies in the specific situation. In some situations, the so-called secondary functions may in fact be the primary concern, e.g. when rural income support is administered per land area or when landscape maintenance is rewarded without requirements to what crops should be grown. If this source of income leads to changes in the production, the subsequent change in composition of product output may be one of the side-effects that has to be accounted for by including the alternative production displaced. This may involve a number of subsequent changes on different markets.
5.9 Complex situations
The situation described by figure 5.1 is a simplification, in that it shows only one determining and one dependent co-product (i.e. only two products coming out of process A) and none of the other processes have co-products. Therefore, this section deals with the more complex situations:
- where process A has more than two co-products,
- where multiple products result from the intermediate process or where the dependent co-products have other applications than in process B, and
- where the displaced process has multiple products.
More than two co-products seems to be rather the rule than the exception when processes have more than one product, as can be seen from most of the examples in the previous sections. This, however, poses no problem for the procedure. Each co-product can be treated separately:
- when studying a change in output of a determining co-product, and there are more than one dependent co-product, the consequences for each of the dependent co-products can be analysed in isolation, one at a time,
- when studying a change in output of a determining co-product, and there are more than one determining co-product, the changes in the co-producing process can be analysed in isolation, separately from the analysis of any dependent co-products,
- when studying a change in output of a dependent co-product, the only thing to be investigated is whether the dependent co-product is utilised fully or not, which can be done without concern for any of the other co-products.
Multiple products resulting from an intermediate process (i.e. a process occurring after the split-off point and before displacing other products) means that the dependent co-product is split up in two or more fractions, each following its own route. Each fraction may be fully utilised in other processes (rule no. 2 of section 5.2) or only partly (rule no. 3). Each fraction can be treated separately, although fractions that follow the same rule may be treated together for convenience (listing the affected products and processes together). Even when the co-product is not composed of separable fractions, it may have many different applications. Then, the process to be considered in the system expansion is the application most sensitive to a change in supply (as identified by the procedure in chapter 4).
Displaced processes that have multiple products, of which the displaced product is only one, will require a repetition of the procedure for each of the co-products from the displaced process. If this leads again to another process with multiple products, as illustrated in figure 5.4, one might fear that this system expansion would continue without end. However, the number of possible processes involved in the system expansion is limited by the very procedure, since:
- the number of markets affected by each displaced process is limited, and the displaced process is only that specific supplier to each market, which is most sensitive to a change,
- the three rules for system expansion (section 5.2) provides clear cut-offs between the different product systems involved (either a process is included or excluded from the studied system),
- for each time the system expansion is iterated, both the economic value and the volume of the displaced processes tend to decrease, because in each iteration the avoided product is the determining co-product of the displaced process and therefore typically of higher value (and often also larger in quantity) than the dependent co-products which go on to the next iteration.
Example: In Europe, the co-production of chlorine and sodium hydroxide involves a displaced production of sodium hydroxide (see also example in section 5.4), which can be identified as the combination of the Solvay process: 2NaCl + CaCO3 ⇒ Na2CO3 + CaCl2 and the lime-soda process (caustification): Na2CO3 + Ca(OH)2 ⇒ + CaCO3 with recycling of the calcium carbonate, giving net process: 2NaCl +Ca(OH)2 ⇒ 2NaOH + CaCl2. Caustification is not a commercial process, but it is used by industry (Kirk-Othmar 1978, van Santen 1998a). Thus, this displaced production route has a co-product, calcium chloride, which can be used for de-icing and dust control because of its hygroscopic properties. However, it is not a very valuable product and part of it is deposited (Moody 1969, Gerhartz 1985). Thus, following rule no. 3, the displacement of the alternative production route for sodium hydroxide will lead to a reduction in calcium chloride deposition. In summary, chlorine will be ascribed the displacement of the alternative production route for sodium hydroxide and credited for the reduced calcium chloride deposition. Using the nomenclature of figure 5.4, the cut-off is after process D and W2, since there is no displacement of alternative supplies to process C (de-icing and dust control with calcium chloride), i.e. process E does not exist, since there is adequate unused supplies in W2.
