| Front page | | Contents | | Previous | | Next |
Identification and assessment of alternatives to selected phthalates
5 Technical and economical assessment of alternative plasticisers
5.1 ASE (Alkylsulfonic phenylester)
ASE is a mixture of similar esters of sulfonic acids, phenyl and C10 – C18 alkanes (mixture CAS 70775–94–10). It is marketed by Lanxess (formerly Bayer) under the product name Mesamoll.
Producer's description (extracts)
The producer Lanxess presents ASE as having the following characteristics (Lanxess, 2009b):
- Outstanding gelling capacity with a large number of polymers including PVC and polyurethanes, resulting in lower processing temperatures and shorter processing times.
- High saponification resistance, especially compared to DEHP, due to ASE's chemical structure; this is especially beneficial for articles which come into contact with water and alkalis.
- Good compatibility with a large number of polymers such as polyurethane (PU), polyvinyl chloride (PVC), natural rubber (NR), styrene-butadiene rubber (SBR), blends of styrene-butadiene rubber and butadiene rubber (SBR/BR), isobutylene-isoprene rubber (IIR), acrylonitrile-butadiene rubber (NBR) and chloroprene rubber (CR)
- Outstanding resistance to weathering and light.
- Good dielectric properties which give plasticised PVC outstanding weldability at high frequencies leading to shorter cycle times than with other plasticisers.
Application and market experience
Lanxess has provided information on application areas for ASE among the traditional DEHP, DBP and BBP applications shown in Table 5.1. The table also indicates the level of market experience in each application area according to Lanxess (2009; interpreted from qualitative text by the report authors). Note that Lanxess has indicated significant market experience for most applications, indicating both general plasticiser characteristics and coverage of several of the special performance characteristics of DBP and BBP.
A Danish study (Nilsson et al., 2002) demonstrated the feasibility of ASE as alternative to phthalates in waterbeds (in the plastisol saturated textile lining), where it is used today.
Table 5.1 Applications of ASE and level of market experience in each application, data from Lanxess provided for this study
Application |
Market experience *1 |
Substituting for DEHP |
|
Polymer applications: |
|
Calendering of film, sheet and coated products |
2 |
Calendering of flooring, roofing, wall covering |
4 |
Extrusion of hose and profile |
2 |
Extrusion of wire and cable |
2 |
Extrusion of miscellaneous products from compounds |
2 |
Injection moulding of footwear and miscellaneous |
? |
Spread coating of flooring |
2 |
Spread coating of coated fabric, wall covering, coil coating, etc. |
2 |
Car undercoating |
2 |
Non polymer applications: |
|
Adhesives/sealant, rubber |
2 |
Lacquers and paint |
2 |
Printing ink |
2 |
Production of ceramics |
|
Substituting for DBP |
|
Plasticiser in PVC |
2 |
Plasticiser in other polymers |
2 |
Adhesives |
2 |
Printing inks |
2 |
Miscellaneous: |
|
Sealants |
2 |
PU foam sealants |
2 |
Nitrocellulose paints |
2 |
Film coatings |
3 |
Glass fibre production |
|
Cosmetics |
|
Substituting for BBP |
|
Polymer applications: |
|
General PVC (e.g. for moulded plastic parts) |
2 |
Plastisol coating, for flooring |
2 |
Extrusion or spreadcoating: Leather and cloth coating (e.g. for furniture, shoes, bags, suitcases) |
2 |
Films, calendering (e.g. for packaging, calendered flooring, wall covering, etc.) |
2 |
Non polymer applications: |
|
Sealants (polysulfide based, polyurethane foam sealants, acrylic based; e.g. for windows, construction etc.) |
2 |
Coatings and inks (e.g. for car care products, construction, paper, board) |
|
Adhesives (polymer based, e.g. for construction, paper) |
2 |
*1: Market experience categories interpretation: 1) Main alternative on market. 2) Significant market experience. 3) Examples of full scale experience. 4) Pilot/lab scale experience.
Key characteristics
Table 5.2 below describes some key characteristics of ASE as alternative to DEHP, DBP and BBP.
Table 5.2 key characteristics of ASE as alternative to DEHP, DBP and BBP
Parameter |
Value |
Remarks |
Efficiency( as plasticiser in PVC compared to DEHP)*1 |
NA |
|
Price (primo 2009) |
€1,75/kg |
Lanxess (2009) |
Price relative to DEHP (≈0.8-1€/kg in 2008/2009; 1€ used for calculations) |
175% |
|
Effective price relative to DEHP |
NA |
|
Compatibility/solubility in PVC |
|
Good (Lanxess, 2009, 2009b) |
Permanency (migration, evaporation, extraction) |
+ |
High resistance to extraction by saponification (extraction with soap water), (Lanxess, 2009, 2009b) |
Processability (fusing speed and temperature, viscosity, etc.) |
+ |
Low gelling temperature. Faster gellation/fusing speed than DEHP; lower than BBP and DBP (Wilson, 1995; Lanxess, 2009, 2009b) |
Limitations in use, if any, noted by supplier |
|
Not suitable for polysulfide based sealants (Lanxess, 2009, 2009b) |
Notes: *1: Effectiveness indicator, also called substitution factor, indicating the concentration of plasticiser in PVC needed, compared to DEHP, to achieve a specified flexibility according to a well defined method. DEHP has substitution factor 1 per definition, while plasticisers needing lower concentration (more effective) have lower values, and plasticisers needing higher concentrations have higher effectiveness value. *2: According to Lanxess, 2009, 2009b. NA = not available
Table 5.3 below shows some performance data for ASE compared to DEHP. As shown, performance parameters are quite close to DEHP's, except for a higher resistance to kerosene (jet-fuel, lipophilic solvent).
Table 5.3 Technical key parameters of ASE in PVC compared to DEHP (from Sears and Darby, 1982)
Plasticiser in PVC, conc. 40% =67 phr in same PVC resin |
Shore A hardness |
Volatility,% lost, 1 day at 87 °C over activated carbon |
Extracted in water,% |
Extracted in kerosene (jet fuel, etc.),% |
DEHP |
69 |
4.5 |
0.01 |
44 |
ASE |
72 |
5.3 |
0.03 |
4.8 |
Wilson (1995) states, that were it not for the higher prices of ASE, it could easily be used as an alternative to the general purpose phthalate plasticisers in a wide range of applications. Its structure gives it some advantages over phthalates for certain processes and aggressive environments. The higher polarity results in faster gelling speed than can be achieved with other plasticisers at similar molecular weight and volatility. ASE has high resistance to degradation from weathering, microorganisms and alkaline media.
Conclusions
Based on the above mentioned, it seems reasonable to conclude that ASE appears - based on technical observations only - to be an actual general plasticiser alternative to DEHP. The producer, Lanxess, has indicated significant market experience for most traditional DEHP, DBP and BBP uses, indicating both general plasticiser characteristics and coverage of several of the special performance characteristics of DBP and BBP.
ASE was reported as used for toys by Danish toy manufacturers (with contract production in China), but was not found in the surveys of plasticisers in toys in the Netherlands and Switzerland.
The significantly higher price currently may, however, likely be an impediment to widespread substitution. The potential for attaining reduced prices with increased production volume has not been investigated by the research made for this study.
5.2 ATBC (Acetyl tri-n-butyl Citrate)
ATBC consists of citrate with three ester bonded butyl groups and one acetyl group bonded to the fourth available oxygen atom, see the structure below. The CAS no. is 77-90-7. It is marketed by Vertellus (formerly Morflex), under the product name Citroflex A-4, and by Jungbunzlauer under the products name CITROFOL® BII.
Citrates (ATBC; acetyl tributyl citrate)
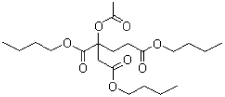
Producer's description (extracts)
Vertellus (formerly Morflex) has characterised ATBC as follows in their sales material (Vertellus, 2009b): ATBC is compatible with PVC resin, as well as with a range of other polymers. ATBC has mostly been used in products used for sensitive purposes such as medical products food contact products and children's toys. It is, however, too extractable to be useful in some of the applications in the medical area where contact with lipids is important. For such uses, the larger molecule n-butyryltri-n-hexyl Citrate is recommended by Vertellus. The higher molecular weight citric acid esters, including ATBC, are effective replacements for di-(2-ethylhexyl) phthalate (DEHP) and di-(2-ethylhexyl) adipate (DEHA). ATBC also has similar characteristics to some of the lower molecular weight phthalates in a variety of polymers. ATBC is widely used in food contact polymers. It provides many improvements over DBP in cellulose nitrate films, including lower volatility, better resistance to yellowing, and better adhesion to metals. ATBC is effective in solution coating both paperboard and foil. It is a good plasticizer for vinyl toys. ATBC Special is developed and recommended for medical articles and similar sensitive applications. It is manufactured in a unique, patented process. A special version for use in pharmaceutical coatings is sold as ATBC, PG.
Application and market experience
Vertellus has provided information on application areas for ATBC among the traditional DEHP, DBP and BBP applications shown in Table 5.4. The table also indicates the level of market experience in each application area according to Vertellus (2009).
Table 5.4 Applications of ATBC and level of market experience in each application (data from Vertellus provided for this study)
Application |
Market experience *1 |
Substituting for DEHP |
|
Polymer applications: |
|
Calendering of film, sheet and coated products |
3 |
Calendering of flooring, roofing, wall covering |
|
Extrusion of hose and profile |
3 |
Extrusion of wire and cable |
|
Extrusion of miscellaneous products from compounds |
2 |
Injection moulding of footwear and miscellaneous |
|
Spread coating of flooring |
|
Spread coating of coated fabric, wall covering, coil coating, etc. |
|
Car undercoating |
|
Non polymer applications: |
|
Adhesives/sealant, rubber |
2 |
Lacquers and paint |
|
Printing ink |
2 |
Production of ceramics |
|
Other applications (added to list by producer) |
|
PVC medical articles |
2 |
Toy and childcare articles |
1 |
Substituting for DBP |
|
Plasticiser in PVC |
2 |
Plasticiser in other polymers |
|
Adhesives |
3 |
Printing inks |
2 |
Miscellaneous: |
|
Sealants |
3 |
PU foam sealants |
4 |
Nitrocellulose paints |
2 |
Film coatings |
3 |
Glass fibre production |
|
Cosmetics |
|
Substituting for BBP |
|
Polymer applications: |
|
General PVC (e.g. for moulded plastic parts) |
|
Plastisol coating, for flooring |
|
Extrusion or spreadcoating: Leather and cloth coating |
|
Films, calendering (e.g. for packaging, calendered flooring, wall covering, etc.) |
|
Non polymer applications: |
|
Sealants (polysulfide based, polyurethane foam sealants, acrylic based; e.g. for windows, construction etc.) |
|
Coatings and inks (e.g. for car care products, construction, paper, board) |
3 |
Adhesives (polymer based, e.g. for construction, paper) |
|
Nails polish |
1 |
*1: Market experience categories interpretation: 1) Main alternative on market. 2) Significant market experience. 3) Examples of full scale experience. 4) Pilot/lab scale experience.
