| Til bund | | Forside |
Arbejdsrapport fra Miljøstyrelsen nr. 4, 2005
Forbehandling af hærdeplastbaserede kompositmaterialer til genanvendelse
Indholdsfortegnelse
Forord
Sammenfatning og konklusioner
Summary and conclusions
1 Indledning
2 Baggrund og formål
3 Kompositmaterialer
4 Forbehandlingsmetoder
5 Eksisterende viden og erfaringer
6 Termisk forbehandling
7 Mekanisk forbehandling
8 Referencer
Bilag A Rapport over pyrolyse
Bilag B Fotos fra første forsøgsserie, termisk forbehandling
Bilag C Rapport over forbrænding af glasfiberplader
Forord
Dette projekt er støttet af Miljørådet for renere produkter under Miljøstyrelsen som en del af plastindustriens brancheprojekt samt af Sektionen for Kompositmaterialer under Plastindustrien i Danmark.
Projektet er udført af en projektgruppe bestående af
Helle Rasmussen, LM Glasfiber A/S
Poul Hinrichsen, EM Fiberglas A/S
Anders Korsgård, Fiberline Composites A/S
Benedikte Jørgensen, Fiberline Composites A/S
Hans Chr. Gabelgaard, Jupiter Plast A/S
Per Hansen Filt, Vestas Wind Systems A/S
Torben Knudsen, Teknologisk Institut, Plastteknologi
Jørn Bech, Teknologisk Institut, Plastteknologi
Kristina Elvebakken, Plastindustrien i Danmark
Der er desuden nedsat en følgegruppe, som ud over de ovenfor nævnte projektgruppemedlemmer består af
Birgitte Kjær, Miljøstyrelsen
Thorvald Isager, H.J. Hansens Genvindingsindustri A/S
Erik Grove-Nielsen, ReFiber ApS
Ole Kristensen, Kommunekemi
Aage Lystrup, Forskningscenter Risø, Afdelingen for Materialeforskning
Følgende virksomheder har medvirket til den praktiske gennemførelse af projektet:
KMT - Nord
Kommunekemi a/s
ReFiber ApS
H.J. Hansen Genvindingsindustri A/S
EM Fiberglas A/S
Jupiter Plast A/S
Vestas Wind Systems A/S
Sammenfatning og konklusioner
I dette projekt er effektiviteten af forskellige metoder til at forbehandle affald af udtjente kompositmaterialer undersøgt. Forbehandlingen er nødvendig, hvis kompositaffaldet skal genanvendes. Mængden af
kompositaffald forventes at stige betydeligt i fremtiden, og dette affald udgør et potentielt ressource for samfundet, som det - afhængig af en samlet vurdering af de miljømæssige, tekniske og
samfundsmæssige forhold - kan være formålstjenligt at udnytte. Der er i projektet hovedsageligt fokuseret på de tekniske forhold vedr. forbehandling af kompositaffald, mens de økonomiske og
miljømæssige forhold kun i begrænset omfang er vurderet.
Forbehandlingsmetoderne er undersøgt ud fra i hvor høj grad de værdifulde egenskaber i materialerne bibeholdes under forbehandlingen og frem til den endelige genanvendelse. Jo flere og bedre egenskaber
det forbehandlede materiale bibeholder, jo højere værdi kan materialet bidrage med under den endelige genanvendelse. Overordnet set sigtes der mod, at det forbehandlede materiale kan bidrage med en
høj værdi ved genanvendelse af materialet og ved fremstilling af nye produkter.
To overordnede metoder til forbehandling af kompositaffald i form af glasfiberarmeret plast er undersøgt:
- Termisk forbehandling, hvor plastmaterialet forbrændes under energigenvinding, og hvor egenskaberne af det tilbageværende uorganiske materiale, primært glasfibre, er undersøgt. Forbrændingen kan
gennemføres vha. flere forskellige metoder, og i dette projekt har der hovedsageligt været fokuseret på en pyrolyselignende forbrænding, der foregår i to trin
- Mekanisk forbehandling, hvor kompositaffaldet neddeles, og hvor egenskaberne af det neddelte materiale er undersøgt
Der er desuden fremstillet prøveemner af det termisk forbehandlede materiale til bestemmelse af egenskaberne ved endelig genanvendelse af materialet. De praktiske forsøg er foretaget på kompositaffald fra
vindmølleindustrien i form af udskæringer af kompositdele af to forskellige typer plastmateriale, polyester og epoxyplast.
På baggrund af undersøgelserne vedrørende den termisk forbehandling kan det konkluderes, at glasfibrenes brudstyrke under den termiske forbehandling reduceres med mere end 50%. Disse reducerede
egenskaber har dog vist sig tilstrækkelige til, at de forbehandlede glasfibre ved imprægnering med umættet polyester eller epoxyplast kan bruges til fremstilling af produkter, hvortil der stilles moderate krav til
mekaniske egenskaber. Produkterne vil kunne fremstilles ved kendte produktionsmetoder som håndoplægning, vakuuminjektion og presning.
For at opnå lettere håndtering af de termisk forbehandlede glasfibre bør der udvikles bedre metoder til at binde glasfibrene, så de kan anvendes på tilsvarende måde, som det kendes for nye glasfibermåtter
og rovingvæv. Endvidere vil det være hensigtsmæssigt både af miljømæssige (generende støv) og procesmæssige årsager at udvikle effektive metoder til at fjerne uorganiske partikler og støv, i form af f.eks.
farvepigmenter og brandhæmmende additiver, fra glasfibrenes overflade.
Der har været gennemført forsøg med at påføre de forbehandlede glasfibre en size for at forbedre bøjestyrken af de prøveplader, som er fremstillet af de forbehandlede glasfibre. Effekten var dog
umiddelbart beskeden, idet det kun for en enkelt prøveplade af polyesterlaminat lykkedes at forbedre bøjestyrken med 11%, mens bøjestyrken for de øvrige 5 prøveplader forblev uændret. Derimod viste
resultaterne en væsentligt mindre spredning på bøjestyrken ved resizing i forhold til de ikke resizede prøveplader, dvs. at man ved at resize de forbehandlede glasfibre kan opnå en mere ensartet kvalitet af
egenskaber.
Af de termisk forbehandlede glasfibre er der ved vakuum-injektionsmetoden blevet fremstillet tre forskellige typer demonstrationsemner. Emnerne er forskellige i udstrækning og højde, og de viser
umiddelbart, at det er muligt at støbe enkle emner uden større problemer. Binding af de forbehandlede glasfibre med en slags lim vil gøre det lettere at drapere glasfibrene i høje forme, og samtidig forhindre
fiberbundterne i at glide fra hinanden.
På baggrund af undersøgelserne vedr. den mekaniske forbehandling er det påvist, at det er muligt at neddele kompositaffald i ensartede fraktioner ved at neddele og sigte materialet ad flere omgange. Af de
neddelte kompositfibre, som består af en blanding af glas og plastmateriale, er fremstillet semifleksible ”måtter”, som er bundet sammen med opløsninger af PVA-lim henholdsvis epoxyplast. Disse måtter kan
formes og delvist tilpasses et emne, ligesom det er tilfældet med nye glasfibermåtter. Formgivningsmulighederne i forhold til nye glasmåtter eller glasfibre efter termisk forbehandling er dog begrænsede, fordi
det neddelte materiale i form af fibre og fiberbundter i ”måtterne” er mere stift i det.
Der er fremstillet prøveplader af semifleksible ”måtter”, men de har vist sig at have lave mekaniske egenskaber. Årsagen hertil er, at der er for mange luftindeslutninger og utilstrækkeligt samvirke mellem
neddelt komposit plastmateriale. De semifleksible ”måtter” vil, efter yderligere udvikling, kunne bruges til fremstilling af produkter, hvortil der stilles krav om moderate mekaniske styrkeegenskaber. De
semifleksible ”måtter” af neddelt kompositmateriale vil generelt kunne benyttes til støbning ved vakuuminjektion, håndoplægning og presning.
Det er ud fra de gennemførte metoder til forbehandling af kompositmaterialer ikke muligt at sige noget om, hvorvidt termisk forbehandling af kompositmaterialer er mere fordelagtig end mekanisk
forbehandling eller omvendt. En sådan vurdering vil afhænge af flere forhold, bl.a. sammensætningen af det konkrete kompositaffald, anvendelsesmuligheder og markeder for det forbehandlede materiale,
muligheder for indsamling og sortering af kompositaffaldet, samt hvor i verden kompositmaterialet befinder sig, når det skal bortskaffes.
Overordnet set har den termiske forbehandling de umiddelbare fordele, at de mange forskellige typer af kompositmaterialer baseret på forskellige plastmaterialer efter forbehandlingen vil bestå af en
forholdsvis ensartet glasfraktion, som lettere kan samles i store mængder. Afhængig af størrelsen af den konkrete forbrændingsovn vil det ved den termiske forbehandling i mange tilfælde kun være
nødvendigt med en begrænset neddeling af de større affaldsemner inden forbehandling. Omvendt kræver den termiske forbehandling typisk store investeringer i form af dyre ovne eller lignende.
Den mekaniske forbehandling vil ikke nødvendigvis kræve så avanceret og investeringstungt neddelingsudstyr, men der kan være stor slitage på udstyret under neddelingen. Det resulterende neddelte
kompositmateriale vil typisk bestå af en kompleks blanding af forskellige plastmaterialer, som det sandsynligvis kan være svært at fremstille i en ensartet kvalitet og finde genanvendelsesmuligheder for, med
mindre der foretages en sortering. Omvendt, hvis der på et marked kan findes specifikke genanvendelsesmuligheder for det neddelte kompositmateriale, kan den mekaniske forbehandling have sine fordele.
Sammenfattende kan det konkluderes, at der formentlig på sigt vil være behov for anlæg til både termisk og mekanisk forbehandling, hvis en større mængde af forskellige typer udtjente kompositmaterialer
skal kunne forbehandles og endeligt genanvendes i Danmark. Mulighederne for endelig anvendelse af de forbehandlede materialer skal ses i lyset af materialernes begrænsede styrkeegenskaber i kombination
med prisen. I denne forbindelse bør det nævnes, at en af de væsentligste årsager til netop at vælge at fremstille produkter af glasfiberforstærket plast, bl.a. er de høje mekaniske styrkeegenskaber, som
kompositprodukter kan udvise.
Hvis det genvundne materiale sammenlignes med virgine glasfibre og deres egenskaber og pris, synes det klart, at udfordringen i at udvikle økonomisk og miljømæssigt fordelagtige genanvendelsesløsninger
for kompositaffald ligger i at opdrive anvendelsesmuligheder af høj værdi for det genvundne materiale.
Der er gode muligheder for at forbedre og optimere begge de undersøgte forbehandlingsmetoder og det heraf resulterende genvundne materiale, som bør tilpasses specielle anvendelser. Det er afgørende, at
det genvundne materiale kan leveres med en ensartet standard og til konkurrencedygtige priser.
Der er i dette projekt lagt vægt på de tekniske forhold for de udvalgte forbehandlingsmetoder, men det udestår at tilpasse de foreliggende resultater til en konkret industriel produktion og undersøge
økonomien herved. Endvidere bør der fortages en mere detaljeret miljø- og samfundsøkonomisk vurdering af de forskellige forbehandlings- og efterfølgende endelige genanvendelsesmetoder for
kompositmaterialer.
Summary and conclusions
In this project the efficiency of various methods to pre-treat waste from worn out products made from composite materials has been investigated. The pre-treatment is necessary, if the composite waste is to
be recycled. The amount of composite waste is expected to increase considerably in the future, and this waste constitutes a potential resource for the society, which it would be expedient to exploit -
depending on an overall evaluation of the environmental, technical and social conditions. In the project the main focus has been on the technical conditions regarding pre-treatment of composite waste, while
the economical and environmental conditions have only been evaluated to a limited extent.
The pre-treatment methods have been examined on the basis of the degree to which the valuable properties of the materials are maintained during the pre-treatment and until final recycling takes place. The
greater the degree to which the material properties are maintained the greater the value of the material during the final recycling. It is the primary aim that the pre-treated material will contribute substantially
when recycling the material and manufacturing new products.
Two key methods for pre-treatment of composite waste in the form of reinforced fibreglass have been investigated:
- Thermal pre-treatment, where combustion of the plastic material is combined with energy recovery, and where the properties of the remaining inorganic material, primarily glass fibres, have been
examined. The combustion can be carried out by means of several methods, and in this project the main focus has been on a pyrolysis-like combustion which takes place in two steps
- Mechanical pre-treatment, where the composite waste is granulated, and where the properties of the granulated material has been examined
Furthermore, test specimens have been produced from the thermally pre-treated material for determination of the properties at final recycling of the material. The practical experiments have been carried out
on waste from the windmill industry in the form of cut-outs of composite parts of two different types of plastic material, polyester and epoxy resin.
On the basis of the evaluations regarding the thermal pre-treatment it can be concluded that the tensile strength of the glass fibres during the thermal pre-treatment is reduced by more than 50%. However
these reduced properties have shown to be sufficient so that the pre-treated glass fibres when being impregnated with unsaturated polyester or epoxy resin can be used for the manufacture of products, on
which moderate demands to mechanical properties are made. Known production methods like hand lay-up, vacuum injection and compression moulding can be used when manufacturing the products.
In order to achieve an easier handling of the thermally pre-treated glass fibres better methods for binding the glass fibres should be developed, making it possible to use them in processes known for the new
glass fibre mats and roving fabric. Furthermore, for environmental (irritant dust particles) and process reasons, it will be advisable to develop efficient methods for the removal of inorganic particles and dust
such as pigments and fire resisting additives, from the surface of the glass fibres.
Experiments have been carried out applying the pre-treated glass fibres with a size in order to improve the flexural strength of the test plates, which have been produced from the pre-treated glass fibres.
However, the effect was modest, as we only succeeded in improving the flexural strength by 11% for one test plate made of polyester laminate, while the flexural strength for the remaining 5 test plates
remained unchanged. However, the results showed a considerably lower deviation of the flexural strength for the resized versus the non-resized test plates, i.e. resizing the pre-treated glass fibres makes it
possible to achieve a more uniform quality of the composite materials.
From the thermally pre-treated glass fibres three different types of demonstration specimens have been manufactured by using the vacuum-injection method. The specimens differ in dimension and height, and
they show that it is possible to mould simple specimens without major problems. Binding of the pre-treated glass fibres with some kind of glue will make it easier to drape the glass fibres in high moulds, and
at the same time prevent the bundles of fibres from sliding away from each other.
Based on the examinations regarding the mechanical pre-treatment it has been demonstrated that it is possible to granulate composite waste into uniform fractions by repeated granulating and sieving the
material. Semi-flexible “mats” have been manufactured from the granulated composite fibres, consisting of a mixture of glass and plastic material. These mats have been bound together with solvents of
PVA-glue and epoxy resin respectively. These mats can be shaped and partly adjusted to a component, as is the case with new glass fibre mats. The possibilities of modelling the granulated composite
materials compared to new glass mats or glass fibre after thermal pre-treatment are, however, limited, as these materials in the form of fibres and bundles of fibres in the “mats” are more stiff.
Test plates of semi-flexible “mats” have been manufactured, however they have low mechanical properties. The reasons for the reduction in mechanical properties are entrapped air and insufficient interaction
between granulated composite material and the matrix material. After further development it should be possible to use the semi-flexible “mats” for manufacture of products where moderate demands are
made regarding mechanical strength properties. In general, the semi-flexible “mats” of granulated composite material can be used for moulding by vacuum injection, hand lay-up and compression moulding.
Based on the evaluated methods for pre-treatment of composite materials it is not possible to conclude whether thermal pre-treatment of composite materials is more advantageous than mechanical
pre-treatment or vice versa. Such an evaluation would be dependent on further criteria such as the composition of the actual composite waste, application possibilities and markets for the pre-treated
material, possibilities of collecting and sorting the composite material, and where in the world the composite material is located at the time of removal.
The thermal pre-treatment has the key advantage that the many different types of composite materials based on different plastic materials after the pre-treatment will consist of a relatively uniform glass
fraction, which will be easier to gather in sufficient quantities. At the thermal pre-treatment - dependent on the size of the specific waste incinerator - it will in many cases only be necessary with a limited size
reduction of the bigger waste parts prior to pre-treatment. The thermal pre-treatment on the other hand requires major investments in the form of expensive ovens or the like.
Often, the mechanical pre-treatment will not necessarily require such advanced and heavy investments of downsizing equipment. However, a high degree of wear will occur on the equipment during the
granulation. The resulting granulated composite material will typically consist of a complex mixture of different plastic materials, which will be difficult to produce in a uniform quality and find recycling
possibilities, unless a pre-sorting is carried out. On the other hand, if there is a specific market demand for the granulated composite material, the mechanical pre-treatment may be advantageous.
In summary, it can be concluded that in the long term there will probably be a need for plants for both thermal and mechanical pre-treatment, where large amounts of different types of worn out composite
material are to be pre-treated and finally recycled in Denmark. The possibilities of final recycling of the pre-treated materials must be seen in the light of the limited strength properties combined with the price.
In this connection it should be mentioned that one of the principal reasons for choosing to manufacture products of glass fibre reinforced plastic is the high mechanical strength properties of composite
products.
When comparing the recycled material with virgin glass fibres and the properties and price, it is obvious that the challenge in developing economically and environmentally advantageous recycling solutions for
composite waste is to procure high value applications for the recycled material.
Good possibilities exist to improve and optimise both examined pre-treatment methods and the resulting recycled material, which should be adjusted to special applications. It is, of course, decisive that the
recycled material can be produced to a uniform standard and at competitive prices.
In this project, the emphasis has been on to the technical conditions for the selected pre-treatment methods; however, the present results must be adapted to a specific industrial production, and the economic
implications must be examined. Furthermore, a more detailed environmental- and socio-economic evaluation of the various pre-treatment- and subsequent final recycling methods for composite materials
should be carried out.
1 Indledning
I dette projekt er der anvendt to forskellige metoder til forbehandling af kompositmaterialer. Den ene vedrører termisk forbehandling; her er formålet at fjerne alt tilstedeværende organiske stof og dermed
efterlade de rene glasfibre og eventuelle andre uorganiske komponenter fx farvepigmenter og brandhæmmende additiver. Den anden vedrører mekanisk forbehandling; her er formålet at neddele
kompositmaterialer til passende fraktioner. Ved begge metoder gælder det om at gøre det forbehandlede materiale egnet til genanvendelse og gerne i produkter, hvor der kan opnås høj værdi i modsætning
til ved anvendelse som fyldstof.