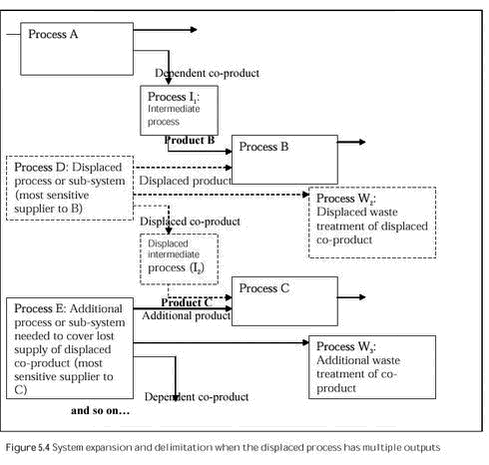
Click on the picture to see the html-version of: Figure 5.4
In Weidema (2003) an example is provided of an iterative solution of the joint production of ethylene and propylene from steam-cracking, where an additional output of ethylene yields also an output of propylene, the displaced production of which again leads to a by-product of ethylene and so on. Below, a similar example with joint production of protein and vegetable oil is given. This example was first published in Weidema (1999).
Example:
Protein by-products from the food industry displace the most sensitive protein source, which is soy meal (see section 4.8). Besides protein, soy production yields the co-product soy oil. The displaced soy oil production will thus lead to an increase in the most sensitive alternative supply of edible oil, which is rapeseed oil (see section 4.8). This gives then an additional amount of rape seed protein as a co-product, which then again displaces more soy protein and so on. Since only two global markets are involved (the fodder protein market and the edible oil market), this loop can easily be closed. The calculation is based on the relative content of oil and protein in the two products. Since soy beans yields half as much oil as protein, while rape yields just the opposite ratio, it can easily be seen that for every amount of soy protein displaced, half the amount of oil is displaced, leading to the displacement of again half of this amount of protein, i.e. 25% of the original amount of protein.
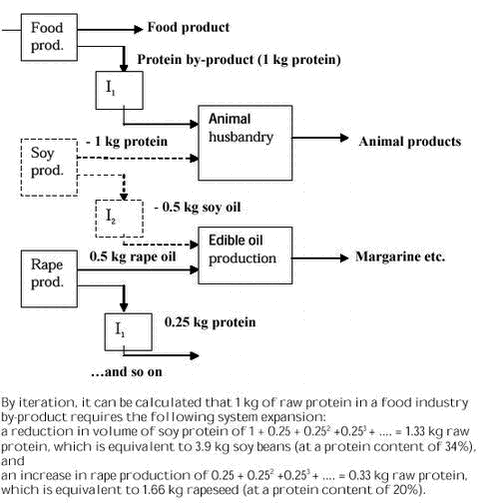
Click on the picture to see the html-version of: Figure
This may also be expressed as the solution to a system of linear equations. If the products are named a and b, the suffixes A and B signify the originating processes, and the 1 represents the desired product output: aA + aB = 1 bA + bB = 0 this system may be solved by iteration or by Gauss-Jordan elimination when expressed in matrix form.
This is simply a specific case of the general solution for a life cycle inventory with the normalised output of 1 unit of a. While the system described above is limited to the product outputs from the co-producing and displaced processes, a standard product system include also the upstream and downstream processes and their product flows (product inputs to a downstream processes expressed as negative amounts in the downstream process).
Therefore, the solution can be generalised to any number of products a, b, c, etc. and any number of processes A, B C. etc. Below an example is provided with 5 interdependent fishery processes which all produce two or more of the 5 fish products.