Note that Vertellus has indicated significant market experience for toys, medical articles, and certain non-polymer applications substituting for both DEHP, DBP and BBP, indicating both general plasticiser characteristics and coverage of some of the special performance characteristics of DBP and BBP.
In a study of alternatives to flexible PVC with phthalates, PVC products plasticised with ATBC were reported to match all of the technical requirements (Postle et al., 2000). Similarly, in a lab test of different alternatives to DEHP for their suitability as plasticisers in PVC for medical uses ATBC was found suitable on all technical parameters tested (Karbæk, 2003).
Key characteristics
According to ECPI, acetyl tributyl citrate is traditionally used in electrical coatings and casings because of its solvating characteristics. It is also used in inks, hair sprays and aerosol bandages (ECPI, 2009).
The table below (from Vertellus, 2009b) compares various characteristics of medical grade PVC with 50 parts by PVC weight plasticiser (= plasticiser concentration in PVC product 33,3% by weight), 2.5 parts by PVC weight stabiliser (Cl/Zn) and 0.25 parts by PVC weight lubricant (stearic acid), milled and pressure died to sheet (mechanical tests by ASTM methods; Vertellus, 2009b). A-4 is ATBC. T4 and Tf are torsion flex indicators at specific conditions (see Vertellus, 2009b).
Table 5.5 Comparison of ATBC (=A-4) with DEHP and DEHA for various parameters, from Vertellus (2009).
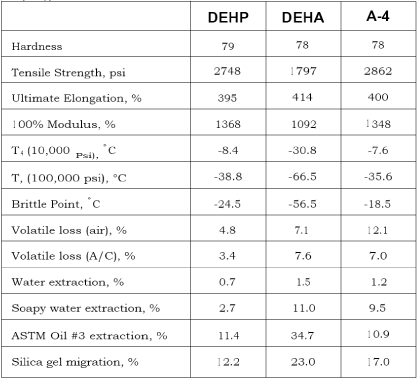
As shown, the mechanical tests and oil extraction for DEHP and A-4 = ATBC are very close, while losses to air and aqueous liquids are a factor 2-3 higher for ATBC. According to the reference, extraction and volatilization properties can be adjusted by adding another plasticiser, for example the less expensive epoxidized soybean oil (ESO).
Table 5.6 describes some key characteristics of ATBC as alternative to DEHP, DBP and BBP.
Table 5.6 key characteristics of ATBC as alternative to DEHP, DBP and BBP
Parameter |
Value |
Remarks |
Efficiency( as plasticiser in PVC compared to DEHP)*1 |
|
Equal to or slightly above 1 judged from Shore A hardness. |
Price (primo 2009) |
NA |
|
Price relative to DEHP |
300% |
ExxonMobil (2009); Karbæk (2003) |
Effective price relative to DEHP |
NA |
|
Compatibility/solubility in PVC |
|
Compatible |
Permanency (migration, evaporation, extraction) |
|
Extractability in medical appliances with lipid (fat) contact not found optimal, but losses to oil is found similar to DEHP. Losses to air and aqueous liquids are a factor 2-3 higher than for DEHP (Vertellus, 2009b). |
Processability (fusing speed and temperature, etc.) |
|
High solvating |
Limitations in use, if any, noted by supplier in data for this study |
|
None noted |
Notes: *1: Efficiency indicator, also called substitution factor, indicating the concentration of plasticiser in PVC needed, compared to DEHP, to achieve a specified flexibility according to a well defined method. DEHP has substitution factor 1 per definition, while plasticisers needing lower concentration (more effective) have lower values, and plasticisers needing higher concentrations have higher effectiveness value. NA = not available
Table 5.7 below shows some performance data for ATBC compared to DEHP, DBP and BBP. As shown, ATBC results in a similar hardness as DEHP and BBP, and volatility and extractability higher than DEHP and BBP, but lower than DBP (DBP is the smallest, most mobile molecule of these phthalates).
Table 5.7 Technical key parameters of ATBC in PVC compared to DEHP, DBP and BBP (from Sears and Darby, 1982)
Plasticiser in PVC, conc. 40% =67 phr in same PVC resin |
Shore A hardness |
Volatility,% lost, 1 day at 87 °C over activated carbon |
Extracted in water,% |
Extracted in kerosene (jet fuel, etc.),% |
DEHP |
69 |
4.5 |
0.01 |
44 |
DBP |
62 |
45.4 |
0.25 |
9.1 |
BBP |
68 |
7.7 |
0.07 |
3.4 |
ATBC |
73 |
17.8 |
0.09 |
|
A Danish toy producing company switched from DINP to ATBC (Citroflex A-4) for all toys for children under 3 years and for toys which are designed to go to the mouth. This particular plasticiser had been given a favourable opinion by the CSTEE for use in toys. However it suffered from a variety of technical drawbacks when compared with DINP. For instance ATBC would not take decoration, it had high migration into adjacent materials leading to swelling and splitting, and there was a need for tooling changes. Development led to the use of a mixture of ATBC, DINCH and DEHT, which could be blended in a variety of combinations to achieve softened PVC that performed to the required standards of safety and reliability with the existing production setup. These blends could be used in many cases as one-to-one replacements for DINP so that major changes to designs and tooling were not necessary.
Conclusions
The performance of ATBC on some parameters seems similar to DEHP, indicating technical suitability for substitution for some purposes. The producer, Vertellus, has indicated significant market experience for toys, medical articles, and certain non-polymer applications substituting for both DEHP, DBP and BBP, indicating both general plasticiser characteristics and coverage of some of the special performance characteristics of DBP and BBP.
ATBC was found in 9% and 10%, respectively, of products analysed in two European studies of large samples of toys and childcare articles. It was also reported as used for toys by Danish toy manufacturers (with contract production in China); used alone it did however not perform adequately in the established toy production setup due to migration to adjacent materials, print resistance, etc. Used in combination with DINCH and DEHT it could be used with no major processing changes.
The higher extractability in aqueous solutions and the higher volatility may reduce the performance of ATBC as a plasticiser in PVC, and could perhaps limit its use for certain applications. Similarly, the extractability in medical appliances with lipid (fat) contact may perhaps limit its use for certain medical applications.
The price of ATBC is significantly higher than the price of DEHP, and this may represent a major impediment for its wider use as alternative to DEHP; DBP and BBP.
5.3 "COMGHA1" (12-(Acetoxy)-stearic acid, 2,3-bis(acetoxy)propyl ester)
12-(Acetoxy)-stearic acid, 2,3-bis(acetoxy)propyl ester is the main constituent (ca. 84%) in a plasticiser consisting of two castor oil derivatives designated as "COMGHA" (by SCENIHR, 2008) and marketed as Soft-n-Safe by Danisco. The other main component (ca. 10%) is octadecanoic acid, 2,3-(bis(acetoxy)propyl ester. Both main substances are shown below (from, SCENIHR, 2008). The remaining 5% are excess glycerine from the production. In the following technical text, this mixed product is therefore described. The CAS number of the mixture is 736150-63-3.
"COMGHA1" , 12-(Acetoxy)-stearic acid, 2,3-bis (acetoxy)propyl ester;
CAS: 330198-91-9
"COMGHA2" , Octadecanoic acid, 2,3-(bis(acetoxy) propyl ester;
CAS: 33599-07-4
Producer's description (extracts)
Danisco characterises COMGHA/Soft-n-safe as follows (Danisco, 2009b):
COMGHA is an efficient, one-to-one replacement for most conventional plasticisers, such as phthalates. In tests, the quality, durability and functional properties achieved have proven equivalent to phthalate-based solutions. Not only that, COMGHA can be directly applied, without any further alteration to the formulation or processing.
COMGHA has been tested against traditional plasticisers in many PVC applications. Compared with plasticisers such as DEHP, DINP and DOA, the efficiency and reliability of COMGHA is consistently on top.
The main application areas for COMGHA are:
- Food contact applications
- Plastisol production
- Medical devices
COMGHA has been compared with DEHP in numerous flexible PVC applications that perform a sensitive medical role, including tubing and medical film. The test results show that COMGHA meets all requirements in the extrusion, calendaring and injection moulding applications where it has been evaluated. In medical applications where plasticiser migration is a particular concern, COMGHA demonstrated high extraction resistance in aqueous and oily solvents.
Compared with traditional plasticisers such as DEHP and DINP, COMGHA performs consistently well in applications such as vinyl flooring, wallpaper, shrink wrap film, textile dyes, ink applications, adhesives and sealants. In application tests with toys for young children, COMGHA provided the same level of efficiency as DEHP, when measured according to the Shore A scale.
While COMGHA has a significantly higher molecular weight than DEHP and a comparable molecular weight to TOTM, its efficiency remains on top. This makes it a viable candidate for applications that demand low volatility. TGA analysis has shown that COMGHA is considerably less volatile than DEHP under all conditions. Although the novel plasticiser is more volatile than a high end permanency plasticiser as TOTM, the lower loading level required means overall volatility is reduced.
Application and market experience
Danisco has provided information on application areas for COMGHA among the traditional DEHP, DBP and BBP applications shown in Table 5.8. The table also indicates the level of market experience in each application area according to Danisco (2009). Note that COMGHA still has relative moderate market experience, albeit with many examples of full scale usage and pilot/lab scale tests, and significant market experience in plastisol applications and cosmetics.