Til gennemførelse af forsøg med metoderne til forbehandling anvendes udskæringer fra produkter, der fremstilles af danske virksomheder. Der er tale om produkter, der er fremstillet af glasfiberforstærket
polyester og glasfiberforstærket epoxy.
Efter forbehandling og fremstilling af forskellige emner af regenerat er der foretaget bestemmelse af udvalgte materialeegenskaber ved prøvning på materialeprøver.
Der er udført en sammenskrivning af eksisterende viden om forskellige metoder til forbehandling af kompositmaterialer og genanvendelse af regenerat til fremstilling af nye produkter af både termoplast og
hærdeplast.
Afslutningsvis er der i projektforløbet blevet fremstillet tre relativt enkle demonstrationsemner for at vise mulighederne for genanvendelse af termisk forbehandlet kompositmateriale.
2 Baggrund og formål
2.1 Baggrund
2.2 Formål
2.1 Baggrund
Dette projekt er en fortsættelse af et tidligere projekt med titlen ”Armeret epoxy- og polyesterplast - forbrug og affaldsmængder” /1/, hvori de forventede mængder af kompositmaterialeaffald i Danmark i de
kommende 20 år er blevet kortlagt. En affaldsprognose fra dette projekt er vist i figur 1.
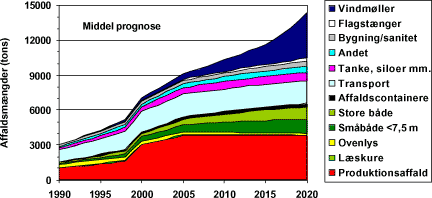
Figur 1 Prognose for kompositaffald i Danmark i 2000 - 2020 (middelprognose). Affald af polyesterbeton og kunstmarmor er ikke medregnet
I dag er det imidlertid vurderingen hos de største fabrikanter af vindmøllevinger, at der forventes en betydeligt hurtigere stigning i affaldsmængderne, end det fremgår af prognosen, fordi der af økonomiske
årsager (større installeret effekt pr. areal) sker en udskiftning til større møller, før de teknisk set er udtjent. I 2003 forventes 340 tons kasserede og udtjente vinger med en stigning til 3900 tons i 2020.
På de ca. 5000 vindmøller der er installeret i Danmark, er der monteret vinger med en samlet vægt på ca. 45.000 tons. De forventes udskiftet i løbet af 15 - 20 år /1/.
En større udfordring, som kompositindustrien står over for i de kommende år, er således, hvordan man skal håndtere produktionsaffald og affald fra udtjente produkter af plastbaserede kompositmaterialer.
Kompositaffald udgør en ressource, som det vil være formålstjenligt at søge udnyttet.
Nye europæiske affaldsdirektiver om deponering og om forbrænding vil medføre et voksende pres på de traditionelle bortskaffelsesmåder. Disse direktiver fortolkes i visse tilfælde forskelligt i de enkelte
medlemslande, hvilket betyder, at det i nogle medlemslande vil blive helt forbudt at deponere kompositaffald. I Danmark derimod vil deponering af kompositaffald fortsat være muligt, men prisen forventes at
stige væsentligt i fremtiden.
Oven i det ser vi lovgivning for specifikke affaldsstrømme så som The End-of-Life Vehicle Directive og The Directive on Waste of Electric and Electronic Equipment, hvormed begreberne
producentansvarlighed og tilbagetagningsforpligtelse indføres, medens der samtidigt pålægges skrappere deponeringsbegrænsninger og begrænsninger i mulighederne for energigenvinding fra slutprodukter.
Det må forventes, at komponent- og produktleverandører, som ikke kan tilbyde et passende affaldshåndterings- og genanvendelseskoncept, kan risikere at miste deres marked. Fra kompositindustriens side
søges der proaktivt efter metoder, der kan give svar på disse tiltag. Fordi produkter, der indeholder plastbaserede fiberkompositter, sælges over hele Europa, og europæisk lovgivning gælder i alle EU- og
EFTA-lande, har kompositindustrien brug for en fælles-europæisk løsning for affald af udtjente kompositprodukter. Green FRP Label-ordningen er et væsentligt bidrag hertil. Green FRP Label er den
europæiske brancheorganisation svar på denne udfordring.
2.2 Formål
Formålet med dette projekt, som er et forprojekt, er at undersøge egnetheden af udvalgte metoder til effektiv forbehandling af hærdeplastbaserede fiberkompositmaterialer, så genanvendelse bliver mulig. Et
væsentligt kriterium for effektiv forbehandling er, at hovedparten af de værdifulde egenskaber i materialerne bibeholdes under forbehandling og frem til endelig genanvendelse. Der sigtes på områder for
genanvendelse, hvor der opnås høj værdi i det nye produkt i modsætning til anvendelser som fyldstof.
Der søges efter forbehandlingsmetoder, som indebærer, at regeneratets egenskaber i størst muligt omfang bibeholdes, således at det- anvendt som råvarer - er bedst muligt egnet til den videre anvendelse.
De undersøgte forbehandlingsmetoder vil blive afprøvet i praksis på et antal udtjente materialeprøver, der anses for at være repræsentative for de komposit produktgrupper, som er kortlagt i det førnævnte
tidligere projekt.
De fysisk/kemiske egenskaber for genvundne glasfibre og neddelte kompositmaterialer bestemmes ved hjælp af forskellige prøvningsmetoder. Endvidere søges mulighederne for genanvendelse vist ved
fremstilling af demonstrations-emner.
I figur 2 vises en generel oversigt over muligheder for genanvendelse af kompositmaterialer, omfattende input i form af kompositaffald af bl.a. udtjente produkter , forbehandlingsmetoder, genanvendelse af
regenerat og eksempler på output-produkter. De område, hvor nærværende projekt har koncentreret indsatsen, er vist med kursiv skrift.
Klik her for at se Figur 2
Figur 2 Oversigt over muligheder for genanvendelse af kompositmaterialer. Dette projekt fokuserer på de områder, som er skrevet med kursiv
3 Kompositmaterialer
3.1 Vedhæftning mellem plast og glasfiber
3.2 Fremstillingsprocesser
3.3 Sandwichkonstruktioner
3.4 Udtjente produkter af kompositmaterialer
Kompositmaterialer er sammensatte materialer, der normalt består af flere synlige faser. To eller flere materialer kombineres så der dannes et brugbart, tredje materiale med nye egenskaber.
Mennesket har tidligt benyttet sig af sammensatte materialer. Et kendt eksempel er klinet ler, der består af halmstrå og ler. I moderne materialeterminologi kunne man kalde dette materiale for stråforstærket
ler eller cellulosefiberforstærket ler. Beton bestående af cement, sand, grus og sten er et andet eksempel. I jernbeton indgår jernarmering som en yderligere fase. Træ er et naturligt forekommende
kompositmateriale, som består af cellulosefibre, der er bundet sammen med limstoffet lignin.
Mange forskellige kompositmaterialer er baseret på plast som bindemiddel mellem fibre. Det bedst kendte plastbaserede kompositmateriale er glasfiberforstærket umættet polyester, som anvendes som
konstruktionsmateriale til en lang række produkter inden for industri, byggeri, transport, energiproduktion og fritidsudstyr. Lystbåde, vindmøller, småfly og landbrugssiloer er nogle af de produkter af
glasfiberforstærket polyester, der er mest synlige i vores omgivelser.
Umættet polyester hører til hærdeplastene. Hærdeplast er karakteristiske ved, at de ikke bliver bløde eller smelter ved opvarmning. Plastdelen i hvert eneste emne af hærdet hærdeplast består faktisk af et
eneste kæmpestort molekyle. Andre almindeligt forekommende hærdeplast er epoxyplast, phenolplast, melaminplast og polyurethan.
I langt de fleste tilfælde er det glasfibre, der anvendes som forstærkningsmateriale i plastbaserede kompositter; men i en række avancerede produkter anvendes carbonfibre eller aramidfibre som
forstærkning. Carbonfibre benævnes undertiden kulfibre eller grafitfibre. Aramid er nok bedre kendt under et af handelsnavnene, nemlig Kevlar&®. Også fibre af andre materialer anvendes i særlige tilfælde.
3.1 Vedhæftning mellem plast og glasfiber
Glas er uorganiske materialer, mens plast er organiske materialer. God vedhæftning mellem plast og glasfiber er en forudsætning for, at kompositmaterialerne kan bruges i lastbærende konstruktioner, idet der
skal kunne overføres kræfter mellem glasfibre og plast. For at forøge vedhæftningen bliver glasfibre, der skal bruges til forstærkning af plast, overfladebehandlet med forskellige stoffer, der sikrer god
vedhæftning både til glasfibre og til plast.
Til forstærkning af umættet polyester og af epoxyplast består overfladebehandlingen typisk af forskellige silaner (siliciumholdige, organiske forbindelser). Foruden det vedhæftningsforbedrende stof indeholder
overfladebehandlingen stoffer, som beskytter de enkelte fibre (monofilamenterne) mod mekanisk overlast under den videre forarbejdning samt stoffer, der binder de enkelte glasfibre sammen til større
bundter. Diameteren af enkeltfibrene er nemlig kun i størrelsesordenen 10 m (= 0,01 mm). Den samlede "pakke" af disse hjælpestoffer i overfladebehandlingen betegnes i branchen med det engelske ord
sizing eller size.
Under termisk forbehandling ved pyrolyse og ved forbrænding som i dette projekt vil hovedparten af hjælpestofferne blive nedbrudt og forsvinde ved fordampning, og man kan defor ikke forvente at opnå
samme gode vedhæftning med regenererede glasfibre som med nye fibre. Muligheden for at tilføre ny size til de regenererede fibre er til stede; der er dog tale om forholdsvis komplicerede og dyre processer.
3.2 Fremstillingsprocesser
Emner af hærdeplastbaserede fiberkompositter fremstilles ved en lang række forskellige processer og varianter heraf. Emnestørrelse, emnegeometri og stykantal er væsentlige faktorer for valg af
fremstillingsproces. Store emner fremstilles traditionelt ud fra flydende plastharpiks ved håndoplægning, sprøjteoplægning og vikling; i de senere år har flere varianter af injektionsmetoder ofte i kombination
med vakuum vundet stor udbredelse. Store emner fremstilles i vore dage også ud fra såkaldt prepregs, som er halvfabrikata, hvori forstærkningsfibrene allerede er positioneret og imprægneret med
plastharpiksen - sædvanligvis i relativt tynde og brede baner. Forsynet med en diffusionstæt plastfolie på begge sider er sådanne prepregs lette at opbevare på rulle eller i lag samt at håndtere under
fremstilling og senere oplægning. Desuden sikrer plastfolien mod, at der ved fordampning mistes materiale, som ellers kan give anledning til arbejdsmiljøproblemer.
Store møllevinger fremstilles i dag både ved vakuumassisteret injektion og ved prepreg-metoden. Små og mindre emner i store seriestørrelser fremstilles traditionelt ved presning enten ud fra flydende
plastharpiks eller ud fra et prepreg-produkt. Plane prepregprodukter baseret på glasfibre og umættet polyester benævnes ofte sheet moulding compounds med forkortelsen SMC. Dej-agtige,
forimprægnerede produkter benævnes DMC (for dough moulding compound) eller BMC (for bulk moulding compound). Disse forkortelser er kendte i branchen. Med de nævnte metoder kan der kun
fremstilles et enkelt emne ad gange, da de bygger på støbning i et formværktøj. Pultrudering, kontinuerlig laminering og kontinuerlig vikling er kontinuerlige metoder til fremstilling af rør, plader og profiler med
ensartet tværsnit.
3.3 Sandwichkonstruktioner
Ofte anvendes hærdeplastbaserede fiberkompositter til yderskaller i sandwichkonstruktioner. Princippet i sandwichkonstruktioner er, at to forholdsvis tynde yderskaller af stærkt og stift materiale holdes
sammen af en forholdsvis tyk, men let kerne med stor forskydningsstyrke. Under forudsætning af, at der er tilstrækkeligt god binding mellem skallerne og kernen, bliver forholdet mellem konstruktionens
bøjestivhed og dens vægt meget stor, idet stivheden principielt stiger med tredje potens af tykkelsen. Man får således samme stive virkning, som kendes fra I-bjælker fx af stål. Sandwichprincippet er
illustreret på figur 3.
Sandwichelementer indgår i mange af de almindeligt forekommende kompositprodukter. Det gælder fx i mange vindmøllevinger og i lystbåde.
I figur 3 er den typiske opbygning og virkemåde af et sandwichelement vist.
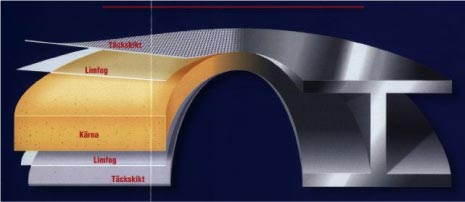
Figur 3 Sandwichprincippet (Efter DIAB)
3.4 Udtjente produkter af kompositmaterialer
Anvendelsen af plastbaserede fiberkompositter både med og uden sandwichelementer er i stærk stigning i disse år. Disse produkter vil efter endt levetid skulle bortskaffes og kan på sigt udgøre et
affaldsproblem, hvis ikke der udvikles og sikres hensigtsmæssige bortskaffelses metoder. Når produkter af hærdeplast skal genanvendes, må man, i modsætning til termoplast som ganske enkelt kan smeltes,
ty til andre principper i form af forbrænding eller mekanisk neddeling for at omdanne sådanne emner til fraktioner, der kan genanvendes.
4 Forbehandlingsmetoder
Dette projekt er gennemført for at skabe grundlag for tekniske løsninger til forbehandling af affald af fiberforstærketkompositmateriale, således at det fremkomne regenerat muliggør fremstilling af nye
kvalitetsprodukter. Tabel 1 er en oversigt over de kendte metoder til at behandle eller anvende affald af plastbaserede fiberkompositter.
Forbrænding behandles i dette projekt under betegnelsen termisk forbehandling, idet organiske materiale herunder plastmaterialer ved forbrænding - som kemisk set er en oxidation - nedbrydes til luftformige
(og sommetider også til flydende) stoffer, som i princippet kan opsamles og viderebehandles. Såfremt affaldet indeholder uorganisk materiale, vil dette efter forbrænding forekomme som en rest, som
ligeledes kan behandles videre eller eventuelt anvendes direkte. Kemisk nedbrydning er også en mulighed, denne metode har bl.a. været anvendt til forbehandling af uhærdet glasfiberforstærket phenolplast.
Overordnet set har den termiske forbehandling de umiddelbare fordele, at de mange forskellige typer af kompositmaterialer baseret på forskellige plastmaterialer efter forbehandling vil bestå af en forholdsvis
ensartet glasfraktion, som lettere kan samles i store mængder. Afhængig af størrelsen af den konkrete forbrændingsovn vil det ved den termiske forbehandling i mange tilfælde kun være nødvendigt med en
begrænset neddeling af de større affaldsemner inden forbehandling. Omvendt kræver den termiske forbehandling typisk store investeringer i form af dyre ovne eller lignende.
Den mekaniske forbehandling vil ikke nødvendigvis kræve så avanceret og investeringstungt neddelingsudstyr, men der kan være stor slitage på udstyret under neddelingen. Det resulterende neddelte
kompositmateriale vil typisk bestå af en kompleks blanding af forskellige plastmaterialer, som det sandsynligvis kan være svært at fremstille i en ensartet kvalitet og finde genanvendelsesmuligheder for, med
mindre der foretages en sortering. Omvendt, hvis der på et marked kan findes specifikke genanvendelsesmuligheder for det neddelte kompositmateriale, kan den mekaniske forbehandling have sine fordele.
Tabel 1. Metoder til bortskaffelse af kompositaffald
Mekanisk genvinding behandles i dette projekt under betegnelsen mekanisk forbehandling. Der er ganske enkelt tale om - eventuelt gennem flere procestrin - at neddele de kasserede emner til mindre dele
Klik her for at se Tabel 1.
5 Eksisterende viden og erfaringer
5.1 Status fra litteraturen vedr. termisk forbehandling
5.2 Status fra litteraturen vedr. mekanisk forbehandling
5.1 Status fra litteraturen vedr. termisk forbehandling
På grundlag af de anførte referencer /3/, /4/, /5/, /7/, /8/, /10/, /12/ kan der gives følgende koncentrerede sammenfatning af de umiddelbart foreliggende erfaringer med anvendelse af termisk forbehandlet
regenerat.
- Ved forbrænding er det muligt at udnytte den energi, der frigøres, når organisk materiale forbrændes. Ved forbrænding af plast frigøres stort set samme mængde energi, som indeholdes i den mængde
petrokemiske stoffer, som plasten er fremstillet af. Den nedre brændværdi af hærdet umættet polyester er 10 - 30 MJ/kg afhængigt af indholdet af uorganiske additiver /4/ og /9/. Genvundne fibre af
uorganiske materialer fx glas kan genanvendes som fiberforstærkning i termoplast og i hærdeplast. Ved forbrænding kan der således både ske materialegenvinding og energigenvinding
- Efter forbrænding af store komponenter af glasfiberforstærket umættet polyester og epoxyplast kan fiberprodukter i form af måtte, væv og roving separeres
- Pyrolyse af neddelte komponenter og produktionsaffald kan udføres i roterovne eller ved fluidised bed, hvor fibre efterfølgende kan separeres. Metoden kan også anvendes til sandwichkonstruktioner
med kerne af celleplast, til malede komponenter mv.
- Separerede fibre kan via opslemning forarbejdes til filt
- Separerede fibre kan tilsættes til DMC, i sammenligning med et materiale med 18% glasfibre af 6 mm længde opnås,
- ved substitution med 50% regenererede fibre opnås uændret træk- og bøjestyrke
- ved 100% substitution med regenererede fibre opnås uændret træk- og bøjemodul
- ved 50% tilsætning af regenererede fibre reduceres slagsejheden med 25%
- effekten af re-sizing er ringe
- Regenererede glasfibres egenskaber:
- ved forbrænding ved 450°C reduceres trækstyrken til 50%; med stigende temperatur reduceres styrken yderligere - ved 650°C til 10%
- E-modul er uforandret
- renhed 80% (fremmede partikler) , i sammenligning med nye glasfibre
- middellængde (vægtbaseret) af fibre: 3 - 5 mm
- fibrene krøller eller er dunet
- Genanvendelse af carbonfibre kan udføres på samme måde som glasfibre; trækstyrken reduceres dog ikke så meget - kun med 20% ved 450°C
- Eksempler på færdigprodukter af BMC/DMC med regenererede glasfibre er el-komponenter
I tabel 2 er vist eksempler på genanvendelse af regenererede glasfibre i forskellige produkter. Tilsætning af fibrene giver en forstærkning af de resulterende materialeegenskaber. Der er også anført forslag til
mulige anvendelser.