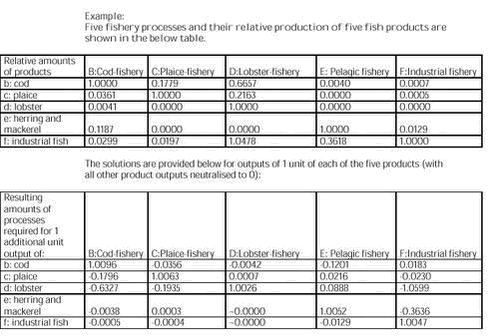
Click on the picture to see the html-version of: Example
This shows that any complexity of co-products can be handled simply by including the affected processes in the product system and using the standard procedure for solving the system (by either iteration or matrix reduction). The most difficult part is thus not the mathematical solution, but the identification of the affected processes and the acquisition of environmental data for these processes.
As part of the Dutch methodology project (Guinée et al. 2001), we had the opportunity to show how the procedure presented in this chapter compares to an economic allocation of the same relatively complex system, namely that of a (hypothetical, simplified) refinery, both receiving co-products (waste from other processes) and supplying a number of both joint and combined co-products. This example (first published in Guinée et al. 2001, part 2b, pp. 36-41 where our method was named “symmetrical substitution method”) is reproduced in annex A, while the economic allocation of the same refinery process can be found in Guinée (2001, part 2b, pp. 32-35).
5.10 Traditional co-product allocation as a special case of the presented procedure
In traditional co-product allocation, the exchanges of the co-producing process is partitioned and distributed over all the co-products according to a product specific allocation factor between 0 and 1, and there is no inclusion of intermediate and displaced processes.
Expressed in the terms of consequential LCA, this implies that for any co-product, the co-producing process is assumed to react to an increase in demand with an increase in production volume in proportion to the product specific allocation factor. For example, a demand of 1000 kg of a co-product with the allocation factor 0.1 will lead to an increase in production volume of the co-producing process resulting in an increase in output of 100 kg of the demanded co-product. This further implies that the remaining part of the demand (here 900 kg) is covered by an alternative supply and/or a reduction in consumption elsewhere, and that the environmental impacts of this are assumed negligible, since the system is not expanded to include this alternative supply and/or changed consumption and related processes.
In a joint production, the increased production volume of the co-producing process implies an equivalent increase in the output of the other joint products. In traditional co-product allocation, since the system is not expanded to include the further fate of these joint products (displacement of alternative supply, increase in consumption and/or waste handling), the implied assumption is that this further fate is having negligible environmental impacts.
This may lead to serious inconsistencies when the alternative supply, consumption or waste handling is included elsewhere in the same product system. For example, in a product recipe using both sunflower oil and soy beans, a traditional allocation of the sunflower production would allocate part of the sunflower production to the sunflower protein cake, but not include the soy production displaced by this additional supply of sunflower protein, while the same soy production would be included for the soy beans used directly in the recipe.
However, there may be situations in which the reaction of the co-producing process to an increase in demand for its co-products is proportional to specific allocation factors, and where at the same time neither alternative supply, consumption, nor waste handling of the co-products will be affected. This is the case when:
- several co-products are determining the volume of the co-producing process in different periods within the time horizon of the study, so that the exchanges of the co-producing process can be allocated over the co-products in relation to the relative lengths of these periods20, and
- the co-products can be stored (without additional environmental impact) during the periods that they are not determining, so that no additional intermediate treatment and no displacement occurs.
Thus, in such a situation, the traditional co-product allocation may be regarded as a special case of the procedure in figure 3.2.
As mentioned in section 5.4, several joint products may influence the production volume of a joint production in proportion to their share in the gross margin of the joint production, when the normalised market trend of all the joint products is aligned as a result of constraints in alternative production routes. In this situation, co-product allocation according to gross margin may correctly reflect the way the co-producing process will be affected. However, as there is no storage of co-products (exactly because the markets are cleared), intermediate treatment and consumption of the co-products will be affected, and the co-product allocation must be supplemented by a system expansion with the affected processes.
