| Front page | | Contents | | Previous | | Next |
Assessment of Mercury Releases from the Russian Federation
5 Turnover of Mercury by Waste Treatment
5.1 Mercury Recycling
5.1.1 Mercury-containing waste
Data on the amounts of mercury-containing waste (manly industrial waste) generated by now in Russia, as published in literature, testify that such amounts are very high.
Thus, by different assessments (Klimov et al, 1999; Report on Research Work ..., 1999), the total amount of such waste makes 1.1 million tonnes. Among such waste, the bulk of
mercury-containing waste (58% by weight) has the mercury content of 10-30 mg/kg; 30% of the waste has the mercury content of over 5000 mg/kg; and about 125 have metal
concentrations at 100-5000 mg/kg. According to other data (http://www.greenpeace.ru/gpeace/43520/gp_article_t...), in Russia there is about 750,000 tonnes of
mercury-containing waste; according to (Donskykh, Skitskiy), this content is about 650,000 (with the mercury content from 200 to 750,000 mg/kg); annually about 11,000
thousands new waste are generated. The most significant volumes of stored mercury-containing waste and, hence, high levels of habitat pollutions are in the regions of the country
where large nonferrous metallurgy, chemical, wood pulp and paper and gold mining enterprises are located.
For example, near Kirovo-Chepetsk Chemical Enterprise (the city of Kirovo-Chepetsk, Perm Oblast) there are temporary dumpsites and deep-burial dump fields which house
409,000 tonnes of mercury-containing waste (Polskykh ...). In Irkutsk Oblast, soils at industrial enterprises producing chlorine and caustic accumulate over 1,000 tonnes of
mercury, and more than 2,000 tonnes of metal can be found in slurry accumulating sites (the State Report "On Environmental Condition in the Russian Federation in 2002"). In the
coastal area of the Northern Dvina River mouth, 3,200 tonnes of mercury-containing waste from Archangelsk Wood Pulp and Paper Enterprise have been recently dumped;
Krasny Bor dumpsite (Leningrad Oblast) located over 100 tonnes of mercury-containing waste (http://www.greenpeace.ru/gpeace/43520/gp_article_t...). In the territory of the
former Amur Wood Pulp and Paperboard Enterprise (city of Amursk, Khabarovsk Krai) about 300-500 tonnes of mercury-containing waste are kept in containers and on open
sites (http://www.3e.opec.ru/news; http://www.khv.ru/MD/2001/12720/ob.htm). According to other data (Parliament Gazette ...), the old (now unused) stores of this enterprise
house about 4,400 tonnes of mercury-containing waste.
At the end of 1990's, Russian nonferrous metallurgy enterprises houses in their territories over 63,000 tonnes of slurry containing about 155 tonnes of mercury (Report on the
Research Work ..., 1999). In Northern Osetia (the area of dumpsites of 250 ha) now accumulate about 9 million tonnes of enrichment rejections (tailings) from Mizurskaya and
Fiagdonskaya enrichment enterprises and waste from the metallurgical enterprises Electrozink and Pobedit (the city of Vladikavkaz), in which the estimated weight of mercury is
about 110 tonnes (Satsayev, 2002). Chelyabinsk electrolyte sink enterprise houses, in its territory, about 40 tonnes of mercury and selenium slurry
(http://www.chrab.chel.su/archive/17-10-97/1/RE12.D... (16.10.1997)).
Significant amounts of mercury-containing slurry are located in the vicinity of gold-extracting enterprises. For example, the rejection stores at Semenovskaya factory (Southern
Ural) contain totally about 60 tonnes of mercury (Mustafin et al., 1998). In the township of Solovyovka (Tynda District, Amur Oblast), the heavy concentrate enrichment
installation houses, in its stores, about 15,000 m3 of mercury-containing slurry (http://www.mhg.ru/proekt/doklad/99/region/am/chapt...); in the township of Tokur (Amur Oblast),
about 30 to tonnes of mercury are stored in unattended store facilities (The Priamurskiye Vedomosti Newspaper ...).
According to Business Books and advertising publications of the recent years, in Russia there are several enterprises that are engaged, to different degrees, in refining of spent
mercury and processing of industrial mercury-containing waste. However, only two of such enterprises operate at a rather full scale and regularly supply secondary mercury and its
compounds to the local markets: they are NPP Kubantsvetmet CJSC and Mercom Ltd.*
5.1.2 Scientific and Production Enterprise Kubantsvetmet CJSC
NPP Kubantsvetmet CJSC is located in the township of Kholmsky (Abinsk District, Krasnodar Krai). In 1998, NPP Kubantsvetmet CJSC performed (using its own resources)
repair and rehabilitation work at the metallurgy plant, which, in the past, belonged to Krasnodarsky Rudnik Ltd. and developed a range of technological instructions regulating
processes for processing of mercury-containing waste, mercury refining and production of mercury compounds. This work was done within the Federal targeted programme
"Waste".
Some time ago, Krasnodarsky Rudnik Ltd. operated, basically, in the area of Sakhalin mercury deposits (quartz-dikkit-cinnabar type), located not far from the township of
Kholmsky. In 1974-1992, about 500 tonnes of metallic mercury was produced from ores extracted in this deposit field. In 1990, the underground part of Sakhalin deposit was
removed from use (due to economic inexpediency of its further development); in 1993 work on the quarry processing the ground-surface part of the deposit was terminated. In
1993-1995, Krasnodarsky Rudnik enterprise was processing ore extracted in the previous years (about 30 tonnes of mercury was produced); beginning from 1992, there has
been sporadic production of secondary mercury (from mercury-containing waste); during 1992-2001, this enterprise produced over 98 tonnes of secondary mercury (including
about 65 tonnes over the period of 1999-2001).
At present, NPP Kubantsvetmet CJSC performs the following operations with mercury-containing waste:
- processing of different mercury-containing industrial waste;
- processing mercury-polluted soils and construction waste;
- disposal of mercury-containing luminophor concentrate;
- de-mercuration of spent mercury lamps;
- disposal of spent and rejected mercury-filled devices;
- refining of unconditioned (spent or black) metallic mercury;
- production of different mercury compounds;
- production of special highly clean metallic mercury.
Activities of NPP Kubantsvetmet CJSC include transportation of waste from places of its generation (placement) in special metal containers for sorting of every waste batch,
separation of groups of metals fit for processing or decontamination in technological devices and extraction of commercial mercury, production of mercury compounds,
grouping of waste generated during activities of the enterprise for its further safe disposal (burial) and/or reuse.
Technological schemes applied to process mercury-containing waste, used at NPP Kubantsvetmet CJSC, make it possible to consider all waste delivered for disposal as a
sort of raw material, while by-products generated as a result of their processing, in turn, are used as secondary raw materials in other production facilities.
Technological and production operations are performed observing conditions and requirements contained in regulatory, technical, sanitary and hygienic documents (State
Standard GOCST 30772-2001; GOST 30773-2001; GOST 30774-2001; GOST 30775-2001; GOST 4658-73; Inter-sectoral rules on protection ...; Melnikov, 1974;
Mercury. Regulatory ..., 2001; Mercury. Specifications ..., 1977) and technological instructions (Technological Instructions ...).
Activities of enterprises are also regulated by:
- Licenses giving the right perform activities on handling hazardous (including mercury-containing waste) waste (like collection, use, decontamination, transportation,
placement, storage), issued by RF Ministry of Natural Resources;
- Licenses giving the right to perform activities on collection, processing and sale of ferrous scrap metals, issued by the Committee on Licensing of Krasnodar Krai;
- Licenses giving the right to use and operate production facilities producing melted ferrous and nonferrous metals and alloys of them, issued by the Federal Mining and
Industrial Supervision Committee of Russia;
- Licenses giving the right to transport cargo by motor vehicles in the Russian Federation, issued by RF Ministry of Transport.
The chemical analytical laboratory of NPP Kubantsvetmet CJSC has the Certification of Accreditation, issued by the State Committee on Standardisation and Metrology of
the Russian Federation.
The enterprise also includes the environmental service, the labour protection and safety department, as well as the section on technical control over raw material processing.
In the course of processing of mercury-containing waste, production of commercial metallic mercury and mercury compounds, there is performed relevant technological
control over processes and their parameters, the composition of processed raw materials, interim products ands final products, the material production balance is assessed
as well as technological performance indicators of the TVP-1 furnace and other equipment.
The total number of personnel at NPP Kubantsvetmet CJSC is more than 160 persons, including technologists and metallurgists who have long-standing experience of work
at large mercury and enterprises and mercury and antimony enterprises of the FSU.
Main technological schemes, equipment and production operations related to processing of mercury-containing raw materials
The production structure of NPP Kubantsvetmet CJSC includes the following:
1) The administrative and production facilities (with the total area of about 6 ha) and the adjacent railway dead-end track;
2) The industrial area (about 39 ha), including the following main facilities:
- a metallurgic plant, including two tubular rotary ovens, gas release and dust cleanup systems, mercury condensation and refining devices, slurry storage places, cinder sites;
the first TVP-1 oven is used for processing the mercury-containing raw materials by oxidation roasting, followed by release of mercury from the gaseous phase
(technological gases); the second TVP-2 oven is used for production of lime;
- an area for conditioning of mercury-containing raw materials for metallurgic processing;
- an area for production of mercury compounds;
- an area for production of highly cleaned mercury (4 plants using multiple-stage distillation with electrical discharge cleaning);
- an area for de-mercuration of high-pressure mercury lamps;
- an area for disposal of metal mercury-filled devices;
- an area for disposal of metal mercury-filled devices;
- an area for disposal of glass mercury-filled devices;
- an area for maintenance and repair of technological equipment;
- an area for technical control of mercury-containing raw material processing;
- a chemical analytical laboratory; and
- a finished products warehouse.
The annual production capacity of the TVP-1 oven (as regards raw material) is 36,000 tonnes; of the plant for de-mercuration of tubular mercury lamps is more than 1 million
pieces; of the plant for cleaning of unconditioned (spent) mercury I 240 tonnes of commercial metal; of the area for production of mercury compounds is 30 tonnes (as commercial
products); and of the plant for production of highly clean mercury is 15 tonnes of metal.
NPP Kubantsvetmet CJSC has the following required equipment and technologies for decontamination and disposal of the following types of mercury-containing production and
consumption waste that are included into several groups as regards their features and conditions of their processing (Table 5.1). The bulk of waste is processed by means of the
tubular rotary oven TVP-1.
The design of the tubular rotary oven
The tubular rotary oven TVP-1 is a metal cylinder (body) 6 with the diameter 1.6 m and the length 14 m, installed at a gradient of 3-4 and lined with refractory bricks. The body of
the oven is supported by bandage elements 5 on rollers 13, on which it is rotated at the velocity of 0.6-2 RPM, by means of the driving mechanism 14; this velocity is regulated by
means of a 4-speed electrical motor (Fig. 5.1). In the bottom part, the body abuts the furnace chamber 4, and in the top part it abuts the dust chamber 8. These chambers
represent metal frames, lines on inside with refractory bricks and having openings for connection of the oven body.