Tabel 2. Eksempler på og forslag til genanvendelse af termisk forbehandlede hærdeplastbaserede
fiberkompositter
Anvendelseseksempler |
Bemærkninger |
Referencer |
Tilsætning til cement-, brugsglas- og glasfiberfremstilling |
Der har været kontakt til cementindustri og til glasfiberfremstillere, dog uden
resultat |
/3/ |
Tilsætning til termoplast ved kompoundering eller tilsætning i proces |
Anvendelsen er vist ved tilsætning til polypropylen (PP) efter forbehandling af
fibrene |
/3/ og /4/ |
Tilsætning til hærdeplast fx til BMC/DMC |
Anvendelsen er vist ved fremstilling af elkomponenter |
/3/ og /4/ |
Tilsætning til fibercement |
Forslag |
Projektgruppen |
Fremstilling af isoleringsbats |
Forslag |
Projektgruppen |
Til forstærkning af tagpap |
Forslag |
Projektgruppen |
Termisk isolering (som mineraluld) |
Forslag |
Projektgruppen |
5.2 Status fra litteraturen vedr. mekanisk forbehandling
På grundlag af de anførte referencer /3/, /5/, /6/, /8/, /10/ kan der gives følgende koncentrerede sammenfatning af de umiddelbart foreliggende erfaringer med anvendelse af mekanisk forbehandlet regenerat,
- Nedknusning/formaling udføres inden for et bredt fraktionsområde fra store flager til pulver af polyester, epoxyplast og phenolplast forstærket med glasfiber eller carbonfiber
- Genanvendelse af regenerater i hærdeplast:
- ved sprøjteoplægning; særligt udstyr er udviklet
- mekanisk blandet i polyester ved håndoplægning
- tør tilsætning ved centrifugalstøbning
- ved vakuuminjektion som kernemateriale i sandwichkonstruktioner
- som kernemateriale ved fremstilling af GUP-rør
- Undersøgelser af mekaniske egenskaber som bøjestyrke, trækstyrke og E-modul foreligger i sammenligning med nye materialers egenskaber, de viser, at der opnås bedre egenskaber end det
uforstærkede plastmateriale, og der opnås ca. 80% af egenskaberne i forhold til tilsætning af nye fibre
- Eksempler på anvendelser: bådskrog, jernbanesveller, SMC- og BMC-produkter, tanke, rør
- Genanvendelse i termoplast behandlet med forskellige silaner:
- som funktionelt fyldstof i polypropylen (PP)
- forarbejdes ved sprøjtestøbning og ekstrudering
- sammenlignende undersøgelser af bl.a. mekaniske egenskaber
- kompoundering i dobbeltsnekkeekstruder kan udføres med knust hærdeplast; der sker udtørring; tilsætning af hjælpestoffer til overfladebehandling; tilsætning af matrix-materialer enten
hærdeplast, termoplast eller elastomerer; resultat i form af granulat, dej eller profiler
- Eksempler på anvendelser: sprøjtestøbte rammer af PP til montage af elkomponenter; pressede interiørdele af PP til biler
I tabel 3 er vist eksempler på tilsætning af neddelt/kværnet kompositmateriale til produkter, samt forslag til mulige anvendelser.
Tabel 3. Eksempler på og forslag til genanvendelse af mekanisk forbehandlede hærdeplastbaserede fiberkompositter
Anvendelseseksempler |
Bemærkninger |
Referencer |
Tilsætning til hærdeplast ved sprøjteoplægning |
Fremstilling af både hos værftet Ryds i Sverige |
Sicom/Ryds, Sverige /10/ |
Som kerne i sandwichkonstruktioner eller som tilsætningsmateriale |
Fremstilling af homogene plader og sandwichplader bl.a. til lyddæmpning |
Sicomp, Sverige /10/ |
Jernbanesveller |
|
TieTek, USA /10/ |
Tanke og rør til fx afløb |
|
BiaMiljø AB, Sverige /10/ |
SMC/BMC |
Forskellige artikler til el, afdækning mm. |
Producenter i EU /5/ |
Tilsætning til pultruderede profiler |
|
Projektgruppe |
Som funktionelt fyld i teglsten |
Orienterende forsøg er udført, se kap. 7 |
Teknologisk Institut |
Tilsætning til vejbelægning |
Forslag |
Projektgruppe |
Tilsætning til gulvebelægninger og til fugemasser |
Forslag |
Projektgruppe |
6 Termisk forbehandling
6.1 Første forsøgsserie
6.1.1 Fremgangsmåde
6.1.2 Eksperimentelt
6.1.3 Diskussion
6.1.4 Konklusion
6.2 Anden forsøgsserie
6.2.1 Fremgangsmåde
6.2.2 Eksperimentelt
6.2.3 Diskussion
6.2.4 Konklusion
6.3 Tredje forsøgsserie
6.3.1 Fremgangsmåde
6.3.2 Eksperimentelt
6.3.3 Diskussion
6.3.4 Konklusion
6.4 Demonstrationsemner
6.4.1 Fremstilling af demonstrationsemner
6.4.2 Konklusion
6.5 Konklusion af forsøg med termisk forbehandling
Ved termisk forbehandling fortages enten opvarmning til flere hundrede grader i en inaktiv (dvs. oxygenfri) atmosfære med nitrogen (pyrolyse) eller forbrænding i en atmosfære med oxygen. Der er i dette
projekt anvendt følgende tre metoder:
- Forbrænding i muffelovn ved trinvis opvarmning i atmosfærisk luft til mindst 450°C. Under opvarmningen sker der en termisk/oxidativ spaltning (nedbrydning) af plasten og af andre organiske
forbindelser under udvikling af en række luftformige nedbrydningsprodukter (afgasning). Denne gasdannelse medfører, at den atmosfærisk luft i ovnkammeret efterhånden fortrænges, således at der i et
vist tidsrum ikke længere er oxygen til stede. Når afgasningen er tilendebragt, åbnes for tilgang af atmosfærisk luft, og resterende organisk materiale brændes af ved reaktion med oxygen
- Ved pyrolyse foretages opvarmning til høj temperatur i inaktiv atmosfære. Efter endt pyrolyse ved mindst 400°C foreligger glasfibre og andet uorganisk materiale med en belægning af carbon
- Ved en 2-trins metode hvor pyrolyse og forbrænding kombineres med energigenvinding. I første trin sker der en afgasning af organiske forbindelser i inaktiv atmosfære af nitrogen for at undgå
eksplosionsfare, efter afgasning tilføres atmosfærisk luft, og det resterende carbon brændes af. Anlægget hos ReFiber ApS kan afbrænde større mængder kompositmateriale som f.eks. møllevinger.
Der henvises til bilag C, hvor de i projektet udførte afbrændinger er rapporteret
Der er blevet udført tre forsøgsserier med termisk forbehandling.
I første forsøgsserie blev der udført forsøg med termisk forbehandling af små prøveemner ved to forskellige temperaturer i muffelovn og ved pyrolyse ved flere temperaturer, for at få et første indtryk af, i
hvilket omfang forbehandling påvirker glasfibres egenskaber, og om der kan opnås tilfredsstillende vedhæftning mellem termisk forbehandlede glasfibre og henholdsvis polyesterharpiks (UP) og epoxyplast
(EP). Der blev fremstillet prøveplader, som der efterfølgende blev foretaget prøvning af.
I anden forsøgsserie blev der på grundlag af erfaringerne fra første serie udført forbehandling på noget større emner ved metoden der kombinerer pyrolyse og forbrænding. Der blev af de termisk
forbehandlede glasfibre (regeneratet) fremstillet nye prøveplader, som der efterfølgende blev foretaget prøvning af.
I tredje forsøgsserie blev der på glasfibre, som var termisk forbehandlet ved metoden der kombinerer pyrolyse og forbrænding, udført forsøg med resizing med silan. Der blev med resizede fibre og ikke
resizede fibre fremstillet prøveplader, som efterfølgende blev foretaget prøvning af.
Afslutningsvis blev der fremstillet tre forskellige demonstrationsemner, for at afprøve i praksis hvordan det er at arbejde med termisk forbehandlede glasfibre.
6.1 Første forsøgsserie
I første forsøgsserie blev der udført forsøg med pyrolyse udført hos Kommunekemi a/s og forsøg med forbrænding i muffelovn hos Teknologisk Institut. Forsøg med fremstilling af prøveplader med
regenererede glasfibre og henholdsvis epoxyplast og polyester, blev udført hos bådværftet KMT - Nord. Der blev foretaget karakterisering af glasfibre og af prøveemner, som blev udskåret af de
fremstillede prøveplader.
Prøveemnerne er udskæringer af glasfiberforstærket polyester og epoxyplast fra produktionen hos EM Fiberglas A/S, hos Jupiter Plast A/S og hos Vestas Wind Systems A/S.
6.1.1 Fremgangsmåde
- Pyrolyse af materialeprøver ved 400 - 600°C med intervaller på 50°C og
- forbrænding af materialeprøver ved 450°C og ved 550°C
- Karakterisering af glasfibrenes overflade ved skanningelektronmikroskopi (SEM)
- Grundstofanalyse af glasfibre ved energidispersiv røntgen-analyse (EDX)
- Bestemmelse af glasfibres brudstyrke
- Fremstilling af prøveplader ved håndoplægning med regenereret fibre og henholdsvis polyester og epoxyplast
- Bestemmelse af styrkeegenskaber og glasindhold på disse prøveplader
- Karakterisering af regeneratpladernes tværsnit ved penetreringsvæske og skanningelektronmikroskopi (SEM)
6.1.2 Eksperimentelt
6.1.2.1 Pyrolyse
På Kommunekemi blev der gennemført forsøg i laboratorieskala med pyrolyse af prøveplader af polyester ved temperatur fra 400°C til 600°C med intervaller på 50°C. Forsøgsrapporten fra Kommunekemi er
vedlagt som bilag A.
6.1.2.2 Forbrænding
Hos Teknologisk Institut blev prøveplader polyester og epoxyharpix med dimensionerne ca. 100 × 100 × 5 mm forasket i en ovn med oxygen til stede. Fra en temperatur på ca. 20°C blev pladerne i løbet af
6 timer opvarmet trinvist til henholdsvis 450°C og 550°C, hvorefter opvarmningen blev afbrudt med efterfølgende naturlig afkøling.
De forbrændte prøveplader består af glasfibermåtte, dvs. fiberbundter med en længde på ca. 50 mm jævnt fordelt i planet, rovingvæv, dvs. lange fiberbundter vævet i to på hinanden vinkelrette retninger, og
uorganiske tilsætningsstoffer i form af brandhæmmere (aluminiumtrihydrat) og farvepigmenter (titanoxid) mv. De forbrændte plader fremstår med en del partikler og støv.
6.1.2.3 Prøvning af glasfibre
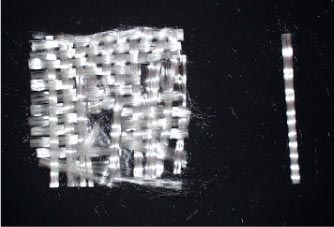
Figur 4 Rovingvæv efter forbrænding i muffelovn, til højre ses fiberbundt til trækprøvning
6.1.2.3.1 Overfladekarakterisering af glasfibre ved SEM
SEM-optagelserne blev udført på nye glasfibre (reference), og på glasfibre, der er blevet forbehandlet i muffelovn ved 450°C og ved 550°C, se figur 1, 2 og 3 i bilag B. Der ses urenheder på fibrenes
overflader; men det kan ikke ud fra disse billeder afgøres, om glasfibrene er blevet beskadiget ved den termiske forbehandling.
6.1.2.3.2 Grundstofanalyse af glasfibre
Grundstofanalysen blev udført for at konstatere eventuelle ændringer af glasfibrenes kemiske sammensætning efter termisk forbehandling i muffelovn i oxygenholdig atmosfære ved 450°C og ved 550°C. Som
det fremgår af billederne i figur 7 og 8 i bilag B, kan der efter forbehandling ved 550°C kun konstateres en øget mængde oxygen og carbon på fibrene.
Figur 9 i bilag B viser analysen af glasfibre efter pyrolyse ved 450°C. Der kan ikke konstateres nogen væsentlig ændring. Tilstedeværelsen af en øget mængde carbon, der ses som et sort lag på fibrene,
fremgår tydeligt af analysespektret (top C).
6.1.2.3.3 Styrkebestemmelse på glasfibre
Påvirkningen af fibrenes styrkeegenskaber efter termiske forbehandling i muffelovn blev undersøgt ved trækprøvning af plane fiberbundter, som er taget fra rovingvævet. Det er antaget, at der er det samme
antal filamenter i hvert fiberbundt fiberbundets bredde er 8 mm, trækhastighed 10 mm/min.
Tabel 4. Brudstyrke bestemt ved trækprøvning af nye og regenererede fiber efter termisk forbehandling i muffelovn og ved pyrolyse
(I parentes er anført den statistiske standardafvigelse på middelværdierne)
Glasfibre |
Brudstyrke N |
% af referencens værdi |
Nye fibre fra EM Fiberglas (reference) |
429 (109) 1) |
- |
Efter forbrænding ved 450°C (UP-emne fra EM Fiberglas) |
127 (14) 1) |
30 |
Efter forbrænding ved 550°C (UP-emne fra EM Fiberglas) |
94 (16) 1) |
22 |
Efter pyrolyse ved 450°C (UP-emne fra EM Fiberglas) |
302 (147) 2) |
70 |
Efter pyrolyse ved 600°C (UP-emne fra EM Fiberglas) |
216 (54) 3) |
50 |
1) Middelværdi af 5 enkeltmålinger.
2) Middelværdi af 3 enkeltmålinger.
3) Middelværdi af 6 enkeltmålinger.
Tabel 5 indeholder supplerende målinger af glasfibres brudstyrke efter termisk behandling ved kombineret pyrolyse og afbrænding udført hos ReFiber ApS.
Tabel 5. Brudstyrke bestemt ved trækprøvning af nye og regenererede fiber efter forbrænding hos ReFiber
(I parentes er anført den statistiske standardafvigelse på middelværdierne)
Glasfibre |
Brudstyrke N |
% af referencens værdi |
Nye fibre fra EM Fiberglas (reference) |
502 (51) 1) |
- |
Nye fibre fra Vestas (reference) |
372 (26) 1) |
- |
Efter ReFibermetoden 450°C |
forsøg nr. 2.1 (UP-emne fra EM Fiberglas) |
190 (30) 2) |
38 |
forsøg nr. 2.2 (UP-emne fra EM Fiberglas) |
196 (29) 2) |
39 |
forsøg nr. 2.3 (UP-emne fra EM Fiberglas) |
154 (11) 1) |
31 |
Vestas-vinge (EP-emne) |
152 (29) 1) |
41 |
1) Middelværdi af 5 enkeltmålinger.
2) Middelværdi af 6 enkeltmålinger.
Antallet af enkeltmålinger varierer, fordi nogle resultater er kasseret pga. brud ved eller glidning i indspændingen.
Det kan ikke med disse resultater afgøres om, der væsentligt forskel i påvirkningen af glasfibrene mellem de tre metoder til termisk forbehandling. Fibrene der indgår i de leverede emner er således
forskellige. Reduktionen i glasfibrenes brudstyrke efter forbrænding er noget større end rapporteret i reference /4/. I den er der anført en reduktion på 50% efter behandling ved 450°C. I samme reference
anføres også, at fibrenes styrke udtrykt ved Weibull-modulet reduceres til 45% ved 450°C og til 18% ved 550°C. (Weibull-modulet er en statistisk størrelse, som udtrykker spredningen på styrkemålinger:
jo højere Weibullmodul - jo mindre spredning).
Ved håndtering af det termisk forbehandlede regenerat under prøvningen blev der observeret en tydelig forøgelse af sprødheden i forhold til nye fibre, idet de forbehandlede fibre skulle håndteres med
forsigtighed, for at de ikke skulle knække.
6.1.2.4 Fremstilling af prøveplader af regenerat
Af regenerat, der er termisk forbehandlet i muffelovn ved 450°C og ved 550°C, blev der hos KMT - Nord ved håndoplægning fremstillet fire prøveplader ved imprægnering med henholdsvis polyester og
epoxyplast, uden at regeneratet forud var blevet renset for andet uorganisk materiale. Der lå således et tyndt lag af uforbrændt materiale af pigment mv. oven på fibrene og noget mellem fibrene.
Regeneratet blev anbragt på en plastfolie, og der blev tilført polyester henholdsvis epoxyplast. Med en almindelig lamineringsrulle (en aluminiumsrulle med langsgående riller) blev regeneratet imprægneret.
Det var nødvendigt at tilsætte relativt meget polyester/epoxyplast for at opnå befugtning, foruden at der skulle rulles intensivt. Det medførte, at den lagvise opbygning af glasfibermåtte og rovingvæv delvist
blev nedbrudt. Ud fra en visuelt bedømmelse blev der opnået en forholdsvis god befugtning af glasfibre og pigmenter.
6.1.2.5 Prøvning af prøveplader af regenerat
6.1.2.5.1 Styrkeegenskaber og glasindhold
Bøjebrudstyrke, elasticitetsmodul ved bøjning (E-modul) og glasindhold blev bestemt ved standardiseret prøvning på prøveemner udskåret prøveplader jf. 6.1.2.4.
Metode: ISO 178.
Deformationshastighed: 6 mm/min ved brudstyrkebestemmelse og 2 mm/min ved E-modul-bestemmelse.
Understøtningsafstand: 16 gange godstykkelsen, dvs. varierende afhængigt af godstykkelsen.
Glasindholdet blev bestemt som glødetab (glasfibre og andre uorganiske stoffer) i henhold til ISO 1172 og er angivet i vægt-%.
Tabel 6. Mekaniske egenskaber og glasindhold (bestemt ved forbrænding ved 625°C) af kompositmaterialer før og efter
termisk forbehandling og genanvendelse.