Table 5.8 Applications of COMGHA and level of market experience in each application, data from Danisco provided for this study
Application |
Market experience *1 |
Substituting for DEHP |
|
Polymer applications: |
|
Calendering of film, sheet and coated products |
3 |
Calendering of flooring, roofing, wall covering |
3 |
Extrusion of hose and profile |
3 |
Extrusion of wire and cable |
3 |
Extrusion of miscellaneous products from compounds |
3 |
Injection moulding of footwear and miscellaneous |
3 |
Spread coating of flooring |
2 |
Spread coating of coated fabric, wall covering, coil coating, etc. |
3 |
Car undercoating |
|
Non polymer applications: |
|
Adhesives/sealant, rubber |
4 |
Lacquers and paint |
4 |
Printing ink |
3 |
Production of ceramics |
|
Substituting for DBP |
|
Plasticiser in PVC |
2 |
Plasticiser in other polymers |
2 |
Adhesives |
4 |
Printing inks |
3 |
Miscellaneous: |
|
Sealants |
4 |
PU foam sealants |
|
Nitrocellulose paints |
|
Film coatings |
|
Glass fibre production |
4 |
Cosmetics |
2 |
Substituting for BBP |
|
Polymer applications: |
|
General PVC (e.g. for moulded plastic parts) |
4 |
Plastisol coating, for flooring |
3 |
Extrusion or spreadcoating: Leather and cloth coating (e.g. for furniture, shoes, bags, suitcases) |
2 |
Films, calendering (e.g. for packaging, calendered flooring, wall covering, etc.) |
3 |
Non polymer applications: |
|
Sealants (polysulfide based, polyurethane foam sealants, acrylic based; e.g. for windows, construction etc.) |
|
Coatings and inks (e.g. for car care products, construction, paper, board) |
|
Adhesives (polymer based, e.g. for construction, paper) |
|
*1: Market experience categories interpretation: 1) Main alternative on market. 2) Significant market experience. 3) Examples of full scale experience. 4) Pilot/lab scale experience.
Key characteristics
Table 5.9 below shows selected comparisons from Danisco (2009b) between COMGHA, DEHP and DINP for selected parameters (more parameters are shown in Danisco, 2009b). Note that COMGHA has very similar characteristics as DEHP and DINP.
Table 5.9 shows comparisons of COMGHA, DEHP and DINP for selected parameters.
Table 5.9 comparison of COMGHA, DEHP and DINP for selected parameters (Danisco, 2009)
Plasticiser (at 40 phr) |
Shore A, after 15 sec |
Tensile strength, MPa |
100% modulus, MPa |
Max. elongation,% |
COMGHA |
88.0 |
25.0 |
9.1 |
367 |
DEHP |
90.0 |
22.2 |
8.5 |
320 |
DINP |
91.5 |
24.1 |
9.3 |
344 |
Table 5.10 describes some key characteristics of COMGHA as alternative to DEHP, DBP and BBP.
Table 5.10 key characteristics of COMGHA as alternative to DEHP, DBP and BBP
Parameter |
Value |
Remarks |
Efficiency( as plasticiser in PVC compared to DEHP)*1 |
≈1 |
(Danisco, 2009b) |
Price |
3.5 €/kg |
Danisco (2009) |
Price relative to DEHP (≈0.8-1€/kg in 2008/2009; 1€ used for calculations) |
≈350% |
|
Effective price relative to DEHP |
≈350% |
|
Compatibility/solubility in PVC |
|
Compatible |
Permanency (migration, evaporation, extraction) |
|
Much lower extractability than DEHP in acidic water solutions and ethanol/water solutions. Lower extractability in sunflower oil (Danisco, 2009b) |
Processability (fusing speed and temperature, viscosity, etc.) |
|
Higher viscosity than DEHP (Danisco, 2009b) |
Limitations in use, if any, noted by supplier in data for this study |
|
None noted |
Notes: *1: Efficiency indicator, also called substitution factor, indicating the concentration of plasticiser in PVC needed, compared to DEHP, to achieve a specified flexibility according to a well defined method. DEHP has substitution factor 1 per definition, while plasticisers needing lower concentration (more effective) have lower values, and plasticisers needing higher concentrations have higher effectiveness value. NA = not available
Both substances in COMGHA are derived from castor oil produced from castor beans. According to Danisco, the beans must be handpicked which sets limits to production volume and cost reductions (Danisco, 2009). Research is therefore ongoing to produce the substances from other, more abundant, biological substrates (Buck Jensen, 2009).
Conclusions
According to the producer, Danisco, COMGHA still has relative moderate market experience, albeit with many examples of full scale usage and pilot/lab scale tests, and significant market experience in some plastisol application and cosmetics. The producers found technically good performance on key parameters indicating a potential for substituting for DEHP and perhaps for some traditional DBP/BBP uses.
The significantly higher price than DEHP is a major impediment to a wider application of COMGHA. New research initiated needs yet to prove potential for increased production at lower prices.
5.4 DEGD (diethylene glycol dibenzoate)
DEGD is the esterification product of two benzoate groups with diethylene glycol, see structural formula below. Its CAS No. is 120-55-8. It is marketed by Genovique in a mixture with two other dibenzoates under the product name Benzoflex 2088. The two other dibenzoates are dipropylene glycol dibenzoate (DGD; CAS 27138-31-4) and triethylene glycol dibenzoate (CAS 120-56-9). In this section, the mixed product is described. Note that DGD is described separately in the toxicological assessment. DGD is quite similar to DEGD in structure except for two extra methyl groups.
DEGD; diethylene glycol dibenzoate)
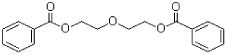
(diagram from www.chemblink.com)
Producer's description (extracts)
Benzoflex® 2088 is a high solvating plasticizer primarily known for its exceptional performance in polyvinyl acetate and water-based adhesive systems. It displays good wet tack, set times and open times. It also improves adhesion in acrylic latex caulks (Genovique, 2009b).
In Europe, Benzoflex® 2088 is Genovique’s most cost effective replacement for fast fusing phthalate plasticizers used in vinyl applications. It can substitute for phthalates such as BBP, DBP, DIHP and DIBP. It has had its greatest success replacing phthalates in plastisol application, the largest of which is resilient flooring. Over the past five years Benzoflex® 2088 has been established as largest volume non-phthalate, fast fusing plasticizer used in resilient flooring in Europe. Most plastisols were formulated with phthalates in mind, so utilizing an alternative chemistry, like benzoates, requires formulation adjustments (Genovique, 2009).
Application and market experience
Genovique has provided information on application areas for Benzoflex 2088 among the traditional DEHP, DBP and BBP applications shown in Table 5.11. The table also indicates the level of market experience in each application area according to Genovique (2009; interpreted from qualitative text by the report authors). Note the significant market experience in several of the traditional DBP and BBP specialty plasticiser applications and certain DEHP applications, notably in the non-polymer (adhesives, sealants, etc.) and PVC spread coating (plastisol) application fields.
In a study of plasticiser alternatives for non-PVC applications (COWI, 2000), DEGD was proposed by market actors as a substitute for phthalates in adhesives and sealants.
Table 5.11 Applications of Benzoflex 2088 and level of market experience in each application. data from Genovique provided for this study
Application |
Market experience *1 |
Substituting for DEHP |
|
Polymer applications: |
|
Calendering of film, sheet and coated products |
4 |
Calendering of flooring, roofing, wall covering |
3 |
Extrusion of hose and profile |
3 |
Extrusion of wire and cable |
3 |
Extrusion of miscellaneous products from compounds |
2 |
Injection moulding of footwear and miscellaneous |
2 |
Spread coating of flooring |
2 |
Spread coating of coated fabric, wall covering, coil coating, etc. |
2 |
Car undercoating |
3 |
Non polymer applications: |
|
Adhesives/sealant, rubber |
1 |
Lacquers and paint |
2 |
Printing ink |
2 |
Production of ceramics |
|
Substituting for DBP |
|
Plasticiser in PVC |
1 |
Plasticiser in other polymers |
|
Adhesives |
1 |
Printing inks |
|
Miscellaneous: |
|
Sealants |
|
PU foam sealants |
|
Nitrocellulose paints |
2 |
Film coatings |
|
Glass fibre production |
|
Cosmetics |
|
Substituting for BBP |
|
Polymer applications: |
|
General PVC (e.g. for moulded plastic parts) |
|
Plastisol coating, for flooring |
1 |
Extrusion or spreadcoating: Leather and cloth coating (e.g. for furniture, shoes, bags, suitcases) |
2 |
Films, calendering (e.g. for packaging, calendered flooring, wall covering, etc.) |
4 |
Non polymer applications: |
|
Sealants (polysulfide based, polyurethane foam sealants, acrylic based; e.g. for windows, construction etc.) |
1 |
Coatings and inks (e.g. for car care products, construction, paper, board) |
|
Adhesives (polymer based, e.g. for construction, paper) |
1 |
*1: Market experience categories interpretation: 1) Main alternative on market. 2) Significant market experience. 3) Examples of full scale experience. 4) Pilot/lab scale experience.
Key characteristics
DGD is a commonly used benzoate. According to Krauskopf and Godwin (2005), benzoates are generally strong solvates due to the high aromaticity, as are lower molecular weight phthalates such as BBP. Commercial practice includes the use of up to 10–20% of the plasticiser system as “strong solvating” type plasticisers, such as aryl-alkyl phthalates (e.g. BBP), benzoates, etc.
Table 5.12 below describes some key characteristics of Benzoflex 2088 as alternative to DEHP, DBP and BBP.
Table 5.12 key characteristics of Benzoflex 2088 as alternative to DEHP, DBP and BBP
Parameter |
Value |
Remarks |
Efficiency( as plasticiser in PVC compared to DEHP)*1 |
|
|
Price (primo 2009) |
|
|
Price relative to DEHP |
|
"Slightly higher" than DEHP and DBP; equivalent to BBP (Genovique, 2009) |
Effective price relative to DEHP |
|
|
Compatibility/solubility in PVC |
|
Compatible |
Permanency (migration, evaporation, extraction) |
|
App. double volatility as DEHP in plastisols. Three times higher water extraction than DEHP. Much lower organic solvents extraction than DEHP (Genovique, 2009). |
Processability (fusing speed and temperature, viscosity, etc.) |
|
Lower gelling/fusing temperature in PVC than with BBP and DEHP. Slightly higher viscosity in plastisols (Genovique, 2009) |
Limitations in use, if any, noted by supplier in data for this study |
|
|
Notes: *1: Efficiency indicator, also called substitution factor, indicating the concentration of plasticiser in PVC needed, compared to DEHP, to achieve a specified flexibility according to a well defined method. DEHP has substitution factor 1 per definition, while plasticisers needing lower concentration (more effective) have lower values, and plasticisers needing higher concentrations have higher effectiveness value. NA = not available
Table 5.13 below shows some performance data for DEGD (as single substance) compared to DEHP, DBP and BBP. As shown, DEGD has similar characteristics to BBP on these parameters, except for a factor 10 higher extractability in water.