Table 5.1 Types of mercury-containing waste processed at NPP Kubantsvetmet CJSC
Group |
Type of waste |
Basic equipment |
Main waste suppliers in 200-2002 |
1 |
Spent catalyst (vinyl chloride production waste) |
Tubular rotary oven TVP-1 |
Khimprom OJSC (City of Volgograd); Plastcard OJSC (City of Volgograd); Azot
NAK (City of Novomoskovsk) |
1 |
Slurry from 1-amino anthrachion production (production terminated in 2000)
|
Tubular rotary oven TVP-1 |
Khimprom JSC (City of Cheboksary, Republic of Chuvashia) |
1 |
Mercury sorbent (activated carbon, KPR brand, etc.) |
Tubular rotary oven TVP-1 |
Sintez OJSC (City of Dzerzhinsk); Lisma OJSC (City of Saransk); Merkuriy EP
(City of St. Petersburg); Chemical enterprise named after Konstantinov (City of
Kirovo-Chepetsk) |
1 |
Concentrate of luminophor generated during mercury lamp disposal |
Tubular rotary oven TVP-1 |
Ecorecycle Ltd. (Town of Noginsk, Moscow Oblast); NPP Ecotrom Ltd. (City of
Moscow); Volgokhimtorg OJSC (City of Volgograd) |
1 |
Graphite waste |
Tubular rotary oven TVP |
Usolyekhimprom OJSC (City of Usolye-Sibirskoye, Irkutsk Oblast) |
1 |
Mercury compounds |
Tubular rotary oven TVP |
Mainly organisations and enterprises of Krasnodar Krai* |
1 |
Soils and construction materials contaminated with mercury |
Tubular rotary oven TVP |
Mainly organisations and enterprises of Krasnodar Krai* performing de-mercuration
of buildings and areas ** |
2 |
Galvanic elements (spent and rejected) |
Tubular rotary oven TVP |
Energia OJDSC (City of Yelets); Signal (City of Chelyabinsk) |
3 |
Tubular luminescent lamps (types LB, LD, etc.) |
Ecotrom-2 plant |
Organisations and enterprises of Krasnodar Krai |
4 |
High-pressure mercury lamps (DRL types) |
According to the adopted scheme |
Organisations and enterprises of Krasnodar Krai |
5 |
Metal devices filled with mercury |
According to the adopted scheme |
Organisations and enterprises of Krasnodar Krai |
6 |
Glass devices filled with mercury (spent and rejected) |
According to the adopted scheme |
Organisations and enterprises of Krasnodar Krai |
7 |
Spent respirators, used special clothes, fabric waste of mercury filtration |
Tubular rotary oven TVP-1 |
Organisations and enterprises of Krasnodar Krai |
8 |
Unconditioned metallic mercury (spent or black) |
Refining installation |
Different organisations and enterprises, including from Krasnodar Krai |
9 |
Gas-cleaning dust and slurry |
Tubular rotary oven TVP-1 |
Cleaning of technological waste |
10 |
Paperboard waste from mercury lamp packages |
Tubular rotary oven TVP-1 |
Organisations and enterprises of Krasnodar Krai |
- For example, in 2002, about 217 kg of chemical reagents containing mercury were received form the Kuban hydrometeorological land-reclamation party;
- ** in 2002, the PASF "Rtutservice" Ltd. (City of Krasnodar) generated 4.69 tonnes of mercury-containing soils;
- *** in 2002, about 2775 kg of unconditioned (black) mercury for received for processing from Belarus (UP "Beltsvetmet") and more than 600 kg from different enterprises
of Krasnodar Krai.
The furnace chamber is installed above the hopper for cinders (roasted raw materials) 1. In it, fuel (natural gas with the flow rate of 26.6 m3 per 1 ton of raw materials) is burned
through the nozzle 2; the flame is fed through the centre to the oven body. The upper (dust) chamber is used for interface of the rotary body of the oven with the stationary gas
duct. The pipe feeder of raw material 11 is laid through a hole in the end wall of the dust chamber into the body; it is used to feed raw material to the oven. The feeder is installed
between the hopper 10 of raw material and the oven. The oven is counter-flow oven: the raw material fed to the oven is moved, during rotation of the body, from the upper end to
the lower end, while gases, on the contrary, are moved from the furnace chamber to the upper end of the body and are released through the upper (dust) chamber 8 to the gas duct
9, whereby they are fed to de-dusting area. When gases pass from the oven to the gas duct through the dust chamber, the large dust particles are precipitated in the latter (the dust
brought out of the oven by the gas flow). To reduce the removal of dust from the oven to the gas system, a minimum pressure is built in the oven, which creates a danger of leakage
of technological gases through adjacent elements between the rotating oven body and the stationary chambers. To prevent gas leakage, these adjacent elements has special seals
12.
Figure 5.1 The layout of the tubular oven
Click here to see the figure.
1 – hopper for cinders; 2 – nozzle (burner); 3 - umbrellas; 4 - furnace; 5 – bandage elements; 6 – oven body; 7 – driving gear; 8 – dust chamber; 9 – gas duct for removal of
technological gases; 10 – hopper for raw materials; 11 - feeder; 12 – upper and lower seals; 13 – supporting rollers; 14 – driving mechanism for oven rotation
Temperature of processed raw material, when it is moved to the oven body, is increased, reaching its maximum near the unload end. Roasted raw material (the so-called cinders) is
fed to the cinder hopper located under the furnace chamber, where it is kept for a definite time, dur8ing which the released mercury vapours together with the hot air are sucked
from the hopper via the furnace chamber back into the oven. To prevent possible loss of vapours, the structure of the connections between the oven, the furnace and the hopper
fore cinders is reinforced by placing the lower seals.
General layout of the pyrometallurgical mercury production
The metallurgical processing of raw materials is effected by means of a regular scheme used in mercury production (raw material roasting – mercury vapour condensation –
mercury slurry processing), which was modernised by specialists of NPP Kubantsvetmet CJSC keeping in mind the conditions for processing of different groups of
mercury-containing waste (Fig. 5.2).
Before roasting in the oven, the raw material is loaded to the receiving hopper, wherefrom it is fed by a tape conveyor (3 m long, 0.8 m wide, 40 t/h capacity) for defragmentation
(to get pieces of 50-70 mm), performed using a special type crusher CM-741 (with the size of the loading slit 6 x 9 cm and the capacity 40 t/h). Dust generated during this process
is removed by means of the local ventilation system, accumulated in a tank with water and then fed for renewed roasting to the TVP-1 oven. The thus prepared raw materials is fed
by means of a tape conveyor (the tape length is 38.96 m and the width is 0.65 m) to the dispenser hopper, wherefrom it is fed by means of a tape feeder (1.8 m long; the tape
width 0.8 m, the capacity up to 6 t/h) to the TVP-1 oven.
Raw material is roasted at a temperature not less than 500 C, at which mercury contained in raw material is sublimed and transferred to vapour condition (technological gases). The
duration of material in the oven is 1.5 hours on the average. When required, the period of roasting can be regulated by the oven rotation velocity. Roasting is going on in an
oxidising environment, i.e. when free oxygen is present. Oxidising conditions in the oven are maintained by means of 30% air excess, as required for fuel combustion. If the raw
material includes other volatiles, then they are sublimed, fully or partially, as well as moisture contained in the roasted raw material. Besides, dust is also turned into gases, in a
definite quantity, just as gas products generated during fuel combustion, and the excessive oxygen and nitrogen fed to the technological process with the air.
Figure 5.2 Principal diagram of the pyrometallurgical mercury-production process
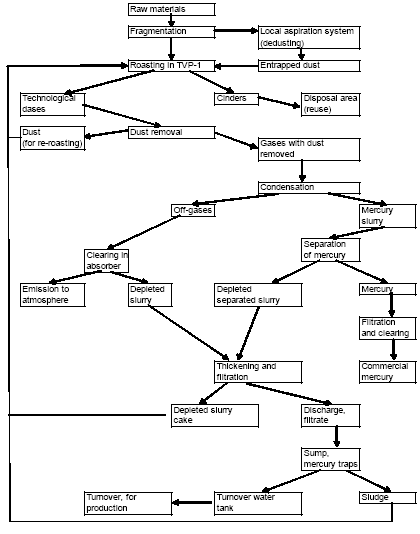
Roasted raw materials or cinders with the temperature at the oven exit at about 500 are fed to the cinder hopper. During unloading of hot cinders ascending hot air flows are
generated as well as dusting; to reduce this phenomenon, cinders are normally are kept in the hopper for 4-6 hours to bring their temperature below 800 C. Experience shows that
in most cases the mercury content in cinders does not exceed 25-26 mg/kg. Cinders are removed to dumpsites by dump trucks.
Technological gases generated during roasting of raw materials with the temperature at the oven exit not less than 500 C are fed, via a special gas duct, to a group cyclone, where
they are cleaned from dust. When cyclones operate efficiently, they entrap up to 90% of dust from gases, after which this dust is returned back for a new roasting. All gas ducts
from the oven to the devices used to remove dust, the devices themselves as well as gas ducts thereof are equipped with heat-insulation and heat-resistant materials.
After removal of dust, technological gases carrying mercury vapours are fed for cooling to the tubular condenser refrigerator where they are cooled down to 30 C and turned into
liquid (Fig. 5.3). The general principle of the condenser operation is as follows:
Figure 5.3. Diagram of the condenser refrigerator for condensation of mercury from technological gases
1 - tap; 2 - receiver; 3 – gas duct; 4 – frame structure; 5 – metal pipes (standpipes); 6 – upper holes (lids); 7 - piping; 8 – lower ends of T-pipes (discharge); 9 – T-pipes
Click here to see the figure.
Technological gases with dust removed are fed via the gas duct 3 and further along the condenser loops. Condenser loops include vertical metal pipes (standpipes) 5, fixed to the
frame structure 4, arranged in pairs and connected in the top area by means of U-shaped piping 7 (elbows). In the lower part, every pair is connected to the neighbouring pair by
means of T-pipes 9. Lower ends of T-pipes (discharge pipes) 8 are immersed into water in the receiver 2, installed in the bottom along the entire loop. Technological gas, fed to
the first standpipe, under impact of rarefaction generated by the fan installed after the condenser, passes stage-by-stage through the entire pipe system, ascending and descending;
then it passes to the neighbouring pair, and further on, till the end of the loop. To speed up cooling of technological gases inside the condenser, the standpipes that are the last in the
row are sprinkled with water fed through sprinklers (sprays) installed in the upper section of the standpipes. Besides, a definite amount of water is also fed to the standpipes, which
facilitates effective cooling of the dust contained in technological gases.
In the process of condensation, starting in the layer near the walls, mercury drops are generated; the largest drops flow down to special receivers (condenser troughs), located in
the lower part of the cooling device; part of the drops precipitate on its inside walls while the finest drops (aerosols) quite from the condenser with the outgoing gas flows exiting the
condenser. Condenser entraps not only metallic mercury, but also its compounds, the water that is accumulated here, oxides of some chemicals as well as a substantial part of dust
that has not been entrapped earlier. As a result, the condenser trough collects not clean mercury but the so-called slurry, i.e. a mixture of metallic mercury, its compounds, dust,
particles of unburned fuel and water. The amount of metallic mercury in the slurry varies from 20 to 80%, depending on a range of factors, like: the content of metal in the initial raw
material, the efficiency of the dust-entrapment system, etc.