As a more academic question, it may be asked whether the entire procedure presented in this chapter could be called “co-product allocation,” rather than a way to avoid allocation. This basically depends on the original viewpoint. If the co-products and their further fate are originally regarded as being outside the studied system, it is reasonable to regard the presented procedure (in which the changes in the processes affected by the change in amount of co-products are added or subtracted from the studied system) as a way to avoid allocation. If the originally studied system is regarded as including the co-products (and their further fate, as well as the processes that the co-products may displace), the presented procedure can be regarded as an allocation of the different changes in production volumes over the different co-products. The word “ascribed” in the four rules can be replaced by “allocated”, and the procedure of “crediting” can be understood as “allocating the decrease in production volume to”. In that case, the term “system expansion” is a misnomer, and should preferably be named “market-based allocation”.
In the ISO standard 14041, system expansion is regarded as a way to avoid allocation, and we have therefore maintained this viewpoint in the present chapter. Step 1 in the procedure in figure 5.3 (dealing with combined production) is equivalent to step 2 in the ISO procedure (allocation according to physical relationships), but because the output of all other co-products are kept constant, these co-products may as well be regarded as being originally outside the studied system, meaning that there is no allocation problem. The entire presented procedure can therefore be regarded as “avoiding allocation.”
5.11 Relation to the procedure of ISO 14041
Because – as shown in this chapter – system expansion is always possible for cases of joint production in consequential LCA studies, the stepwise procedure of ISO 14041 (ISO 14041, clause 6.5.3) will lead to the same results as the procedure presented in figure 5.3:
- Step 1 in the ISO procedure requires that system expansion shall be performed wherever possible. As shown above, this applies to all cases of joint production in consequential studies.
- Step 2 in the ISO procedure requires that, when ISO step 1 cannot be applied, allocation shall be done “in a way which reflects the underlying physical relationships between them” (“them” being the co-products), i.e. reflecting “the way inputs and outputs are changed by quantitative changes in the products.” This is also known as allocation according to physical causalities (Guinée et al. 2001) and is equivalent to step 1 of the procedure in figure 5.3. This step is relevant for cases of combined production in consequential studies. The order of step 1 and 2 in the ISO procedure is not significant for the result of applying the procedure, see below.
- Step 3 in the ISO procedure provides the option to allocate according to the relative economic value of the co-products21. For consequential studies, all possible cases of co-production (combined and joint) were covered by ISO steps 1 and 2, which means that ISO step 3 is only relevant for attributional studies. It should be noted that ISO step 1 and 2 could also be applied to “hypothetical consequential” studies that analyse hypothetical, historical changes (see sections 1.2 and 5.1).
Since each step in the ISO procedure can be related to a specific group of cases (step 1: joint production in consequential studies; step 2: combined production in consequential studies; step 3: attributional studies) the step-wise nature of the ISO procedure is unnecessary. Simply describing the application area of each step in the procedure, as suggested here, would give a more straightforward presentation.
In the procedure presented in this article, step 1 deals with combined production (ISO step 2), while steps 2 to 4 deals with system expansion (ISO step 1), because it appears more logical to deal first with the simple case, where the outputs of the other co-products can be kept constant without system expansion, before dealing with the more complicated cases, where the outputs of the other co-products can only be kept constant by applying system expansion.
However, in practice the order does not matter. If applying system expansion to a case of combined production, the same result will be obtained as when applying the simpler procedure of step 1 of the procedure presented in this article. In fact, step 1 can be treated as a special case of the model for system expansion if the limiting parameter for the combined production is seen as the determining co-product, and the non-limiting parameters as the dependent co-products.