(I parentes er anført den statistiske standardafvigelse på middelværdierne)
Prøveplader |
Bøjestyrke MPa |
% af referencens værdi 5) |
E-modul MPa |
% af referencens værdi 5) |
vægt-% glasfibre |
Materialeprøve (reference) 1) 2) |
249 (14) |
- |
13571 (690) |
- |
34 |
Regenerat 450°C, UP 3) |
161 (20) |
65/43 |
12314 (1786) |
91/61 |
47 |
Regenerat 450°C, EP 4) |
146 (19) |
59/47 |
11727
(337) |
86/69 |
42 |
1) Referenceprøven er et GUP-emne fra EM Fiberglas.
2) 6 emner; understøtningsafstand 78 mm.
3) 4 emner; understøtningsafstand 84 mm og 106 mm.
4) 3 emner; understøtningsfstand 84 mm og 106 mm.
5) Første tal angiver egenskabsværdien i forhold til referencen, andet tal er korrigeret for volumenandelen af glasfibre, idet 34 vægt-% ≈ 20 volumen-%, 42 vægt-% ≈ 25 volumen-% og 47 vægt-% ≈ 30 volumen-%.
De første resultater viser, at bøjestyrken reducers til 60-65% og E-modulet til 85-90% af referenceprøvens værdier.
6.1.2.5.2 Poresøgning ved hjælp af penetreringsvæske
Prøveemnernes tværsnit blev undersøgt ved hjælp af penetreringsvæske. Der blev observeret mindre porøsiteter mest udtalt på pladerne med polyester. Prøvepladerne jf. 6.1.2.4 varierede en del i
godstykkelse. Inden for et område på ca. 80 × 80 mm var godstykkelsen dog nogenlunde ensartet ca. 5 mm, prøveemnerne er udskåret inden for dette område.
6.1.2.5.3 SEM-karakterisering
For at undersøge strukturen i prøvepladerne jf. 6.1.2.4 blev pladerne savet igennem og udvalgte tværsnit blev undersøgt ved hjælp af SEM. Optagelserne viser, at der er opnået en hvis homogenitet, men
også at der er områder, hvor fibrene ikke er blevet befugtet, samt at der er en del partikler (farvepigment) til stede.
SEM-optagelserne er vist i figur 4 og 5 i bilag B.
6.1.3 Diskussion
Bestemmelsen af glasfibrenes brudstyrke efter termisk behandling skal betragtes som orienterende, idet det er ganske vanskeligt at håndtere fibrene, uden at der opstår mikroskader i overfladen. Det skyldes,
at sizingen og andre stoffer ikke længere er til stede. Fibrene er således meget sprøde og er ikke sammenhængende i bundter i modsætning til nye rovingvæv.
Det er vist, at der på enkel vis ved bearbejdning med rulle opnås befugtning af fibrene. Det forstyrres dog en del af, at det er vanskeligt at befugte farvepigmenterne, som både ligger som et lag på fibrene og
mellem de enkelte fiberbundter og mellem fiberlagene (måtte og rovingvæv).
Reduktion af bøjestyrken er ikke særligt dramatisk, når man tager den meget enkle fremstillingsmetoden i betragtning. Reduktion af E-modulerne er beskeden, når der sammenlignes med referenceværdien
uden omregning af volumenandele glasfibre. Andre undersøgelser har da også vist, at glasfibres E-modul ikke ændres på grund af termisk forbehandling /4/.
SEM-optagelserne af fibre ved dels forbehandling i muffelovn ved 450°C og ved 550°C og dels ved pyrolyse viser ingen forskelle ved sammenligning med nye fibre. Ved grundstof- analyse af de samme
fibre kunne der ikke konstateres forskelle ud over tilstedeværelsen af carbon på de fibre, der er forbehandlet ved pyrolyse.
SEM-optagelserne af håndoplagte plader viser, at der er beskeden vedhæftning både mellem polyester og glasfibre og mellem epoxyplast og glasfibre. Desuden er det tydeligt, at der er mange partikler af
forskellige størrelser, som ikke er befugtet, samt at der er en del knækkede glasfibre.
6.1.4 Konklusion
Den umiddelbare vurdering efter første forsøgsseries resultater er, at der dels kan opnås befugtning af og vedhæftning til regenererede glasfibre med både polyester og epoxyplast, dels at der kan opnås
mekaniske egenskaber på et noget reduceret niveau. Glasfibrenes brudstyrke reduceres væsentligt ved termisk forbehandling. Denne reduktion vurderes at skyldes temperaturen under forbehandling snarere
end hvilken forbehandlingsmetode, der har været benyttet.
Ud fra en visuel vurdering er det konstateret, at der både med polyester og med epoxyplast kan opnås vedhæftning til glasfibre, som er behandlet ved pyrolyse. Da der kun kan foretages ren pyrolyse af
forholdsvis små prøveemner jf. bilag A, anvendes denne metode ikke i det videre projektforløb.
6.2 Anden forsøgsserie
Anden forsøgsserie blev udført på to skiveformede udskæringer af glasfiberforstærket polyester med en diameter på ca. 400 mm fra vindmøllehuse, der er fremstillet hos EM Fiberglas A/S. Forsøg med
fremstilling af nye prøveplader med regenererede glasfibre blev udført hos bådværftet KMT - Nord.
Materialeprøverne blev termisk forbehandlet hos ReFiber ApS.
6.2.1 Fremgangsmåde
- Forbehandling ved kombineret pyrolyse og forbrænding
- Fremstilling af nye prøveplader af regenererede glasfibre
- Prøvning af prøveplader af regenerat
6.2.2 Eksperimentelt
6.2.2.1 Forbehandling
I anden forsøgsserie blev forbehandlingen af to runde udskæringer fra EM Fiberglas A/S udført hos ReFiber ApS efter følgende proces:
- Kombineret pyrolyse ved opvarmning til 450°C eller 490°C og forbrænding af carbon i atmosfærisk luft ved 450°C.
Forsøgsrapport fra ReFiber ApS indgår som bilag C.
6.2.2.2 Fremstilling af prøveplader af regenerat
Efter forbehandlingen blev der af de tilbageværende glasfibre, regeneratet, fremstillet nye kompositemner ved vakuum-injektion med henholdsvis polyester og epoxyplast, efter at den ene halvdel af hver af
skiverne var blevet forsøgt renset for støv ved støvsugning gennem et net for at holde fibrene tilbage. Injektionen blev udført hos bådværftet KMT - Nord, og egenskaberne af disse nye laminater blev
bestemt ved prøvning på Teknologisk Institut.
6.2.2.3 Prøvning af prøveplader af regenerat
6.2.2.3.1 Styrkeegenskaber og glasindhold
Bøjebrudstyrke, elasticitetsmodul ved bøjning (E-modul) og glasindhold blev bestemt ved standardiseret prøvning.
Bøjebrudstyrke og E-modul:
Metode: ISO 178.
Antal emner: 6.
Deformationshastighed: 1-2 mm/min både ved bestemmelse af brudstyrke og E-modul.
Understøtningsafstand: 16 gange godstykkelsen, dvs. varierende afhængigt af godstykkelsen.
Glasindholdet blev bestemt som glødetabet (summen af indholdet af glasfibre og af andre uorganiske stoffer) efter ISO 1172 og er angivet i vægt-%.
Tabel 7. Mekaniske egenskaber af kompositmaterialer før og efter termisk forbehandling ved forbrænding og genanvendelse baseret på ikke renset regenerat
(I parentes er anført den statistiske standardafvigelse på middelværdierne)
Prøveplader |
Bøjestyrke MPa |
% af referencens værdi 2) |
E-modul MPa |
% af referencens værdi 2) |
Glasindhold vægt-% |
Materialeprøve (reference) 1) |
249 (14) |
- |
13571
(690) |
- |
34 |
Polyesterlaminat med regenererede glasfibre 450°C |
192 (26) |
77/38 |
11805 (1135) |
87/42 |
59 |
Epoxylaminat med regenererede glasfibre 450°C |
156 (17) |
63/34 |
10463 (917) |
77/42 |
56 |
1 Referenceprøven er et GUP-emne fra EM Fiberglas.
2) Første tal angiver egenskabsværdien i forhold til referencens; andet tal er korrigeret i forhold til volumenandelen af glasfibre, idet 34 vægt-% ≈ 20 volumen-%, 56 vægt-% ≈ 37 volumen-%, og 59 vægt-% ≈ 41 volumen-%.
Tabel 8. Mekaniske egenskaber af kompositmaterialer før og efter termisk forbehandling ved forbrænding og
genanvendelse baseret på renset regenerat
(I parentes er anført den statistiske standardafvigelse på middelværdierne)
Prøveplader |
Bøjestyrke MPa |
% af referencens værdi 2) |
E-modul MPa |
% af referencens værdi 2) |
Glasindhold vægt-% |
Materialeprøve (reference) 1) |
249 (14) |
- |
13571 (690) |
- |
34 |
Polyesterlaminat med regenererede glasfibre 450°C |
150 (19) |
60/29 |
11137 (1158) |
82/40 |
59 |
Epoxylaminat med regenererede glasfibre 450°C |
188 (25) |
75/41 |
10704 (1631) |
79/43 |
56 |
1) Referenceprøven er et GUP-emne fra EM Fiberglas.
2) Første tal angiver egenskabsværdien i forhold til referencens; andet tal er korrigeret i forhold til volumenandelen af glasfibre, idet 34 vægt-% ≈ 20 volumen-%, 56 vægt-% ≈ 37 volumen-%, og 59 vægt-% ≈ 41 volumen-%.
Der kan ikke konstateres nogen entydig effekt af, at glasfibrene er blevet renset ved støvsugning. Tværtimod er der en modsat rettet tendens for prøver af polyester og epoxyplast mht. bøjestyrke,
E-modulernes variation ligger inden for spredningen.
6.2.2.3.2 Interlaminar forskydningsstyrke
Med udgangspunkt i prøvningsstandarden DS/EN 2377 blev den tilsyneladende, interlaminare forskydningsstyrke bestemt ved prøvning. Prøvelegemernes dimensioner afviger imidlertid noget fra dem, som
er specificeret i standarden, hvorfor de registrerede værdier kun må betragtes som vejledende.
De anførte middelværdier er baseret på 5 eller 6 enkeltværdier.
Tabel 9. Interlaminar forskydningsstyrke af kompositmaterialer før og efter termisk forbehandling ved
forbrænding og genanvendelse baseret på ikke renset regenerat
(I parentes er anført den statistiske standardafvigelse på middelværdierne)
Prøveplader |
Interlaminar forskydningsstyrke MPa |
% af referencens værdi |
Brudtype |
Materialeprøve (reference) 1) |
32,7 (9,9) |
- |
Trækbrud samtidigt med forskydningsbrud |
Polyesterlaminat med regenererede glasfibre 450°C |
13,9 (2,1) |
42 |
Både flerlagsforskydningsbrud og trækbrud samtidigt med forskydningsbrud forekommer |
Epoxylaminat med regenererede glasfibre 450°C |
26,9 (2,0) |
82 |
Trækbrud samtidigt med forskydningsbrud |
1) GUP-emne fra EM Glasfiber.
Tabel 10. Interlaminar forskydningsstyrke af kompositmaterialer før og efter termisk forbehandling ved
forbrænding og genanvendelse baseret på renset regenerat
(I parentes er anført den statistiske standardafvigelse på middelværdierne)
Prøveplader |
Interlaminar forskydningsstyrke MPa |
% af referencens værdi |
Brudtype |
Materialeprøve (reference) 1) |
32,7 (9,9) |
- |
Trækbrud samtidigt med forskydningsbrud |
Polyesterlaminat med regenererede glasfibre 450°C |
13,0 (2,5) |
40 |
Trækbrud samtidigt med forskydningsbrud |
Epoxylaminat med regenererede glasfibre 450°C |
19,5 (2,7) |
60 |
Både flerlagsforskydningsbrud og trækbrud samtidigt med forskydningsbrud forekommer |
1) GUP-emne fra EM Glasfiber.
Resultaterne af disse målinger viser, at der ikke er nogen effekt af rensning ved støvsugning af prøveemner af polyester, derimod er der en tendens til en noget lavere værdi for rensede prøveemner af
epoxyplast.
6.2.2.3.3 Vandoptagelse
Med udgangspunkt i prøvningsstandarden ISO 62 blev vandoptagelsen bestemt eksperimentelt på ikke rensede prøver. Prøvelegemernes dimensioner afviger imidlertid fra dem, som er specificeret i
standarden. Derfor må de registrerede mængder optaget vand kun betragtes som vejledende. Eksponeringen blev fortsat ud over det ene døgn, som er specificeret i standarden.
Vandoptagelsesdataene ved eksponering op til 28 døgn er vist på figurerne 5 - 7. For at gøre vandoptagelsesdataene sammenlignelige, er dataene for hvert enkelt prøvelegeme relateret til prøvelegemets
overfladeareal. Prøveemnerne er lige brede og har næsten samme godstykkelse. Bemærk, at enhederne på ordinataksen er forskellige for polyester- og epoxylaminaterne. Først ved mætning giver det
mening at se på den procentvise optagelse. Efter endt eksponering blev prøverne afkølet til 23°C i vand, inden mekanisk prøvning blev foretaget.
Resultaterne kan således give en første indikation om, at de regenererede glasfibre vil kunne bruges i produkter, der kommer i kontakt med vand.
6.2.2.3.4 Styrkeegenskaber
Bøjebrudstyrke, elasticitetsmodul ved bøjning (E-modul) blev bestemt ved standardiseret prøvning.
Bøjebrudstyrke og E-modul:
Metode: ISO 178.
Antal emner: 5.
Deformationshastighed: 2 mm/min både ved brudstyrkebestemmelse og ved E-modulbestemmelse.
Understøtningsafstand: 16 gange godstykkelsen, dvs. varierende afhængigt af godstykkelsen.
Glasindholdet antages at være af samme størrelsesorden, som bestemt under punkt 6.2.2.3.1.
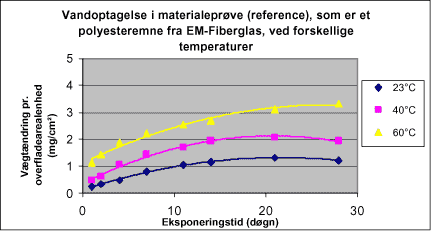
Figur 5 Vandoptagelse i materialeprøve (reference) ved 23°C, 40°C og 60°C
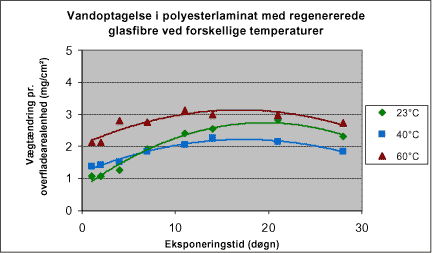
Figur 6 Vandoptagelse i polyesterlaminat med regenererede glasfibre ved 23°C, 40°C og 60°C
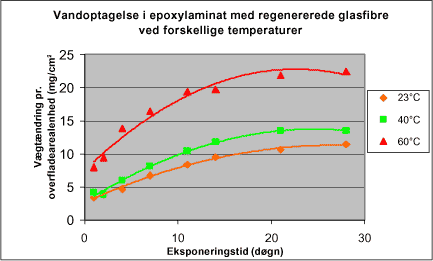
Figur 7 Vandoptagelse i epoxylaminat med regenererede glasfibre ved 23°C, 40°C og 60°C
Tabel 11. Mekaniske egenskaber af kompositmaterialer ved 23°C efter eksponering i vand ved 23°C i 28
døgn
(I parentes er anført den statistiske standardafvigelse på middelværdierne)
Prøveplader |
Bøjestyrke MPa |
% af referencens værdi 2) |
E-modul MPa |
% af referencens værdi 2) |
Glasindhold vægt-% |
Materialeprøve (reference) 1) ikke eksponeret |
152 (26) |
- |
6654 (545) |
- |
34 |
Materialeprøve (reference) 1) eksponeret |
147 (11) |
97/- |
5744 (807) |
86/- |
34 |
Polyesterlaminat med regenererede glasfibre |
43 (5) |
28/29/14 |
3875 (697) |
58/67/39 |
59 |
Epoxylaminat med regenererede glasfibre |
102 (8) |
67/69/37 |
8289 (1333) |
125/144/78 |
56 |
1) Referenceprøven er et GUP-emne fra EM Fiberglas.
2) Første tal angiver egenskabsværdien i forhold til referencens; andet tal angiver egenskabsværdien i forhold til den eksponerede references; tredie tal er korrigeret i mht. volumenandelen af glasfibre i forhold til den eksponerede references værdi, idet 34 vægt-% ≈ 20 volumen-%, 56 vægt-% ≈ 37 volumen-%, og 59 vægt-% ≈ 41 volumen-%.
Tabel 12. Mekaniske egenskaber af kompositmaterialer ved 23°C efter eksponering i vand ved 40°C i 28
døgn
(I parentes er anført den statistiske standardafvigelse på middelværdierne)
Prøveplader |
Bøjestyrke MPa |
% af referencens værdi 2) |
E-modul MPa |
% af referencens værdi 2) |
Glasindhold vægt-% |
Materialeprøve (reference) 1) ikke eksponeret |
152 (26) |
- |
6654 (545) |
- |
34 |
Materialeprøve (reference) 1) eksponeret |
126 (17) |
83/- |
5975 (612) |
90/- |
34 |
Polyesterlaminat med regenererede glasfibre |
34 (8) |
22/27/13 |
2675 (780) |
40/45/22 |
59 |
Epoxylaminat med regenererede glasfibre |
64 (13) |
42/51/28 |
5732 (1826) |
86/96/52 |
56 |
1) Referenceprøven er et GUP-emne fra EM Fiberglas.
2) Første tal angiver egenskabsværdien i forhold til referencens; andet tal angiver egenskabsværdien i forhold til den eksponerede references; tredie tal er korrigeret i mht. volumenandelen af glasfibre i forhold til den eksponerede references værdi, idet 34 vægt-% ≈ 20 volumen-%, 56 vægt-% ≈ 37 volumen-%, og 59 vægt-% ≈ 41 volumen-%.