The generated slurry is fed (by pumps) to the so-called mercury separation, which is effected in a hydraulic cyclone, wherein centrifugal forces result in coagulation and separation)
of metallic mercury from moisture and lighter solid products of roasting. During separation of metallic mercury the so-called depleted slurry is generated which is fed to the
thickener and then to the vacuum filter, wherefrom the dewatered mass, i.e. the depleted slurry cake (12-15% of humidity) is fed (after blending with lime) to the oven for a new
roasting so as to remove the remaining mercury.
Technological gases exiting from the condenser refrigerator (emitted off-gases) always contain some quantity of mercury vapours which corresponds to the equilibrium content
predetermined by the gas temperature, i.e. the higher the temperature, the greater the amount of mercury in them (Table 5.2). It is precisely for this reason that it is always
preferable to cool down the gases in the condenser to lowest possible temperatures (normally below 30 C). Beside mercury vapours, the released gases, removed from the
condenser, include also aerosols of metallic mercury, water steam, fine dust particles, ash and some other admixtures.
Table 5.2 Content of mercury in saturated vapour depending on the temperature (Melnikov, 1974)
Temperature, °C |
10 |
20 |
30 |
40 |
50 |
60 |
70 |
80 |
90 |
100 |
Mercury, mg/m3 |
5.64 |
13.38 |
29.81 |
62.8 |
126.6 |
234.9 |
452 |
807 |
1,396 |
2,338 |
Emitted off-gases are fed for additional (sanitary) cleaning, performed in a two-stage absorber. The first stage represents a spraying device (SD), wherein the bulk amount of dust
and some mercury are entrapped. Then the gases are fed to the ball-packing device (BPD), wherein an alkaline (lime) solution is used as a spray liquid. Dust entrapped by the
absorbers (depleted slurry) also is fed to the oven for a new roasting.
Gases purified in the absorber are emitted to atmosphere through the enterprise stack 30 m high (it may be over 60 m depending on the terrain), which secures the required dilution
of gases with air. Normally, up to 2,400 m3 of such gases are generated per tonne of processed raw materials, on the average; in normal conditions of the technological process,
the mercury content in the gases makes not more than 25.4 mg/m3, i.e. at present the specific emission of mercury to atmosphere makes 61 g per 1 tonnes of raw materials
processed in the TVP-1 oven. Maximum allowed emission of mercury for the metallurgical enterprise NPP Kubantsvetmet CJSC " is set at 80 kg/year. According to data
(Methodological ..., 1989), the content of dust (after cleaning) in emitted gases of mercury production (ore processing) usually does not exceed 5-6 g/m3.
At the metallurgical enterprise NPP Kubantsvetmet CJSC, they use a circulating water-supply system with the daily water makeup (15 m3/day for technological needs, and 5
m3/day for communal and other needs; the water if supplied from a special metal tank). Production circulation water is fed to the sump, passing through mercury traps, and then is
fed to the return water tank, wherefrom it is returned to the technological process. The generated sludge is fed to the roasting oven TVP-1. Communal and other non-production
wastewater is discharged to the sewerage system.
Mercury refining
The separation process allows getting metallic mercury that is filtered through a cotton belting and military cloth. As a rule, mercury obtained in this way is, without any additional
processing, a commercial product, P3 brand (Russian abbreviation), used for production of mercury compounds and/or supplied to users. Further required mercury cleaning is
performed at the mercury refining plant, manufactured by specialists of NPP Kubantsvetmet CJSC, which is based on using a hydrochemical method.
About 0.05 kg of cotton belting and 0.05 kg of military cloth are used to clean 1 ton of mercury. Soft waste generated after the cleaning and refining of mercury (about 3 kg per
year, with the mercury content up to 2%) is accumulated in acid-resistant, tight vessels and then burned in the oven TVP-1.
The composition, conditions of acceptance, analysis, transportation and storage of mercury are defined in the State Standard GOST 4658-73, which specifies metals used for
production of semiconductor materials, for use in vacuum electrical engineering, manufacture of instruments, mercury and zinc current supply sources, various reagents and
pharmaceutical preparations, as well as in chemical, metallurgical and other sectors of industries (Table 5.3).
Table 5.3 Chemical composition of mercury (GOST 4658-73)
Requirements to the composition |
Mercury brand |
|
P0 |
P1 |
P2 |
P3 |
Mercury, %, minimum |
99.9997 |
99.999 |
99.99 |
99.9 |
Non-volatile residue, %, maximum |
0.0003 |
0.001 |
0.01 |
0.1 |
In particular, mercury of brands P1, P2 and P3 (Russian designation letters) is poured into special steel cylinders (ER-2,75; manufactured at Pervouralskiy pipe manufacturing
enterprise), rated 34.5 kg of metal. Each cylinder is tightly closed by a screwed cap with a gasket from fluoride plastic material of at least 0.15 mm thick. When cylinders are
stored for a long time, seals are attached to them. P0 mercury is poured into cylinders made from thick-wall glass with a capacity of 5 kg of metal. Mercury P1 and P2 can be
poured into cylinders made from thick-wall glass, after which these cylinders are closed with a metal lid and a gasket from plastic material. P1 mercury, designed for medical use, is
poured into vials containing 50 g of metal; these vials are plugged with polyethylene plugs and lids. Each vial is placed into a polymer can 30 cm3 and sealed with alignine. The
warranty storage period for P1 and P2 mercury is two years, for P0 mercury – three years, for P0 mercury – unlimited.
Conditions and specific features of processing of mercury-containing waste
The technological scheme for processing of each group of mercury-containing waste has its specific features, depending on the waste generation source, and its substances and
consistency (see Table 5.1).
Processing 1st group waste
Processing of this waste, which includes spent mercury catalysts (waste from vinyl chloride production), sorbent (activated carbon KPR brand, etc.), mercury compounds,
production sludge from 1-amine anthrachion, soils and construction materials polluted with mercury, graphite waste, luminophor concentrate, etc., is generally performed using the
single technological scheme, which includes the following main technological operations:
- blending of raw materials, i.e. adding of lime for neutralizing the acid residue, in the weight ratio of 1.0:0.8 (raw material : lime);
- heating of the blend in a tubular rotary oven to the temperature of at least 500 °C by flue gases so as to convert mercury contained in the initial raw material into a gaseous
phase;
- dedusting of the vapour and gas mixture in a group cyclone;
- condensation of mercury in a condenser refrigerator;
- accumulation of mercury slurry in condenser troughs;
- separation of metallic mercury in a hydraulic cyclone;
- cleaning of mercury from admixtures so as to obtain commercial metal;
- cleaning of off-gases from mercury in absorber;
- unloading of cinders from the oven to the cinder hopper (cinder output makes 94-96% of the roasted blend weight);
- removal of cinders to the cinder dump or the area for processing of scrap lead in a reflector oven wherein they are used as reducer agents.
Fig. 5.4 shows, as an example, the scheme for processing of waste from vinyl chloride production (spent mercury catalyst), with the average mercury content being 3,000
mg/kg (30 kg of metal per tonne of waste).
It was planned that since January 2003 cinders generated during roasting of mercury catalyst, sludge generated during production of 1-amino anthrachion and graphite waste
would be transferred to enterprises processing scrap ferrous and nonferrous metals, where they would be used as reducing agents and flux. Cinders from roasting of soils
and construction mater8ials would be used for levelling of roads of IV and V classes.
Figure 5.4 Scheme of processing of waste generated from vinyl chloride production facilities (spent catalyst) in TVP-1
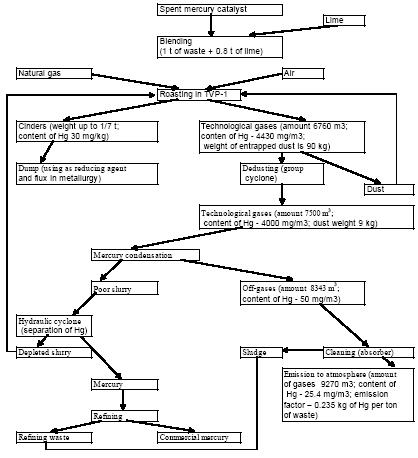
It is planned that from 2003 NPP Kubantsvetmet CJSC will be processing annually 600 tonnes of waste from vinyl chloride production, 50 tonnes of mercury sorbent
based on activated carbon, 50 tonnes of mercury-containing soils and construction waste, 60 tonnes of graphite waste, 30 tonnes of sludge from 1-amine anthrachion
production. The considered technological scheme can be used also for processing waste generated at facilities producing V2 vitamins (activated carbon sludge),
sludge from chlorine and alkaline enterprises and other types of secondary mercury-containing raw materials that have similar conditions of generation, compositions
and consistency.
Disposal of galvanic elements
Disposal of spent and rejected galvanic elements (mercury-zinc and mercury-containing elements) and batteries is performed using the same technological scheme, i.e.
roasting in the oven TVP-1, but with separate loading of mercury elements or mercury-containing elements and batteries and without blending of raw materials with
lime (Fig. 5.5).
Waste from such production process includes cinders (roasted element bodies), containing about 45% of iron and 55% of zinc; concentration of mercury in such
elements does not exceed 0.0002% by weight. Cinders are placed into metal drums and sold to organisations that are specialised in collection and processing of scrap
ferrous and nonferrous metal. The weight of generated cinders is about 10-20 t/year.
Figure 5.5 Scheme of disposal of chemical current supply elements in TVP-1
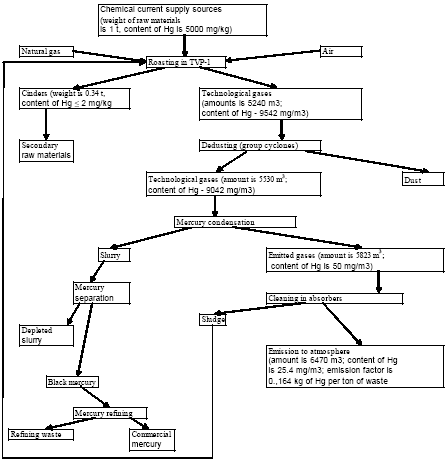
De-mercuration of tubular luminescent lamps
Processing of mercury luminescent lamps (types LB, etc.), performed by using the vibration pneumatic plant Ecotrom-2, includes their mechanical destruction and
separation under discharge of glass fractions (broken glass), aluminium bases and luminophor, i.e. the basic mercury concentrates. Characterisation of the basic units
of this plant is given in Table 5.4, while the technological process scheme is given in Fig. 5.6.
