| Front page | | Contents | | Previous | | Next |
Identification and assessment of alternatives to selected phthalates
2 Application of DEHP, DBP and BBP in products and articles
2.1 The phthalates
The term "phthalates" is here (and commonly) used for esters of ortho-phthalic acid and are the most commonly used plasticisers in the world.
The general structural formula of phthalates is shown in Figure 2.1. The functional groups (indicated as R) can either be linear aryl groups or alkyl groups with an aromatic ring. The properties of the phthalates are determined by the functional groups.
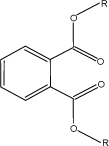
Figure 2.1 General structural formula of ortho-phthalates. R can be linear alkyl groups or aryl groups with an aromatic ring.
Examples of two of the phthalates are shown below, DEHP with symmetric linear functional groups and BBP with asymmetric aryl and alkyl functional groups.
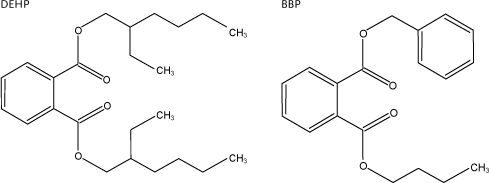
Figure 2.2 Examples of structural formula of phthalates
The softening effects of the phthalates decrease with increasing length of the functional groups (Hoffmann, 1996): DBP > BBP > DEHP > DINP > DIDP > DTDP. Consequently higher loading are necessary to obtain a certain level of softness for the phthalates with longer functional groups.
One property of importance for the application of the phthalates concerned in this study is the gelling ability of the plasticiser i.e. the ability of the plasticiser to mix with the resin by processing. The ability decrease in the following order: BBP > DBP > DIHP > DEHP > DINP > DIDP > DTDP (Hoffman, 1996).
The most common phthalates are di-isononyl phthalate (DINP); di-isodecyl phthalate (DIDP); and di-2-ethyl hexyl phthalate (DEHP).
Phthalates are widely used as general-purpose plasticisers because they offer the advantage of lower costs and increased production efficiency. When added to plastics, phthalates allow the long polyvinyl molecules to slide against one another. The phthalates show low water solubility, high oil solubility, and low volatility.
This is achieved through improved melt viscosity and production speeds of heated PVC with phthalates added. Increased flow characteristics give better workability and reduced out-of service breaks in equipment.
Table 2.1 Classification of and use restrictions on phthalates included in this study
Chemical name |
Abb. |
CAS No |
Classification
cf. 1272/2008 (GHS) |
Use restrictions |
Di(2-ethylhexyl) phthalate |
DEHP, DOP |
117-81-7 |
Repr. 1B
(Repr. Cat. 2;
R60-61) |
Shall not be used as substances or as constituents of preparations, at concentrations of greater than 0,1% by mass of the plasticised material, in toys and childcare articles (Regulation No 552/2009)
Not permitted for use in cosmetics (Directive 2004/93/EC) |
Di-n-butyl phthalate |
DBP |
84-74-2 |
Repr. 1B
Aquatic Acute 1
(Repr. Cat. 2;R61
Repr. Cat. 3; R62
N; R50) |
Butyl benzyl phthalate |
BBP |
85-68-7 |
Repr. 1B
Aquatic Acute 1
Aquatic Chronic 1
(Repr. Cat. 2; R61
Repr. Cat. 3; R62
N; R50-53) |
Diisononyl phthalate |
DINP |
28553-12-0
68515-48-0 |
No harmonised classification |
Shall not be used as substances or as constituents of preparations, at concentrations of greater than 0,1% by mass of the plasticised material, in toys and childcare articles which can be placed in the mouth by children (Regulation No 552/2009) |
Diisodecyl phthalate |
DIDP |
26761-40-0
271-091-4 |
No harmonised classification |
Di-n-octyl phthalate |
DNOP |
117-84-0 |
No harmonised classification |
Diisobutyl phthalate |
DIBP |
84-69-5 |
Repr. 1B
(Repr. Cat. 2; R61
Repr. Cat. 3; R62 ) |
Not permitted for use in cosmetics (Directive 2004/93/EC) |
Table 2.2 Summary on application and technical properties of concerned phthalates
Chemical name |
Abb. |
Use and technical properties |
Di(2-ethylhexyl) phthalate |
DEHP |
Offers a good all-round performance and is therefore used for a great many cost-effective, general purpose products including building material such as flooring, cables, profiles and roofs, as well as medical products such as blood bags and dialysis equipment
The content of DEHP in flexible polymer materials varies, but is often around 30% (w/w). |
Di-n-butyl phthalate |
DBP |
Is a specialist plasticiser often used in combination with other high molecular weight phthalates.
