| Forside | | Indhold | | Forrige | | Næste |
Miljø- og sundhedsforhold for plastmaterialer
13 Ekstrudering
Se også:
Termoplastbranchens_råvarer
Emissioner ved forarbejdning af termoplast
Kemiske belastninger i arbejdsmiljøet
Miljø- og sundhedsvurderinger
Referencer
Indholdsfortegnelse
Oversigtsfigur
13.1 Introduktion
Den følgende beskrivelse af ekstruderingsbranchen og dens produkter er i al væsentlighed baseret på rapporten ”Renere teknologi i plastindustrien” (Plastindustrien i Danmark, 2000) og lærebogen ”Plastteknologi” Jensen et al. (2005). Det er ikke forsøgt at opdatere de to kilders oplysninger om råvareforbrug mv.
13.2 Kort om ekstruderingsbranchen
Ekstrudering er fællesbetegnelsen for en kontinuerlig proces, som anvendes til fremstilling af en lang række produkter, der kendes fra dagligdagen. Plastfolie (plastposer), rør, profiler, plader, kunstfibre, slanger og isolerede ledninger og kabler er alle eksempler på ekstruderede produkter.
Ekstruderingsbranchen er volumenmæssigt den største delbranche i Plastindustrien. Der anvendes en lang række råvarer, hvor polyethylen (PE), polypropylen (PP) og polyvinylchlorid (PVC) er de vægtmæssigt mest betydende, fulgt af polystyren (PS) og polyethylenterephthalat (PET) og i mindre omfang acrylonitril-butaidien-styren (ABS), polycarbonat (PC) og andre plasttyper.
Der anvendes en bred vifte af additiver ved ekstrudering. I de følgende afsnit nævnes en række additiver, der anvendes ved typiske produkter og processer, men listen er langt fra udtømmende.
13.3 Ekstruderingsprocessen
Et ekstruderingsanlæg består generelt af en eller flere ekstrudere samt noget følgeudstyr. Ekstruderen anvendes til at fremstille en sejtflydende, formbar plastmasse, som efterfølgende kan formes til f.eks. et af ovennævnte produkter, mens følgeudstyret er specielt fremstillet til det produkt, man ønsker at fremstille.
Ved fremstilling af de fleste af ovennævnte produkter kan coekstrudering komme på tale. Dette begreb dækker over anvendelsen af mere end 1 ekstruder til fødning af værktøjet. Herved er man i stand til at fremstille produkter sammensat af flere forskellige råvarer, hvilket giver mange interessante produktmuligheder.
Figur 1. Principskitse af ekstruder. (Kilde: PlastTeknologi-lærebogen udgivet af Erhvervsskolernes Forlag)
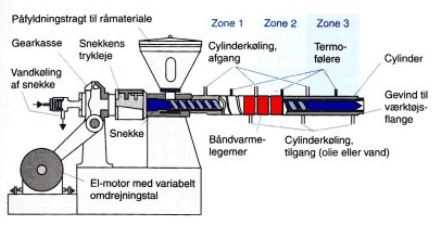
Råvaren, som oftest er i granulatform, fødes fra ekstruderens tragt til snekkens indtrækszone, hvorfra den føres fremad (som i en kødhakkemaskine) af den roterende snekke. Dels på grund af varmen fra den tempererede cylinder, men især på grund af friktionen mod cylinderen og den indre friktion i selve råvaren, opvarmes denne og bliver til en sejtflydende, formbar masse, lidt inden, den når enden af cylinderen. På grund af snekkens udformning opbygges der også et relativt højt tryk for enden af snekken, som skal bruges til at presse plastmassen igennem det værktøj, der spændes på enden af ekstruderen. Afhængigt af værktøjets udformning kan der herefter fremstilles (formes) en lang række forskellige produkter.
13.3.1 Folieekstrudering
Ved folieekstrudering er ekstruderen monteret med et folieværktøj, der kan lave en tyndvægget slange, som danner udgangspunkt for det færdige produkt. Normalt ekstruderes slangen i lodret, opadgående retning. Slangen føres op til aftræksvalserne, som klemmer slangen flad. Det er herefter muligt at blæse luft ind i slangen for at udvide den til den ønskede diameter, som er bestemmende for den færdige foliebredde, ligesom aftræksvalsernes hastighed kan indstilles, så man opnår den ønskede folietykkelse. Udvendig køles slangen (boblen) af med luft, og når aftræksvalserne er passeret, kan den fladlagte, orienterede plastslange spoles op. Denne kan så enten i processen eller senere skæres op i den ønskede bredde.
Figur 2. Principskitse af folieekstruder.. (Kilde: PlastTeknologi-lærebogen udgivet af Erhvervsskolernes Forlag)
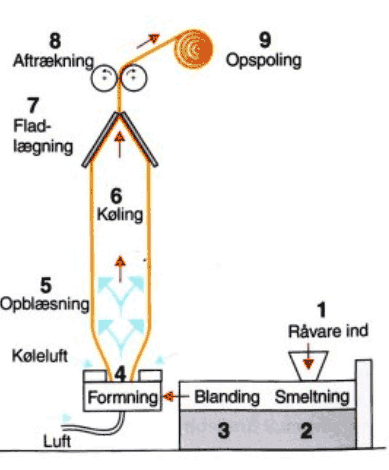
13.3.2 Ekstrudering af rør
Ved ekstrudering af rør fremstiller det værktøj, der monteres på enden af ekstruderen, et rør eller en slange med nogenlunde den dimension, man ønsker for det færdige produkt. Det kan dog varieres inden for visse grænser. Når den bløde slange forlader værktøjet, føres den ind i en kalibrering, som skal sørge for, at rørets eller slangens udvendige diameter bliver korrekt. Rørets/slangens overflade presses mod kalibreringen ved hjælp af vakuum eller trykluft. Under og efter kalibreringen afkøles plastmaterialet i et eller flere vandbade eller brusekamre. Fremføringen foregår mellem to larvefodslignende transportbånd, som holder en konstant aftrækshastighed, og til sidst sker der en afkortning eller opspoling af det færdige produkt.