Table 5.13 Technical key parameters of DEGD in PVC compared to DEHP (from Sears and Darby, 1982)
Plasticiser in PVC, conc. 40% =67 phr in same PVC resin |
Shore A hardness |
Volatility,% lost, 1 day at 87 °C over activated carbon |
Extracted in water,% |
Extracted in kerosene (jet fuel, etc.),% |
DEHP |
69 |
4.5 |
0.01 |
44 |
DBP |
62 |
45.4 |
0.25 |
9.1 |
BBP |
68 |
7.7 |
0.07 |
3.4 |
DEGD (as single substance) |
69 |
5.5 |
0.75 |
3.4 |
Conclusions
The producer, Genovique, has indicated significant market experience in several of the traditional DBP and BBP specialty plasticiser applications and certain DEHP applications, notably in the non-polymer (adhesives, sealants, etc.) and PVC spread coating (plastisol) application fields. According to the producer, Benzoflex 2088 has become the main non-phthalate alternative to DBP/BBP in vinyl flooring production in Europe. The higher extractability in water may limit its use for some applications. Prices are indicated as "slightly higher" than DEHP and DBP; equivalent to BBP by Genovique.
5.5 DGD (dipropylene glycol dibenzoate)
DGD is the esterification product of two benzoate groups with dipropylene glycol, see structural formula below. Its CAS No. is 27138-31-4. It is marketed by Genovique under the product name Benzoflex 9-88. DGD is quite similar to DEGD except for two extra methyl groups.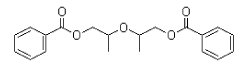
DGD; dipropylene glycol dibenzoate
Producer's description (extracts)
DGD is a high solvating plasticizer that has been used for many years in a wide variety of applications. Its diverse uses include resilient flooring, adhesives, artificial leather cloth and caulk (Genovique, 2009b).
DGD can be used as a replacement for BBP and DBP in vinyl applications. Its gel fusion temperature is identical to BBP and DBP in vinyl plastisol applications allowing it to be as close to a drop-in replacement for BBP and DBP as possible (Genovique, 2009).
Application and market experience
Genovique has provided information on application areas for DGD among the traditional DEHP, DBP and BBP applications shown in Table 5.14. The table also indicates the level of market experience in each application area according to Genovique (2009; interpreted from qualitative text by the report authors). Note the significant market experience in sealants, adhesives, coatings and inks as well as in PVC spread coating (plastisols), extrusion and injection moulding. DGD seems to be capable of substituting for both DEHP, DBP and BBP, indicating coverage of some general plasticiser features as well as some of the special performance characteristics of DBP and BBP.
In a study of plasticiser alternatives for non-PVC applications (COWI, 2000), DGD was proposed by market actors as a substitute for phthalates in adhesives and sealants.
Table 5.14 Applications of DGD and level of market experience in each application, data from Genovique provided for this study
Application |
Market experience *1 |
Substituting for DEHP |
|
Polymer applications: |
|
Calendering of film, sheet and coated products |
4 |
Calendering of flooring, roofing, wall covering |
3 |
Extrusion of hose and profile |
3 |
Extrusion of wire and cable |
3 |
Extrusion of miscellaneous products from compounds |
2 |
Injection moulding of footwear and miscellaneous |
2 |
Spread coating of flooring |
2 |
Spread coating of coated fabric, wall covering, coil coating, etc. |
2 |
Car undercoating |
3 |
Non polymer applications: |
|
Adhesives/sealant, rubber |
1 |
Lacquers and paint |
2 |
Printing ink |
2 |
Production of ceramics |
|
Substituting for DBP |
|
Plasticiser in PVC |
1 |
Plasticiser in other polymers |
|
Adhesives |
|
Printing inks |
|
Miscellaneous: |
|
Sealants |
|
PU foam sealants |
|
Nitrocellulose paints |
2 |
Film coatings |
|
Glass fibre production |
|
Cosmetics |
|
Substituting for BBP |
|
Polymer applications: |
|
General PVC (e.g. for moulded plastic parts) |
|
Plastisol coating, for flooring |
1 |
Extrusion or spreadcoating: Leather and cloth coating (e.g. for furniture, shoes, bags, suitcases) |
|
Films, calendering (e.g. for packaging, calendered flooring, wall covering, etc.) |
4 |
Non polymer applications: |
|
Sealants (polysulfide based, polyurethane foam sealants, acrylic based; e.g. for windows, construction etc.) |
1 |
Coatings and inks (e.g. for car care products, construction, paper, board) |
1 |
Adhesives (polymer based, e.g. for construction, paper) |
|
*1: Market experience categories interpretation: 1) Main alternative on market. 2) Significant market experience. 3) Examples of full scale experience. 4) Pilot/lab scale experience.
Key characteristics
DGD is a commonly used benzoate. According to Krauskopf and Godwin (2005), it's preferred use is in PVC flooring products, owing to its strong solvating strength, and it reportedly controls plasticiser bleeding into asphalt adhesives. In vinyl sheet flooring, the benzoate enhances processing, while the low molecular weight contributes a hardened, stain resistant surface, due to volatilization, similar to the effect of BBP in flooring. Benzoates are generally strong solvents due to the high aromaticity, as are lower molecular weight phthalates such as BBP. Commercial practice includes the use of up to 10–20% of the plasticiser system as “strong solvating” type plasticisers, such as aryl-alkyl phthalates (e.g. BBP), benzoates, etc.
Table 5.15 describes some key characteristics of DGD as alternative to DEHP, DBP and BBP.
Table 5.15 key characteristics of DGD as alternative to DEHP, DBP and BBP
Parameter |
Value |
Remarks |
Efficiency( as plasticiser in PVC compared to DEHP)*1 |
0.98 |
TURI (2006, citing industry) |
Price |
0.73 USD/Lb |
TURI (2006, citing industry) |
Price relative to DEHP
(2006: 0.70 USD/Lb) |
2009: "Slightly higher"
2006: 104% |
2009: "Slightly higher" according to Genovique (2009); also compared to DBP prices. Equivalent to BBP prices.
2006: Calculated from (TURI, 2006, citing industry); Same price relative to BBP. |
Effective price relative to DEHP |
102% |
|
Compatibility/solubility in PVC |
|
Compatible |
Permanency (migration, evaporation, extraction) |
|
Lover volatility than its competitor BBP (Wilson, 1995). |
Processability (fusing speed and temperature, viscosity, etc.) |
|
High solvating, fast fusing; competing with BBP (Wilson, 1995, and others).
TURI (2006): Compounding easier than with DEHP; calendering: no issues identified.
Some general plasticiser like applications will require blends with slower fusing plasticizers (Genovique, 2009). |
Limitations in use, if any, noted by supplier in data for this study |
|
None noted |
Notes: *1: Efficiency indicator, also called substitution factor, indicating the concentration of plasticiser in PVC needed, compared to DEHP, to achieve a specified flexibility according to a well defined method. DEHP has substitution factor 1 per definition, while plasticisers needing lower concentration (more effective) have lower values, and plasticisers needing higher concentrations have higher effectiveness value. NA = not available
Table 5.16 below shows some performance data for DGD compared to DEHP, DBP and BBP. As shown, DGD has very similar characteristics to BBP on these parameters, except for a higher extractability in water.
Table 5.16 Technical key parameters of DGD compared to DEHP, DBP and BBP (from Sears and Darby, 1982)
Plasticiser in PVC, conc. 40% =67 phr in same PVC resin |
Shore A hardness |
Volatility,% lost, 1 day at 87 °C over activated carbon |
Extracted in water,% |
Extracted in kerosene (jet fuel, etc.),% |
DEHP |
69 |
4.5 |
0.01 |
44 |
DBP |
62 |
45.4 |
0.25 |
9.1 |
BBP |
68 |
7.7 |
0.07 |
3.4 |
DGD |
71 |
7.9 |
0.45 |
2.9 |
Wilson (1995) states that the consumption of benzoates had so far been minor in Europe although they were well known in the USA, where they were established plasticisers in the PVC flooring industry. Here they were used as fast fusing stain resistant plasticisers. Wilson states the most commercially important benzoate as DGD, which is broadly competitive with BBP, had the advantage of somewhat lower volatility.
Wilson (1995) also emphasises that DGD had replaced much of the previous C4 phthalate use (i.e. DBP, BBP) in PVA adhesives in the USA. In the mid 1990s this substitution had not yet happened in Europe, partly due to higher benzoate prices in Europe, partly due to less regulatory (health and environment) pressure at that time.
Karbæk (2003), who tested DGD and other plasticisers in PVC for medical purposes, found its poor resistance to extraction by water a major drawback for its use in medical applications. Otherwise DGD performed technically well compared to DEHP on all tested parameters, except for tensile strain at break and flexibility at low temperatures.
BBP is mentioned as a critical component in seals for insulating double glaz-ing (BBP Information Centre, 2009), but it has not been specifically investigated whether DGD or other benzoates can substitute for BBP for this particular application.
Conclusions
Genovique, the producer of DGD, has indicated significant market experience in sealants, adhesives, coatings and inks as well as in PVC spread coating (plastisols), extrusion and injection moulding. The qualities of DGD seem especially suitable for substitution of BBP, while it may also substitute for some traditional uses of DEHP and DBP. The fact that DGD has for many years been a well known and much used competitor to BBP in USA, especially in the flooring industry and in PVA adhesives, indicates a clear potential for substituting DGD for BBP, from a technical point of view. DGD and benzoates may already have played a part in the observed reductions (COWI, 2009c) of BBP usage in Europe.
The price of DGD seems also to be largely competitive with low molecular weight phthalates such as BBP. Currently the effective price is only slightly higher than the price of BBP. As with many other substitution processes, a price decrease may occur if the market increases in open competition between producers.