It is a fast fusing plasticiser which by itself it is too volatile for PVC applications. It is frequently used as a gelling aid in combination with other plasticisers.
DBP is used extensively in the adhesives industry to plasticise polyvinyl acetate (PVA) emulsions and used solvent for many oil-soluble dyes, insecticides, peroxides and other organic compounds. It is used as an antifoam agent and as a fibre lubricant in textile manufacturing. |
Butyl benzyl phthalate |
BBP |
Butyl benzyl phthalate is an unusual plasticiser because of its chemical asymmetry which results in unique performance properties.
One of the manufacturing benefits of using BBP is that it allows PVC transformers to operate with less energy input than with many similar plasticisers.
It is used widely by the flooring industry because it adds surface properties to flooring materials that minimise maintenance and give it a prolonged life.
More than 90% of BBP is used for plasticising PVC or other polymers. Butyl benzyl phthalate is also used in seals for insulating double glazing |
Diisononyl phthalate |
DINP |
General, all-purpose plasticiser. Wide range of indoor and outdoor applications. 95 per cent of DINP is used as a plasticiser for flexible PVC used for construction and industrial applications, and durable goods (wire and cable, film and sheet, flooring, industrial hoses and tubing, footwear, toys, food contact plastics).
Heat resistance, low temperature resistance and volatility resistance are some of its main properties that make it suitable for a wide range of applications (ECPI, 2009) |
Diisodecyl phthalate |
DIDP |
Diisodecyl phthalate (DIDP) is a common phthalate plasticiser, used primarily to soften Polyvinyl chloride (PVC). The typical content of DIDP in flexible PVC products is between 25 and 50% (w/w).
It has properties of volatility resistance, heat stability and electric insulation and is typically used as a plasticiser for heat-resistant electrical cords, leather for car interiors, and PVC flooring (ECPI, 2009). |
Di-n-octyl phthalate |
DNOP |
The principal use of DNOP is as a plasticiser in the production of PVC resins and other polymers, such as cellulose esters and polystyrene resins, as a dye carrier in plastic production (primarily PVC), and as a chemical intermediate in the manufacture of adhesives, plastisols, and nitrocellulose lacquer coatings (ATSDR, 2005)
DNOP may represent 5 to 60% of the total weight of the plastics and resins (ATSDR, 2005)
No actual confirmation of the use of DNOP in the EU today has been identified |
Diisobutyl phthalate |
DIBP |
Diisobutyl phthalate (DIBP) is a specialist plasticiser often used in combination with other high molecular weight phthalates.
It is a fast fusing plasticiser which by itself it is too volatile for PVC applications. It is frequently used as a gelling aid in combination with other plasticisers.
A plasticiser for nitrocellulose, cellulose ether, and polyacrylate and polyacetate dispersions.
Has very similar application properties to DBP and may therefore be used to substitute for DBP in most, if not all, of its applications. |
The main alternatives to DEHP have been the two phthalates di-isononyl phthalate (DINP) and di-isodecyl phthalate (DIDP). As illustrated in Figure 2.3 in Sweden the shift from DEHP to first of all DINP took mainly place in the period 1999 to 2002.