Example:
In a situation where combined transport is weight-limited, the determining co-product could be described as “transport of weight (mass)”. The dependent co-product “transport of volume” is not utilised fully. An additional demand for transport of volume alone (i.e., provided it has no weight!) can be satisfied without changes in the co-producing process, that is, the co-producing process is fully ascribed to the determining co-product (rule no. 1). If the co-transport is substituting another transport (i.e., a separate transport of a light-weight product), it is the transport of this light-weight product that benefits from shifting to co-transport, because the unutilised volume in the co-transport would else have been wasted (although not requiring any waste treatment!). This is a variation of the reasoning behind rule 3.
Step 2 of the ISO procedure may also be regarded as a special case of the very first procedural step of the ISO procedure, which we have ignored in the above presentation, namely the obvious option of avoiding allocation by subdividing the process into sub-processes that only produce one product. Such a subdivision is obviously not possible for joint production as is mainly relevant when “black box” data have been collected for a production that is in fact an aggregate of independent production lines. However, in consequential LCA, combined production may be regarded as such independent production lines, since it is possible to measure the independent reaction of the co-producing process to variation in output of each co-product separately.
When step 2 of the ISO procedure is regarded as describing special cases of either process subdivision or system expansion (both termed “avoiding allocation” in ISO 14041), it would be more relevant to include it in step 1, before the description of system expansion, i.e. resulting in the same order as in the procedure in figure 5.3.
Besides the three-step procedure, ISO 14041 (section 6.5.2) prescribes an allocation principle, which has popularly become known as “the 100% rule”: “The sum of the allocated inputs and outputs of a unit process shall equal the unallocated inputs and outputs of the unit process”, i.e. there should not be any exchanges that are allocated twice or not allocated at all. Although, according to the ISO text, this principle applies only to allocation and not to avoiding allocation, it is worth noting that the procedure presented in this article adheres to this principle: The three rules in section 5.2 ensure that all processes are fully ascribed to (allocated to) either one or the other co-product.
____________________________________________________________ 15 An early version of this chapter was published as Weidema 2001a. 16 Other allocation problems in LCA include the allocation of products over different functions, the allocation of aggregated environmental data over individual processes, the allocation of emissions over different environmental compartments, and the allocation of emissions over parallel or serial environmental mechanisms. 17 This is parallel to the implicit assumption of the procedure in chapter 4 (see section 4.1) and as suggested there, separate scenarios should be applied when this assumption is regarded as too simplified (especially as it may change over time, depending on location, and depending on the scale of change). This implies that when more than one joint product is found to be determining within the studied scale or geographical or temporal horizon, a scenario may be calculated for each joint product that may be determining. These scenarios may be kept separate or added up to form averages, weighted in proportion to the influence of the different co-products. Such a weighted average of scenarios have close relations to an allocation of the co-producing process (see section 5.9). 18 In an early version (Weidema 2001a), a fourth rule was included, covering the situation when a dependent co-product does not displace any other product. With the current wording of the rules, this situation is now regarded as a special case of rules 2 or 3, depending on whether the co-product is fully utilised or not; see also section 5.5. 19 In the early version of the described procedure (Weidema 2001a), this situation was described by a special fourth rule, in addition to the three rules in section 5.2, while it is now seen simply as a special case of the second point in rule 2, namely that the intermediate treatment shall be ascribed to product A (the determining product for the co-producing process). 20 This may also be expressed in terms of relative influence of the co-products on the production volume of the co-producing process, which may be represented by long-term price elasticities. As a further approximation, allocation factors based on revenue or gross margin (as in cost allocation) may be seen as proxies for price elasticities. 21 The ISO text states “in a way which reflects other relationships between them” (i.e. between the co-products). The close parallel to the wording in step 2 of the ISO procedure reveals that it is still causalities that are intended as allocation factors. Thus, step 3 should not be seen as an opening for any arbitrary allocation key (Jerlang et al. 2001), as this would also render the standard meaningless on this point. In practice, economic causality is the only non-physical causality that has so far been suggested as allocation key.
| Front page | | Contents | | Previous | | Next | | Top |
|