Figur 3. Principskitse for en rørekstruder. (Kilde: PlastTeknologi-lærebogen udgivet af Erhvervsskolernes Forlag)
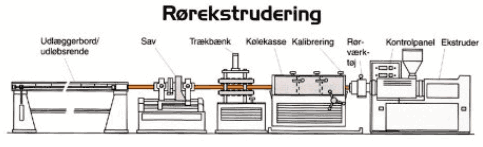
13.3.3 Profilekstrudering
Principielt er der ikke den store forskel på ekstrudering af rør/slanger og profiler. Ofte vil selve værktøjskonstruktionen dog være mere kompliceret. Profilværktøjet, som skal forme den bløde plastmasse til en profil, monteres for enden af ekstruderen. Umiddelbart efter dyseudløbet føres den varme profil ind i en vakuumkalibrering, som omslutter profilets udvendige overflade, for at holde de ønskede mål, mens profilet afkøles. Afkølingen foregår i et eller flere vandbade eller brusekamre. Fremføringen foregår mellem to larvefodslignende transportbånd, som holder en konstant aftrækshastighed. Afhængig af materialets stivhed og de ydre dimensioner sker der til sidst enten en afkortning eller opspoling af slutproduktet.
Figur 4. Priincipskitse af profilekstruder. (Kilde: PlastTeknologi-lærebogen udgivet af Erhvervsskolernes Forlag)
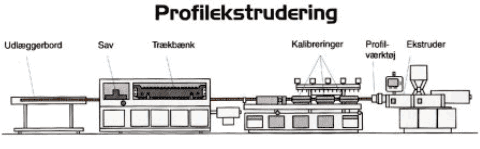
13.3.4 Plade- og planfolieekstrudering
Til plade- og planfolieekstrudering anvendes et fladdyseværktøj med en specielt udformet flydekanal, som former den bløde plastmasse til et bredt bånd. Straks efter, at båndet forlader dysen, føres det ind imellem et antal tempererede valser, som glatter og afkøler materialet. Herefter skæres kanterne af for at opnå den ønskede plade- eller foliebredde, og til sidst klippes pladerne til det ønskede længdemål eller rulles op i ”endeløse” baner.
13.3.5 Monofilamentekstrudering
Monofilamenter, som betyder enkelte tråde/fibre, fremstilles ved at spænde en dyse med et passende antal huller for enden af ekstruderen. Den varme plastmasse formes til et antal tråde, som føres lodret ned i en køletank med tempereret vand. Herefter føres trådene omkring et antal valser (ofte 7), som sørger for et konstant aftræk fra dysen. Herfra føres trådene gennem en luftovn eller et tempereret vandbad, som opvarmer trådene, og derefter omkring et antal valser (ofte 7), som kører ca. 8-10 gange hurtigere end de før omtalte. Herved strækkes trådene i længderetningen og øger derved trækstyrken betydeligt p.g.a. den langsgående orientering. Efter en yderligere opvarmning i en luftovn føres de strakte tråde omkring endnu et sæt valser, som kører lidt langsommere end ”strækvalserne”. Herved aflastes trådene, så de bliver mere fleksible, ligesom de vil krympe mindre ved en fornyet opvarmning under brug. Til sidst spoles monofilamenterne op på passende spoler og er herefter klar til brug.
Figur 5. Principskitse for en monofilamentekstruder. (Kilde: PlastTeknologi-lærebogen udgivet af Erhvervsskolernes Forlag)
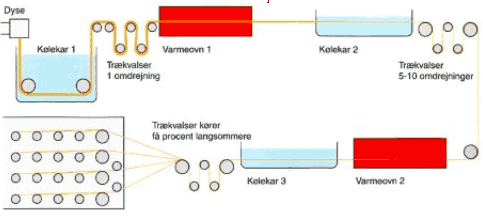
13.3.6 Kabelisolerings- og kapperørsekstrudering
Til dette formål monteres ekstruderen med et sidefødt rørværktøj, der kan forme et isolerende plastlag uden om det ledende materiale. Princippet kan også anvendes til plastbelægning af rør og lignende. Det forvarmede ledende materiale føres gennem dysens centrum og ekstruderen, som er placeret på den ene side af dysen, og føder denne med det isolerende plastmateriale, der lægger sig som et ”rør” uden om det materiale, der skal isoleres eller belægges. Herefter skal belægningen nedkøles i et kølebad, som kan være endog meget langt p.g.a kabelindustriens høje hastigheder. Hastigheden kontrolleres af en til formålet konstrueret ”trækbænk”, og det færdige produkt kan herefter afkortes på en indbygget sav eller opspoles, som det selvfølgelig sker for ledninger og kabler.
Figur 6. Principskitse af en ekstruder til kabelisolering. (Kilde: PlastTeknologi-lærebogen udgivet af Erhvervsskolernes Forlag)
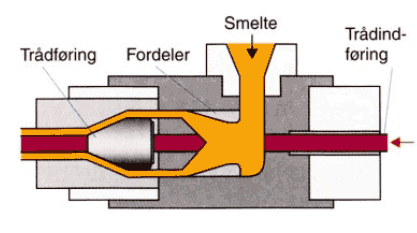
13.4 Ekstruderingsbranchens produkter og dens karakteristika
13.4.1 Rør
Produktionen i Danmark omfatter rør til ledning af vand, herunder trykrør (PE+PVC), afløbsrør (PE, PP og PVC), drænrør (PVC), gasrør (PE) og fjernvarmekapperør (PE).