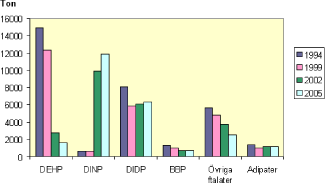
Figure 2.3 Use of plasticisers for PVC in Sweden. KemI (2008) quoting the Swedish Productregister as source. 2005 figures are indicated as "preliminary". "Övrige ftaalter" = "Other phthalates", ”Adipater” = ”Adipates”.
The evolution in the EU use of plasticisers shows that the consumption of DEHP deceased from 1999 to 2005 from 42% of the market to 21% (Figure 2.4). The DEHP was replaced by DINP/DIDP, while the non-phthalate plasticisers remained a market share of around 7-8%.
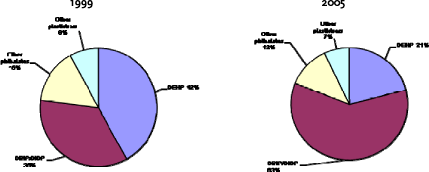
Figure 2.4 Evolution of PVC plasticisers’ sales between 1999 and 2005 (based on Cadogan, 2006)
Technical key parameters of some ortho-phthalates
For comparison with other plasticisers described in this report, some technical key parameters for selected phthalates are shown in Table 2.3. Note that for these related substances, the larger the molecule, the lower is the volatility, the extractability and the softness (efficiency), whereas the gelling temperature increases with higher molecule weight.
Click here to see: Table 2.3 Technical key parameters of selected phthalate plasticisers' performance in PVC (from Wilson, 1995, citing BP Chemicals)
2.2 Application of DEHP
The following information is, if nothing else is mentioned, extracted from an assessment of the manufacturing and use of di(2-ethylhexyl) phthalate (DEHP) recently published by the European Chemicals Agency (COWI, 2009a).
DEHP is widely used as a plasticiser in polymer products, mainly PVC. It offers a good all-round performance and is therefore used for a many general purpose products. The content of DEHP in flexible polymer materials varies, but is often around 30% (w/w).
The main end-product uses of DEHP are as follows:
- Flooring:
- PVC flooring (with PVC surface);
- Carpets with PVC back-coating;
- Cork with PVC top-coating or back-coating ;
- Wall covering;
- Roofing;
- Film/sheet and coated products:
- Curtains, blinds, table linen, etc.;
- Packaging;
- Tape and self-adhesive foils;
- Office supplies (ring binders, files, slip cases, etc.);
- Medical bag/sheet devices;
- Bottom sheets for hospitals.
- Wires and cables;
- Hoses and profiles;
- Garden hoses and tubes;
- Hoses and tubes in industry;
- Profiles of windows and electrical products;
- Medical tubing.
- Coated fabric;
- Upholstery and car seats (synthetic leather);
- Luggage;
- Rainwear;
- Tarpaulins;
- Water beds.
- Moulded product;
- Footwear;
- Adult toys; (DEHP is not permitted in toys for children)
- Car undercoating;
Non-polymer applications:
- Adhesives;
- Lacquers and paints;
- Printing inks (see comment below);
- Sealants (glass insulation, construction);
- Ceramics.
The main part of DEHP is added to PVC in different formulation and processing steps including calendering, extrusion, spread coating, and moulding.
At EU level in total 341,000 tonnes was produced in 2007. A part of this was exported and around 291,000 tonnes DEHP was used for manufacturing processes in the EU in 2007. DEHP accounted for around 18% of all plasticiser usage in Western Europe (data for the entire EU plasticiser use is not available). The consumption of DEHP has decreased markedly the last decade. Of the 341,000 tonnes produced in the EU in 2007, 187,000 tonnes were produced in Western Europe corresponding to 31% of the 1997 level of 595,000 t/y. In the early 1990s, DEHP represented about 51% of the total phthalate plasticiser market in Western Europe.