Tabel 13. Mekaniske egenskaber af kompositmaterialer ved 23°C efter eksponering i vand ved 60°C i 28
døgn
(I parentes er anført den statistiske standardafvigelse på middelværdierne)
Prøveplader |
Bøjestyrke MPa |
% af referencens værdi 2) |
E-modul MPa |
% af referencens værdi 2) |
Glasindhold vægt-% |
Materialeprøve (reference) 1)
ikke eksponeret |
152 (26) |
- |
6654 (545) |
- |
34 |
Materialeprøve (reference) 1)
eksponeret |
125 (11) |
82/- |
5409 (695) |
81/- |
34 |
Polyesterlaminat med regenererede glasfibre |
44 (9) |
29/35/17 |
3787 (1220) |
57/70/34 |
59 |
Epoxylaminat med regenererede glasfibre |
78 (13) |
51/62/34 |
7988 (1962) |
120/148/80 |
56 |
1) Referenceprøven er et GUP-emne fra EM Fiberglas.
2) Første tal angiver egenskabsværdien i forhold til referencens; andet tal andet tal angiver egenskabsværdien i forhold til den eksponerede references; tredie tal er korrigeret i mht. volumenandelen af glasfibre i forhold til den eksponerede references værdi, idet 34 vægt-% ≈ 20 volumen-%, 56 vægt-% ≈ 37 volumen-%, og 59 vægt-% ≈ 41
volumen-%.
6.2.3 Diskussion
I anden forsøgsserie blev der udført støbning af prøveplader ved brug af vakuum-injektion, efter at det halve areal af hver prøve af de termisk forbehandlede glasfibre var blevet renset for partikler ved
støvsugning. Da der kun blev udført forbehandling af to plader, har det ikke været muligt at optimere selve støbeprocessen.
De mekaniske målinger viser varierende resultater, men ikke væsentlige forskelle på, om emnerne er renset eller ikke renset. De målte bøjestyrker er noget højere end i første forsøgsserie, og E-modulerne er
lidt lavere jf. tabel 9. For begge egenskaber gælder, at der til trods for et forholdsvist højt glasindhold ikke opnås tilsvarende stigning i egenskaber, som generelt er gældende for fiberforstærkede
kompositmaterialer. Bestemmelse af glasindhold i referenceprøven inkluderer gelcoatlaget, hvilket betyder, at det reelle glasindhold er 3-5% højere.
Der blev udført orienterende bestemmelser af interlaminar forskydningsstyrke. Der kan konstateres en vis forskel på de emner, der er støbt med polyester, og dem med epoxyplast, idet der opnås en noget
højere værdi med epoxyplast. Denne forskel kan ikke umiddelbart forklares.
Der blev foretaget en sammenlignende undersøgelse af vandoptagelse ved tre temperaturer. Resultaterne viser en væsentlig forskel mellem epoxylaminat og polyesterlaminat, idet vandoptagelsen for
epoxylaminat er 5-7 gange så stor. Det skyldes formentligt, at epoxylaminatet er mindre homogent og indeholder lunker. Vandoptagelsen sker hurtigere og er større ved højere temperatur. På figur 6 ses
imidlertid, at vandoptagelsen er større ved 23°C end ved 40°C. Det antages at skyldes forskelle i emnernes kvalitet og den omstændighed, at glasfibrene ligger tæt ved eller lige i overfladen. Industrielt
fremstillede produkter vil almindeligvis være udført med beskyttende gelcoat og topcoat eller egentligt spærrelag som beskyttelse mod ydre påvirkninger. Det bemærkes, at referenceprøverne har gelcoat på
den ene side og et tyndt lag ren polyester på den anden side.
De mekaniske egenskaber efter eksponering i vand viser ikke entydige sammenhænge mellem eksponeringstemperatur og egenskaber. Der kan dog ses en vis tendens, nemlig at egenskaberne reduceres ved
højere eksponeringstemperatur, selv om laminaterne med regenererede glasfibre pga. forskellig kvalitet ikke helt følger den tendens, som lidt tydeligere ses for de eksponerede referenceprøver.
6.2.4 Konklusion
Anden forsøgsserie udbygger resultaterne fra første forsøgsserie med yderligere bestemmelse af mekaniske egenskaber og undersøgelse af vandoptagelse ved forskellige temperaturer. Der er grundlag for at
kunne fremstille produkter med egenskaber, der er reduceret i forhold til brug af nye glasfibre, men dog tilstrækkelige til visse anvendelser. Resultaterne af vandoptagelse indikerer, at termisk forbehandlede
fibre vil kunne anvendes i produkter, der påvirkes af vand. Fremstillingsprocessen er ikke forsøgt optimeret, hvilket sikkert vil kunne give forbedrede egenskaberne.
6.3 Tredje forsøgsserie
I tredje forsøgsserie blev effekten af resizing med silan af termisk forbehandlede glasfibre undersøgt. Tre firkantede udskæringer af glasfiberforstærket polyester fra EM Fiberglas A/S blev termisk
forbehandlet hos ReFiber ApS. Påføring af silan og fremstilling af prøveplader med regenererede glasfibre blev udført hos KMT - Nord.
6.3.1 Fremgangsmåde
- Forbehandling ved kombineret pyrolyse og forbrænding
- Fremstilling af prøveplader af regenererede glasfibre med og uden resizing
- Prøvning af prøveplader af regenerat med og uden resizing
6.3.2 Eksperimentelt
6.3.2.1 Forbehandling
I tredje forsøgsserie blev forbehandlingen af tre plader på ca. 80×80 cm fra EM Glasfiber A/S udført hos ReFiber ApS efter følgende proces:
- Kombineret pyrolyse ved opvarmning til 450°C eller 490°C og forbrænding af carbon i atmosfærisk luft ved 450°C.
Forsøgsrapport fra ReFiber ApS er indgår som bilag C.
6.3.2.2 Resizing og fremstilling af prøveplader af regenerat
Resizing blev udført i en 2% vandig opløsning af -aminopropyltriethoxysilan med handelsbetegnelsen A1100. Opløsningen blev justeret med eddikesyre til pH ca. 4,6. Efter at glasfibrene - fastholdt mellem to
fintmaskede net for at holde fibrene tilbage - var blevet renset ved støvsugning, blev de i femten minutter holdt neddyppet i et kar med opløsningen, mens glasfibrene blev påvirket med en metalrulle for at
sikre befugtning af alle fibre. Derefter blev de lagt til tørring ved 105°C i 4 timer.
Ved vakuuminjektion blev der støbt fire prøveplader med henholdsvis polyester og epoxyplast og glasfibre med og uden resizing. Resizing og injektion blev udført hos bådværftet KMT - Nord. Analyse af
glasfibrenes overflade og mekaniske egenskaber af laminater blev bestemt ved prøvning på Teknologisk Institut.
6.3.2.3 Prøvning af prøveplader med og uden resizing
6.3.2.3.1 Styrkeegenskaber og glasindhold
Bøjebrudstyrke, elasticitetsmodul ved bøjning (E-modul) og glasindhold blev bestemt ved standardiseret prøvning.
Bøjebrudstyrke og E-modul:
Metode: ISO 178.
Antal emner: 6.
Deformationshastighed: 1,5 mm/min både ved brudstyrkebestemmelse og ved E-modulbestemmelse.
Understøtningsafstand: 16 gange godstykkelsen, dvs. varierende afhængigt af godstykkelsen.
Glasindholdet blev bestemt som glødetabet (summen af indholdet af glasfibre og af andre uorganiske stoffer) efter ISO 1172 og er angivet i vægt-%.
Tabel 14. Mekaniske egenskaber af kompositmaterialer ved 23°C med og uden resizing
(I parentes er anført den statistiske standardafvigelse på middelværdierne)
Prøveplader |
Bøjestyrke MPa |
med/uden resizing 1) |
E-modul MPa |
med/uden resizing 1) |
Glasindhold vægt-% |
Polyesterlaminat med regenererede glasfibre uden resizing |
195 (46) |
- |
13717 (1298) |
- |
57 |
Polyesterlaminat med regenererede glasfibre med resizing |
216 (14) |
1,11 |
13031 (781) |
0,95 |
55 |
Epoxylaminat med regenererede glasfibre uden resizing |
271 (64) |
- |
15084 (2321) |
- |
56 |
Epoxylaminat med regenererede glasfibre med resizing |
263 (19) |
0,97 |
14439 (863) |
0,96 |
58 |
1) Angiver forholdet mellem egenskabsværdierne med og uden resizing.
6.3.2.3.2 Overfladeanalyse af glasfibre
For at konstatere om processen med resizing har medført, at der er afsat et lag af silan på de termisk forbehandlede fibre, er der ved brug af analysemetoden TOF-SIMS (time-of-flight secondary ion
mass spectrometry) udført en analysen af fibre der er blevet termisk forbehandlet i muffelovn ved 450°C, fibre der er blevet behandlet med silan og af nye fibre. Analysen indikerer, at der inden for
analyseområdet er opnået en forholdsvis jævn belægning af silan.
6.3.3 Diskussion
I tredje forsøgsserie blev det på to prøveplader undersøgt, om resizing med silan af regenererede glasfibre giver bedre mekaniske egenskaber end regenererede glasfibre uden resizing. De foreliggende
resultater viser, at kun i et enkelt tilfælde med polyesterlaminat blev bøjestyrken forbedret med 11%. I de øvrige resultater kan der ikke konstateres nogen forbedring. Mest markant er det, at spredningen er
væsentligt mindre for alle resultater med resizede glasfibre.
6.3.4 Konklusion
Tredje forsøgsserie underbygger de tidligere resultater mht. hvilke mekaniskeegenskaber der kan opnås og viser, at der alt andet lige kan opnås mere ensartede egenskaber, hvis regenererede glasfibre
behandles med silan. Det er konstateret, at behandlingen med silan har påført fibrene en ny size. Der er brug for, at metoder til resizing udvikles og optimeres. Dette kan være af betydning for såvel
anvendelses- som afsætningmulighederne af regenererede glasfibre, idet en bedre kvalitet vil fremme en industriel produktion
6.4 Demonstrationsemner
6.4.1 Fremstilling af demonstrationsemner
Af regenerat, der er blevet termisk forbehandlet hos ReFiber ApS, blev der hos bådværftet KMT - Nord fremstillet tre demonstrationsemner. Det første er den del af en motorcykelskærm, der kunne
afformes af en gammel polyesterform; det andet er en rorplader til en jolle, og det sidste er en lugeindfatning.
Regeneratet til de to første emner stammer fra emner, der blev termisk forbehandlet ved 490°C, regeneratet til det sidste emne blev fremstillet ved samme proces, men ved en temperatur på 525°C, som
beskrevet i bilag C.
Motorcykelskærmen blev støbt med glasfibre, der ikke var blevet renset for partikler. Lugeindfatningen blev fremstillet i to versioner, én hvor glasfibrene blev renset ved støvsugning, og én hvor glasfibrene
blev resizet med silan. Den ene rorplade blev støbt med rensede og den anden med glasfibre, der ikke var blevet renset. Alle emner blev støbt med epoxyplast. Emnerne er vist i figur 8, 9 og 10.
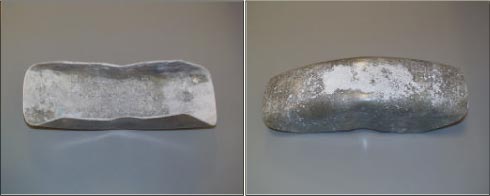
Figur 8 Motorcykelskærm af ikke renset regenerat. Dimensioner: Længde 38 cm, bredde 11 cm, højde 9 cm, godstykkelse 4 mm
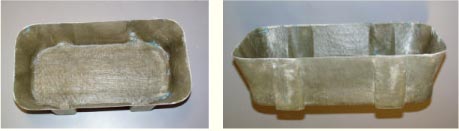
Figur 9 Lugeindfatning af renset regenerat. Dimensioner: Længde 38 cm, bredde 19 cm, højde 10 cm, godstykkelse 2 mm
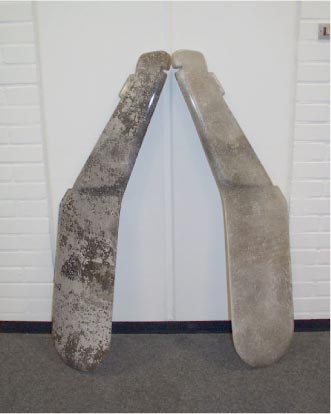
Figur 10 Rorplader til jolle; til venstre rorplade af ikke renset regenerat, til højre rorplade af renset regenerat. Dimensioner: Højde 108 cm, største bredde 26 cm, godstykkelse 5 mm
6.4.2 Konklusion
De fremstillede emner er forskellige i udstrækning og i højde. Det viser umiddelbart, at det er muligt at støbe enkle emner relativt uproblematisk. Det vil dog lette arbejdet med regenererede glasfibre, hvis de
blev bundet med en slags lim, så det blev nemmere at drapere og håndtere dem og undgå, at fiberbundterne glider fra hinanden; det gælder specielt, hvis formene er høje.
6.5 Konklusion af forsøg med termisk forbehandling
Sammenfattende kan det konkluderes, at der ved anvendelse af termisk forbehandlede glasfibre imprægneret med umættet polyester eller med epoxyplast kan opnås egenskaber, som vil være tilstrækkelige
til produkter, til hvilke der stilles moderate krav til mekaniske egenskaber selv om deres brudstyrke bliver reduceret med mere end 50%. Endvidere indikerer resultaterne af vandoptagelse, at termisk
forbehandlede fibre vil kunne anvendes i produkter, der påvirkes af vand.
Fremstillingsprocessen er ikke forsøgt optimeret, hvilket sikkert vil kunne give forbedrede egenskaberne. Produkterne vil kunne fremstilles ved kendte produktionsmetoder som håndoplægning,
vakuuminjektion og presning.
For at opnå lettere håndtering af de termisk forbehandlede glasfibre vil det være en væsentlig forbedring at finde en enkel metode til at binde glasfibrene, så de kan anvendes på tilsvarende måde, som kendes
for nye glasfibermåtter og rovingvæv. Endvidere vil det være hensigtsmæssigt både af miljømæssige (generende støv) og af procesmæssige årsager at finde en effektiv måde at fjerne uorganiske partikler og
støv på. Termisk forbehandlede fibre kan påføres en size, som efter udvikling af mere rationelle metoder til påføring vil kunne føre til både mere ensartede og højere egenskabsværdier.
På baggrund af de opnåede resultater og erfaringer udestår der en del arbejde med at forbedre række delprocesser, der er knyttet glasfibrene. Det drejer sig blandt andet om at optimere rensning af
glasfibre, at påføre ny size på en effektiv måde, at påføre et bindemiddel så glasfibrene er sammenhængende i bundter og som måtte eller væv, således at de kan håndteres under sædvanlige
produktionsforhold.
7 Mekanisk forbehandling
7.1 Eksperimentelt
7.1.1 Mekanisk forbehandling
7.1.2 Genanvendelse af mekanisk forbehandlet kompositmateriale
7.1.3 Prøvning af prøveplader
7.2 Diskussion
7.3 Konklusion af forsøg med mekanisk forbehandling
Den mekaniske forbehandling omhandler en neddelingsproces i flere trin, hvorved det oprindelige emne neddeles til mindre dele og/eller knuses til mindre partikler.
Med en møllevinge som eksempel vil en typisk neddelingsproces omhandle:
- Opskæring af emne (fx bortskæring af vingerod)
- Første neddeling i ”cutter/shredder”
- Resultatet bliver typisk stykker på 5 - 20 cm samt enkelte fiberdele dækket af plastmateriale, støv og diverse smuld
- Første adskillelse
- Fibre opsamles til genanvendelse. Eventuelt neddeles de til en mere ensartet størrelse
- Store stykker kan føres tilbage til foregående proces
- Støv opsamles og genanvendes som funktionelt fyldstof og/eller bortskaffes
- Anden neddeling i slagmølle/hammermølle/kværn (gentages efter behov)
- Resultatet er typisk en blanding af korte fibre delvist dækket af plastmateriale samt små stykker og støv
- Adskillelse af komponenter (fibre, emnestykker, støv mv.)
- Fibre opsamles til genanvendelse. Eventuelt neddeles de til en mere ensartet størrelse
- Større stykker føres tilbage til foregående proces
- Støv opsamles og genanvendes som funktionelt fyldstof og/eller bortskaffes
- Evt. yderligere neddeling i kværn/mølle
- Evt. formaling til finkornet fyldstof
Den mekanisk neddelingsproces vil ifølge litteraturen typisk resultere i en opdeling i to genanvendelige fraktioner bestående af:
- Forstærkningsmaterialer (hovedsageligt meget korte stykker af fibre og fiberbundter, der er helt eller delvist dækket af plastmateriale)
- Fyldstoffer, der ved genanvendelse ikke umiddelbart bidrager med nogen forstærkende effekt
7.1 Eksperimentelt
7.1.1 Mekanisk forbehandling
7.1.1.1 Mekanisk forbehandling af polyesterbaseret kompositmateriale
Der er blevet udført et forsøg med neddeling af to udskæringer af glasfiberforstærket umættet polyester (GUP) fra vindmøllehuse, som er fremstillet hos EM Fiberglas A/S. Prøverne havde en diameter på
ca. 400 mm.
Neddelingen blev udført i en cutter/shredder hos H.J. Hansen Genvindingsindustri i Odense.
Det mekanisk neddelte materiale fremstod som en blanding af løse fiberbundter, der er mere eller mindre dækket af plastharpiks, stykker i varierende størrelser (1 - 25 cm) og diverse smuld og støv. Se figur
11 - 13.