13.4.1.1 Trykrør - PE
I Danmark findes 3 producenter af trykrør til vand. Rørene fremstilles i Danmark af MDPE og efter følgende standard: EN12201.
Rørproducenten tilsætter hverken pigmenter eller additiver selv. Der indkøbes færdigblandet råvare, såkaldt compound. Lyseblå rør er tilsat et blåt organisk pigment. Rørets blå farve er en kode for rør til drikkevand. Visse rør er endvidere farvet sorte ved tilsætning af pigmentet carbon black.
En leverandør oplyser, at den leverede polymer til PE-rør kan være tilsat UV-stabilisator, antioxidant og smøremiddel. UV-stabilisatoren er ofte sterisk hindrede aminer indeholdende ester- og/eller piperidingrupper. Antioxidanterne er typisk hydroxy-phenyl propionatbaserede og/eller fosfitbaserede. Smøremidlet er typisk calciumstearat, zink- eller natriumsalte eller blandinger heraf. Herudover er compounden ikke tilsat additiver.
13.4.1.2 Trykrør – PVC
I Danmark findes 2 producenter af PVC-trykrør. Trykrør af PVC fremstilles i Danmark blandt andet efter følgende standard: EN 1452.
Rørproducenten tilsætter selv additiver til råvaren. Som stabilisator anvendes Ca/Zn-forbindelser eller OBS (Organically Based Stabiliser), der angiveligt har et højere metalindhold end Ca/Zn-forbindelserne, på trods af navnet. Producenten tilsætter endvidere selv pigmenter. Det typiske pigment, som anvendes til PVC-trykrør til vand er enten et blåt organisk pigment eller carbon black. Endelig tilsættes der proceshjælpemidler, typisk i form af kridt. Herudover tilsættes PVC-polymeren til trykrør ikke yderligere additiver.
13.4.1.3 Afløbsrør - PE
I Danmark findes 1 producent af PE-afløbsrør. Rørene fremstilles i Danmark af HDPE og bl.a. efter standarden EN 13244. Rørene fremstilles på en måde, som adskiller sig radikalt fra den almindelige fremstillingsmetode til rør. Et bånd af HDPE ekstruderes og vikles omkring et roterende metalvæv. Samlingerne svejses sammen efterfølgende. Metoden anvendes til fremstilling af store rør (diameter > 1 m).
Der indkøbes såkaldt compound, og rørproducenten tilsætter hverken additiver eller pigmenter til råvaren.
PE-afløbsrør er sorte rør, og plastråvaren er tilsat pigmentet carbon black. Den leverede compound til afløbsrør er endvidere tilsat samme additiver (UV-stabilisator og antioxidant) som er tilfældet for blandt andet trykrør af PE. Herudover tilsættes compounden ikke additiver.
13.4.1.4 Faldrør og kloakrør af PP
Invendige faldrør og kloakrør fremstilles i Danmark efter standarderne EN 1451, henholdsvis EN 1852. De udgør cirka 10% af markedet. Der er ingen oplysninger om, hvordan plasten er modificeret eller farvet.
13.4.1.5 Afløbsrør – PVC
I Danmark findes 2 producenter af PVC afløbsrør. Afløbsrør af PVC fremstilles i Danmark efter følgende standard: EN 1401.
Rørproducenten tilsætter selv additiver til råvaren. Som stabilisator anvendes Ca/Zn-forbindelser eller OBS (Organically Based Stabiliser), der angiveligt har et højere metalindhold end Ca/Zn-forbindelserne, på trods af navnet. Producenten tilsætter endvidere selv pigmenter. Afløbsrør til indendørs brug er farvet grå med carbon black. Afløbsrør til udendørs brug er "lerfarvede". Der tilsættes fyldstoffer typisk i form af kridt. Herudover tilsættes PVC-polymere til afløbsrør ikke additiver.
13.4.1.6 Drænrør
I Danmark findes 2 producenter af drænrør. Drænrør af PVC fremstilles i Danmark efter følgende standard: DS 2077 del 1 og 2 + SBC 211.
Rørproducenten tilsætter selv additiver til råvaren. Som stabilisator anvendes Ca/Zn-forbindelser eller OBS (Organically Based Stabiliser), der angiveligt har et højere metalindhold end Ca/Zn-forbindelserne, på trods af navnet. Producenten tilsætter endvidere selv pigmenter. Drænrør er "lerfarvede". Herudover bliver PVC til drænrør tilsat slagmodificerende polymerer i koncentrationer på op til 5 pct. Polymererne kan bl.a. være af chloreret PE eller ABS. Der tilsættes fyldstoffer typisk i form af kridt. Herudover tilsættes PVC-polymerer til drænrør ikke additiver.
13.4.1.7 Gasrør
I Danmark findes 2 producenter af gasrør. Rørene fremstilles i Danmark af MDPE og efter følgende standard: EN 1555.
Rørproducenten tilsætter hverken additiver eller pigmenter til råvaren. Der indkøbes såkaldt compound.
Gasrør er farvet gule, idet gul er en farvekode, som signalerer en advarsel om fare for gasudslip. Det gule pigment er et organisk pigment. Indtil midten af 1980’erne siden var pigmentet cadmiumgult, men i dag fremstilles alle gasrør i Danmark med cadmiumfrie pigmenter. Visse gasrør kan endvidere også være farvet sorte med carbon black.