Investigations of the historic use of phthalates in Denmark in different products shows that DEHP represented a major part of the phthalate use in the 1990's and was to a large extent replaced by DINP around 2000. Today DEHP seems to have been replaced by DINP or non-phthalate plasticisers in Danish produced PVC products (Christensen et al., 2007; Brandt et al., 2009).
Quantitative information is available on the approximate split between the different processes. In combination with information on which products are produced by different processes it is possible to indicate the main and uses of DEHP as illustrated in Figure 2.5.
Click here to see: Figure 2.5 Overall flow of DEHP through manufacturing processes in 2007. For processing steps without prior formulation step, the formulation and processing are integrated in one step. All figures in tonnes DEHP/year. (COWI, 2009a)
DEHP is to some extent imported and exported with finished products. Table 2.4 shows the estimated extra-EU import and export for some of the main product groups, for which information can be estimated on the basis of the trade statistics (please see COWI, 2009a for details regarding the calculation method). For most product groups the net import is relatively small compared to the production within the EU, and the end-use distribution follows in broad outline the distribution of EU production.
Table 2.4 Estimated DEHP tonnage in end-products marketed in the EU based on EU manufacture and EU-extra import and export data (based on COWI, 2009a)
End-product use area |
Tonnage, t/y |
% of |
|
EU Manufacture |
Import |
Export |
End-product use |
total use |
Polymeric applications: |
|
|
|
|
|
Flooring |
33,000 |
2,000 |
4,800 |
30,200 |
10.6 |
Wall covering |
11,000 |
700 |
1,600 |
10,100 |
3.5 |
Roofing material |
3,600 |
n.d. |
n.d. |
3,600 |
1.3 |
Film/sheet and coated products made by calendering |
44,000 |
13,600 |
16,400 |
41,200 |
14.5 |
Wires and cables |
64,100 |
6,200 |
5,600 |
64,700 |
22.3 |
Hoses and profiles |
34,700 |
1,600 |
3,000 |
33,300 |
12.7 |
Coated fabric and other products from plastisol |
43,800 |
2,200 |
1,400 |
44,600 |
15.1 |
Shoe soles |
19,400 |
n.d. |
n.d. |
19,400 |
6.8 |
Other moulded products |
3,000 |
2,700 |
700 |
5,000 |
1.8 |
Car undercoating |
4000 |
n.d. |
n.d. |
4000 |
1.4 |
Other polymer applications |
12,300 |
10,900 |
3,100 |
20,100 |
7.1 |
Non polymer applications: |
|
|
|
|
0.0 |
Adhesives and sealant |
4,000 |
n.d. |
n.d. |
4,000 |
1.4 |
Lacquers and paints |
900 |
n.d. |
n.d. |
900 |
0.3 |
Adhesives and sealant |
3300 |
n.d. |
n.d. |
3300 |
1.2 |
Printing ink |
1,000 |
n.d. |
n.d. |
1,000 |
0.4 |
Other non-polymeric |
20 |
n.d. |
n.d. |
20 |
0.0 |
Total end-product use (round) |
282,000 |
40,000 |
37,000 |
285,000 |
100 |
2.3 Application of DBP
The following information is, if nothing else is mentioned, extracted from an assessment of the manufacturing and use of dibutyl phthalate (DBP) recently published by European Chemicals Agency (COWI, 2009b).
DBP is a specialist, fast fusing plasticiser. By itself it is too volatile for PVC applications and it is used in PVC as a gelling aid in combination with other high molecular weight plasticisers. The gelling agent is the agent which reacts fastest with the PVC.
The total manufactured tonnage in 2007 in the EU is confidential, but it was less than 10,000 tonnes. A significant part of the manufactured tonnage is exported to countries outside the EU. DBP seems to represent less than 1% of the production of phthalates in Europe. As DBP is used in relatively small concentrations it may however be present in higher share of products. Dutch surveys of phthalates and other plasticisers in toys and childcare products demonstrate that 30% of 24 analysed products in 2004 contained DBP (FCPSA, 2008a). The share had decreased to 13% of the products in 2007 and 1% in 2008 (FCPSA, 2008b).