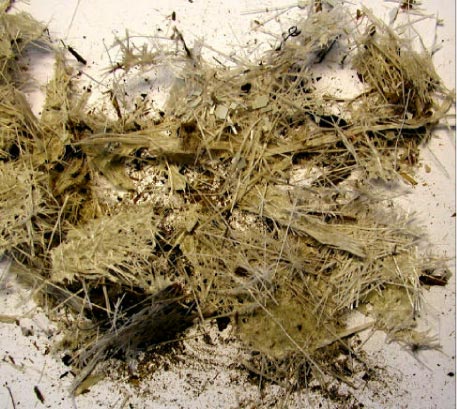
Figur 11 Foto af håndsorterede dele af neddelt materiale fra H.J. Hansen Genvindingsindustri: Fortrinsvis fiberdele, der er mere eller mindre dækket af plastmateriale
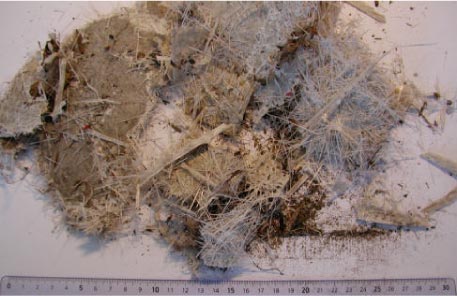
Figur 12 Foto af neddelt materiale fra H.J. Hansen Genvindingsindustri: Stykker på 5 - 20 cm, enkelte fiberdele, støv og diverse smuld
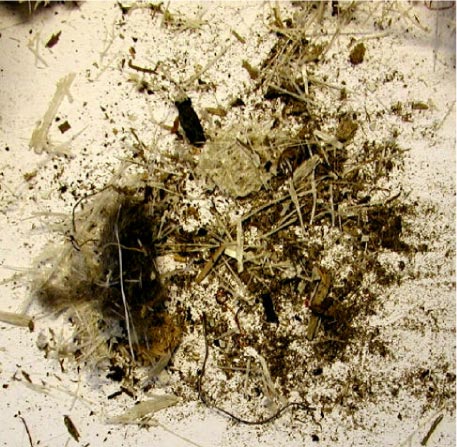
Figur 13 Foto af neddelt materiale fra H.J. Hansen Genvindingsindustri: Smuld og støv
Efterfølgende blev materialet yderligere neddelt i en knivmølle (RAPID K20) monteret med hhv. ø6 mm sold og 10 mm firkantet sold.
Der blev lavet forsøg både med en gang og to gange igennem knivmøllen. Det neddelte materiale blev derpå sorteret i fire fraktioner efter størrelse i en mekanisk sigte med maskestørrelser 1,0 mm, 2,0 mm
og 2,5 mm.
I tabel 15 beskrives fordelingen i vægt-% af de fire fraktioner.
Tabel 15. Fordelingen i vægt-% i fire størrelsesfraktioner efter mekanisk forbehandling af materialeprøve af polyester fra EM Fiberglas
Størrelsesfraktioner mm |
Kværnet en gang med 10 x 10 mm sold |
Kværnet to gange med 10 x 10 mm sold |
Kværnet to gange: En gang med 10 x 10 mm sold og en gang med ø6 mm sold |
> 2,5 |
76,23 |
62,51 |
33,18 |
< 2,5 og > 2,0 |
3,02 |
6,80 |
9,06 |
< 2,0 og > 1,0 |
5,21 |
4,27 |
16,64 |
Rest (1,0 >) |
15,49 |
26,42 |
41,12 |
7.1.1.2 Mekanisk forbehandling af epoxybaseret kompositmateriale
Der er hos H.J. Hansen Genvindingsindustri i Hadsund blevet udført neddeling og fraktionering i fuld skala af store emner af glasfiberforstærket epoxyplast. Emnerne var møllevinger fra Vestas skåret i
stykker af ca. 4 meters længde (se figur 14), og neddelingen blev udført i virksomhedens shredder, der har en kapacitet på ca. 50 tons materiale i timen.
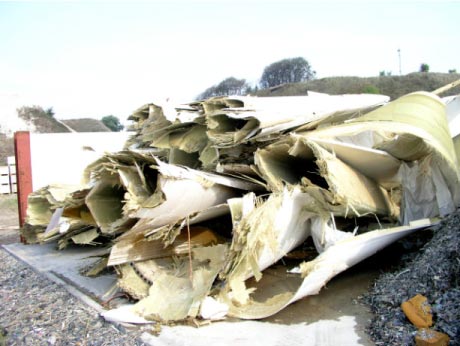
Figur 14 Foto af møllevinger klippet i stykker af ca. 4 meters længde før neddeling
Det neddelte materiale havde en umiddelbart overraskende ensartet sammensætning, hvilket sandsynligvis skyldes, at materialeprøven også var ret ensartet (se figur 15).
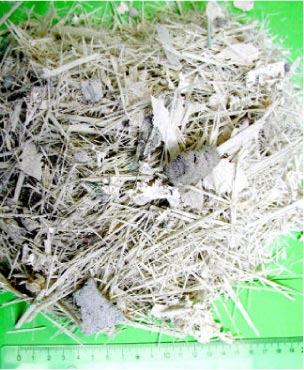
Figur 15 Foto af neddelt epoxybaseret materiale fra forsøg hos H. J. Hansen Genvindingsindustri i Hadsund
Efterfølgende blev materialet yderligere neddelt ved hjælp af en knivmølle (RAPID K20) monteret med hhv. ø6 mm sold og 10 mm firkantet sold.
Der blev lavet forsøg både med en gang og to gange igennem kværnen. Det neddelte materiale blev efterfølgende sorteret i fire fraktioner i en mekanisk sigte med maskestørrelse 1,0 mm, 2,0 mm og 2,5
mm.
I tabel 16 beskrives fordelingen i vægt-% af de fire fraktioner.
Tabel 16. Fordelingen i vægt-% i fire størrelsesfraktioner efter mekanisk forbehandling af vinge af epoxyplast fra Vestas
Størrelsesfraktioner mm |
Ubehandlet materiale |
Kværnet en gang med 10 x 10 mm sold |
Kværnet to gange med 10 x 10 mm sold |
Kværnet en gang med ø6 mm sold |
> 2,5 |
52,53 |
49,17 |
34,59 |
24,75 |
< 2,5 og > 2,0 |
12,58 |
15,11 |
13,87 |
18,85 |
< 2,0 og > 1,0 |
13,21 |
11,84 |
21,23 |
22,95 |
Rest (< 1,0) |
21,67 |
23,88 |
30,31 |
33,45 |
Det neddelte materiale fra en vinge har meget forskellig karakter, i figur 16 vises det materiale som stammer fra vingeroden til sammenligning med figur 15.
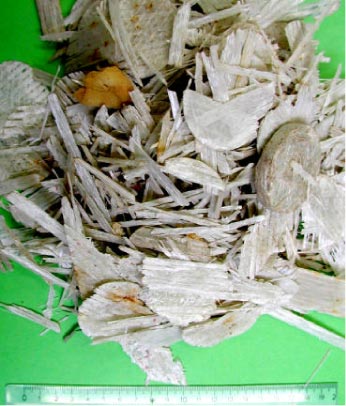
Figur 16 Foto af den nederste del af vingeroden, som var vanskelig at neddele pga. den kompakte karakter dvs. meget høje glasindhold
7.1.1.3 Glasindhold i sorteringsfraktioner
Glasindholdet i de neddelte sorteringsfraktioner fremgår af tabel 19. Det skal bemærkes, at to fraktioner er slået sammen, således at fragmenter med størrelse i intervallet 1,0 mm til 2,5 mm er blevet
behandlet under et.
Tabel 19. Glasindholdet (bestemt ved forbrænding ved 625°C) i det neddelte materiale fra møllevinge fra Vestas af epoxyplast. Nneddeling er udført hos H.J. Hansen Genvindingsindustri i Hadsund før og yderligere mekanisk neddeling i RAPID-knivkværn er udført hos Teknologisk Institut.
|
Ubehandlet materiale |
1 x knivkværn 2,5 mm sigte |
1 x knivkværn 1,0 mm sigte |
1 x knivkværn restfraktion (< 1,0 mm) |
Glasindhold (vægt-%) |
61,0 |
62,6 |
64,5 |
71,1 |
7.1.2 Genanvendelse af mekanisk forbehandlet kompositmateriale
7.1.2.1 Som funktionelt fyld i teglstensler
Mekanisk forbehandling resulterer, som tidligere beskrevet, i flere fraktioner af korte fibre (typisk fiberbundter) delvist dækket af plastharpiks, små stykker og en restfraktion med meget støv. De løse fibre
og fiberbundter kan umiddelbart anvendes som forstærkningsmateriale i den form, de er i. Håndtering og udlægning vanskeliggøres dog af, at fibre og fiberbundter er delvist dækket af plastharpiks og derfor
er ret stive.
Et forsøg med at tilsætte mekanisk forbehandlet kompositaffald til teglstensler er blevet udført. Det neddelte materiale fra H.J. Hansen Genvindingsindustri i Hadsund er uden yderligere forbehandling blevet
ført til teglstensler i varierende andele op til 20 volumen-%. Lerblandingen blev efterfølgende æltet og formet til kasseformede prøveemner. Disse emner kan udtørres, uden at de revner, og de kan tåle
efterfølgende at blive brændt i ovn ved 625°C, hvorved alt organisk materiale forbrændes.
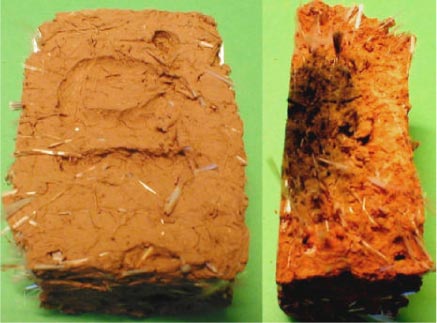
Figur 17 Foto af prøveemner: Minimursten med mekanisk forbehandlet kompositaffald af epoxyplast før anden brænding
Prøveemnerne brændes endeligt i elektrisk ovn ved ca. 1000°C
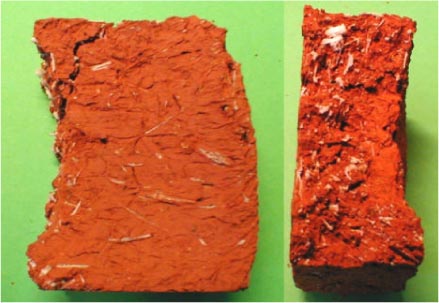
Figur 18 Foto af prøveemner: Minimursten efter sidste brænding ved 1000°C
7.1.2.2 Binding af regenererede fibre og fiberbundter til semifleksible "måtter"
For at gøre fibre og fiberbundter mere brugbare blev der udført bindingsforsøg med det neddelte materiale fra møllevingen og en klæber på basis af polyvinylalkohol (PVA), hvorved fibre og fiberbundter
bindes som i en traditionel glasfibermåtte. Til forsøget blev der anvendt en standard-snedkerlim til udendørs brug med højt indhold af PVA.
For at undersøge bindingsevnen blev der udført forsøg med forskellige blandingsforhold mellem PVA og vand. Forsøgene blev udført med et PVA/vand-forhold på op til 1:10; men umiddelbart så det ud til,
at indholdet af PVA kan reduceres yderligere. Vandindholdet i PVA-limen blev eksperimentelt bestemt til 45,5 vægt-%. Det blev antaget, at det resulterende indhold af PVA, dvs. eksklusive vand,
emulgatorer og andre hjælpestoffer, udgjorde ca. 50%. I de udførte bindingsforsøg blev der tilført 30 g fortyndet PVA-lim pr. 100 g fibre/fiberbundter. Det resulterende indhold af PVA efter udtørring var
mindst ca. 3%.
De løse fibre og fiberbundter blev placeret i en spand, og fortyndet lim påsprøjtes under omrøring, så den fordeles godt. De våde fibre/fiberbundter blev udlagt på to måder:
- Våde fibre/fiberbundter fordeles på et opvarmet stålplan i en hydraulisk presse og udsættes for varme og tryk i ca. 5 minutter, hvorved limen hærder, og det tiloversblevne vand mere eller mindre
fordamper
- Våde fibre/fiberbundter fordeles på en stålplade med en tværriflet nylonrulle. Pladen placeres i varmeskab for at forcere udtørringen
Umiddelbart blev resultatet med de to metoder meget ensartet, og da udlægning med nylonrulle er langt den letteste at udføre, blev den fremgangsmåde brugt efterfølgende.
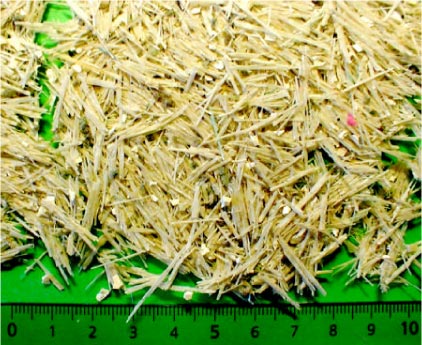
Figur 19 Foto af semifleksibel "måtte" bundet af løse fibre/fiberbundter fra møllevinge og fortyndet PVA-lim
Slutproduktet er en semifleksibel ”måtte”, der kan formes i bløde kurver. Sådanne ”måtter” kan eventuelt anvendes på tilsvarende måde som glasfibermåtter, de er dog ikke nær så fleksible.
Prøvning af kompositemner indeholdende disse semifleksible ”måtter” viste efterfølgende lave værdier af styrke og stivhed, hvilket indikerer, at der sandsynligvis ikke kunne opnås tilstrækkeligt god
vedhæftning mellem PVA-lim og injektionsharpiks. For at imødegå dette blev der i stedet for PVA-lim anvendt en binder bestående af injektionsepoxy fortyndet med ethanol. Injektionsepoxyen er af samme
type som den, der anvendes til fremstilling af prøveplader hos bådværftet KMT - Nord.
Der blev udført forsøg af bindingsevnen med to forskellige blandingsforhold af epoxyplast og ethanol (1:5 og 1:10 epoxyplast/ethanol efter vægt). I de udførte bindingsforsøg blev der tilført 30 g fortyndet
epoxyplast pr. 100 g fibre/fiber- bundter. Det resulterede i et indhold af epoxyplast efter udtørring på ca. 3%.
De løse fibre og fiberbundter blev placeret i en spand, og fortyndet epoxyplast blev påsprøjtet under omrøring for at opnå god fordeling af bindemidlet. De våde fibre/fiberbundter blev udlagt på en stålplade
med en tværriflet plastrulle. Stålpladen blev herefter placeret i et varmeskab for at forcere udtørringen.
Slutproduktet blev en noget mindre fleksibel ”måtte”, med dog stadig med mulighed for at forme den i bløde kurver.
7.1.2.3 Fremstilling af prøveplader med semifleksible "måtter"
Af de ovenfor fremstillede "måtter" blev der fremstillet nye kompositemner ved injektion med henholdsvis polyester og epoxyplast. Injektionen blev udført hos bådværftet KMT - Nord, og egenskaberne af
disse kompositmaterialer blev bestemt ved prøvning på Teknologisk Institut.
Der blev også fremstillet en prøveplade direkte med løse fibre og fiberbundter, uden at disse forinden var samlet i en semifleksibel ”måtte”. Støbning af denne prøveplade lykkedes ikke og derfor egnet til
prøvning. Den prøveplade, der blev fremstillet med epoxyplast og en semifleksibel "måtte" af 2,5 - 6 mm-fraktionen, var ligeledes ufuldstændigt støbt og ikke egnet til prøvning. Årsagen til ufuldstændig
støbning var, at vakuumfolien var blevet gennemhullet af de skarpe og stive fiberbundter.
Følgende prøveplader var gode nok til at blive prøvet:
- 1 plade af epoxyplast og en semifleksibel "måtte" af 1,0 - 2,5 mm-fraktionen
- 1 plade af polyester og en semifleksibel "måtte" af 2,5 - 6,0 mm-fraktionen
Efterfølgende blev der fremstillet yderligere prøveplader baseret på ”måtter” med epoxybinder - 3% epoxyplast opløst i ethanol - og epoxyplast. Injektionen blev udført hos bådværftet KMT - Nord,
og egenskaberne af disse kompositmaterialer blev bestemt ved prøvning på Teknologisk Institut.
I forbindelse med fremstillingen af de seneste prøveplader blev der anvendt to lag vakuumfolie for at undgå, at folien blev gennemhullet.
Samtidigt blev der af Teknologisk Institut fremstillet en prøveplade baseret på epoxysmuld (0 - 1,0 mm-fraktionen); den blev vædet med samme injektionsepoxy, som blev anvendt af KMT-Nord.
Det ”våde” epoxysmuld blev efterfølgende udrullet til en plade med en plastrulle og efterhærdet. Materialeegenskaber blev bestemt ved prøvning på Teknologisk Institut. Heraf var følgende
prøveplader gode nok til at blive blev prøvet:
- 1 plade af epoxyplast og en "måtte" af 1,0 - 2,5 mm-fraktionen
- 1 plade af epoxyplast og løs epoxysmuld af 0 - 1,0 mm-fraktionen
7.1.3 Prøvning af prøveplader
7.1.3.1 Styrke og glasindhold
Glasindhold, bøjebrudstyrke og elasticitetsmodul ved bøjning (E-modul) blev bestemt ved standardiseret prøvning.
Bøjebrudstyrke og E-modul:
Metode: ISO 178.
Antal emner: 7
Deformationshastighed: 1,5 mm/min både ved brudstyrkebestemmelse og ved bestemmelse af E-modul.
Understøtningsafstand: 16 gange godstykkelsen, dvs. varierende afhængigt af godstykkelsen.
Glasindholdet blev bestemt på sorteringsfraktioner og på de to prøveplader som glødetab (glasfibre og uorganiske stoffer) i henhold til ISO 1172 og er angivet i vægt-%.
I tabel 17 vises de mekaniske egenskaber af og glasindholdet i de to første prøveplader.
Tabel 17. Mekaniske egenskaber af prøveplader fremstillet ved injektion af polyester henholdsvis epoxyplast i PVA bundne "måtter" af mekanisk forbehandlet kompositmateriale
(I parentes er anført den statistiske standardafvigelse på middelværdierne)
Prøveplader |
Bøjestyrke MPa |
E-modul MPa |
Glasindhold vægt-% |
Injiceret polyesterplade 1) |
30 (10,6) |
2672 (444) |
24,9 |
Injiceret epoxyplade 2) |
72 (19,3) |
3295 (734) |
25,5 |
1) "Måtte" med 2,5 - 6 mm store fragmenter injiceret med polyester og efterhærdet i 6 timer ved 60°C.
2) "Måtte" med 1,0 - 2,5 mm store fragmenter injiceret med epoxyplast og efterhærdet i 6 timer ved 60°C.
I tabel 18 vises de mekaniske egenskaber af og glasindholdet i de to sidste prøveplader.
Tabel 18. Mekaniske egenskaber af prøveplade fremstillet ved injektion af epoxyplast i epoxybundne "måtte" af regenereret mekanisk forbehandlet kompositmateriale samt prøveplade fremstillet ved håndoplægning af vædet epoxysmuld
(I parentes er anført den statistiske standardafvigelse på middelværdierne)
Prøveplader |
Bøjestyrke MPa |
E-modul MPa |
Glasindhold vægt-% |
Injiceret epoxyplade 1) |
79 (9,2) |
3623 (188) |
25,9 |
Injiceret epoxyplade 2) |
97 (14,6) |
4298 (633) |
25,8 |
1) "Måtte" med 1,0 - 2,5 mm store fragmenter injiceret med epoxy og efterhærdet i 6 timer ved 60°C.