En leverandør oplyser, at den leverede polymer til PE-rør kan være tilsat UV-stabilisator, antioxidant og smøremiddel. UV-stabilisatoren er ofte sterisk hindrede aminer indeholdende ester og/eller piperidingrupper. Antioxidanterne er typisk hydroxy-phenyl-propionatbaserede og/eller fosfitbaserede. Smøremidlet er typisk calciumstearat, zink- eller natriumsalte eller blandinger heraf. Herudover er compounden ikke tilsat additiver.
13.4.1.8 Kapperør (til fjernvarmerør)
I Danmark findes 4 producenter af fjernvarmerør, som alle selv fremstiller kapper. Kapperør fremstilles af HDPE og efter standard EN 253. I denne standard er det bl.a. fastlagt, at kapperør max. må indeholde 15 pct. regenerat og at det skal være fra virksomhedens eget produktionsaffald. I standarden er vedhæftningen mellem kapperørets inderside og isole-ringsskummet endvidere fastlagt.
Rørproducenterne anvender enten færdig PE-compound eller tilsætter selv additiver og pigmenter i form af masterbatch til den leverede polymer. Både den færdigt compounderede og den masterbatchtilsatte polymer til kapperør indeholder carbon black (sort pigment + UV-stabilisator). En leverandør oplyser, at deres råvarer til kapperør herudover indeholder under 0,5 pct. varmestabilisator. Denne varmestabilisator er baseret på antioxidanter indeholdende hydroxy-phenyl-propionater. Herudover er compounden ikke tilsat yderligere additiver.
13.4.2 Slanger
Ekstruderede plastslanger anvendes fortrinsvis som haveslanger, industrislanger til transport af vand, væske og luft, levnedsmiddelslanger samt som medicinske slanger. Typisk er plastslanger fremstillet af blødgjort PVC. Ekstrudering af slanger adskiller sig i princippet ikke fra ekstrudering af rør. Den væsentligste forskel er, at slanger fremstilles i blødgjort PVC, og at ekstruderen til slangefremstilling typisk er enkeltsnekket.
PVC-slanger ekstruderes typisk ved en temperatur på 150-160 °C, og fremstillingen kræver totalt ca. 0,35 kWh pr. kg. råvare inkl. el til administration.
Slangerne er bl.a. kendetegnet ved lang levetid, god styrke og evne til at sikre et flow uden at kinke (knække sammen). Det skal nævnes, at der stilles særlige krav til fremstilling af medicinske slanger, bl.a. foregår produktionen af disse i specielle renrum.
13.4.2.1 PVC-slanger til industri, havebrug mm.
Industrislanger anvendes til transport af vand, væske og luft i industrien. En mindre mængde slanger anvendes i levnedsmiddelindustren. Endvidere anvendes PVC-slanger som haveslanger.
Slangerne består typisk af flere forskellige lag PVC, som coekstruderes omkring en armering af polyesterfibre. Der er to producenter af disse slanger i landet. Herudover findes en lille håndfuld producenter som fremstiller relativt små mængder specialslanger.
PVC-slangerne er blødgjort med ca. 30 pct. DEHP, dog er de levnedsmiddelslanger, som anvendes specielt til transport af mælk typisk blød-gjort med en polymer blødgører (adipinsyrebaseret polyester). Slanger fremstillet i Danmark stabiliseres altid med calcium-/zinkstabilisatorer. Både blødgøreren og stabilisatoren er tilsat den leverede råvare. Slangeproducenten tilsætter alene pigmenter til råvaren. Disse tilsættes i form af masterbatch. De typisk anvendte pigmenter er titanoxid, jernoxid, og carbon black. Herudover tilsættes endvidere en mindre del pigmenter alle af organisk karakter.
Udover blødgører og stabilisator indeholder PVC-råvaren et smøre-middel bestående af en amidvoks samt epoxyderet soyabønneolie (co-stabilisator). Herudover er den leverede compound ikke tilsat additiver.
Der anvendes ofte store dele PVC-regenerat som råvare ved fremstillingen af haveslanger. Regeneratet coekstruderes til de "indre lag" af slangerne.
13.4.2.2 Slanger til medicinsk brug
Produkterne i denne gruppe anvendes til hospitalsslanger, katetre, rør, sug etc. Der er 2 producenter af medicinske slanger i Danmark. Fremstilling af slangerne foregår i renrum. Materialekvalitetskravene til medicinske slanger er fastlagt i European Pharmacopeia VI, 1212.
Råvaren (compounden) til fremstilling af medicinske slanger er blødgjort med DEHP og stabiliseret med calcium/zink stabilisatorer samt med epoxyderet soyabønneolie (co-stabilisator). Herudover indeholder compounden et smøremiddel bestående af en amidvoks. Endelig kan compounden indeholde små mængder blå eller violet pigment. Begge pigmenter er af organisk karakter. Pigmentet tilsættes for at give slangen en neutralt udseende farve i modsætning til den lidt gullige nuance blødgøreren kan give.
Herudover er compounden til fremstilling af medicinske slanger ikke tilsat andre additiver.
13.4.3 Profiler
Ved ekstrudering fremstilles en stor og varieret gruppe af profiler i mange forskellige materialer, med vidt forskellige anvendelsesformål som f.eks. profiler til fremstilling af vinduesrammer (PVC), tagrender og nedløbsrør (PVC), tætningsrammer til køle- og fryseskabe (PVC samt blødgjort PVC). Profilekstrudering omfatter endvidere fremstilling af tagplader af PVC og PC, idet teknikken hertil er beslægtet med teknikken til fremstilling af profiler i almindelighed.
En restgruppe "andre" profiler, omfatter tusindvis af forskellige lister til vidt forskellige formål som f.eks. møbellister, plakatlister, gulvlister og "trælister", tekniske lister og kabelafdækningsbånd m.m. Disse profiler fremstilles fortrinsvis i PE, PVC, PS, ABS samt i termoplastiske elastomerer. Volumenmæssigt skønnes det, at denne rest-gruppe anvender få tusinde tons pr. år og at gruppens produkter fremstilles af ca. 10 producenter i Danmark.