Table 5.4 Basic technical characteristics of the plant Ecotrom-2
Name of the device and its characteristics |
Name and composition of the environment |
Flow rate per operation |
De-mercuration device, 1200 lamps/hour |
Fragmented lamp components |
360 kg/hour |
Cyclone, diameter 200 mm, length 800 mm |
Air containing luminophor and glass dust |
360 nm3/hour |
Sleeve filter, 9 sleeves, diameter 180 mm, length 2000 mm |
Air containing luminophor and glass dust |
360 nm3/hour |
Cassette filter, 4 filters |
Air containing luminophor and glass dust |
360 nm3/hour |
Luminophor collectors, volume 50 l, diameter 350 mm |
Mercury-containing luminophor |
40 l |
Working absorber, diameter 800 mm, sorbent, containing activated carbon |
Air containing mercury vapours |
360 nm3/hour |
Base collection container, volume 0.06 m3 |
Aluminium bases |
8.4 kg/hour |
Hopper fore collection of broken glass, volume 0.12 m3 |
Broken glass |
10 m3 |
Processed products contain on the average (by weight): glass – 94.61%, aluminium bases – 2.39%, luminophor – 3%, with mercury concentration is 34,400 mg/kg.
Figure 5.6 Scheme of disposal of tubular luminescent lamps (types LB, LD, etc.)
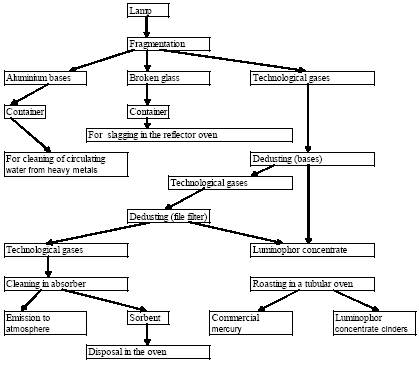
Waste from de-mercuration of tubular luminescent lamps includes:
- broken glass, the output of which makes 92% of the weight of the processes products; it contains not more than 0.2% of mercury included into processed products (the
specific mercury concentration in broken glass is not more than 2.1 mg/kg);
- aluminium bases (their output is 2.33%0;
- luminophor concentrate (their output is 5.67%) with mercury concentration up to 3.44% (by weight);
- emission (after cleaning) of off-gases to atmosphere (about 0.69 mg of mercury from its total quantity contained in processed lamps is emitted per tonne of disposable
products).
Broken glass is accumulated in metal containers and then used in lead production (for slagging of the reflector oven). Aluminium bases of luminescent lamps are used in
technological processes for pyrometallurgical; processing of mercury-containing raw materials as reducing agents during cleaning of circulating technological water from
soluble heavy metal salts. Luminophor concentrate produced during lamp processing at Ecoptrom-2 plant (about 1 t/year) is stored in tight packs and is processed in a
tubular oven TVP-1 (together with luminophor concentrate delivered from other organisations), using the above described scheme. Output of cinders from luminophor
concentrate roasting makes about 96% of the initial freight of processed raw materials; they are used for reclamation of old cinder dumpsites.
Disposal of high-pressure mercury lamps
Processing of high-pressure mercury lamps (DRL type) includes (Fig. 5.7):
- destruction of the lamp tubes and accumulation of broken glass with luminophor in special containers;
- separation of the quartz burner from the base with the lug and their separately accumulation in containers;
- defragmentation of burners in a hammer crusher and roasting of the obtained mass in the oven TVP-1 together with other mercury-containing secondary raw materials.
Waste of this process includes broken glass (used for processing of scrap lead, for slagging of the reflector oven) and scrap nonferrous and ferrous metal that is sold (as
secondary raw materials) to respective organisations.
Figure 5.7 Scheme of disposal of high-pressure mercury lamps (DRL type)
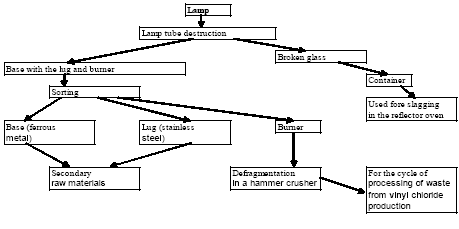
Disposal of metal mercury-filled devices
Disposal of metal devices with mercury fill is performed as follows (Fig. 5.8). The device is placed into a special tray; then a mechanical method or electrical gas welding is
used to open a section in the device filled with mercury; this mercury is poured into a steel cylinder. Bodies of devices with mercury removed as described above are placed
into the oven TVP-1 and are roasted for 3-4 hours at temperature of at least 500 °C. Mercury sorbed on the walls of the bodies is evaporated and is fed together with
technological gases to the system of condensation in the TVP-1. Then the body of the device (with mercury content ≤ 1 mg/kg) is disassembled into different types of scrap
metals.
Figure 5.8 Scheme of disposal of metal mercury-filled devices
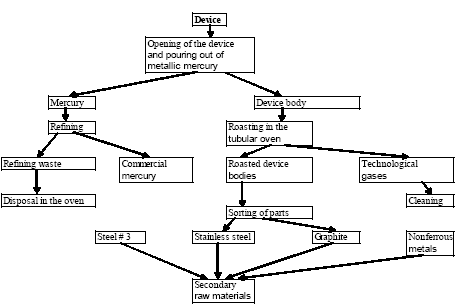
Disposal of glass mercury-filled devices
Disposal of glass devices filled with metallic mercury (on the average up to 3.7% of the total weight of the product) is performed as follows (Fig. 5.9):
- destruction of the glass tube (body) of the device in a bathtub under a water layer;
- pouring of metallic mercury into a tub;
- separation of metal parts; <
- pouring of metallic mercury from the tub into a special container;
- roasting of broken glass to remove residual mercury;
- refining of metal using the technological scheme adopted at the enterprise.
The degree of removal of mercury in this technological process makes over 99.9%. Waste of the process includes broken glass (up to 89% of the total weight of disposable
products) and metal fragments (up to 6.53% of the weight of disposable products). Broken glass is used in production of lead (for slagging of the reflector oven) and metal
fragments are sold as secondary raw materials.
Figure 5.9 Scheme of disposal of glass mercury-filled devices
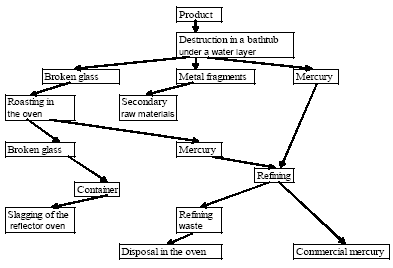
Disposal of paperboard packs
This type of waste is generated in the area of de-mercuration of mercury lamps delivered to processing in paperboard packs (the average weight of one pack is 20 g). With
the average annual number of processed lamps at 145,000 lamps, the weight of paper waste makes about 2.9 tonnes. This waste is accumulated in a metal container (1 m3)
and then incinerated in a tubular rotary oven TVP-1.
Disposal of spent personal protection equipment and special clothes
Spent respirators (one respirator is about 0.2 kg) and used special clothes are collected in a metal container with a lid and then incinerated in an oven. Annually, about 580
kg of spent respirators and up to 660 kg of used working clothes and footwear are disposed.
Refining of unconditioned (spent) metallic mercury
Unconditioned (spent or black) mercury delivered from different organisations is filtered and cleaned at the refining plant. The thus obtained mercury is used in production of
mercury compounds or supplied to different organisations and enterprises.
Amounts of processed mercury-containing waste
Tables 5.5 and 5.6 show data about amounts of different types of mercury-containing waste from production and consumption, processed at NPP Kubantsvetmet CJSC in
2001-2002; Table 5.7 includes summarised data about processed mercury-containing raw materials and production of secondary mercury at NPP Kubantsvetmet CJSC in
1998-2002.
Table 5.5 Processing of mercury-containing waste at NPP Kubantsvetmet CJSC, 2001
Type of waste |
Weight of waste, kg |
Commercial Hg, kg |
Catalyst, sorbent, sludge |
244312 |
9793 |
Unconditioned (spent, black) mercury |
16113 |
16097 |
Mercury lamps |
20610 |
7 |
Mercury-containing devices |
1784 |
131 |
Luminophor concentrate |
23700 |
78 |
Other (galvanic elements, mercury-contaminated construction waste
and soils, proper production waste, etc.) |
54800 |
343 |
Total |
361319 |
26449 |
Table 5.6 Processing of mercury-containing waste at NPP Kubantsvetmet CJSC , 2002
Type of waste |
Weight of waste, kg |
Commercial Hg, kg |
Unconditioned (spent, black) mercury |
783.5 |
727 |
Mercury lamps |
31200 |
10.5 |
Mercury-containing devices |
384 |
65.3 |
Luminophor concentrate |
59570 |
163.2 |
Other (galvanic elements, mercury-contaminated construction waste
and soils, proper production waste, etc.) |
2750 |
9.5 |
Total |
94687.5 |
975.5 |
Table 5.7 Processing of raw materials and production of secondary mercury at NPP Kubantsvetmet CJSC, 2002
Year |
Weight of waste, t |
Commercial Hg, kg |
1998 |
56.6 |
1459 |
1999 |
840.4 |
16020 |
2000 |
919.7 |
22061 |
2001 |
361.3 |
26449 |
2002 |
94.7 |
976 |
Total |
2272.7 |
66965 |
Greater part of metallic mercury produced during processing of production and consumption waste was used for production of different mercury compounds (brands HCh,
ChDA, Ch) (Russian abbreviation) production of which is described in section 3.10. In 2000-2002, metallic mercury was supplied in small amounts (2-4 t/year) to some
Russian enterprises (chemical enterprises in Volgograd, Termopribor OJSC in Klin, Lisma OJSVC in the city of Saransk, etc.). In 2003, about 150 tonnes of metallic
mercury was delivered to Energia OJSC (city of Yelets).
Production of highly pure mercury
As mentioned above, NPP Kubantsvetmet CJSC has 4 areas for production of special pure mercury (brands 5N, 6N or higher), based on the use of multiple distillation of
metal with electrical discharge cleaning. Processes of distillation refining are performed in the devices that are tightly isolated from the working space of the production area.
Mercury is packed into tight glass ampoules, containing 50 g or 75 g of metal. Some year ago, this mercury was used for scientific research, pilot production and in
semiconductor industry. In the recent years, no orders have been received for production of pure mercury, which can be explained by objective and subjective reasons
(financial problems, some enterprises have their own mercury refining plants, etc.).
Emission of mercury in the course of pyrometallurgical processing of raw materials
Table 5.8 and Table 5.9 show the basic indicators of operation of the tubular rotary oven TVP-1 and characteristics of the generated waste; Table 5.10 shows the balance
of distribution of mercury loss in the course of pyrometallurgical processing of mercury-containing raw materials. Since 2000, there has been a substantial reduction of total
mercury loss, due to increased degree of dust entrapment and conversion of the dust containing mercury into recycling technological water, increased efficacy of metallic
mercury separation and reprocessing of a range of interim products and waste in the ovens. In particular, in 2002 roasting of entrapped dust (entrapped by cleaning facilities)
in the oven together with the raw materials was started. A certain role is played by the factor that waste with high concentrations of mercury is now delivered for processing.
It is well known that practically all losses of mercury at mercury enterprises in the course of technological processes, as a rule, greatly depend on its content in the initial raw
materials: the higher the mercury concentration in the initial raw materials, the lower its loss (Pak et al., 1984).