5.6 DEHT (di-ethyl-hexyl-terephthalate)
DEHT is a phthalate ester stoekiometrically equal to DEHP, i.e. phthalate ester bound to two ethylhexyl groups, but with a different spatial structure, because one of the carboxylic groups is placed differently on the benzyl ring; see diagram of the structure below ("tere" means tertiary, or third, because the carboxylic group is placed on the third carbon atom counted from the first carboxyl group). DEHT is marketed by Eastman Chemical Company under the product name Eastman 168. It is also marketed by LG Chem under the name LGflex GL300. There are several other producers world wide.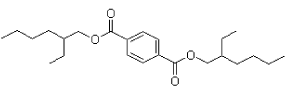
Terephthalate, (DEHT; di 2-ethylhexyl terephthalate); CAS no. 6422-86-2
Producer's description (extracts)
Eastman Chemicals has given the following short presentation of DEHT (Eastman, 2009b): DEHT is a good general purpose plasticizer for PVC, with performance equal or better than most orthophthalate plasticizers (Eds.: "ortho" is the form for most common phthalate plasticisers, such as in DEHP). It offers good performance properties, good low temperature flexibility, resistance to extraction by soapy water and good non-migration properties. In plastisols, DEHT results in low initial viscosity and good keeping viscosity.
Applications/Uses according to Eastman (2009b):
- Bottle caps and closures
- Coatings
- Coatings for cloth
- Electric connectors
- Flexible film
- Pavement striping compounds
- Sheet vinyl flooring
- Toys
- Traffic cones
- Vinyl compounding
- Vinyl gloves
- Vinyl products
- Vinyl water stops
- Walk-off mats
Application and market experience
Eastman Chemicals has provided information on application areas for DEHT among the traditional DEHP, DBP and BBP applications shown in Table 5.17. The table also indicates the level of market experience in each application area according to Eastman (2009; interpreted from qualitative text by the report authors). Note that Eastman has indicated significant market experience for all traditional DEHP uses, except car undercoating and production of ceramics. No traditional DBP and BBP applications have been indicated by Eastman, signalling that they consider DEHT as general plasticiser (such as DEHP, DINP and DIDP).
Table 5.17 Applications of DEHT and level of market experience in each application, data from Eastman Chemicals provided for this study
Application |
Market experience *1 |
Substituting for DEHP |
|
Polymer applications: |
|
Calendering of film, sheet and coated products |
2 |
Calendering of flooring, roofing, wall covering |
2 |
Extrusion of hose and profile |
2 |
Extrusion of wire and cable |
2 |
Extrusion of miscellaneous products from compounds |
2 |
Injection moulding of footwear and miscellaneous |
2 |
Spread coating of flooring |
2 |
Spread coating of coated fabric, wall covering, coil coating, etc. |
2 |
Car undercoating |
|
Non polymer applications: |
|
Adhesives/sealant, rubber |
2 |
Lacquers and paint |
2 |
Printing ink |
2 |
Production of ceramics |
|
PVC medical articles |
2 |
Toy and childcare articles |
2 |
*1: Market experience categories interpretation: 1) Main alternative on market. 2) Significant market experience. 3) Examples of full scale experience. 4) Pilot/lab scale experience.
Key characteristics
Table 5.18 below shows selected comparisons from Eastman (2009c) between DEHT ("168"), DEHP ("DOP"), TXIB and other plasticisers of interest for selected parameters (more parameters are shown in Eastman 2009c). Note that DEHT has similar extraction values to DEHP in oil and hexane, and a factor two lower in soapy water. Volatility at elevated temperatures (expressed as activated carbon extraction) is 50%-67% of the volatility of DEHP. The low temperature flexibility of DEHT in PVC is equal to that of DEHP, whereas 100% modulus is app. 20% higher than for DEHP indicating slightly lower efficiency of DEHT (substitution factor 1.03) than DEHP. DEHT has about half the viscosity of DEHP in plastisols.
Table 5.18 Comparison between DEHT ("168"), DEHP ("DOP"), TXIB and other plasticisers (from Eastman, 2009c)
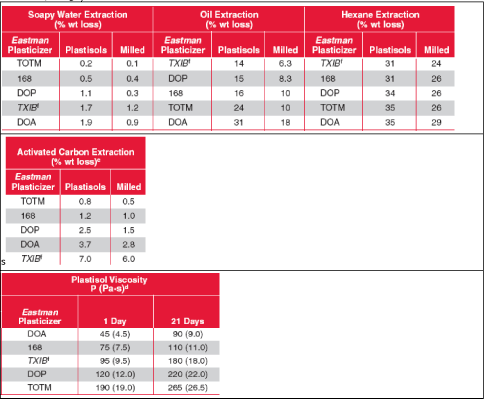
Notes: Plastisols contain 60 phr plasticiser; milled and calendered PVC contains 50 phr plasticiser; phr meaning parts per 100 parts hard PVC by weight. a) Stress at which PVC is elongated 100%. Lower value indicates higher efficiency of plasticiser (ASTM D638). b) Temperature at which the shown stiffness (torsion) is reached (ASTM D1043). c) Indication of volatility at elevated temperatures (ASTM D1203). d) Brookfield viscosity, determined with a number 4 spindle at 6rpm and 23 C.
Table 5.19 shows another performance data set for DEHT compared to DEHP. As shown, DEHT results in quite similar hardness as DEHP on these parameters. The volatility of DEHT is somewhat lower, and the extractability in water and kerosene is somewhat higher.
Table 5.19 Technical key parameters of DEHT compared to DEHP (from Sears and Darby, 1982)
Plasticiser in PVC, conc. 40% =67 phr in same PVC resin*1 |
Shore A hardness*2 |
Volatility,% lost, 1 day at 87 °C over activated carbon |
Extracted in water,% |
Extracted in kerosene (jet fuel, etc.),% |
DEHP (PVC2) |
73 |
3.6 |
0.02 |
54.7 |
DEHT (PVC2) |
76 |
1.9 |
0.09 |
70.8 |
Table 5.20 below describes some generalised key characteristics of DEHT as alternative to DEHP.
Table 5.20 key characteristics of DEHT as alternative to DEHP
Parameter |
Value |
Remarks |
Efficiency( as plasticiser in PVC compared to DEHP)*1 |
1.03 |
TURI (2006) |
Price |
0.74 USD/Lb |
TURI (2006) |
Price relative to DEHP (2006: 0.70 USD/Lb) |
106% |
TURI (2006)
Also according to Krauskopf and Godwin (2005), DEHT is commercially available at similar price as DEHP. |
Effective price relative to DEHP |
109% |
TURI (2006) |
Compatibility/solubility in PVC |
|
Compatible |
Permanency (migration, evaporation, extraction) |
|
Similar to DEHP, slightly higher permanence on some parameters, slightly lower on others, see above (Eastman, 2009c). |
Processability (fusing speed and temperature, viscosity, etc.) |
See some values in Table 5.18 above |
Overall very similar to DEHP and DINP (Eastman, 2009; TURI, 2006). Half the viscosity in plastisols as DEHP (advantage of DEHT); slightly higher gelling temperatures than DEHP (Eastman, 2009c). |
Limitations in use, if any, noted by supplier in data for this study |
|
Poor weatherability properties for external applications such as roofing and coil coating (Eastman, 2009) |
Notes: *1: Efficiency indicator, also called substitution factor, indicating the concentration of plasticiser in PVC needed, compared to DEHP, to achieve a specified flexibility according to a well defined method. DEHP has substitution factor 1 per definition, while plasticisers needing lower concentration (more effective) have lower values, and plasticisers needing higher concentrations have higher effectiveness value. NA = not available.
In practice, terephthalates are more commonly used in the USA than elsewhere (TURI, 2006).
Conclusions
All available information indicates that, technically, DEHT may be a good substitute for most or all traditional DEHP uses. In practice, terephthalates are more commonly used in the USA than elsewhere. DEHT was found in 7% and 10%, respectively, of products analysed in two European surveys of large samples of toys and childcare articles. It was also reported as used for toys by Danish toy manufacturers (with contract production in China).
According to 2006 information, DEHT is slightly more expensive than DEHP. As with many other substitution processes, a price decrease may occur if the market increases in open competition between producers.
5.7 DINA (diisononyl adipate)
DINA is formed by an adipate (hexanoic acid) ester bound with two C-9 alkanes, see diagram. It is marketed by ExxonMobil under the product name Jayflex-DINA, by BASF under the product name Plastomoll DNA, and formerly by Lanxess under the product name Adimoll® DN.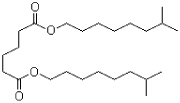
DINA = di isononyl adipate; CAS 33703-08-1
www.chemblink.com
Producers' descriptions (extracts)
BASF has given the following short presentation of DINA (BASF, 2009): DINA is a nearly colourless, clear and practically anhydrous liquid with a hardly noticeable odour. It is soluble in the usual organic solvents and is miscible and compatible with all of the monomeric plasticizers commonly used in PVC. In water DINA is soluble only in very small amounts. Owing to its chemical structure, DINA permits – preferably, in combination with phthalates and polymeric plasticizers – the production of plasticized PVC products with exceptionally good low temperature properties. PVC plasticized with DINA has far less volatility than, for example, PVC plasticized with DOA.
ExxonMobil has given the following short presentation of DINA (ExxonMobil, 2009b):
Improved permanent adipate widely used in a variety of end-uses.
- Low temperature flexibility, low freezing point
- Lower volatility/higher permanence than DOA
- Enhanced viscosity stability and air release properties in plastisols
- Partial replacement for phthalates to improve low temperature flexibility
Applications:
- Films
- Shrink wrap
- Electrical wire jacket
Application and market experience
Neither BASF nor ExxonMobil has wished to provide detailed feedback for this project on DINA's suitability for substituting for DEHP, DBP and BBP.
In a study of plasticiser alternatives for non-PVC applications (COWI, 2000), DINA was proposed by market actors as a substitute for phthalates in adhesives, printing inks, paint and lacquer, and rubber.
Key characteristics
The family of adipic acid esters used in PVC applications improves low temperature performance relative to phthalates and give significantly lower plastisol viscosities in plastisol applications, due to the lower inherent viscosities of the plasticisers themselves (ECPI, 2009).
Table 5.21 shows some performance data for DINA compared to DEHP, DBP and BBP. As shown, DINA has similar hardness and volatility as DEHP, but higher extractability in water and kerosene.