13.4.3.1 PVC-profiler
Som det fremgår af ovennævnte tabel er størstedelen af profilerne fremstillet af PVC. Indenfor PVC-profilerne er vinduesprofilerne den type, som fremstilles i det største volumen.
Energiforbruget til fremstilling af PVC-profiler er typisk 0,5 kWh pr. kg PVC (totalt forbrug til ekstrudering, administration m.m.).
13.4.3.2 Vinduesprofiler
Vinduesprofiler fremstilles i Danmark af to producenter. Profilerne er omfattet af normen for vinduer "RAL 716/1 pkt. 1.2.2", der bl.a. angiver hvilke parametre og DIN-normer, som profilet skal overholde. Endvidere er vinduer, beregnet for det svenske marked, underkastet Verksnorm 3000. Begge normer foreskriver, at vinduet skal fremstilles i slagfast PVC, modificeret med CPE (chloreret polyethylen), EVA (ethylen-vinyl acetat) eller acrylat i mængder på 6-10%. Dansk Vindues Kontrol's (DVK) specifikationer for profilerne henviser til de to første normer. Endelig har British Standard i BS 7413 fastlagt normer for vinduesprofiler. Heraf fremgår bl.a. at et profil max. må indeholde 10 pct. regenerat fra eget produktionsaffald.
Vinduesprofiler fremstilles i hård PVC uden tilsætning af blødgører. En af producenterne compounderer selv råvaren. Profilerne ekstruderes typisk ved en temperatur på 180-205 °C.
PVC-vinduesprofiler har i mange år været stabiliseret med stabilisatorsystemer indeholdende bly eller cadmium. Dette er ikke tilladt længere i Danmark, men det vides ikke, hvilke stabilisatorer, der præcist har erstattet bly og cadmium. Endvidere tilsættes smøremidler til råvaren. Disse kan være paraffin-, voks-, stearat- eller oliederivatbaserede produkter. Stabilisator og smøremiddel udgør typisk et samlet system og tilsættes tilsammen i mængder varende til 3-5 pct. Typisk fremstilles profilerne i farverne hvid eller grå. Pigmenter anvendt hertil er titandioxid og kridt, eller carbon black. Endelig tilsættes 5-12 pct. kridt som fyldstof.
Mange PVC-profiler har farvet overflade. Disse farves ofte ved at co-ekstrudere et tyndt lag farvet PMMA (acryl) på overfladen af profilet. Endvidere farves profilerne ved pålægning af en farvet folie eller ved lakering.
13.4.3.3 Tagrender, nedløbsrør o.l.
Foruden tagrender og nedløbsrør omfatter produktgruppen profiler til afskærmning af bygningsdele mod vejrlig m.v. Produkterne fremstilles i Danmark af 2 producenter. Begge producenter compounderer deres egen råvare.
Tagrenderne og nedløbsrørene fremstilles i hård PVC uden tilsætning af blødgører. Profilerne ekstruderes typisk ved en temperatur på ca. 180 °C. Som for vinduesprofiler tilsættes der ikke længere bly eller cadmium ved produktion i Danmark, men hvilke stabilisatortyper, der har erstattet bly og cadmium vides ikke. Der tilsættes voks, stearat og oliederivater, som smøremiddel.
Stabilisator og smøremiddel udgør typisk et samlet system og tilsættes i mængder svarende til 3-5 pct. Normalt fremstilles profilerne i farverne hvid, grå, brun eller sort. Pigmenter anvendt hertil er titandioxid, carbon black og brunt organisk pigment. Typisk tilsættes endvidere 5-12 pct. kridt som fyldstof.
13.4.3.4 Rammer
PVC-rammer anvendes indenfor køle- og fryseskabsindustrien som tætningsrammer til døre, låger m.m.
I Danmark produceres disse af 2 producenter. Ingen af producenterne compounderer råvaren selv.
Rammerne består af et hårdt PVC-profil og et fleksibelt PVC-profil, som co-ekstruderes, udskæres og svejses sammen. Det fleksible profil fungerer som pakning, og svejsningen foregår ved varmsvejsning også kaldet stuksvejsning og spejlsvejsning.
Profilerne ekstruderes typisk ved en temperatur på 130-200°C. Det bløde profil er stabiliseret med calcium/zink.
Det fleksible profil er hovedsageligt blødgjort med DEHP. Blødgøreren tilsættes i forholdet 20-60 pct. alt afhængigt af profilets ønskede fleksibilitet.
Typisk fremstilles profilerne i farverne hvid, grå, brun eller sort. De anvendte pigmenter er titandioxid, kridt, carbon black og jernoxid. Udover pigment er råvaren tilsat mængder af paraffinolier på mindre end 1 pct., der virker som smøremiddel. Endelig er råvaren tilsat umættede fedtsyrer i mængder på under 1 pct., der virker som antioxidant.
13.4.4 Fladekstruderede plader og folie
Fladekstruderede plader og folier, fremstillet i Danmark, er fortrinsvis til videreforarbejdning (termoformning af emballager og tekniske artikler). Termoformningsprocessen er beskrevet i et selvstændigt afsnit. De mest udbredte materialer ved fladekstrudering er PS, PET, ABS, PP og PE.
I Danmark eksisterer 5 virksomheder, som fladekstruderer plader og folie, der fortrinsvis videreforarbejdes til emballage eller tekniske artikler ved termoformning.