The market for DBP has been decreasing over recent decades: In 1994 the production volume of DBP in the EU was 49,000 tonnes and in 1998 it was 26,000 tonnes, with an export of 8,000 tonnes.
Current uses of DBP, according to actual information obtained from industry or product registers, are listed below:
- Gelling aid in combination with other plasticisers in plastics. In general, limited information is available on the actual uses of DBP in polymers. DBP is used in PVC (manufacturer information). It has not been possible to obtain very specific information on the uses, but the following applications are mentioned by different sources: floor coverings, automotive uses (manufacturer information) and garden hoses. The European Plastic Converters (EuPC), has in a survey by their members not indentified any use of DBP, and assume that DBP today is used by relatively few companies for different niche purposes. The results of the Dutch surveys show that DBP was formerly used at a relatively high frequency in many different types of toys (FCPSA, 2008a).
- Rubbers (manufacturer information). The Risk Assessment for DBP (ECB, 2004) specifies that DBP is used in some polychloroprene rubber and nitrile rubber, but not in all polychloroprene (neoprene) or nitrile rubbers. New information on actual uses is not available.
- DBP is used extensively in the adhesives industry to plasticise polyvinyl acetate (PVA) emulsions. The low viscosity and compatibility of DBP make it suited for PVA-based adhesives for bonding cellulosic materials. According to the Risk Assessment for DBP (ECB, 2004) the most important uses of the adhesives are for paper and packaging, wood building and automobile industry.
- Epoxy resins. Probably same application that in the Risk Assessment for DBP (ECB, 2004) is mentioned as "solvent in the production of fiber glass". More specific information on this application has not been available.
- In the coatings industry as a primary plasticiser-solvent for nitrocellulose lacquers.
- Grouting agents, used to reduce water leakages in tunnels, sewer systems, buildings etc. DBP contents as high as 30-60% were found in polyurethane foams used in grouting applications for water control in tunnels, sewer systems, buildings etc. No actual confirmation of this application has been obtained.
- Other applications:
- Solvent for many oil-soluble dyes, insecticides, peroxides and other organic compounds;
- Antifoam agent and as a fibre lubricant in textile manufacturing;
- Used in compounding flavours;
- Printing inks, polishing agents, corrosion inhibitor materials;
- Use in PP (polypropylene) catalytic systems;
- One application described in the confidential part of the ECHA report.
According to CEPE (European Council of producers and importers of paints, printing inks and artists’ colours), DEHP, BBP and DBP are no longer used in printing inks by CEPE/EuPIA (European Printing Ink Association) members following its classification as reprotoxic.
The flow chart below illustrates the "best estimate scenario" for the flow of DBP through the different process and the resulting end-products. It was for the ECHA report (COWI, 2009b) not possible to obtain comprehensive quantitative updated information on the use of DBP for the different uses from manufacturers and suppliers and the available information did not allow real estimates of the distribution between the different use areas to be made. It is, however, deemed that the distribution between applications most likely is different from the 1997 distribution used in the RAR, but the updated distribution is highly uncertain. The figures are for confidentiality reasons rounded and somewhat higher than the actual figures.
Click here to see: Figure 2.6 "Best estimate scenario" of the overall flow of DBP through manufacturing processes. Tonnes DBP/year. Figures are rounded and higher than actual figures. (COWI, 2009b)
DBP may be exported and imported in preparations and articles, but no statistical information allowing an estimate of this import/export is available.
Use in Denmark
No detailed assessment of the use of DBP in Denmark exists. The use of DBP in chemical products (preparations) registered in the Danish product register is shown in Table 2.5. The total consumption of DBP in declared preparations has decreased from 320 tonnes/year in 2000 to 71 tonnes/year in 2004. In the period from 2004 to 2006 the registered consumption was stable at a level of 70-80 tonnes. The main use category was paint, lacquers and varnishes and in total 56 different products within this use category in was registered in 2006. Other preparations representing significant uses of DBP were binding agents (may be used as synonymous for adhesives) and corrosion inhibitors/under seal materials.