Table 5.8 Basic characterisations of operation of the oven TVP-1 at the metallurgical plant NPP Kubantsvetmet CJSC for 1999-2001
Parameter |
1999 |
2000 |
2001 |
Processes mercury-containing raw materials (dry weight), kg |
840,390 |
919,744 |
361,319 |
Quantity of mercury in raw materials, kg |
16,313.73 |
22,302.56 |
26,746.25 |
Amount of metallic mercury produced, kg |
15,803.11 |
22,055 |
26,625.89 |
Total loss of mercury during technological processes, kg |
510.6 |
247.6 |
120.4 |
Table 5.9 Characterisation of waste generated during pyrometallurgical processing of mercury-containing raw materials, NPP Kubantsvetmet CJSC
Year |
Cinders |
Off-gases |
Circulating water * |
Dust of cyclones ** |
|
Weight, t |
Hg, mg/kg |
Volume, m3 |
Hg, mg/m3 |
Volume, m3 |
Hg, mg/m3 |
Weight, t |
Hg, mg/kg |
1999 |
748 |
38 |
10,449,745 |
30.68 |
360 |
22.3 |
25 |
3,400 |
2000 |
844 |
25 |
8,182,680 |
25.4 |
275 |
39 |
- |
- |
2001 |
129.9 |
26 |
2,119,487 |
24.3 |
250 |
259.4 |
- |
- |
- With annual fresh water makeup;
- ** From 2000, dust has been burned in the oven together with the raw materials (during the technological process).
In 2001, the share of irrecoverable mercury loss in the course of pyrometallurgical processing of raw materials made 46.1% (or 55.5 kg); the majority of this amount
included emitted off-gases emitted to atmosphere (42.8% or 51.5 kg). About 65 kg of mercury (53.9% of the total mercur4y loss) was finally returned together with
the circulating water to the technological process.
Table 5.10 Distribution of mercury loss in the course of the pyrometallurgical processing of raw materials in the oven TVP-1, at NPP
Kubantsvetmet CJSC
Types of loss |
1999 |
2000 |
2001 |
|
kg |
share, % |
kg |
share, % |
kg |
share, % |
With cinder * |
32.3 |
6.3 |
21.1 |
8.5 |
3.4 |
2.8 |
With off-gases ** |
320.6 |
62.8 |
207.8 |
83.9 |
51.5 |
42.8 |
With circulating water *** |
8 |
1.6 |
10.7 |
4.3 |
64.9 |
53.9 |
With cyclone dust **** |
85 |
16.6 |
- |
- |
- |
|
Unaccounted loss ***** |
64.7 |
12.7 |
8 |
3.3 |
0.6 |
0.5 |
Total loss |
510.6 |
100 |
247.6 |
100 |
120.4 |
100 |
- Unaccounted loss (into dumps or secondary use);
- ** Irrecoverable loss, emission to atmosphere via the stack;
- *** returned to the technological process;
- **** From 2000, dust has been burned in the oven together with the raw materials (during the technological process).
These observation data demonstrate that air in most working rooms at the enterprise from time to time includes mercury vapour concentrations exceeding the MAC
(Table 5.11). As a rule, the highest mercury vapour concentrations have been observed in the areas of mercury pouring into containers and in the operator room of
the tubular rotary oven TVP-1. In the open site, near the oven TVP-1, levels of mercury vapours in the air usually are about 0.01 mg/m3, going down to
0.0001-0.0003 mg/m3 on the border of the sanitary protection area.
Table 5.11 Levels of mercury concentrations in the air of the working rooms and within the sanitary protection area (SPA) at the metallurgical plant
of NPP Kubantsvetmet CJSC , 2002, in mg/m3
Area |
Average |
Limits |
Number of measurements per year * |
Operator's room of the tubular rotary oven |
0.019 |
0.010-0.025 |
12 |
Area for mercury pouring into containers |
0.026 |
0.023-0.028 |
13 |
Finished products warehouse |
0.010 |
0.001-0.014 |
10 |
Chemical analytical laboratory |
0.007 |
0.002-0.010 |
13 |
Mechanical shop |
0.010 |
0.003-0.012 |
12 |
Administrative and auxiliary building |
0.011 |
0.007-0.012 |
14 |
Open site, near TVP-1 |
Average about 0.01 |
- |
On the border of the SPA ** |
0.0001-0.0003 |
- |
MAC *** in the working area, average per shift |
0.005 |
- |
MAC in the working area, maximum |
0.010 |
- |
MAC in the air of populated localities |
0.0003 |
- |
Typical background content |
0.000010-0.000015 |
- |
- Approximately once a month;
- ** Size of the SPA is 100 m;
- *** Maximum allowed concentrations
The planned increase of mercury-containing waste amounts will, no doubt, lead to a noticeable growth in mercury emission to the habitat; above all, together with emitted
gases. This makes it necessary to:
- perform preventive operations to increase reliability of work and tightness of basic technological lines in the tubular rotary oven TVP-1;
- update (overhaul) the existing dust-and-gas cleaning system;
- create a system for additional cleaning of emitted gases from mercury, which must secure several-fold reduction of metal in them (at least, by one order as compared
to the excising);
- perform full-scale operations for de-mercuration of the basic working, administrative and warehouse rooms in the industrial area at NPP Kubantsvetmet CJSC and in
the area adjacent directly to the metallurgical plant (including the required range of full-scale mercury research);
- organise at the enterprise a permanent service for current de0mercuration.
5.1.3 Merkom Ltd.
Merkom Ltd. was organised in 1992; it is located in the research Institute of Instruments and devices (town of Lytkarino, Moscow Oblast); the total personnel includes over
40 persons.
Merkom performs disposal of the following mercury-containing waste:
- spent (unconditioned or black) metallic mercury (collection, transportation, refining, obtaining of secondary metal);
- mercury compounds (collection, transportation, processing and production of different mercury compounds);
- instruments filled with mercury, like thermometers, sphygmomanometers, ignitrons, normal elements, mercury contacts, etc. (collection of instruments and devices,
removal and cleaning of metallic mercury, preparation of instruments' bodies and their transportation to places of disposal);
- mercury lamps (collection, transportation and disposal);
- mercury-zinc galvanic elements (collection, packing and transportation to places of processing);
- hard, paste and liquid mercury-containing waste (collection, packing and transportation to places of processing).
Refining of spent (unconditioned, black) metallic mercury so as to produce commercial (secondary) metal; cleaning, processing (re-crystallisation) and production of
mercury compounds are performed using technologies developed by specialists of Merkom Ltd. (Donskykh, Skitskiy ...; Skitskiy, Donskykh, 1999). The basic
commercial products of the enterprise include metallic mercury P0 and P1 and mercury compounds of reactive purity.
Basic technological schemes and production operations
- Production facilities of the Merkom Ltd. include:
- the area for refining of the unconditioned (spent, black) mercury;
- the area for production of mercury compounds;
- the area for disposal of mercury-filled instruments and devices;
- the area for de-mercuration of tubular luminescent lamps;
- the area for receiving mercury-containing dry galvanic elements.
Production output for refining of unconditioned mercury and producing secondary metal is 100 t/year; for production of mercury compounds – 30 t/year; plants for
de-mercuration of tubular luminescent lamps – 1 million lamps/year.
Technological and production operations are performed observing conditions and requirements of the existing regulatory and technical as well as sanitary and hygienic
documents (GOST 30772-2001; GOST 30773-2001; GOST 30774-2001; GOST 30775-2001; GOST 4658-73; Inter-sectoral Rules on Protection ...; Mercury.
Regulatory ..., 2001; Mercury. Specifications ..., 1997).
Refining of the unconditioned metallic mercury
Cleaning of unconditioned metal is performed at the area for refining mercury at a special plant, based on the use of technology developed at Merkom Ltd. This
technology is based on a hydrochemical cleaning method, including multiple-stage processing of unconditioned mercury by different solutions.
In a general case, the technological scheme for refining of unconditioned metallic mercury is as is shown in Fig 5.10. Testing and quality control of commercial mercury
are effected according to GOST 4657-73 (GOST 4658-73). The final product is mercury of brands P0 and P1 that meet the requirements of the indicated State
Standard.
Figure 5.10 Technological scheme of substandard mercury refinement
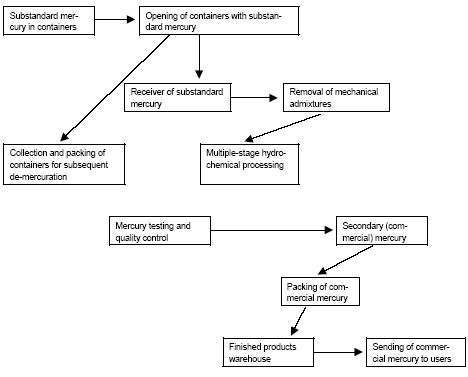
Packing of P1 mercury is made into standard steel cylinders containing 34.5 kg of mercury; P0 mercury is packed into plastic containers (3 kg of metallic mercury in
each container) in inert gas atmosphere.
Production of mercury compounds
The following technological operations are performed at the area for production of mercury compounds:
Disposal of instruments and devices filled with mercury
The area designed for disposal of mercury-filled instruments and devices includes different manual operations related to opening of the devices' bodies (ignitrons,
sphygmomanometers, etc.) and removal of mercury from them into special containers (mercury is delivered to the refining area). Then bodies and other parts of the
instruments and devices are packed and sent to FID-Dubna de-mercuration company (town of Dubna, Moscow Oblast).
In 2001 and 2002, a greater part of collected large-size instruments and de3vices filled with mercury (after verification of their tightness and respective packaging)
were sent to FID-Dubna for processing.
De-mercuration of mercury lamps
In 2001, Merkom Ltd. collected and packed low-pressure luminescent lamps (LD, LB and other types) and high-pressure mercury lamps (DRL, DNaT types),
which were then sent to Dubna, FID-Dubna, for disposal (about 50,000 lamps).
In 2002, the enterprise started its own vibration and pneumatic plant for de-mercuration of tubular luminescent lamps Ecotrom-2; its basic principles and features
were described above. In 2002, this plant was used to dispose of 214,000 luminescent lamps. In addition, 17,000 high-pressure mercury lamps (DRL, DNaT) were
collected and sent to Dubna for processing. Plans of Merkom Ltd. include expansion of the scopes of processing of tubular luminescent lamps up to 1 million lamps a
year.
The site for receiving galvanic elements
In this area, regular and mercury-zinc galvanic elements are packed which are delivered from different enterprises (they are packed into polyethylene bags ands then
into metal barrels). When these lamps are collected in large amounts, they are sent for secondary processing to other organisations (in 2001, the total weight of
collected galvanic elements was about 200 kg).
In 2002, the collected and disposed elements included 1,868 regular galvanic elements (with glass bodies), producing 18 kg of metallic mercury from them (they were
collected from organisations and enterprises of Moscow City and Moscow Oblast).
Other mercury-containing waste
Merkom Ltd. collects, packs and transports mercury-contaminated soils, communal and industrial waste, spent carbon sorbent and catalysts, mercury-containing
chemical sludge. As a rule, when the above waste is in small amounts, the company secures its safe packing and accumulation in the special production area, and then
it is transported to places of its direct disposal (to other organisations). Preparation and packing of large volumes of waste for its transportation is performed directly
at its source.