Fremstillingen af plader og folie adskiller sig på visse områder fra fremstillingen af de hidtidigt omtalte produkter. Ved ekstrudering af plader og folier er der ikke monteret en kalibreringsdyse efter værktøjet, som ved de tidligere nævnte produkter. I stedet kalibreres og køles pladen eller folien ved at passere et sæt kølevalser, som er monteret umiddelbart efter værktøjet. En anden forskel er, at plader og folier ikke køles i vandbad.
De to sider i længderetningen af pladen eller folien er altid ujævn, hvorfor disse afskæres. Dette afskær hakkes og recirkuleres, hvis ikke folien er et laminat af flere forskellige polymertyper. Efter kølingen oprulles eller opskæres og stables ekstrudatet.
13.4.4.1 Plader og folie til emballage
Som angivet i Tabel 1 fremstilles plader til emballage fortrinsvis af PET og PS. Endvidere fremstilles der mindre mængder plader af PE, PP. Sundhedsstyrelsens bekendtgørelse om plastmaterialer og -genstande bestemt til at komme i berøring med levnedsmidler angiver en positivliste for råvarer, der er godkendt til at komme i kontakt med levnedsmidler og dermed bl.a. til levnedsmiddelemballage.
I Danmark er der 4 virksomheder, som fremstiller sådanne plader og folier.
PE- og PP-plader og folie til emballage
PE-plader fremstilles i HDPE. Over 95 pct. af pladerne anvendes til emballager til direkte kontakt med fødevarer. HDPE-plader og -folier ekstruderes ved en temperatur på 220-240 °C, mens temperaturen ved ekstrudering af PP-plader og folie normalt ligger i intervallet 230-250 °C.
Der anvendes både organiske og uorganiske pigmenter. De uorganiske pigmenter indeholder ikke tungmetaller. Tungmetaller i mængder på mindre end 0,015 pct. kan dog findes i de rene pigmenter. Fra råvareleverandørens side er polymeren normalt alene tilsat antioxidanter samt glidemiddel. Herudover er compounden ikke tilsat additiver.
PS-plader og –folie til emballage
PS-plasder og folie til emballage inkluderer også brugen af slagfast polystyren, HIPS. Plader og folie af slagfast PS fremstilles ofte med et tyndt toplag af ikke slagfast PS, PET eller mere sjældent med et toplag af PE. Toplaget coekstruderes samtidigt med selve folien. Ved laminering med PET coekstruderes et meget tyndt lag af ABS mellem toplag og selve folien. Mængdemæssigt udgør toplagene ca. 10 pct. af foliens masse, mellemlaget få procent.
Over 95 pct. af pladerne anvendes til emballager til direkte kontakt med fødevarer.
PS-plader og -folier ekstruderes ved en temperatur på 200-220 °C. Der anvendes både organiske og uorganiske pigmenter. De uorganiske pigmenter indeholder ikke tungmetaller. Tungmetaller i mængder på mindre end 0,015 pct. kan findes i de rene pigmenter. Fra råvareleverandørens side er polymeren normalt ikke tilsat andet. Under 1 pct. af folierne er dog tilsat antistatmiddel. Dette additiv består af et amorft syntetisk silikat. Polymeren tilsættes herudover kun pigmenter hos producenten.
13.4.4.2 Plader og folie til tekniske artikler
Fremstillingen af plader og folie til tekniske artikler adskiller sig i princippet ikke fra fremstillingen af plader og folie til emballage.
Pladerne fremstilles fortrinsvis af PS (inkl. HIPS) og ABS. En mindre mængde af pladerne fremstilles af PC og andre tekniske plasttyper. Disse andre plasttyper er ikke nøjere undersøgt.
Der var i 2000 to producenter af disse produkter i Danmark.
PS-plader og -folier ekstruderes typisk ved temperatur på 200-220°C.
Der anvendes både organiske og uorganiske pigmenter. De uorganiske pigmenter er ikke tungmetalbaserede. Tungmetaller i mængder på mindre end 0,015 pct. kan findes i de rene pigmenter.
Under 1 pct. af pladerne fremstilles af råvarer tilsat brandhæmmer. Denne brandhæmmer indeholder blandt andet bromerede forbindelser, men ikke polybromerede biphenyler. Råvaren indeholder i alt under 1 pct. brom. Brandhæmmeren indeholder endvidere antimontrioxid. Denne er tilsat i mængder svarende til over 0,1 pct. af den færdige compound.
Herudover er der normalt ikke tilsat additiver til PS plader og folie.
13.4.5 Mono- og multifilamenter
Filamenter eller plastfibre fremstilles ligeledes ved ekstrudering, med PP og PE som de altdominerende materialer i Danmark. Filamenter opdeles i to hovedområder, nemlig monofilamenter, der er enkeltfibre, samt multifilamenter, der betegner produkter bestående af bundter af meget fine enkeltfibre.
Monofilamenter anvendes typisk i væverier til fremstilling af bl.a. geotekstiler, afdækningsnet, armering samt til fletning af tovværk og fiskenet. Værktøjet, hvori monofilamenterne ekstruderes i hundredvis af fibre, som enkeltvis opspoles for videre forarbejdning. Multifilamenter anvendes hovedsageligt indenfor to områder, nemlig til hygiejneprodukter som bleer, bind og inkontinensprodukter og til tekstilindustrien til fremstilling af bl.a. geotekstiler, væksthustekstiler, tæpper samt møbel- og madrastekstiler.
Multifilamenterne fremstilles groft sagt på samme måde som monofilamenter, dog har multifilamenterne en finere diameter. Det videre forløb afviger dog, idet bundter med over 100.000 fibre opskæres i forskellige længder for derefter at blive pakket i baller med henblik på opbevaring inden videre forarbejdning.