Table 5.21 Technical key parameters of DINA compared to DEHP, DBP and BBP (from Sears and Darby, 1982)
Plasticiser in PVC, conc. 40% =67 phr in same PVC resin |
Shore A hardness |
Volatility,% lost, 1 day at 87 °C over activated carbon |
Extracted in water,% |
Extracted in kerosene (jet fuel, etc.),% |
DEHP |
69 |
4.5 |
0.01 |
44 |
DBP |
62 |
45.4 |
0.25 |
9.1 |
BBP |
68 |
7.7 |
0.07 |
3.4 |
DINA |
72 |
4.1 |
0.14 |
80.4 |
Table 5.22 describes some generic characteristics of DINA as alternative to DEHP, DBP and BBP.
Table 5.22 key characteristics of DINA as alternative to DEHP, DBP and BBP
Parameter |
Value |
Remarks |
Efficiency( as plasticiser in PVC compared to DEHP)*1 |
0.98 |
|
Price (primo 2009) |
NA |
|
Price relative to DEHP |
150-200%
≈130% |
ExxonMobil (2009)
Arbeitsgemeinschaft PVC und Umwelt e.V. (2006; statement for adipates in general) |
Effective price relative to DEHP |
NA |
|
Compatibility/solubility in PVC |
|
Compatible |
Permanency (migration, evaporation, extraction) |
|
Far less volatility in PVC than DOA (BASF, 2009); DOA is slightly more volatile than DEHP (Eastman, 2009c) |
Processability (fusing speed and temperature, viscosity, etc.) |
|
Enhanced viscosity stability and air release properties in plastisols |
Limitations in use, if any, noted by supplier in data for this study |
|
NA |
Notes: *1: Efficiency indicator, also called substitution factor, indicating the concentration of plasticiser in PVC needed, compared to DEHP, to achieve a specified flexibility according to a well defined method. DEHP has substitution factor 1 per definition, while plasticisers needing lower concentration (more effective) have lower values, and plasticisers needing higher concentrations have higher effectiveness value. NA = not available
Conclusions
It has not been possible to get detailed application data compared to DEHP, DBP and BBP for DINA from producers. Among the adipates, DEHA (or DOA) is the most used. It was however not included for further investigation in this study because it was reported by SCENIHR (2008) to have reproductive toxicity. Instead DINA was chosen for further study. In PVC DINA has similar hardness and volatility as DEHP, but higher extractability in water and kerosene. DINA has mostly been used for low temperature PVC applications and in PVC film/wrapping. According to the producers, PVC plasticized with DINA has far less volatility than, for example, PVC plasticized with DEHA. DINA seems therefore potentially more suitable than DEHA, from a technical point of view, as an alternative to DEHP than DEHA. DINA seems currently only to have a small European market and data for DINA are scarcer than for DEHA. In fact two producers have ceased marketing of DINA on the European market. However, DINA was found in 6% and 4%, respectively, of products analysed in two European studies of large samples of toys and childcare articles. It was also reported as used for toys by Danish toy manufacturers (with contract production in China). The data available for this study does not allow clear-cut conclusions as regards DINA's suitability as alternative to DEHP, but DINA could perhaps be worth investigating in future technical explorations for alternatives.
The price for DINA is currently somewhat higher than for DEHP, but as mentioned the market is small and DINA is used as a specialty plasticiser.
5.8 DINCH (di-isononyl-cyclohexane-1,2dicarboxylate)
DINCH is the hydrogenated parallel to DINP, with the difference that the ring structure is cyclohexane (a cyclic alkyl hydrocarbon) instead of a benzene ring (an aromate). Its CAS no. is 166412-78-8. It is marketed by BASF as Hexamoll DINCH. There may be other producers outside the EU.
Producer's description (extracts)
BASF describes DINCH as follows (BASF, 2009): The combination of an good toxicological profile and a very low migration rate makes DINCH the plasticizer of choice for medical devices made with soft PVC products such as tubes for internal feeding and haemodialysis bags, respiratory tubes, catheters, gloves and breathing masks.
DINCH is the ideal additive for toys. Thanks to its low migration rate, lack of odour and technical suitability, DINCH is the plasticizer of choice for toys and children’s articles such as dolls, inflatables and balls, figurines, modelling clay, swimming aids, baby and childcare articles, wire and cable for toys.
Thanks to its toxicological profile, its low migration rate, and especially the low solubility in water and ethanol, this additive is developed for food contact applications such as cling film, hoses, sealants and cap closures, crown corks, artificial wine corks, gaskets and gloves.
DINCH is also suitable for other applications where safety is needed, also outside PVC: Thermoplastics and polar rubbers, coatings and printing inks, dispersions, adhesives, cosmetics (e.g. nail polish), masterbatches, artificial leather, textile coatings (e.g. rain coats), erasers, film and sheets (e.g. lifestyle bags).
Application and market experience
BASF has not wished to provide detailed feedback for this project on DINCH's suitability for substituting for DEHP, DBP and BBP.
In 2007, BASF raised its DINCH production capacity from 25,000 to 100,000 tonnes/yr (MPW, 2008), indicating an increasing demand.
Key characteristics
Table 5.23 below describes some key characteristics of DINCH as alternative to DEHP, DBP and BBP.
Table 5.23 key characteristics of DINCH as alternative to DEHP, DBP and BBP
Parameter |
Value |
Remarks |
Efficiency (as plasticiser in PVC compared to DEHP)*1 |
NA |
|
Price |
$0.91 /lb |
TURI (2006) |
Price relative to DEHP (2006: 0.70 USD/Lb) |
130% |
TURI (2006) |
Effective price relative to DEHP |
NA |
|
Compatibility/solubility in PVC |
|
Compatible |
Permanency (migration, evaporation, extraction) |
|
Migration levels eight times lower than that of DEHP (MPW, 2008). |
Processability (fusing speed and temperature, viscosity, etc.) |
|
NA |
Limitations in use, if any, noted by supplier in data for this study |
|
NA |
Notes: *1: Efficiency indicator, also called substitution factor, indicating the concentration of plasticiser in PVC needed, compared to DEHP, to achieve a specified flexibility according to a well defined method. DEHP has substitution factor 1 per definition, while plasticisers needing lower concentration (more effective) have lower values, and plasticisers needing higher concentrations have higher effectiveness value. NA = not available
Conclusions
The producer’s sales appraisal indicates a relatively wide usage of DINCH for general plasticiser purposes, where safety is prioritised. The production capacity has been raised substantially, indicating a growing demand and market experience. More detailed information of applications substituting for DEHP; DBP and BBP has not been available from the producer. DINCH was the most frequently found plasticiser in two European studies of large samples of toys and childcare articles. It was found in 25% and 48%, respectively, of the analysed products. It was also reported as used for toys by Danish toy manufacturers (with contract production in China). The data available does not allow a closer assessment of DINCH's technical suitability as alternative to DEHP, DBP and BBP.
Sales prices in 2006 were somewhat higher than DEHP. As with many other substitution processes, a price decrease may occur if the market increases in open competition between producers.
5.9 GTA (glycerol triacetate)
GTA is an ester of glycerol and three acetate groups, see diagram below. Its CAS no. is 102-76-1. It is marketed by Lanxess and Eastman under the name Triacetin.
Glyceryl triacetate (GTA, Triacetin)
Producer's description (extracts)
Lanxess (2009) presents GTA as follows: Triacetin is used for the solidification of acetyl cellulose fibres in the manufacture of cigarette filters. The water content must be kept constant to achieve constant solidification. Triacetin is also used as a support for flavourings and essences in the food industry and as a plasticiser for chewing gum. In technical applications, Triacetin is used for example as a core sand binder in the metal foundry sector. Another application is inks and printing inks. Triacetin is used as a highly effective plasticiser for cellulose-based plastics.
The major features of Triacetin are:
- good suitability for the solidification of acetyl cellulose fibres for the manufacture of cigarette filters
- very good dissolving power for a number of organic substances
- good plasticising effect for various plastics such as cellulose acetates or celluloseacetobutyrates
- good plasticising effect for cellulose-based paints
- good compatibility with natural and synthetic rubber
- good light resistance
Eastman presents GTA as follows (Eastman, 2009d): GTA is used as a plasticizer for cellulosic resins and is compatible in all proportions with cellulose acetate, nitrocellulose, and ethyl cellulose. GTA is useful for imparting plasticity and flow to laminating resins, particularly at low temperatures, and is also used as a plasticizer for vinylidene polymers and copolymers. It serves as an ingredient in inks for printing on plastics, and as a plasticizer in nail polish. GTA is approved by the FDA for food packaging and many other food-contact applications.
Application and market experience
Lanxess has provided information on application areas for GTA among the traditional DEHP, DBP and BBP applications shown in Table 5.24. The table also indicates the level of market experience in each application area according to Lanxess (2009; interpreted from qualitative text by the report authors). Note that Lanxess has indicated significant market experience for adhesives, coatings and inks and examples of full scale experience in a number of other non-polymer traditional DBP and BBP uses. Lanxess has not indicated use of GTA in any traditional DEHP uses.
Table 5.24 Applications of GTA and level of market experience in each application, data from Lanxess provided for this study
Application |
Market experience *1 |
Substituting for DEHP |
|
Plasticiser in PVC |
|
Plasticiser in other polymers |
|
Adhesives |
2 |
Printing inks |
3 |
Miscellaneous: |
|
Sealants |
|
PU foam sealants |
|
Nitrocellulose paints |
3 |
Film coatings |
|
Glass fibre production |
|
Cosmetics |
|
Substituting for BBP |
|
Polymer applications: |
|
General PVC (e.g. for moulded plastic parts) |
|
Plastisol coating, for flooring |
|
Extrusion or spreadcoating: Leather and cloth coating (e.g. for furniture, shoes, bags, suitcases) |
|
Films, calendering (e.g. for packaging, calendered flooring, wall covering, etc.) |
|
Non polymer applications: |
|
Sealants (polysulfide based, polyurethane foam sealants, acrylic based; e.g. for windows, construction etc.) |
|
Coatings and inks (e.g. for car care products, construction, paper, board) |
2 |
Adhesives (polymer based, e.g. for construction, paper) |
|
*1: Market experience categories interpretation: 1) Main alternative on market. 2) Significant market experience. 3) Examples of full scale experience. 4) Pilot/lab scale experience.