Waste generated during technological processes and operations
In the course of technological processes and operations connected with processing of mercury-containing products, mercury refining and production of mercury
compounds at Merkom Ltd. the following types of mercury-containing waste are generated that should be decontaminated.
Wastewater, the majority of which (up to 80%) is generated at the area of cleaning and production of mercury compounds, is characterised by the content of mercury
up to 30-49 mg/l; ts has high content of minerals (up to 300-400 g/l) and high concentrations of sodium, potassium, nitrogen, chloride and sulphate compounds. Such
wastewater is pre-treated on the site from mercury (using chemical deposition by creating an alkaline environment) and then accumulated in special containers (tanks).
The volumes of generated wastewater are not great. Thus, in 1999, 5 m3 of wastewater was accumulated and sent for disposal to NPP Kubantsvetmet CJSC; by
now, the volume of wastewater stored in accumulation tanks is about 4 m3. An urgent problem for the enterprise is development and using of a scheme for in-depth
treatment of wastewater directly on the site, which would allow a substantial increase of the volumes of refined unconditioned mercury and production of mercury
compounds.
Solid waste (pasty) contain, on the average, 0.2-0.3% of mercury generated during refining of unconditioned mercury and of its compounds from mechanical
admixtures, as well as during pre-treatment of wastewater (wastewater sludge). Waste is packed into polyethylene bags (20-30 l) with a polyethylene insert; then it is
placed into a metal barrel also having a polyethylene insert. When waste is accumulated it is sent to Karsnodardsky Rudnik enterprise for disposal (NPP
Kubantsvetmet CJSC). The specific generation of solid waste makes about 1 g per tonne of refined commercial mercury.
Containers from glass and plastics used to deliver unconditioned metallic mercury for disposal and other mercury-containing waste are de-mercurised (de-mercuration
solutions are drained to wastewater). Metal containers are packed and delivered to disposal to FID-Dubna. Usually, up to 3-4 tonnes of such containers are collected
every year.
Luminophor concentrate generated during disposal of mercury lamps is packed (using technology of Ecotrom Ltd.) into polyethylene bags; when Luminophor
concentrate is accumulated it is planned to deliver it form processing to NPP Kubantsvetmet CJSC; broken glass is removed to dumpsites; aluminium parts of lamps
are delivered to organisations that collect nonferrous scarp metals.
Cleaning emission to atmosphere
The area of mercury refining is equipped with carbon sorbent (UPR type); the area for lamp de-mercuration is also equipped with Pertyanov filters; efficiency of used
emission cleaning systems is over 90%. As a rule, the content of mercury vapours in the air of the working rooms and at the exit of emissions to atmosphere is not
more than 0.2-0.3 MAC for the working area (average monthly).
All local emissions (including suctions from point sources) are fed to industrial general exchange ventilation system, pass through three carbon absorbers and then
released (3,000 m3/h) through the stack (120 m high).
The maximum allowed emission of mercury vapours set for Merkom Ltd. is 800 mg a year.
Processing of mercury-containing waste and production of metallic mercury
Table 5.12 shows data about collection and processing of mercury-containing waste and production (refining) of metallic (secondary) mercury at Merkom Ltd., in
200-2002.
Metallic mercury obtained by Merkom Ltd. in 2000-2002 was delivered, mainly, to domestic electrical lamp manufacturers (Smolensk and Saransk), the plant of
mercury thermometers (Klin), Altaykhimprom OJSC (Slavgorod) and, in small amounts, to intermediary trade organisations. It should be noted that in 2002 Merkom
Ltd. purchased a batch of metallic mercury of 8,442 kg (from an enterprise located in the city of Ryazan which in the past manufactured mercury valves). After the
required technical tests, containers preparation and checking of the packages tightness, mercury was also delivered to the market (to the above enterprises).
Table 5.12 Processing of unconditioned mercury and mercury-containing waste at Merkom Ltd.
Year |
Unconditioned Hg, kg ** |
Commercial Hg, kg *** |
Unconditioned Hg compounds, kg |
Ignitrons, sphygmomanometers, thermometers, etc. |
Waste (soils, garbage, sorbent, etc.), kg ******* |
Total weight, kg |
Extracted Hg, kg |
2000 |
10,990 |
9,343 |
271 |
-**** |
- |
No data |
2001 |
5,766 |
5,199 |
38 |
3,137 |
395 ****** |
7,460 |
2002* |
8,987 |
8,744 |
- |
110.5***** |
17.4 ****** |
2,561 |
- In 2002, the number of disposed mercury contacts was 287 (removing 4.3 kg of metallic mercury) and 1,721 mercury thermometers (3.4 kg of ,mercury);
- ** Weight together with the containers;
- *** Metal obtained during refining of unconditioned (black) mercury);
- **** Devices were sent for disposal to FID-Dubna;
- ***** The greater part of devices was sent to FID-Dubna;
- ****** Mercury was refined;
- ******* Sent to NPP Kubantsvetmet CJSC; during first 7 months of 2003 Merkom Ltd. collected, packed and prepared for deliver to disposal about 10
tonnes of mercury-contaminated soils and construction waste.
5.2 Mercury Turnover with Solid Waste
To identify all sources of mercury-containing consumption and production wastes (MCW) generation, it's important to take into consideration the spheres where
mercury or its compounds are used intentionally or mercury is present in considerable quantities as natural impurity in the raw materials and products. According to the
Article 1 of the Law of the Russian Federation On Production and Consumption Waste No. 89-FL dated June 24, 1998, u mercury-containing waste are
mercury-containing residual raw materials, semi-products and products generated as a result of production or consumption and as well as goods that have lost their
consuming properties.
Generation of mercury-containing solid waste could be in:
- Extraction and production of mercury;
- Processing of natural materials, containing mercury;
- Use of mercury in gold mining;
- Use of mercury and its compounds in production of chemical products;
- Production and use of goods containing mercury and its compounds;
- Reprocessing of mercury-containing wastes (MCW).
5.2.1 Generation of Mercury-containing Solid Waste in Russia
Official data on MCW accumulation, generation and neutralization in various sectors and main regions of Russia is shown in Table 5.13 and Table 5.14. As it can be
seen the three industrial sectors - chemical, machine-building and non-ferrous metallurgy - are accounted for the major part of generated mercury-containing waste.
Machine-building waste which most probably covers the mercury-containing consumption waste (used and outdated thermometers, lamps, batteries, etc.) are
described in chapter 3.
Siberian, Ural, Volga and Central Federal Districts of the Russian Federation account for a major part of generated mercury-containing waste. The reason is the
location of large industrial enterprises generating mercury-containing waste. Central Federal District is characterized by the biggest volume of MCW processing,
though the District holds the second place with MCW generation in Russia. The most urging situation is in Ural Federal District: having MCW annual generation share
as 30 %, wastes treatment volumes are as 2 %.
A consideration should be given to the fact that official informational sources do not mention Hg concentrations in accumulated and annually generated MCW, as well
as typification of waste by Hg concentration level. As mentioned above, the whole amount of MCW accumulated in Russia by tiday includes about 58% waste with
Hg content of 10-100 mg/kg, about 12% - 100-5,000 mg/kg, about 30% - above 5,000 mg/kg. According to information from other sources, Hg content in stored
and annually generated MCW varies from 0.02 to 75%. In Russia there is no lower limit of mercury concentration in waste according to which the waste could be
included into the mercury-containing waste category. It is known that in practice such lower limit is considered as MAC of mercury in soil (2,1 mg/kg) which is
obviously not always relevant.
Table 5.13 Accumulated, generated and neutralised mercury-containing waste in 2002 (Goscomstat RF, Ministry of Natural Resources RF)
Sector |
Accumulated mercury-containing wastes by the end of 2001 |
Generated mercury-containing wastes in 2002 |
Neutralized mercury-containing wastes in 2002 |
t |
% |
t |
% |
t |
% |
Industry, including: |
2,874 |
83.1 |
7,214 |
85.9 |
1,655 |
65.8 |
Chemical |
1,159 |
33.5 |
1,200 |
14.3 |
536 |
21.3 |
Machine-building |
801 |
23.5 |
3,342 |
39.8 |
1,158 |
46.0 |
Non-ferrous metallurgy |
691 |
20.0 |
2,075 |
24.7 |
1.9 |
0.08 |
Pulp and paper |
20 |
0.58 |
45 |
0.53 |
- |
|
Flour-and-cereals and feed mill |
|
|
|
|
|
|
Power industry |
41 |
1.19 |
126 |
1.5 |
16 |
0.64 |
Fuel industry |
30 |
0.87 |
85 |
1.0 |
- |
|
Construction materials industry |
108 |
3.1 |
145 |
1.7 |
- |
|
Municipal housing economy |
332 |
9.6 |
62 |
0.07 |
185 |
7.4 |
Totally in Russia |
3,458 |
100 |
8,396 |
100 |
2,517 |
100 |
Table 5.14 Mercury-containing wastes distribution by the federal districts of RF (Goscomstat and Ministry of Natural Resources)
District |
Accumulated mercury-containing wastes at the end of 2001 |
Generated mercury-containing wastes in 2002 |
Neutralized mercury-containing wastes in 2002 |
t |
% |
t |
% |
t |
% |
Central |
376.9 |
10 |
2,184 |
26 |
950 |
38 |
North-West |
88.4 |
2.6 |
145.2 |
1.7 |
44 |
1.8 |
South |
1,029.9 |
30 |
559 |
7 |
210 |
8 |
Privolzhskij |
287.1 |
8 |
936 |
11 |
747.4 |
30 |
Ural |
213.3 |
6 |
2,422 |
29 |
54.8 |
2.1 |
Siberia |
1,407.9 |
41 |
2,129.8 |
25 |
510.1 |
20 |
Far east |
54.6 |
1.6 |
19.4 |
0.2 |
0.135 |
0.0 |
Totally in Russia |
3,458 |
100 |
8,396 |
100 |
2,517 |
100 |
Figure 5.11 Accumulation, generation and treatment of mercury-containing solid waste in RF regions in 2002.
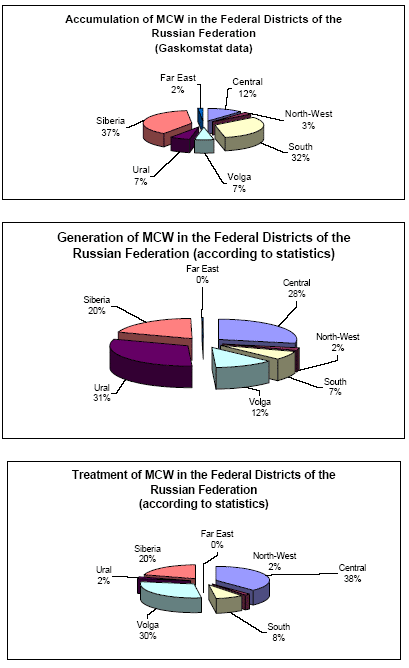
5.2.2 Mercury in Industrial Waste and Waste from Energy Production
Mercury in industrial waste and waste from energy production has been described in the different sections in Chapter 3 and 4. The information on the waste that is
disposed of to landfills/waste dumps is summarized in Table 5.15.