Multifilamenterne til hygiejnemarkedet er typisk af en langt lettere kvalitet end multifilamenterne til tekstilindustrien.
Filamenter produceres i Danmark af i alt fire virksomheder, idet to virksomheder fremstiller monofilamenter og to virksomheder fremstiller multifilamenter.
Fremstillingen af monofilamenter adskiller sig fra fremstilling af de tidligere omtalte produkter. Filamenternes tykkelse beskrives ved at angive vægten af én 9 km lang fiber. Vægten af 9 km monofilament varierer fra små 200 g til godt 1500 g.
Efter værktøjet, som fremstiller 100-200 monofilamenter ad gangen, køles filamenterne ved at passere et vandbad.
Efter kølingen genopvarmes filamenterne delvist. I varm tilstand strækkes de i længderetningen. Herved orienteres molekylerne i hvert enkelt filament, hvilket øger filamentets styrke væsentligt.
Strækningen udføres ved, at filamenterne passerer en række ruller, hvor de sidste rullers omdrejningshastighed er større end de første rullers.
Efter endt strækning afkøles filamenterne endeligt, hvorefter de enkeltvis vikles på spoler med henblik på videre forarbejdning på bl.a. væverier.
Energiforbruget til fremstilling af monofilamenter incl. belysning, ventilation, tørring m.m. udgør ca. 1,25 kWh pr. kg. PP monofilamenter ekstruderes typisk ved temperatur på 250-270°C.
Monofilamenter fremstilles normalt i gennemfarvede kvaliteter.
Der anvendes både organiske og uorganiske pigmenter. De uorganiske pigmenter er ikke tungmetalbaserede.
25-50 pct. af filamenterne tilsættes UV-stabilisatorer af HALS-typen (hindrede aminer). Additivet tilsættes i form af masterbatch. UV-stabilisatoren tilsættes i omkring 0,5 pct.
Under 2 pct. af filamenterne fremstilles af råvarer tilsat brandhæmmer. Brandhæmmeren indeholder blandt andet bromerede forbindelser, men ikke polybromerede biphenyler. Råvaren indeholder i alt under 1 pct. brom. Brandhæmmeren indeholder endvidere antimontrioxid. Denne er tilsat i mængder svarende til over 0,1 pct. af den færdige compound.
Endvidere er råvaren leveret med indhold af smøremiddel og forarbejdnings- samt langtidsstabilisatorer. Smøremidlet er typisk calciumstearat og stabilisatorerne er antioxidanter. Herudover er råvaren ikke tilsat additiver.
13.4.5.1 PE monofilamenter
HDPE monofilamenter ekstruderes typisk ved temperatur på 240- 260°C.
Monofilamenter fremstilles normalt i gennemfarvede kvaliteter.
Der anvendes både organiske og uorganiske pigmenter. De uorganiske pigmenter er ikke tungmetalbaserede. (Kilde 29 og 30). Mellem 25 og 50 pct. af filamenterne tilsættes UV-stabilisator af HALS-typen. Additivet tilsættes i form af masterbatch. UV-stabilisatoren tilsættes i mængder omkring 0,5 pct.
En lille del af polymeren til monofilamenterne er tilsat glidemiddel. Glidemidlet er en modificeret polyolefin copolymer som tilsættes råvaren i form af masterbatch. Koncentrationen af det aktive stof i det færdige produkt overstiger ikke 500 ppm.
Under 2 pct. af filamenterne fremstilles af råvarer tilsat brandhæmmer. Denne brandhæmmer indeholder blandt andet bromerede forbindelser, men ikke polybromerede biphenyler. Råvaren indeholder i alt under 1 pct. brom. Brandhæmmeren indeholder endvidere antimontrioxid. Denne er tilsat i mængder svarende til over 0,1 pct. af den færdige compound.
Endvidere er råvaren leveret med indhold af smøremiddel og forarbejdnings- samt langtidsstabilisatorer. Smøremidlet er typisk calciumstearat og stabilisatorerne er antioxidanter.
Herudover er polymeren til PE-monofilamenter normalt ikke tilsat additiver.
13.4.5.2 Multifilamenter
Multifilamenter fremstilles næsten på samme måde som monofilamenter, men er som nævnt langt finere end monofilamenterne.
Multifilamenterne samles i bundter med flere hundrede tusinde enkelte fibre. Bundterne køles i vand, genopvarmes, strækkes, kruses, opskæres til stabelfibre i forskellige længder for endeligt at blive presset sammen til baller med henblik på videre forarbejdning til "non-woven" produkter.
I Danmark fremstilles multifilamenter hovedsageligt af PP.
Den enkelte fibers tykkelse angives blandt andet ved enheden Denier, som er vægten af 9 km fiber. Denne vægt varierer efter anvendelsen. Til non-woven produkter anvendes fra 15 gram og nedefter.
PP multifilamenter ekstruderes typisk ved en temperatur på 300°C. Energiforbruget til fremstilling af et kg PP multifilament er typisk 0,5 kWh.
Filamenter fremstilles typisk i hvid eller grå kvalitet, men farvede kvaliteter produceres også.
De normalt anvendte pigmenter er titanoxid, carbon black og jernoxid. Herudover anvendes mindre mængder organiske pigmenter. Der anvendes indfarvet polymer.
Råvaren er leveret med tilsætning af stabilisatorer. Der anvendes både phenol- og phosphitbaserede antioxidanter. De phenolbaserede er typisk hydroxyphenylpropionatestere og de phosphitbaserede er typisk hydroxybenzylphosphonater (butylphenoler).
Råvaren er endvidere leveret med et indhold af forarbejdningsforbedrende glidemiddel (calciumstearat).
Der tilsættes UV-stabilisatorer af HALS typen (Hindered Amine Light Stabilizers)til visse specielle multifilamenttyper. Disse specialtyper stabiliseres endvidere med hydroxybenzylforbindelser.