Key characteristics
Table 5.25 describes some key characteristics of GTA as alternative to DEHP, DBP and BBP.
Table 5.25 key characteristics of GTA as alternative to DEHP, DBP and BBP
Parameter |
Value |
Remarks |
Efficiency (as plasticiser in PVC compared to DEHP)*1 |
NA |
|
Price (primo 2009) |
€1,50/KG |
Lanxess (2009) |
Price relative to DEHP (≈0.8-1€/kg in 2008/2009; 1€ used for calculations) |
150% |
|
Effective price relative to DEHP |
NA |
|
Limitations in use, if any, noted by supplier in data for this study |
|
NA |
Notes: *1: Efficiency indicator, also called substitution factor, indicating the concentration of plasticiser in PVC needed, compared to DEHP, to achieve a specified flexibility according to a well defined method. DEHP has substitution factor 1 per definition, while plasticisers needing lower concentration (more effective) have lower values, and plasticisers needing higher concentrations have higher effectiveness value. NA = not available
Conclusions
According to a producer, GTA can substitute for DBP and BBP in adhesives, inks and coatings. The price of GTA is somewhat higher that DEHP (and DBP and BBP). The data available does not allow a closer assessment of GTA's technical suitability as alternative to DEHP, DBP and BBP.
5.10 TXIB (trimethyl pentanyl diisobutyrate)
TXIB is an ester of the branched alkane trimethyl pentanyl with two butyrate groups. Its CAS no. is 6846-50-0. Until 2006, it was marketed by Eastman as TXIB plasticiser, but since then it has been renamed TXIB formulation additive.
TXIB

(Eastman, 2009e)
Producer's description (extracts)
Eastman has given the following presentations of TXIB (Eastmann, 2006, 2009f): TXIB formulation additive is a superior primary plasticiser for PVC plastisols. It has good compatibility with PVC, and it is compatible with all common primary and secondary plasticisers. TXIB provides low viscosity characteristics in plastisols with good viscosity stability over time. TXIB is the lowest viscosity (9 cps) additive available to the flexible PVC industry. TXIB is completely compatible with PVC in all proportions and is usually blended with general-purpose plasticizers such as DOP or DOTP. The unique low viscosity makes this material particularly suitable for PVC plastisols and often allows adding additional fillers to the plastisol, resulting in a cost savings. TXIB has efficiency generally equal to DOP, which makes substitution in a vinyl formulation very easy. It imparts a dry surface to the vinyl, excellent resistance to staining, and physical properties equivalent to DOP. TXIB is also used in inks, coatings, urethane elastomers, and nail polish lacquers.
Application/Uses:
- Automotive OEM
- Coatings for automotive plastics
- Lithographic and letterpress oil-based inks
- Nail care
- Phthalate-free diluent for MEKP formulations
- Plastisols
- Sheet vinyl flooring
- Toys/Sporting goods
- Traffic cones
- Vinyl compounding
- Vinyl gloves
- Wall coverings
Application and market experience
Eastman has not wished to provide detailed feedback for this project on TXIB's suitability for substituting for DEHP, DBP and BBP. Eastman has informed that TXIB cannot be used as a direct replacement for DEHP, DBP or BBP. TXIB is used to lower the viscosity of plastisols; one function DBP has been used for. TXIB does however not increase gellation speed for faster production, as DBP and BBP is used for. TXIB cannot work as a primary plasticiser (Eastman, 2009).
In a study of plasticiser alternatives for non-PVC applications (COWI, 2000), TXIB was proposed by market actors as a substitute for phthalates in adhesives and sealants.
Key characteristics
Table 5.26 below shows selected comparisons from Eastman (2009c) between TXIB, DEHP ("DOP"), DEHT ("168") and other plasticisers of interest for selected parameters (more parameters are shown in reference). Note that TXIB in PVC has lower extractability in oil and hexane than DEHP, but higher in soapy water. The modulus (resistance to elongation) and low temperature flexibility is similar to DEHP, while the volatility of TXIB is a factor three higher than DEHP. Plastisol viscosities are lower than for DEHP.
Table 5.26 Comparison between DEHT ("168"), DEHP ("DOP"), TXIB and other plasticisers (from Eastman, 2009c)
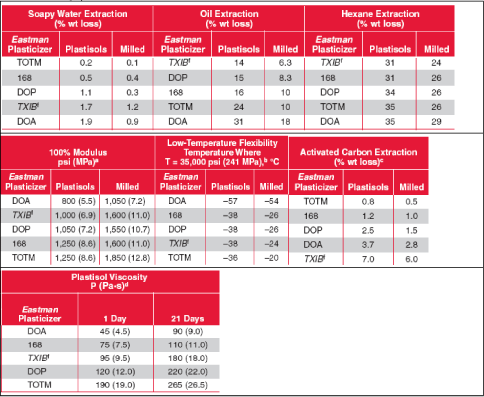
Notes: Plastisols contain 60 phr plasticiser; milled and calendered PVC contains 50 phr plasticiser; phr meaning parts per 100 parts hard PVC by weight. a) Stress at which PVC is elongated 100%. Lower value indicates higher efficiency of plasticiser (ASTM D638). b) Temperature at which the shown stiffness (torsion) is reached (ASTM D1043). c) Indication of volatility at elevated temperatures (ASTM D1203). d) Brookfield viscosity, determined with a number 4 spindle at 6rpm and 23 C.
Table 5.27 below shows some other performance dataset for TXIB compared to DEHP, DBP and BBP. As shown, here TXIB has higher hardness (lower efficiency) than the phthalates, high volatility (yet lower than DBP) and much higher extractability in water. Extractability in kerosene is higher than BBP, but lower than DEHP and DBP.
Table 5.27 Technical key parameters of TXIB compared to DEHP, DBP and BBP (from Sears and Darby, 1982)
Plasticiser in PVC, conc. 40% =67 phr in same PVC resin |
Shore A hardness |
Volatility,% lost, 1 day at 87 °C over activated carbon |
Extracted in water,% |
Extracted in kerosene (jet fuel, etc.),% |
DEHP |
69 |
4.5 |
0.01 |
44 |
DBP |
62 |
45.4 |
0.25 |
9.1 |
BBP |
68 |
7.7 |
0.07 |
3.4 |
TXIB |
76 |
23.7 |
2.83 |
5.2 |
Table 5.28 below describes some key characteristics of TXIB as alternative to DEHP, DBP and BBP.
Table 5.28 key characteristics of TXIB as alternative to DEHP, DBP and BBP
Parameter |
Value |
Remarks |
Efficiency (as plasticiser in PVC compared to DEHP)*1 |
|
Close to 1 (Eastman, 2009f) |
Price (primo 2009) |
NA |
|
Price relative to DEHP |
NA |
|
Effective price relative to DEHP |
NA |
|
Compatibility/solubility in PVC |
|
Compatible |
Permanency (migration, evaporation, extraction) |
|
High volatility, see below (Wilson, 1995) |
Processability (fusing speed and temperature, etc.) |
|
Gives low viscosity to plastisols (Eastman, 2009f) |
Limitations in use, if any, noted by supplier in data for this study |
|
NA |
Notes: *1: Efficiency indicator, also called substitution factor, indicating the concentration of plasticiser in PVC needed, compared to DEHP, to achieve a specified flexibility according to a well defined method. DEHP has substitution factor 1 per definition, lower = more effective, higher = less effective. NA = not available
According to Wilson (1995), TXIB shows unique performance parameters in PVC plastisols. It is a useful component of plastisols formulated to give hard end products since it confers little viscosity at low levels of addition. It has been widely used in cushion vinyl flooring for this purpose, usually in conjunction with BBP; this use has however declined greatly in the 1990s as its high volatility causes unacceptable emissions from end products.
Conclusions
TXIB seems to have some technically relevant characteristics as plasticiser. TXIB was found in many products analysed, 25% and 11% respectively, in two European studies of large samples of toys and childcare articles (its presence need not have been as a primary plasticiser). Given the fact that the producer does not consider TXIB an alternative to DEHP, DBP or BBP, and the information that the usage of TXIB in vinyl flooring has declined in the 1990s due to high emissions from end products, it seems that TXIB should maybe not be seen as a suitable alternative to any of these substances.
5.11 Summary and discussion of technical and economical assessment of alternative plasticisers
The technical description in this report of ten selected alternatives to DEHP, DBP and BBP is based on the producers' assessments of relevant application fields and experience on the market, as well as the evidence of already established practises, especially in the toys, foodstuffs and medical product fields, but also for other end-uses. Based on the available information, a number of suitable alternative plasticisers have been identified for most applications. Some of the alternative plasticisers have a broad application scope, others are more specialised. A summary of the assessed alternatives is given in Table 5.29. A summary of some technical performance parameters for the assessed alternatives compared to DEHP, DBP, BBP and other selected phthalates is given below in annex 3. For some of the substances the manufacturers have provided information on market experience. The data are summarised in Table 5.30. Some of the substances, for which specific information on market experience has not been supplied (e.g. DINCH), certainly have some experience as indicated by the production volumes of the substances.
Industry may have, or may get in the future, more knowledge on the possibilities and limitations of the described plasticisers, which can feed into the decision-making process as regards regulation of DEHP, DBP and BBP. So far, the dominance for many years of DEHP and other ortho-phthalate plasticisers may have naturally limited the motivation to get more full scale experience with other plasticiser types. Under other circumstances, driven by other priorities, the experience with so far less favoured plasticisers would inevitably increase. The expenses associated with such additional research and implementation has not been assessed in this study. The research would however not have to start from scratch, as many relevant substances have been investigated for plasticiser characteristics in early research.
DINP and DIDP have become dominating alternatives to DEHP due to their closeness in performance to DEHP, their availability and their only moderately higher costs. As mentioned, these ortho-phthalates were not included for deeper assessment in this study, because they are already well described, technically and environmentally.
In some cases, blends of different alternative plasticisers may be needed to attain the desired technical characteristics. This is also a well known practice with many DEHP uses. More blending may be needed with some of the non-phthalate alternatives to achieve general plasticiser characteristics. By way of example, a Danish toy producing company attempted a switch to ATBC as primary plasticiser in all PVC toys etc. for small children. However in the existing production setup, it suffered from a variety of technical drawbacks when compared with DINP: ATBC would not take decoration, it had high migration into adjacent materials leading to swelling and splitting, and there was a consequent need for tooling changes. Development led to the use of a mixture of ATBC, DINCH and DEHT, which could be blended in a variety of combinations to achieve softened PVC that performed to the required standards with the existing production setup, and could be used as a one-to-one alternative to DINP. Also, some of the marketed plasticiser products consist of several substances, pre-mixed to provide desired performance characteristics. The products Soft-n-safe and Benzoflex 2088 described in this report are examples of such mixed plasticiser products.