The declaration of the substances to the product register is mandatory for preparations containing one or more substances listed in Annex 1 of Directive 67/548/EEC (now the Annex VI to Regulation 1272/2008). All preparations containing DBP should consequently be declared. However, there is no systematic updating of quantities of products. The companies are obliged to send in any new information regarding their products whenever changes occur. If companies fail to fulfil their obligations, a result might be that products that have been discontinued still remain on the lists. The relatively high consumption of DBP in paint, lacquers and varnishes may reflect that DBP is used for production of some specific paints by Danish paint manufacturers.
The data shows a steep decrease i the use of DBP in "flooring materials", "casting materials", " printing inks", "adhesives" and "other".
Table 2.5 Uses of DBP registered in the Danish product register (SPIN, 2009)
Product group |
Registered consumption, tonnes DBP/year |
|
2006 |
2005 |
2004 |
2003 |
2002 |
2001 |
2000 |
Paint, lacquers and varnishes |
64.7 |
69.4 |
67.0 |
29.0 |
27.8 |
27.9 |
63.4 |
Binding agents |
9.1 |
1.4 |
0.8 |
21.1 |
13.3 |
21.4 |
21.7 |
Filling materials |
0.2 |
0.2 |
0.2 |
2.7 |
51.1 |
49.1 |
50.2 |
Hardeners, curing agents |
1.7 |
2.0 |
2.0 |
5.9 |
9.8 |
10.3 |
28.6 |
Flooring materials (joint-less floors) |
0.0 |
0.1 |
0.1 |
18.3 |
18.9 |
19.0 |
19.0 |
Corrosion inhibitors, anticorrosive paints, underseal materials, incl. cavity seals |
3.9 |
0.1 |
0.1 |
0.2 |
0.3 |
0.3 |
0.7 |
Casting materials |
0.5 |
0.1 |
0.1 |
3.3 |
4.2 |
4.3 |
6.1 |
Surface treatment for non-metals |
0.0 |
0.1 |
0.1 |
1.7 |
1.7 |
1.7 |
1.7 |
Polishing agents |
0.2 |
0.2 |
0.2 |
0.6 |
0.0 |
0.0 |
1.2 |
Printing inks |
0.7 |
0.9 |
0.1 |
0.7 |
0.3 |
0.3 |
102.0 |
Adhesives |
0.0 |
0.0 |
0.0 |
4.4 |
0.2 |
0.2 |
16.8 |
Other |
0.0 |
0.0 |
0.0 |
8.7 |
22.4 |
29.5 |
8.7 |
Total |
81 |
75 |
71 |
97 |
150 |
164 |
320 |
2.4 Application of BBP
The following information is, if nothing else is mentioned, extracted from an assessment of the manufacturing and use of butyl benzyl phthalate (BBP) recently published by European Chemicals Agency (COWI, 2009c).
The total manufactured tonnage in 2007 in the EU was below 18,000 tonnes. A significant part of the manufactured tonnage is exported to countries outside the EU. BBP seems to represent less than 1% of the production. The market for BBP has been decreasing over the last decade. In the period 1994-1997, the total reported Western European manufacture of BBP was 45,000 tonnes/year whereas for 2004 a production volume of 19,500 tonnes/year was reported.
More than 70% of the BBP was in 2007 used as a plasticiser in polymer products, mainly PVC for flooring. BBP is, according to industry, an unusual plasticiser because of its chemical asymmetry which results in unique performance properties.
BBP is typically used together with other plasticisers e.g. DEHP or DINP. It has not been possible to identify information on typical concentration of BBP in the final materials, but examples of formulations indicate that the concentration may be in the range of 5-20%. As an example Eastman (2001) compares two different BBP/DINP plastisol formulations with other formulation. One of the formulations has 12 parts BBP and 28 parts DINP (together with other additives) to 100 parts PVC whereas the other has 24 parts BBP and 56 parts DINP to 100 parts PVC.