As regards intentional industrial uses of mercury, chlor-alkali production account by far for the major part of mercury in the waste, which is in general disposed of in
dumps close to the production sites. The total amount of mercury in the waste is tentatively estimated to be equal to 39 tonnes. Mercury contained in waste generated
at the territory of Novosibirsky Chemical Concentrates Production Facility (production of lithium isotopes) by now amounts to 100-500 tonnes.
Table 5.15 Mercury in industrial waste and waste from energy production disposed on to landfill/waste dumps 2001/2002
Activity |
Mercury masstonnes/year Best estimate |
Section |
Chlor-alkali production |
39,3 |
3.1 |
Production of consumer products: lamps, batteries, etc. |
0,3 |
3.5- 3.9 |
Gold mining using amalgamation method |
0,55 |
3.3 |
Coal extraction and use |
5,6 |
4.1 |
Oil, gas and biofuels |
? |
4.2 |
Copper/nickel production * |
6,6 |
4.3 |
Lead and zinc production |
8,5 |
4.3 |
Other non-ferrous metal production |
4,2 |
3.3; 4.3 |
Cement production |
0,4 |
4.3 |
Total |
65 |
|
* Exclusive tailings
In total more than 3000 t mercury is accumulated in the soil and at dumpsites around production facilities in which mercury has been used. Table 5.16 lists the
identified production facilities. The list is considered comprehensive as regards the use of mercury for production of chlorine (inclusive chlorine production in paper
plants), but significant amounts of mercury may also be accumulated around facilities for production of thermometers, switches and other eletrotechnical products.
For the whole history of gold mining in Russia, about 6,000 t mercury has been used for gold mining by the amalgamation method. The major part of this mercury is
accumulated in tailings and other wastes. A significant amount of mercury may be released by mining of these waste heaps and tailings.
Tailings from production of non-ferrous metals may contain significant amounts of mercury, but no data has been available on total mercury content of tailings.
Table 5.16 Sites with accumulation of mercury containing waste
Plant |
Activity |
Period of activity |
Approximate amount of Hg, t In dumps and slag-heaps |
Comment |
JSC «Usolyechimprom»,
Usolye-Sibirskoye
|
Chlor-alkali |
1970-1998 |
800 |
|
JSC «Kaustic» «Krebs» Plant Sterlitamak City |
Chlor-alkali |
1964-1987 |
50 |
|
OAO «Kaprolaktam», dzherzhinsk,
Nezhegorodskaya oblast |
Chlor-alkali |
1948-1982 |
60 |
|
JSC "Kirovo-Chepetsk Chemical Enterprise", Kirovo-Chepetsk,
Kirovsk oblast |
Chlor-alkali |
1955-today |
300-700 |
|
JSC "Kaustic",
Volgograd
|
Chlor-alkali |
1968-today |
<500? |
In soil under building
In waste dumps
|
CJSC "Kaustic", Sterlitamak |
Chlor-alkali |
1997- today |
200-300? |
In soil under building
In waste dumps
|
JSC "Sayanskchimplast", Sayani, Irkutsk oblast |
Chlor-alkali |
1979-today |
500 |
|
Kotlass PPF Koryazhma, Arkhangelsk oblast |
Cl for paper production |
1964- 1998 |
130 |
|
Arkhangelsk PPF Novodvinsk,
Arkhangelsk oblast
|
Cl for paper production |
1962-1996 |
120 |
|
Amursky PPF
Komsomolsk-na-Amure
|
Cl for paper production |
1970-1997 |
56 |
|
Svetlogorsk PPF
Svetlogorsk, Leningrad oblast
|
Cl for paper production |
1951-1993 |
11 |
|
Lithium production, Novosibirsk |
Lithium isotopes |
- |
100-500 |
35 t/year by mid 1990's |
Total |
|
|
more than 3,000 |
|
5.2.3 Mercury in Municipal Solid Waste
Mercury lamps, thermometers, batteries and other mercury-containing devices used at homes as well as batteries can be considered as major sources of mercury in
municipal solid waste (MSW).
In 1997, it was established that in St. Petersburg the amount of mercury in devices used by the population contained more than 3 tonnes mercury (Mercury. Complex
safety system...., 1996). Extrapolation of these data on the Russian Federation suggests that about 93 tonnes of mercury is in the devices used by population of the
country. If every Russian family has two mercury thermometers, then the total number of thermometers used by population makes about 70 million pieces (140 tonnes
of mercury), which is much higher than the data obtained by extrapolation of the indicators for St. Petersburg. To estimate the amount of mercury that goes into waste
from population, we used the presumption that 1/6 of all devices used by population loss their consumer properties every year. In this case, 15.5 tonnes of mercury
(using the St. Petersburg data) or 23.3 tonnes of mercury (using the thermometer approach) will be lost with MSW. In section 3.5 it is described that in the outadted
thermometers for the domestic market in 2001 contained about 9.3 t mercury of which the major part was disposed of with solid waste. All in all it is estimated that
some 16-23 t may be disposed of with mercury-containing devices. Besides, about 1.6 t of mercury is included into MSW with spent luminescent lamps (see section
3.8), 1.6 with batteries (section 3.7) and 0.4 t with switches (section 3.9). The estimate for batteries is very dependent on the actual life of batteries, as the
consumption of mercury has decreased steeply the last years. In the 1980's, up to 100-130 tonnes of mercury were used every year for manufacture of galvanic
elements and batteries. The actual life-time of batteries may be significantly longer than their technical life as it may take some time before the batteries are disposed of.
For this reason these products as a source of mercury in MSW may be underestimated.
The releases of mercury contained as a trace element (impurity) in MSW may be significant, but is difucult to estimate as no data on the background level of mercury
in the waste exist.
The average content of mercury in MSW from mercury-containing devices and materials was determined on basis of the source estimate (see Table 5.17), and the
total amount of MSW generated in the Russian Federation. According to the estimates, mercury content in MSW (except as impurity) may reach 0.7-0.9 mg/kg of
MSW, which is lower than mercury MAC for soils of 2.1 mg/kg.
Table 5.17 Sources of mercury in municipal solid wastes
Source of Hg releases with wastes |
Approximate amount of Hg, t/year |
Note |
Hg-containing devices (mainly thermometers) |
16-23 |
Section 3.5 |
Batteries |
1.6* |
Section 3.6 |
Lamps |
2 |
Section 3.8 |
Dental amalgam fillings |
6* |
Section 3.4 |
Switchers |
0.4 |
Section 3.9 |
As trace element/impurity in all waste |
? |
|
Total |
26-33 |
|
* It is unclear how much of this exactly ends up in solid waste.
In the Russian Federation, almost all annually generated MSW are disposed on dumpsites or landfills. MSW incinerating plants operate in Moscow, Pyatigorsk,
Sochi, Vladivostok and Murmansk (see Table 5.18 and Figure 5.12). The share of MSW incinerated by these enterprises may be assessed at 2-3% of the total
annual amount of MSW. Using the above estimate some 0.5 t mercury should be contained in the incinerated MSW. It is known ("Reference materials...,1999) that
Hg emissions to the atmosphere from MSW incineration plant of Vladivostok in 1999 amounted to 0.5 t (according to the official state statistical observation 2
TP-air). Extrapolation of these data to other enterprises taking into account their design capacity allows to obtain the approximate amount of Hg emissions from
garbage incineration plants 3.5 t/year (for Pyatigorsk, Sochi, Vladivostok and Murmansk). It should be noted that the estimate seems to be quite high if the expected
mercury content of the incinerated waste is considered.
Two plants are operated in Moscow with total capacity 40,000 tonnes of wastes/year. Cleaning system is carried out by activated carbon. Mercury emissions were
not detected by analytical control. Emissions of the plant are in a compliance with regulatory requirements of the Directive dated year 2000.
The plant in Sochi was closed because of significant impact on the environment
The plant in Pyatigorsk is operated with annual capacity 150,000 tonnes/year. Mercury emissions detected by analytical method is 0.000013 g/second (old data), by
calculations is 0.000052 g/second. Mercury content in ashes is 4 mg/kg., in slag is 0.8 mg/kg, in aqueous extract of ashes is 0.003*10-3 % mass.
Figure 5.12 Location of municipal waste incinerators in the Russian Federation (indicated as I)
Click here to see the figure.
The difference between sources and emissions may to some extent be explained by differences in domestic consumption structure between urban and rural population.
In big cities, where garbage incineration plants are located, mercury concentration in MSW will most probably be higher than the average values. Mercury content of
waste water seems also to be higher in big cities (discussed below). The difference may also indicate that the mercury content of waste could be significantly higher
than estimated above. The reason could be that mercury as trace element account for a major part of the mercury in the waste or that the life-time of batteries,
switches, etc. is longer than assumed. The consumption of mercury for production of these products ten years ago was several times higher than the consumption
today.
According to official data, emissions from housing and communal sector make 3 kg of mercury a year (see Annex 1), but this includes most probably not MSW
incineration.
Table 5.18 Municipal solid waste incinerators in the Russian Federation
Town |
Capacitytonnes |
Emission abatement technology |
Moscow |
40,000 |
Activated carbon |
Pyatigorsk |
150,000 |
no data |
Sochi |
"closed" |
no data |
Vladivostok |
no data |
no data |
Murmansk |
no data |
no data |
Total |
no data |
no data |
5.2.4 Mercury in Medical Waste
Medical mercury-containing waste includes luminescent lamps used for medical and technical porpoises (they may contain up to 500 mg of mercury) and medical
thermometers.
In medicine mercuric chloride solutions (II) or HgCI2 with concentrations from 1:1000 to 1:5000, were formerly used for disinfecting medical equipment, laboratory
vessels and decontamination of skin. Today, use of mercuric compounds for disinfections is strictly restricted.
An investigation of the amount of medical waste in health and children's preschool institutions was performed in 2002, using data on the account of waste in Perm
Oblast, where the accumulated mercury-containing waste reached 175 tonnes (without luminescent lamps). The content of mercury in this mercury-containing waste
made 29.9 kg, including 21.7 kg in thermometers, 7.9 kg in devices, 1.2 kg in bactericidal lamps and 0.2 kg in different mercury compounds. Extrapolation of these
data for the entire Russian Federation suggests that the non-productive sectors, not involved into reporting campaigns, have accumulated 5,750 tonnes of devices,
containing 1.5 tonnes of mercury. Considering the significant amounts of mercury that have been used for production of other thermometers and other devices the
estimate, however, seems very low.
In the Russian Federation, there is no broad practice of incineration of hazardous waste, and hospital waste. An approximate composition of medical wastes which
may be incinerated looks like the following (The State Report... 2002): 74.5% - bandaging material, 9.3% - polymers, 7.9% - food waste, resin and metal - by 3.1%
each, 1.09% - pathologoanatomic waste. The probability of Hg content in these wastes is very low. These wastes are buried and incinerated in boiler houses and
crematoriums.
Hg-containing wastes are classified as medical wastes Class D. This group also includes the outdated medicines and disinfectants, wastes of diagnostic medications
etc.