Table 5.29 summary of the technical assessment of alternative plasticisers
Substance |
Overall technical assessment |
ASE |
ASE is a general plasticiser alternative to DEHP. The producer has indicated significant market experience for most traditional DEHP, DBP and BBP uses. |
ATBC |
The performance of ATBC on some parameters seems similar to DEHP, indicating technical suitability for substitution of DEHP for some applications. The higher extractability in aqueous solutions and the higher volatility may reduce the performance of ATBC as a plasticiser in PVC. The data available does not allow a closer assessment of ATBC's technical suitability as alternative to DEHP, DBP and BBP |
COMGHA |
The producer has indicated significant market experience in several of the traditional DBP and BBP specialty plasticiser applications and certain DEHP applications, notably in the non-polymer (adhesives, sealants, etc.) and PVC spread coating (plastisol) application fields. According to the producer, Benzoflex 2088 (with DEGD) has become the main non-phthalate alternative to DBP or BBP in vinyl flooring production in Europe. The higher extractability in water may limit its use for some applications. |
DEGD |
According to the producer, COMGHA still has relative moderate market experience, albeit with many examples of full scale usage and pilot/lab scale tests, and significant market experience in some plastisol application and cosmetics. The producer found good performance on key technical parameters indicating a potential for substituting for DEHP and perhaps for DBP and BBP in some traditional uses og these substances. |
DGD |
DEHT is a general plasticiser alternative to DEHP. Today, terephthalates like DEHT are more commonly used in the USA than elsewhere. |
DEHT |
DINA has mostly been used for low temperature PVC applications and in PVC film/wrapping . The data available for this study does not allow clear-cut conclusions as regards DINA's suitability as alternative to DEHP |
DINA |
The producer’s sales appraisal indicates a relatively wide usage of DINCH for general plasticiser purposes. DINCH was the most frequently found plasticiser in two European surveys of plasticisers in toys and childcare articles. The data available does not allow a closer assessment of DINCH's technical suitability as alternative to DEHP, DBP and BBP. |
DINCH |
The fact that DGD for many years has been a well known and much used competitor to BBP, especially in PVC flooring and in PVA adhesives, indicates a clear potential for substituting DGD for BBP, from a technical point of view. DGD may probably also substitute for some traditional uses of DEHP and DBP. |
GTA |
According to a producer, GTA can substitute for DBP and BBP in adhesives, inks and coatings. The data available does not allow a closer assessment of GTA's technical suitability as alternative to DEHP, DBP and BBP. |
TXIB |
TXIB was found in more than 10% of the samples in surveys of plasticisers in toys and childcare articles. However, the producer does not consider TXIB an alternative to DEHP, DBP or BBP, and the usage of TXIB in vinyl flooring has declined in the 1990’s due to high emissions from end products. Consequently, TXIB seems not to be a suitable alternative to DEHP, DBP or BBP. |
Table 5.30 Alternatives to DEHP, BBP and DBP proposed by contacted manufactures, by application and with indication of market experience
Application |
ASE |
GTA |
DGD |
Mix of DGD, DEGD, TGD |
ATBC |
COMGHA |
Substitute for DEHP |
|
|
|
|
|
|
Polymer applications: |
|
|
|
|
|
|
Calendering of film, sheet and coated products |
2 |
2 |
4 |
4 |
3 |
3 |
Calendering of flooring, roofing, wall covering |
4 |
2 |
3 |
3 |
|
3 |
Extrusion of hose and profile |
2 |
2 |
3 |
3 |
3 |
3 |
Extrusion of wire and cable |
2 |
2 |
3 |
3 |
|
3 |
Extrusion of miscellaneous products |
2 |
2 |
2 |
2 |
2 |
3 |
Injection moulding of footwear and miscellaneous |
? |
2 |
2 |
2 |
|
3 |
Spread coating of flooring |
2 |
2 |
2 |
2 |
|
2 |
Spread coating |
2 |
2 |
2 |
2 |
|
3 |
Car undercoating |
2 |
|
3 |
3 |
|
|
PVC medical articles |
|
2 |
|
|
2 |
|
Toy and childcare articles |
|
2 |
|
|
1 |
|
Non polymer applications: |
0 |
|
|
|
|
|
Adhesives/sealant, rubber |
2 |
2 |
1 |
1 |
2 |
4 |
Lacquers and paint |
2 |
2 |
2 |
2 |
|
4 |
Printing ink |
2 |
2 |
2 |
2 |
2 |
3 |
Production of ceramics |
|
|
|
|
|
|
Substitute for DBP |
|
|
|
|
|
|
Plasticiser in PVC |
2 |
|
1 |
1 |
2 |
2 |
Plasticiser in other polymers |
2 |
|
|
|
|
2 |
Adhesives |
2 |
2 |
|
1 |
3 |
4 |
Printing inks |
2 |
3 |
|
|
2 |
3 |
Miscellaneous: |
|
|
|
|
|
|
Sealants |
2 |
|
|
|
3 |
4 |
PU foam sealants |
2 |
|
|
|
4 |
|
Nitrocellulose paints |
2 |
3 |
2 |
2 |
2 |
|
Film coatings |
3 |
|
|
|
3 |
|
Glass fibre production |
|
|
|
|
|
4 |
Cosmetics |
|
|
|
|
|
2 |
Substitute for BBP |
|
|
|
|
|
|
Polymer applications: |
|
|
|
|
|
|
General PVC (e.g. for moulded plastic parts) |
2 |
|
|
|
|
4 |
Plastisol coating, for flooring |
2 |
|
1 |
1 |
|
3 |
Extrusion or spread coating |
2 |
|
|
2 |
|
2 |
Films, calendering |
2 |
|
4 |
4 |
|
3 |
Non polymer applications: |
|
|
|
|
|
|
Sealants |
2 |
|
1 |
1 |
|
|
Coatings and inks) |
|
2 |
1 |
|
3 |
|
Adhesives |
2 |
|
|
1 |
|
|
Nail polish |
|
|
|
|
1 |
|
*1: Market experience categories interpretation: 1) Main alternative on market. 2) Significant market experience. 3) Examples of full scale experience. 4) Pilot/lab scale experience
Prices of alternative plasticisers
Some of the alternative plasticisers investigated have similar or only slightly higher prices than the relevant competing substances among DEHP, DBP and BBP; see Table 5.31 below. Others have higher or substantially higher prices. As shown in the table, the non-phthalate alternatives DGD, DEGD and DEHT were in the same price range as the DEHP, DBP and BBP, (as well as the ortho-phthalate alternatives DINP and DIDP), whereas ASE, DINA , DINCH and GTA were somewhat more expensive and ATBC and COMGHA were considerably more expensive (counted as direct relative price). We have not been able to find a price for TXIB for this study. Note that here BBP and DEHP had the same price per weight unit in this case. In older literature, BBP is reported to be a specialty plasticiser with higher price than DEHP.
Prices of chemicals (and other industrial products) tend to decrease as production capacity and competition is increased. Different chemicals are however based on different raw materials and more or less complex and resource demanding chemical synthesis technologies. This of course sets limits to the minimum prices attainable even in a mature market, and some of the alternative plasticisers described may likely remain at higher price levels. It should be noted that the prices of DEHP have dropped significantly over the last decade or more.
According to a Danish manufacturer, when the Danish ban of DEHP and 5 other phthalates in toys etc. came into force, the price of products for one Danish toy company rose by approximately 50% because the international manufacturers had to produce special deliverances to the Danish marked without phthalates. Later, when the ban comprised the entire EU the prices dropped again. The company estimates that the ban has resulted in a remaining increase in prises of approximately 10-20% because the alternative substances generally are more expensive even after the preliminary reduced costs related to changing production methods.
Table 5.31 Prices and relative prices to DEHP of the assessed alternatives and some other reference plasticisers
Substance |
Price |
Relative price to DEHP,% |
Substitution factor |
Effective relative price,% |
Remarks´´´´´´ |
Phthalates and other reference plasticisers: |
|
|
|
|
|
DEHP (2006) |
0.70 USD/Lb |
- |
- |
- |
TURI (2006) |
DEHP (2006-2009) |
≈0.8-1 €/kg |
- |
- |
- |
ExxonMobil (2009), Arbeitsgemeinschaft PVC (2006) |
BBP (2006) |
0.70 USD/Lb |
100% |
0.94 |
94% |
TURI (2006) |
DINP (2006) |
0.73 USD/Lb |
104% |
1.06 |
111% |
TURI (2006) |
DIDP (2006) |
0.77 USD/Lb |
110% |
1.10 |
121% |
TURI (2006) |
Assessed alternatives: |
|
|
|
|
|
ASE (2009) |
1,75 €/kg |
175% *1 |
NA |
NA |
Lanxess (2009) |
ATBC |
NA |
300% |
NA |
NA |
ExxonMobil (2009); Karbæk (2003) |
COMGHA |
3.5€/kg |
≈350% *1 |
≈1 |
≈350% |
Danisco (2009) |
Benzoflex 2088 (with DEGD) |
|
"Slightly higher" |
|
|
Genovique (2009) |
DGD (2006) |
0.73 USD/Lb |
104% |
0.98 |
102% |
TURI (2006) |
DEHT (2006) |
0.74 USD/Lb |
106% |
1.03 |
109% |
TURI (2006) |
DINA |
|
150-200% |
|
|
ExxonMobil (2009) |
DINCH (2006) |
0.91 USD/Lb |
130% |
NA |
NA |
TURI (2006) |
GTA |
€1,50/KG |
150% *1 |
NA |
NA |
Lanxess (2009) |
TXIB |
NA |
NA |
NA |
NA |
|
Notes: *1: DEHP price in 2006-2009 ≈0.8-1 €/kg; 1 € is used for calculations. NA = Not available for this study.
| Front page | | Contents | | Previous | | Next | | Top |
Version 1.0 November 2010, © Danish Environmental Protection Agency
|