2) Epoxysmuld med 0 - 1,0 mm store fragmenter vædet epoxy og efterhærdet i 6 timer ved 60°C.
7.2 Diskussion
Det har vist sig muligt af foretage en yderligere neddeling og sortering i fraktioner af det materiale fra møllevingen, som ikke stammer fra vingeroden jf. figur 15. Derimod har det vist sig særdeles vanskeligt at
neddele det materiale, der stammer fra vingeroden og fra udskæringer til bolthuller jf. figur 16. Til den form for kompositaffald kræves en anden slags kværn. Den grovere neddeling udført hos H.J. Hansen
Genvindingsindustri er forløbet uproblematisk.
At glasindholdet, som vist i tabel 15, i det neddelte materiale er højere end i det ikke sigtede materiale, skyldes, at der under neddelingen dannes en del støv, som hovedsageligt består af hærdeplast, og som
ikke opsamles. Desuden forblev der en del tilsvarende støv tilbage i den sæk, hvori fraktionerne opsamledes efter behandling.
Det neddelte materiale fra H.J. Hansen Genvindingsindustri i Hadsund er uden yderligere forbehandling blevet blandet i ler til tegl i varierende mængder op til 20 volumen-%. Tanken var, at
kompositmaterialet skulle bidrage tilmurstenenes styrke. Prøveemner baseret på dette materiale kan udtørres, uden at de revner, og de kan tåle efterfølgende at blive brændt i ovn ved 625°C og herefter ved
samme temperaturstigningshastighed, som anvendes i teglværksindustrien op til ca. 1000°C , hvorved alt organisk materiale forbrændes.
Prøvning af kompositemner indeholdende semifleksible ”måtter” med en binder af PVA-lim viste sig at have lave værdier af styrke og stivhed jf. tabel 17, hvilket indikerer, at der sandsynligvis ikke kan opnås
tilstrækkeligt god vedhæftning mellem PVA-lim og injektionspolymer. For at imødegå dette blev der i stedet for PVA-lim anvendt en binder bestående af injektionsepoxy fortyndet med sprit (ethanol).
Ved brug af injektionsepoxy som binder fås en noget stivere ”måtte”, der dog stadigt lader sig bøje i bløde kurver.
Forsøg med direkte vædning af epoxysmuld (0 - 1,0 mm-fraktionen) gav et pænt resultat. Blandingen havde umiddelbart et meget ”tørt” udseende; men efter bearbejdning med plastrulle ændrede
konsistensen sig til en dejagtig substans, som kan udlægges og formes med simple værktøjer.
Prøvning af prøveplader indeholdende semifleksible ”måtter” med en epoxybinder viste sig at ligge på niveau med de prøver der er bundet med PVA. Prøvning af kompositemne baseret på epoxysmuld viste
sig til gengæld at have lidt bedre værdier både mht. bøjestyrke og E-modul jf. tabel 18. De opnåede værdier er dog kun noget bedre, end de værdier der kan opnås med udhærdet polyester eller epoxyplast
uden forstærkning. Der udestår således et yderligere udviklingsarbejde, for at reducere mængden af luftindeslutninger og opnå en bedre fordeling af fibre og fiberbundter mht. fraktioner og øge deres andel
samt at forbedre forstærkningsmaterialernes samvirke med polyester og epoxyplast.
7.3 Konklusion af forsøg med mekanisk forbehandling
Fraktionering af løse fibre eller fiberbundter kan umiddelbart foretages på et tidligt tidspunkt i neddelingsforløbet. Fibre og fiberbundter med en vis længde kan ved simple metoder bindes sammen til nye,
semifleksible "måtter", der kan anvendes i kendte fremstillingsprocesser som vakuuminjektion, presning og håndoplægning.
Mekanisk forbehandlet kompositmateriale kan anvendes i fremstillingen af produkter af tegl. Det er dog ikke undersøgt, om neddelt komposit har en positiv virkning på teglstens styrke. Dette ville være
relevant at undersøge, hvis denne anvendelse skal komme på tale.
Den fineste fraktion af neddelt materiale kan ved simpel vædning med injek-tionsepoxy ligeledes anvendes i kendte fremstillingsprocesser som presning (BMC) og håndoplægning.
Sammenfattende kan det konkluderes, at der ved anvendelse af mekanisk forbehandlede glasfibre og glasfiberbundter - imprægneret med epoxyplast - vil kunne opnås egenskaber, som vil være
tilstrækkelige til produkter, hvortil der stilles moderate krav til mekaniske egenskaber. Det kræver dog forbedring af den semifleksible ”måttes” egenskaber. Prøvning af disse ”måtter” har vist, at der opnås
forholdsvis lave mekaniske egenskaber. Årsagen hertil er, at der er for mange luftindeslutninger og utilstrækkeligt samvirke mellem det neddelte kompositmateriale og såvel polyester som epoxyplast.
Sådanne ”måtter” vil kunne benyttes til støbning ved vakuuminjektion, håndoplægning og presning.
8 Referencer
8.1 Referenceliste
- Armeret epoxy- og polyesterplast - forbrug og affaldsmængder, Miljøstyrelsen, Miljøprojekt nr. 656, 2002
- 2-Trins forbrænding af udtjente vindmøllervinger, Erik Grove Nielsen, Nordisk AeroForm ApS, november 2001
- The Application of Thermoset Recyclate as Functional Filler for Polymers,
Peter Hornsby, Brunel University (Project LINK - Structural Composites)
- Recycling of Fibres from Thermoset Composites, Steve Pickering, University of Nottingham
- The ecological answer of Lonza Compounds, BMC 900 RZG
- Riktlinjer för återvinning av fiberkompositter, Försöksrapporter inom området materialåtervinning, www.mtov.lth.se/vamp18, omfatter 28 rapporter
- www.seghersgroup.com henvisning til fluidised bed-behandling af affald
- Ole Thomas McClimans, Bruk av resirkulert GRP, Miniseminar i Sandefjord 22.01.2001
- Plast og Brand Nr. 5 Bygningskomponenter, Plast-Sammenslutningen, Dansk Brandforsikrings Forening og Bygningsbrandforsikrings-Foreningen 1978
- Paal Fischenich, Resirkulering av kompositter - Metoder, kapasiteter, egenskaper, anvendelser, Sundvollen 11. juni 2003
- GPRMC JEC 2003 Press Release 2003-2
- Use of glass-fibre reinforced phenolic prepreg waste as filler material in thermoplastics, Mikael Gröning, Minna Hakkarainen, Dept. of Fibre- and polymer Technology, Royal Institute of Technology,
Stockholm Sweden
- Organofunctional Silanes as Surface Treatments for Particulate Minerals, A. C. Vecere, E. J. Sadler, A. Guillet and T. S. Wu, GE Silicones
- Renere Teknologi i Tegl- og Mørtelbranchen, Katalog: Kriterier for anvendelse af alternative materialer i tegl- og mørtelprodukter. Teknologisk Institut, januar 1999
8.2 Øvrig litteratur om genvinding af plast
- R.J.Ehrig (ed.), Plastics Recycling - Products and Processes, SPE, Hanser Publishers 1992
- G.D. Andrews and P.M. Subramanian (ed.), Emerging Technologies in Plastics Recycling, ACS Symposium Series, American Chemical Society, Washington, DC 1992
- G. Menges,W. Michaeli og M. Bittner, Recycling von Kunststoffen, Carl Hanser Verlag 1992
- M. Neitzel, J.C. Lambert, G. Menges and A. Kelly, ECCM Recycling Concepts and Procedures, September 22-23, 1993, European Association for Composite Materials, Bordeaux, Frankrig og
Woodhead Publishing Ltd, Cambridge, England
8.3 Ordforklaring
Bindemiddel
Materiale påført glasfibre for at fastholde dem i et givet arrangement
BMC og DMC
Bulk Moulding Compound og Dough Moulding Compound, betegner dejagtige forimprægnerede produkter hvor korte fibre, fyldstoffer og et hærdbart plastmateriale er blandet, materialet formes ved f.eks.
presning og hærder ved opvarmning
E-modul
Elasicitetsmodul er en materialekonstant som angiver forholdet mellem en spænding og den tilsvarende elastiske forlængelse i et materiale
Gelcoat
Lag af uforstærket polyester eller epoxyplast, påført en formoverflade og hærdet forud for videre opbygning af et laminat
GUP
Forkortelse for Glasfiberforstærket Umættet Polyester
Laminat
Et lagvis opbygget produkt, her af glasfibre og enten polyester eller epoxyplast
Matrix
Plastmaterialet der binder kompositmaterialet sammen f.eks. polyester eller epoxyplast
Måtte
Et plant glasfiberprodukt bestående af tilfældigt orienterede fibre, der holdes sammen af et bindemiddel
SMC
Sheet Moulding Compounds, forimprægneret plant produkt med korte/lange fibre, fyldstoffer og et hærdbart plastmateriale, som formes vedpresning og hærder ved opvarmning
Topcoat
Lag af uforstærket polyester eller epoxyplast påført det færdige laminats overflade
Bilag A Rapport over pyrolyse
Pyrolyse af kompositmateriale af glasfiberforstærket polyester
1 Sammenfatning
Der er blevet gennemført seks forsøg med pyrolyse af prøver af kompositmateriale i laboratorieskala. Prøverne, der var blevet afleveret af Teknologisk Institut, blev pyrolyseret ved følgende temperaturer:
Forsøg nr. |
Temperatur |
1 |
500°C |
2 |
450°C |
3 |
500°C |
4 |
400°C |
5 |
550°C |
6 |
600°C |
Der ses bort fra forsøg 1, idet temperaturmålingen blev foretaget uden for det glasrør, hvori pyrolysen fandt sted, og det viste sig ikke at være pålideligt nok.
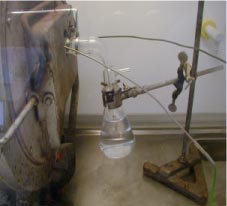
Forsøgene blev udført, ved at en prøve blev lagt ind i et glasrør, der blev placeret i en kold ovn. Glasrøret blev proppet til i den ene ende, og i den anden ende var der gasudtag via en vandfyldt vaskeflaske.
Temperaturen blev målt med en termoføler, der var ført ind i glasrøret gennem en gummiprop. Ovnen blev varmet op til den ønskede temperatur, hvorefter denne temperatur blev holdt konstant, indtil der
ikke blev observeret mere gasudvikling i røret.
Opstilling inden opvarmning
Temperaturmålingerne blev registreret i en datalog. Disse ses som trendkurver i efterfølgende logbog.
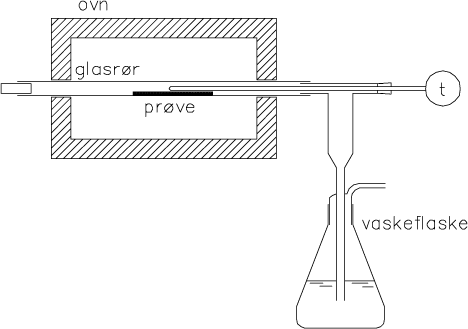
Det så ikke ud til, at variationen af temperaturen havde den store indflydelse på, hvordan pyrolyseprocessen forløb. Det var stort set de samme observationer, der blev gjort ved de enkelte forsøg.
- Ved ca. 350°C så man en ravgul væske i bunden af glasrøret, og ganske hurtigt var der så megen væske, at det løb ned i vaskeflasken. Samtidigt var der en kraftig udvikling af hvidgul damp/røg, der
kondenserede på væggene af glasrør og bøjninger. Der var en kraftig gasudvikling svarende til 4 - 5 bobler pr. sekund i vaskeflasken.
- Få minutter senere var der ikke mere røgudvikling. Gasdannelsen svarede til ca. 1 boble pr. sekund.
- Herefter var gasdannelsen jævnt aftagende over de næste 1 - 2 timer, og ovnen blev slukket, når der ikke var observeret bobler i ca. 5 min.
- Pyrolyseresten var sort med temmeligt mange koksskaller og støv.
Forsøg nr. |
Temperatur |
Pyrolysetid |
Vægt før |
Vægt efter |
Vægttab |
|
°C |
min. |
g |
g |
% |
2 |
450 |
72 |
15,15 |
6,53 |
56,9 |
3 |
500 |
130 |
24,35 |
10,08 |
58,6 |
4 |
400 |
80 |
17,05 |
8,83 |
48,2 |
5 |
550 |
107 |
16,91 |
6,78 |
59,9 |
6 |
600 |
73 |
15,62 |
6,47 |
58,6 |
Registreringer ved pyrolyseforsøgene
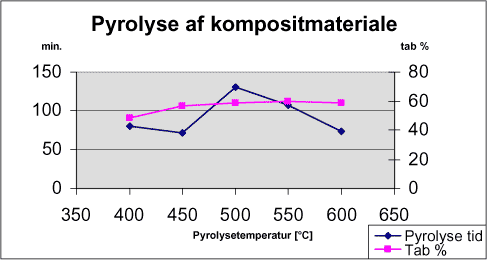
Diagram over pyrolysetid og vægttab
Det ses, at vægttabet af prøverne ligger meget konstant ved alle temperaturer bortset fra i forsøg 4 (400°C), hvor prøven har ligget for tæt på ovnlågen, hvorfor den yderste ende ikke er blevet
færdig-pyrolyseret. Om forsøg 2, 3, 5 og 6 må man konkludere, at pyrolysen er fuldstændig.
Ved pyrolysetiden forstås den tid, der er gået, fra den ønskede temperatur blev opnået, indtil der ikke blev observeret gasbobler i vaskeflasken i ca. 5 min.
Mht. pyrolysetiden er det svært at drage nogle konklusioner. At tiden ikke er så lang ved de 600°C, kan skyldes, at opvarmningsperioden har været længere end ved de lavere temperaturer, og/eller at
reaktionen er hurtigere ved den høje temperatur.
Der er ikke lavet analyser af pyrolyseprodukterne.
2. Logbog
20-05-2003
Kontaktperson: Torben Knudsen, Teknologisk Institut, tlf. 72 20 31 19.
Der skal laves fem forsøg med de tilsendte prøver. Prøverne skal varmes op fra kold ovn til hhv. 400, 450, 500, 550 og 600°C.
Prøverne vejes før og efter pyrolysen.
De pyrolyserede prøver skal sendes til Teknologisk Institut.
Lavet registreringsprogram 'molle.ltc'. Data gemmes i loggen molleMMDDseq.prn
Lavet opstilling i stinkskab.
21-05-2003
Prøver at finde den rigtige indstilling på ovnen.
Forsøg 1
Har kørt første forsøg. Temperaturen har ligget på ca. 500 °C. I starten løb der en væske ned i vaskeflasken, da den smeltede. Røret blev vippet, så det hælder modsat vaskeflasken.
Der måles med to termofølere på begge sider af røret. Der var stor temperaturforskel (200°C). Næste forsøg vil jeg prøve at måle temperaturen inde i røret i stedet for.
Efter 2 timer og 10 min kommer der stadig enkelte gasbobler ud gennem vaskeflasken (ca. 1 hver 1½ min.)
Slukket kl. 14.42, og ladet udstyr blive i ovnen.
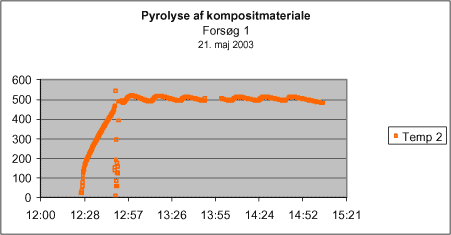
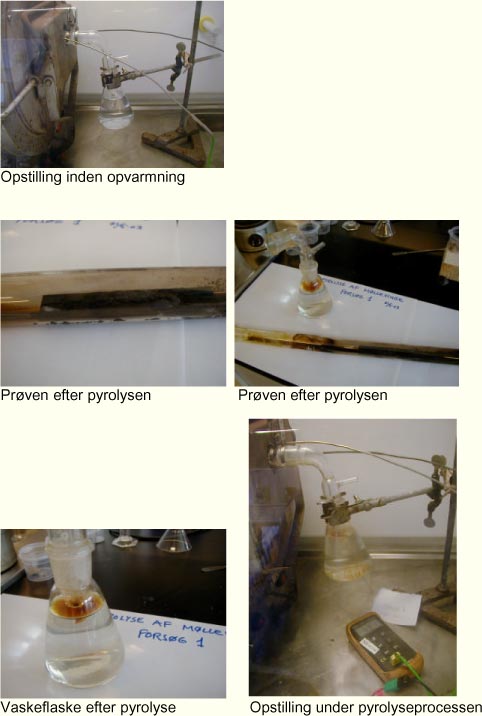
22-05-2003
Har skilt opstillingen fra forsøg 1 ad. Pyrolyseresten vejer 12,03 g. Røret er meget sodet til, og der ligger kondens i rørenden væk fra lågen.
Forsøg nr. 2.
450°C.
Prøven vejer 15,15 g.
Startindstilling på ovnen 3,0. Slutindstilling 3,3.
I modsætning til ved forsøg 1 måles der her temperatur inde i røret. Det tilstræbes at ramme 450°C i røret.
Ved 400°C begynder der at løbe en brunlig væske ned i vaskeflasken. Der er en smule hvidlig røg. Der er ca. 1 boble pr. sekund. Da det stadigt er i opvarmningsfasen, kan det både være pyrolysegas og et
udslag af varmeudvidelse af gassen.
Temperaturen i røret ligger ca. 50°C under den, der er målt i ovnen uden for røret. Dvs. at temperaturen i røret ved forsøg 1 ikke kendes nøjagtig. Det vælges derfor at se bort fra forsøg 1.
Der slukkes for varmen kl. 11.40, da der ikke observeres mere gasproduktion.
Pyrolysetiden ved ca. 450°C var fra kl. 10:28 til kl. 11:40 = 1 time 12 min. Vægt efter pyrolyse: 6,53g.