The inventory carried out in 2000 in Novokuznetsk revealed, that a share of Class D wastes constitutes 6.3% of the total amount of medical wastes (4,249,052 t)
(Economical and social geography of Russia. Moscow,2001). Inventory in Yeraterinburg indicated 6.6%.
The total amount of medical wastes was calculated by extrapolation of medical wastes inventory data in Kaluga oblast (999.457 t) and Novokuznetsk city to Russian
Federation dimension, with the given specific amount of wastes per capita. Thus, the obtained amount of medical wastes constitutes 461,000 t.
5.3 Mercury in Waste Water
Data on the content of mercury in organized wastewater discharge and its subsequent entering water bodies are included into Form 2 of the water sector (Form
òï-Âîäõîç). Below are given data of the state statistics on discharge of contaminants to water bodies in 2001 (see Tables 5.19 and 5.20 and Annex 1).
Table 5.19 Discharge of mercury in surface water sources by regions of the Russian Federation in 2001
Territory name |
Volume of polluted discharges
million m3
|
Mercury discharge,
kg
|
Note |
Russian Federation (in total) |
22,370 |
177 |
|
Saint-Petersburg |
1,244 |
19 |
|
Leningrad region |
413 |
2 |
|
Moscow |
2,185 |
2 |
|
Kirov region |
183 |
2 |
Chemical industry |
Republic of Bashkortostan |
449 |
16 |
Chemical industry |
Novosibirsk region |
385 |
1 |
|
Krasnoyarsk krai |
644 |
1 |
|
Irkutsk region |
911 |
129 |
Chemical industry |
Sakhs Republic (Yakutia) |
93 |
4 |
|
Amur region |
109 |
1 |
|
Table 5.20 Discharge of mercury into surface water sources by industrial sector in 2001
Sector |
Volume of polluted discharges, mln cub m |
Mercury discharge, kg |
Russian Federation (in total) |
22,370 |
177 |
Industry |
7,273 |
156 |
Non-ferrous metallurgy |
593 |
6 |
Chemical |
855 |
146 |
Pulp and paper |
1,421 |
1 |
Flour-and-cereals and feed mill |
23 |
2 |
Municipal housing economy |
13,474 |
20 |
Chemical industry accounts for the major part of the industrial sources. According to official data, the total discharge from chemical industry was 146 kg mercury.
According to the assessment in section 3.2 about 20 kg mercury is discharged from VCM production. Most probably the remaining part of Hg is discharged from
chlor-alkali industry. However, according to the assessment in section 3.1, only about 1 kg should be discharged with waste water from such facilities. Thus, the
official statistics indicate that this amount most probably is underestimated.
Wastewater from housing and communal facilities brings according to the statistic 20 kg of mercury into water bodies. It is not clear which activities are included in
"municipal housing economy". Most likely we are talking about waste water discharge from waste water treatment facilities operated by local municipalities and city
administrations.
The total discharge of mercury with municipal wastewater may be estimated based on it concentration in sewage sludge from wastewater treatment facilities. Data on
mercury concentration of sewage sludge from a number of towns obtained from different sources is shown in Table 5.21. As it can be seen, the mercury concentration
varies considerably. The higher concentration of mercury is found in sludge from towns where large volumes of mercury is used in industrial enterprises (e.g. Klin and
Saransk), but high concentrations may be found in other towns as well.
In the major cities, e.g., St. Petersburg and Moscow, the measured concentration is within 1-2 mg/kg dry weight whereas it seems to be lower in the smaller towns.
The established norms for mercury content of sludge to be used as fertilizer is 15 mg/kg dry weight (SanPiN 2.1.7.573-96).
The number of data is too limited to make an exact estimate of the total annual mercury content in sewage sludge in Russia, but they can be used for a first rough
estimate.
The total amount of sewage sludge generated can be estimated from the volume of waste water using general experience on the amount of sludge generated by the
water treatment.
Most Russian cities have centralized municipal sewage treatment plants where household and industrial wastewater is treated. Usually, a 2-stage treatment system is
used, including mechanical and biological treatment. In the course of treatment, significant sewage sludge is generated, i.e. colloidal sludge mixture of mineral and
organic substances that has a specific chemical composition and the average humidity of 96.2% (Turovsky, 1988).
To remove water and decontaminate the sludge, it is usually placed to the sludge beds or (less frequently) to filtration fields located near the municipal sewage
treatment plants. In most cases, sludge is fed (poured) onto sludge beds from time to time, in separate layers (up to 20-25 cm thick). When it dries, the sludge loses
moisture, mainly through evaporation; some water is filtered through ground. Some mercury in the sludge may be released from the fields but no data exists.
At technical calculations the sludge content (the average humidity of 96.2%) is usually considered as equal to 0.5-1.0% of the wastewater volume (Turovsky, 1988);
a density of sludge is 949 kg/m3 on the average (Disposal of solid wastes, 1985) - this corresponds to 0.18-0.36 kg dry weight per m3 wastewater. The capacity of
sewage treatment facilities in the Russian Federation constitutes 57.2 million m3/day / (The State Catalogue on pesticides and agricultural chemicals allowed for
application in Russia – M. 2002), i.e. about 20,878 million m3/year of water passes trough the wastewater treatment facilities in Russia. If all wastewater is biologically
treated, the sludge generation volume will amount to 3.8-7.5 million t dry weight.
Using these data the total mercury content of municipal sewage sludge can be estimated at 3.4-11.9 t/year (table 5.22).
It is assumed that the wastewater treatment efficiency for mercury is 50 %. For comparison the treatment efficiency of Danish treatment plants is about 65% (Skaarup
et al 2003). Assuming a 50% efficiency, the estimates indicate that in Russia 3.4-11.9 t mercury is discharged to the water bodies from municipal sewage treatment
plants; more that 20 times more than the total registered discharges from industrial sources. It should be kept in mind, that the municipal sewage treatment plants
receive not only household but industrial wastewater as well, which might input a considerable amount of mercury. Official statistics on industrial mercury discharges to
water obviously covers only the wastewater directly discharged to water bodies from the treatment facilities of the enterprises (avoiding municipal sewage treatment
plants).
Table 5.21 Mercury in municipal sewage sludge
locality |
Mercury content mg/kg dry weight |
Moscow oblast (Achkasov) |
Klin (mercury thermometer enterprise) |
220 |
Kolomna |
10 |
Aprelevka |
3.6 |
Zagorsk |
2.8 |
Orekhovo-Zuyevo |
2.4 |
Bronnitsy |
0.8 |
Serpukhov |
0.4 |
Zaraysk |
0.4 |
Voskresensk |
0.3 |
Domodedovo |
0.2 |
Pavlovsky Posad |
0.2 |
Podolsk |
0.2 |
Shatura |
0.2 |
Elektrostal |
0.1 |
Belozersky |
0.1 |
Istra |
0.1 |
Naro-Fominsk |
0.1 |
Ramenskoye |
0.03 |
Moscow (Achkasov) |
Lubertsy wastewater treatment plant |
1.8 |
Kuryanovo wastewater treatment plant |
1.3 |
Republic of Mordovia (Yanin, 1995) |
Saransk, municipal wastewater treatment plant (mercury lamp enterprise) |
4 (3-5) |
Perm oblast (the Analytical Center, 1998) |
Gubakha (industrial enterprises) |
14.1 |
Kungur |
0.6 |
St. Petersburg (Waste generation and utilization........) |
Treatment facilities of St. Petersburg |
1.6 |
Table 5.22 Mercury in the municipal wastewater sludge
City type * |
Share in population of Russia, % |
Amount of dry Hg-containing sludge,
million tonnes dry weight
|
Average mercury content
mg/kg dry weight
|
Mercury in sludge
tonnes
|
Small and medium |
30 |
1.1-2.3 |
0.2-0.6 |
0.2-1.4 |
Big |
70 |
2.64-5.27 |
1.2-2.0 |
3.2-10.5 |
Total (round) |
100 |
3.8-7.5 |
|
3.4-11.9 |
* Small and medium cities are the cities with population number up to 100,000 people and more than 100,000 people respectively.
Thus in Russia in total the untreated municipal waste water contains 7-24 t mercury per year. In some Russian localities (towns of Klin, Saransk, etc.) industrial
enterprises which use mercury intentionally in technological processes may be significant sources of mercury to wastewater delivered and treated at the centralized
municipal treatment plants together with the domestic sewage. Nevertheless, on a national scale, such enterprises input an insignificant share of mercury in
wastewater/effluents discharged to water bodies. Some part of mercury may be delivered to water bodies with the surface run-off (rain and melted water) from urban
territories which don't undergo the necessary treatment in most Russian cities. A detailed analysis of sources of mercury to waste water in Denmark indicated that rain
water may account for about 10% of the total sources (average mercury content in sludge was 1.2 mg/kg (Skaarup et al 2003)).
A major source may be dental amalgams from dental clinics discharging it to the centralized municipal sewerage (up to 6 tonnes of mercury as indicated in section
3.4). Besides, mercury from broken thermometers and measuring equipment may be significant sources. If only a small part of the 18 t used annually with
thermometers ends up in the sewage it would be significant.
Infiltration water from landfills for municipal solid waste which include used\broken mercury-containing appliances can be considered as a source of mercury in water
bodies. According to data (EIA of MSW landfill in Perm), the content of mercury in the landfill leachate can be 2 microgram/l in the average (with the range from
0.055 microgram/l to 1.46 microgram/l).
A practical example can be given using data of control of underground water in St. Petersburg (Report on wastes management, 2002). Only in one field mercury was
found in samples in the amount of 0.0007 mg/l.
Disposal of sewage sludge
Out of the total sewage sludge generated every year in Russia, about only 10-15% is treated according to modern requirements, i.e. compacted, stabilised, dewatered
and used as fertilisers or transported to special fields (Agranovich, 1992). According to other data, the level of practical use of sewage sludge today is about 1-1.5%
(Lotosh, 2002). In any case, the overwhelming majority of sewage sludge is placed (for a rather long period of time) to sludge beds (filter beds) and then, as a rule,
brought to waste dumpsites (or to quarries). In Russia, the content of mercury in WWS that can be used as fertilizers must not exceed 15 mg/kg of dry weight
(SanPiN ...). In soils with middle and heavy granulometric compositions, to avoid accumulation of metal, it is not allowed to use more than 10 t/ha of dry sludge in its
pure substance or as part of compost (the frequency of application at least 5 years). In light sand and clay sand soils, the norm of application is limited to 7 t/ha with
the frequency of use 3 years minimum. It is prohibited to use WWS and composts based on WWS in soils with pH below 5.5, without liming of such soils, if the
content of calcium in the sludge or compost does not maintain pH at 5.5 or higher. It should be noted that Hg concentration in WWS are as usual considerably higher
than in standard mineral fertilizers in which it is equal to 0.05 mg/kg (Kovda,1985).
hr align="left" width="25%">
Footnotes
* The majority of information and primary statistical data used as the basis for the below materials about activities of NPP Kubantsvetmet CJSC and Mercom Ltd. In
the field of processing of mercury-containing waste and production of mercury and its compounds were obtained directly from the above enterpreises.
| Front page | | Contents | | Previous | | Next | | Top |
Version 1.0 March 2005, © Danish Environmental Protection Agency
|