BBP is used widely by the flooring industry because it speeds up production and adds surface properties to flooring materials that minimise maintenance and give it a prolonged life.
The end-product uses of BBP are as follows:
- Flooring (both calendered and spread coated flooring);
- Wall covering;
- Coating of leather and textiles (upholstery, shoe uppers, wallets/bags, luggage);
- Packaging films;
- Sealants (polysulphide based, polyurethane based or acrylic-based) for insulating double glazing and other applications;
- Paints for car care and construction (acrylic lacquers and other);
- Inks for paper and board;
- Adhesives (polyvinyl acetate and other);
- Miscellaneous (hard PVC, nitrile rubber and other).
The main part of BBP is added to PVC in different formulation and processing steps including calendering and plastisol spread coating. The following flow diagram illustrates the relationship between the different processes and the end-product uses. The major application area is flooring accounting for about 50% of the total while the second larges application area, polysulphide sealants account for about 19% of the total.
Click here to see: Figure 2.7 Overall flow of BBP through manufacturing processes in 2007. Tonnes BBP/year (COWI, 2009c)
BBP may be exported and imported in preparations and articles, but no statistical information allowing an estimate of this import/export is available.
Use in Denmark
No detailed assessment of the use of DBP in Denmark exists. The use of DBP in chemical products (preparations) registered in the Danish product register is shown in Table 2.6. The total consumption of DBP in declared preparations has decreased from 233 tonnes/year in 2000 to 75 tonnes/year in 2004. In the period from 2004 to 2006 the registered consumption was fairly stable at a level of 60-75 tonnes.
The main use categories were filling materials (may be used synonymous with sealants), paint, lacquers and varnishes and adhesives. The increase in the use of DBP from a level below 1 tonnes/year in 2000-2005 to 11 tonnes in 2006 may be due to an error in the registration.
The declaration of the substances to the product register is mandatory for preparations containing one or more substances listed in Annex I to Directive 67/548/EEC (now Annex VI to Regulation 1272/2008) . All preparations containing BBP should consequently be declared. However, there is no systematic updating of quantities of products. The companies are obliged to send in any new information regarding their products whenever changes occur. If companies fail to fulfil their obligations, a result might be that products that have been discontinued still remain on the lists. This may explain the relatively high registered consumption of DBP in preparations in Denmark compared to the EU consumption for non-polymeric applications as shown in Table 2.5.
Table 2.6 Consumption of BBP registered in the Danish product register (SPIN, 2009)
Product group |
Registered consumption, tonnes BBP/year |
|
2006 |
2005 |
2004 |
2003 |
2002 |
2001 |
2000 |
Filling materials |
47.8 |
46.7 |
46.7 |
65.0 |
19.2 |
8.4 |
79.3 |
Paint, lacquers and varnishes |
14.9 |
8.7 |
25.5 |
18.4 |
9.3 |
14.2 |
45.8 |
Adhesives |
10.9 |
0.1 |
0.2 |
0.5 |
0.1 |
0.1 |
0.3 |
Casting materials |
0.2 |
2.7 |
2.7 |
0.0 |
7.0 |
7.0 |
0.0 |
Binding agents - for binding together the individual constituents in the product |
0.4 |
0.0 |
0.0 |
1.1 |
2.9 |
2.9 |
3.9 |
Padding materials |
0.0 |
0.0 |
0.0 |
0.0 |
40.1 |
40.1 |
0.0 |
Tightening materials (putty) |
0.0 |
0.0 |
0.0 |
0.0 |
28.5 |
28.6 |
0.0 |
Other and unknown function |
0.3 |
0.3 |
0.3 |
0.5 |
164.8 |
110.9 |
103.3 |
Total |
75 |
59 |
75 |
86 |
272 |
212 |
233 |
| Front page | | Contents | | Previous | | Next | | Top |
Version 1.0 November 2010, © Danish Environmental Protection Agency
|