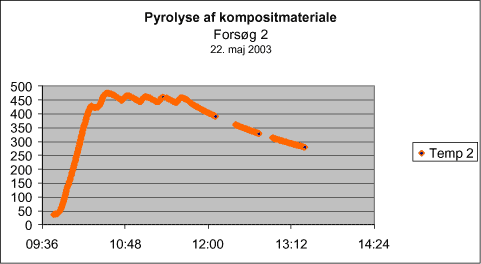
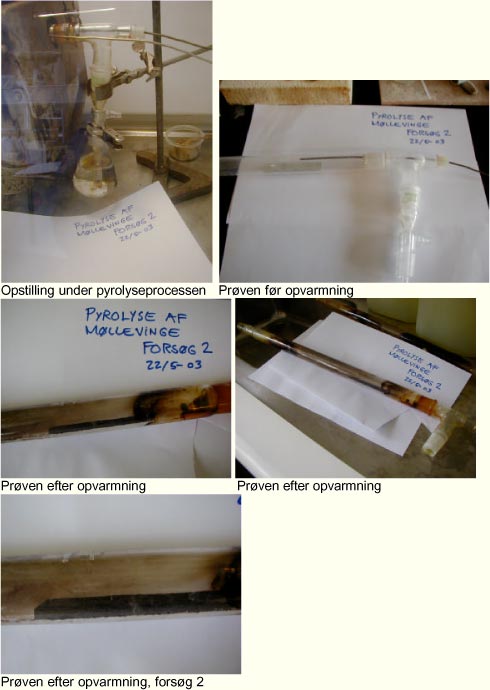
23-05-2003
Forsøg 3.
500°C.
Prøven vejer 24,35 g før pyrolysen. Ovnindstilling 3,7.
Samme opstilling som ved forsøg 2.
Vaskeflasken er ikke renset, men nyt vand er påfyldt.
6.55 |
Opstart |
7.15 |
244°C. Der er ikke observeret væske endnu |
7.22 |
Begyndende væskedannelse |
7.23 |
Loggen blev afbrudt – startet den op igen. |
7.24 |
376°C. Gylden væske løber ned i vaskeflasken. Hvidlig damp/røg i reaktorrøret. Kraftig gasudvikling (4 - 5 bobler pr. sekund) |
7.30 |
Gullig røg/damp fylder det bøjede rør (464°C) |
7.35 |
500°C er nået. Ikke så megen røg mere. Færre bobler (1 - 2 pr. sekund). Den væske der kommer ud, er mørkebrun. |
7.55 |
Ca. 1 boble pr. sekund |
8.03 |
503°C. 1 boble pr. 4 s |
8.40 |
1 boble pr. 8 - 9 s. |
8.55 |
1 boble pr. 30 – 60 s. |
9.25 |
Mellem 18 s og 1 min 44 s |
9.30 |
Koks i dataloggen; temperaturen er 505°C. Det ses af nedenstående diagram |
9.45 |
Slukket for ovnen, da der var over 4 min mellem boblerne |
Skilt opstillingen ad den 25/5-03. Vægt af pyrolyseresten: 10,08 g
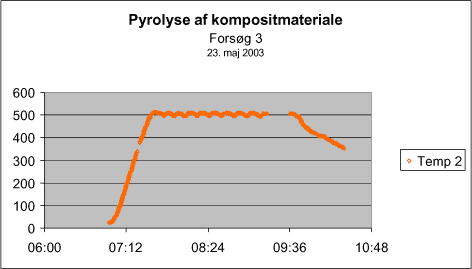
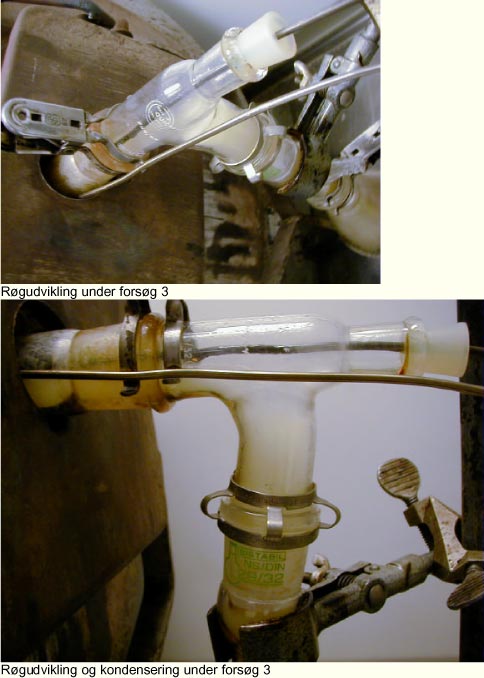
26-05-2003
Gjort klar til forsøg 4.
Samme opstilling som ved forsøg 3.
Alle dele er blevet rengjort.
27-05-2003. Forsøg 4.
400°C.
Prøven vejer 17,05 g før pyrolysen.
Ovnindstilling 3,0.
8:40 |
Opstart |
9:00 |
286°C. Ingen reaktioner observeret |
9:07 |
348°C. Gullig væske i bunden af røret |
9:09 |
360°C. Svag, hvidlig røg/damp. |
9:12 |
390°C. Mørkbrun væske, der løber ned i vaskeflasken. 1 - 2 bobler pr. sekund |
9:30 |
Ca. 400°C. 1 boble pr. s |
9:50 |
Ca. 1 boble pr. 10 s |
10:10 |
Ca. 1 boble pr. 20 s |
10:50 |
Stoppet, da der ikke er observeret bobler i over 5 minutter. |
Pyrolysetid : 1 time 20 min
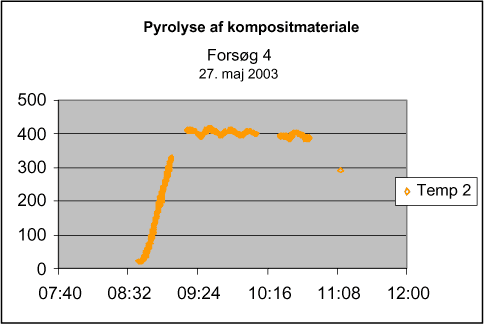
Der har været problemer med dataloggen. Som det ses, er der 'huller', hvor der ikke er blevet registreret noget. Det første hul er dog pga., at termoføleren blev koblet af.
Vægt af pyrolyseresten: 8,83 g.
Den ene ende af staven var ikke pyrolyseret; den må have ligget for langt henne mod åbningen. Røret var meget rent i det område, hvor det har været varmt. I bøjningen efter røret sidder der krystaller på
væggene.
28-05-2003. Forsøg 5. 550°C.
Prøven vejer 16,91 g før pyrolysen.
Rent rør. Øvrige dele som ved forsøg 4.
Ovnindstilling 4,0.
8:40 |
Opstart |
9:07 |
384°C. Gul væske i bunden af rør. Hvid damp/røg |
9:09 |
3 - 4 bobler pr. s |
9:12 |
466°C. Meget hvidgul damp/røg og meget udkondensering |
9:16 |
501°C. En smule hvid røg/damp |
9:22 |
Nået 550°C. 1 boble pr. s |
9:33 |
1 boble pr. 4 - 6 s |
9:50 |
1 boble pr. 5 s |
10:10 |
1 boble pr. 10 - 15 s |
10:23 |
1 boble pr. 40 s |
10:40 |
1 boble pr. 40 s |
11:09 |
Stoppet, da ingen gasudvikling i minimum 5 minutter |
Prøven vejer 6,78 g efter pyrolysen.
Pyrolysetid ved 550°C: 1 time 47 min.
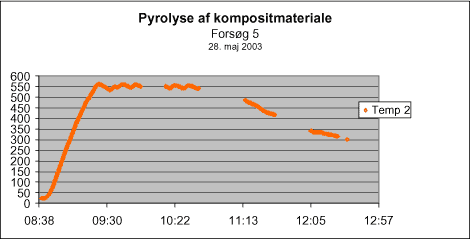
02-06-2003. Forsøg 6. 600°C.
Prøven vejer 15,62 g før pyrolysen.
Rent udstyr.
Ovnindstilling 5,0.
10:42 |
Opstart |
11:07 |
Begyndende væskedannelse og kondensering. 333°C |
11:09 |
Mørk, brunlig væske. En enkelt gul skal i vaskevandet. Hvidgul røg |
11:11 |
Væsken løber ned i vaskeflasken sammen med meget kondensat, der dannes på glasvæggen |
11:15 |
Kun svag røg |
11:18 |
1 boble pr. s |
11:33 |
1 boble pr. 4 s |
11:43 |
Nået 600°C |
12:06 |
1 boble pr. 16 - 18 s |
12:35 |
Der er fra 16 s til 5 min mellem boblerne |
12:56 |
Stoppet forsøget, da der ikke er kommet bobler i over 5 minutter |
Pyrolyse tid: 1 time 13 min.
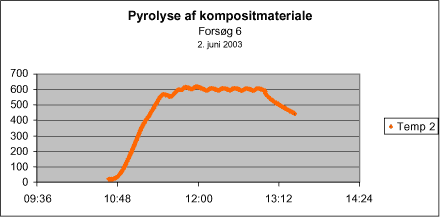
Bilag B Fotos fra første forsøgsserie, termisk forbehandling
Figur 1 Nye glasfibre (reference)
Klik her for at se Figur 1
Figur 2 Glasfibre efter afbrænding ved 450°C
Klik her for at se Figur 2
Figur 3 Glasfibre efter afbrænding ved 550°C
Klik her for at se Figur 3
Figur 4 Tværsnit af polyesterlaminat med regenererede glasfibre, afbrændt ved 550°C
Klik her for at se Figur 4
Figur 5 Tværsnit af epoxylaminat med regenererede glasfibre, afbrændt ved 550°C
Klik her for at se Figur 5
Figur 6 Forsøg 5, glasfibre efter pyrolyse ved 550°C
Klik her for at se Figur 6
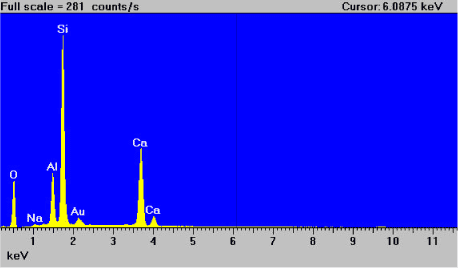
Figur 7 Grundstofanalyse af nye glasfibre
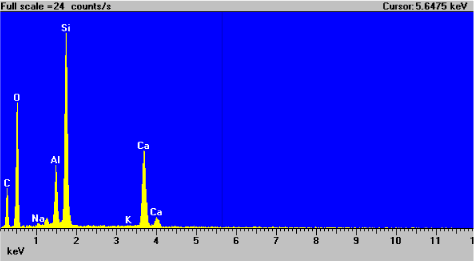
Figur 8 Grundstofanalyse af glasfibre afbrændt ved 550°C
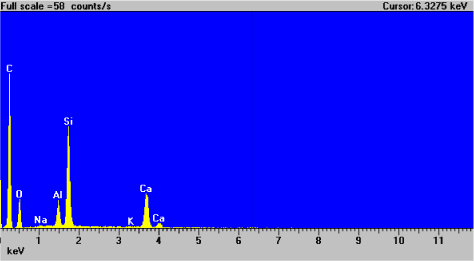
Figur 9 Grundstofanalyse af glasfibre efter pyrolyse ved 550°C
Bilag C Rapport over forbrænding af glasfiberplader
Forgasning af glasfiberplader hos ReFiber ApS
I projektet ”Forbehandling af kompositmaterialer til genanvendelse” har ReFiber ApS udført følgende:
Serie 1:
I juni 2003 modtog vi tre laminater fra EM Fiberglas med diameter 400 mm.
To af pladerne blev forgasset i afsnit 1 af ReFibers pyrolyseovn (1.5 m x Ø 0.9 m)
Prøve |
Vægt |
Tykkelse |
Iltforhold |
Temperatur |
Opholdstid v. 450°C |
I |
1067 g |
4 – 9 mm |
N2 atmosfære |
450°C |
ca. 3 timer |
II |
926 g |
4 – 7 mm |
Luftadgang |
450°C |
ca. 2 timer |
Den lange opholdstid ved høj temperatur reducerer glasfibrenes trækstyrke betydeligt. I en kommercielt drevet ovn (roterovn i ReFibers tilfælde) vil opholdstiden være under 20 minutter, og tabet i
styrkeegenskaber må derfor forventes væsentligt mindre.
Prøver i ovn før og efter forgasning:
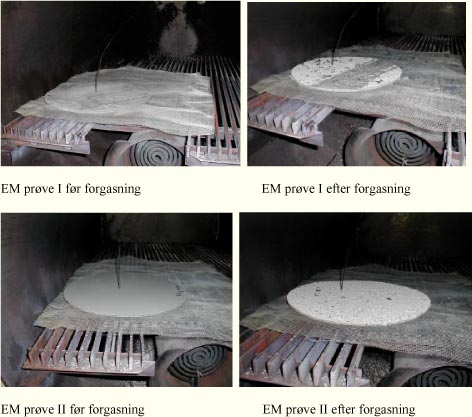
Serie 2:
19. september 2003 modtog vi:
Tre laminater fra EM Fiberglas med dimension 750 mm × 750 mm
Et laminat fra Vestas Windsystems med dimension 250 mm × 500 mm
Pladerne blev forgasset i afsnit 1 af ReFibers pyrolyseovn (1.5 m × Ø 0.9 m)
Pladerne blev anbragt – og transporteret på – et finmasket væv af rustfrit stål
Prøve |
Vægt |
Tykkelse |
Iltforhold |
Temperatur |
Opholdtid v. 450°C |
”Vestas” |
0.8 kg |
3.5 –5.5 mm |
Luftadgang |
max 450°C |
ca. 2 timer |
EM 2.1 |
4.8 kg |
ca. 5.5 mm |
N2 atmosfære |
max 450°C |
ca. 2 timer |
EM 2.2 EM 2.3 |
5.5 kg 4.7 kg |
ca. 5.5 mm ca. 5.5 mm |
N2 atmosfære - |
max 490°C - |
ca. 2 timer - |
Prøverne EM 2.2 og EM 2.3 er forgasset sammen. Se temperaturforhold på grafer herunder.
Den lange opholdstid ved høj temperatur reducerer glasfibrenes trækstyrke betydeligt. I en kommerciel drevet ovn (roterovn i ReFibers tilfælde) vil opholdstiden være under 20 minutter, og tabet i
styrkeegenskaber må derfor forventes væsentligt mindre.
Prøver før og efter forgasning:
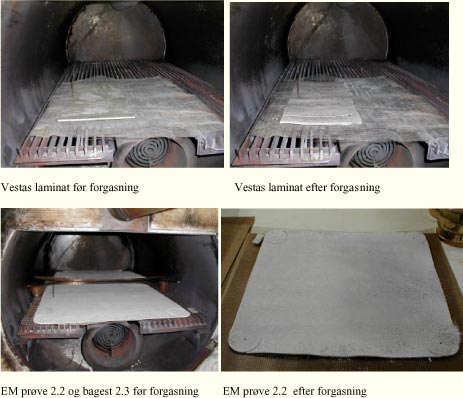
Temperatur målt på prøvens overflade under forgasningen i serie 2:
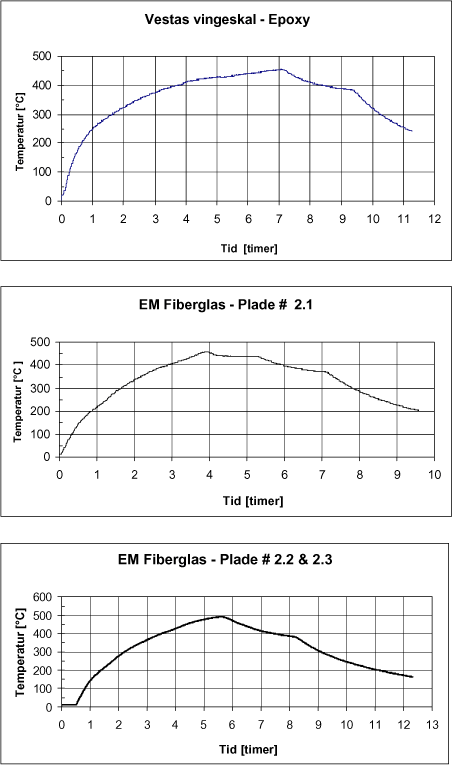
Serie 3:
17. december 2003 modtog vi:
Tre laminater fra EM Fiberglas med dimension 370 mm × 1500 mm
Pladernes længde blev reduceret med 200 mm før placering i ovnen.
Pladerne blev forgasset samtidigt i afsnit 1 af ReFibers pyrolyseovn (1.5 m × Ø 0.9 m)
Pladerne blev anbragt – og transporteret på – et finmasket væv af rustfrit stål.
Prøve |
Vægt |
Tykkelse |
Iltforhold |
Temperatur |
Opholdtid v. 500°C |
EM 3.1
EM 3.2
EM 3.3 |
4.2 kg
4.2 kg
4.2 kg |
ca. 5.7 mm
ca. 5.7 mm
ca. 5.7 mm |
N2 atmosfære
-
- |
max 516°C
-
- |
ca. 1.5 timer
-
- |
Prøverne EM 3.1, EM 3.2 og EM 3.3 er forgasset sammen. Se temperaturforhold på graf herunder.
Temperaturen i serie 3 var ca. 50 °C højere end temperaturen i serie 1 og 2, hvorfor glasfibrenes styrke må forventes at blive en del lavere i materialet fra serie 3.
Den lange opholdstid ved høj temperatur reducerer glasfibrenes trækstyrke betydeligt. I en kommercielt drevet ovn (roterovn i ReFibers tilfælde) vil opholdstiden være under 20 minutter, og tabet i
styrkeegenskaber må derfor forventes væsentligt mindre.
Prøver før og efter forgasning:
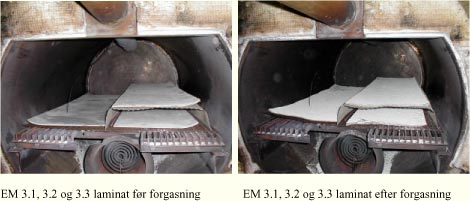
Temperatur målt på prøvernes overflade under forgasningen i serie 3:
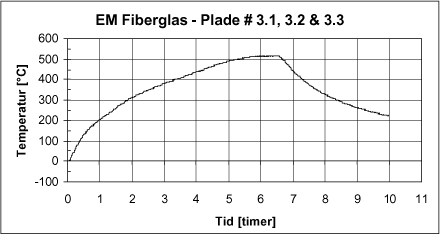
ReFiber den 19. Februar 2004 Erik Grove-Nielsen
| Til Top | | Forside |
Version 1.0 Maj 2005 • © Miljøstyrelsen.
|