Herudover er polymeren normalt ikke tilsat additiver.
Efter ekstruderingen, men inden opskæringen, befugtes fibrene med spindeolie. Spindeolien forbedrer fibrenes forarbejdningsegenskaber idet den dels påvirker fibrenes overfladeegenskaber og dels reducerer evnen til elektrisk opladning. Denne olie er typisk rene polyglycolfedtsyreestre.
13.4.6 Elkabler
I Danmark fremstilles elkabler til spændingsområdet 0,005-400 kV, dvs. installationskabler, samt lav- og mellemspændingskabler.
Kort fortalt fremstilles kabler ved at ekstrudere op til flere lag plast omkring en eller flere elektriske ledere. Det inderste plastlag udgør et isoleringslag om den enkelte leder. Dernæst følger et fyldlag om et bundt isolerede ledere og yderst et robust beskyttende kappelag.
Materialevalget afhænger i særdeleshed af, hvilken spænding kablerne skal anvendes til, idet man til høj spænding fortrinsvis bruger PE samt tværbundet PE (= PEX), og til lavere spænding fortrinsvis anvender PVC. Herudover anvendes andre materialer (gummi, papir, asfalt, metal), som ikke beskrives i denne rapport.
I Danmark er der 1 stor og 2 mindre virksomheder, som fremstiller elkabler. Virksomhederne har produktion 5 steder i landet. Oplysningerne i denne rapport er baseret på oplysninger fra den ene store producent.
PVC anvendes fortrinsvis i lavspændingsområdet under 1.000 volt og PE fortrinsvis i højspændingsområdet over 1.000 volt.
PVC'en er blødgjort, og virksomheden compounderer selv sin råvare. Som noget specielt pelleterer producenten compounden efter compounderingen.
PE kvaliteterne er LDPE, MDPE og PEX (tværbundet PE).
Som tidligere nævnt fremstilles kabler ved at ekstrudere flere lag plast omkring en eller flere elektriske ledere af kobber eller aluminium.
Ekstruderingsværktøjet minder i princippet om et værktøj til rørfremstilling. I niplen, som danner rørets hulrum, bliver den elektriske leder trukket ind i kabelværktøjet og polymeren lægges som et rør omkring lederen.
Ekstruderingen foregår uden brug af kalibreringsdyse og ekstrudatet køles i vandbad.
Ved fremstilling af kabler med flere ledere (årer) ekstruderes først et isolerende lag omkring de enkelte ledere. Derefter bliver årerne opsamlet på store spoler. Inden det endelige kabel fremstilles, afspoles de ønskede årer og vikles sammen i et bundt.
Bundtet bliver herefter pålagt de forskellige plastlag. Viklingen danner hulrum mellem de enkelte årer, og for at opnå et pænt rundt kabel pålægges først et fyldlag med et såkaldt trykværktøj. Trykværktøjet presser den bløde compound ned i hulrummene mellem årerne.
I installationskabler er de forskellige plastlag adskilt af et fint lag talkum. Dette talkumlag sikrer bl.a., at lederen nemt kan afisoleres i forbindelse med installation, og påføres umiddelbart før et lag ekstruderes.
Lederen i højspændingskabler omgives af flere lag elektrisk halvledende og isolerende plast. De halvledende lag pålægges for at opnå en ensartethed i det elektriske felt omkring lederen.
Endelig skal det nævnes, at kabler til mellem- og højspændingsområdet ofte omvikles med kobberbånd, ledende papir, asfalt, bly eller kombinationer af disse. Brugen af disse materialer er ikke yderligere undersøgt i denne rapport.
Plasten bliver i visse tilfælde coekstruderet. Et eksempel herpå er ekstrudering af flerfarvede isoleringslag i installationskabler (gul/grøn = jordforbindelse) samt coekstrudering af ledende og isolerende lag i højspændingskabler.
Endelig skal det nævnes, at en linie ofte er monteret med flere ekstrudere, således at flere lag kan pålægges i umiddelbart forlængelse af hinanden. På figuren er der kun angivet brugen af en ekstruder.
Kabler indeholdende lag af PEX eller gummi skal efter ekstruderingen vulkaniseres. Vulkaniseringen foretages ved 300-400 °C og under forhøjet tryk. Trykket etableres i nitrogen atmosfære.
Ekstruderingstemperaturen for PVC, PE og EPDM er henholdsvis 180 °C, 220 °C og 80 °C. Energiforbruget til ekstrudering er ca. 0,25 kWh/kg for PE/PEX og ca. 0,15 kWh/kg for PVC (excl. køling, udsugning m.m.).
De anvendte pigmenter er alle, på nær mindre mængder titanoxid, af organisk karakter og anvendes i form af masterbatch.
PVC-råvaren er endvidere tilsat blødgører. Den anvendte blødgører er for 90 pct. vedkommende DEHP. De resterende 10 pct. er overvejende andre phthalatbaserede blødgørere. Chlorparaffiner anvendes ikke længere ved fremstilling af kabler i Danmark. Der anvendes i gennemsnit små 30 pct. blødgører pr. kg PVC-compound.
Som stabilisator anvendes hovedsageligt calcium-zink stabilisatorer. Det skal her nævnes, at den største danske producent er verdens første producent af blyfri PVC-kabler. En mindre mængde PVC til specialkabler og telekabler stabiliseres stadigvæk med blyholdige stabilisatorer.
Omkring 15 pct. af PVC-mængden bliver i dag brandhæmmet med antimontrioxid. Der tilsættes små 2 pct. antimontrioxid, som anvendes til visse specielle kabeltyper, primært til eksportmarkedet.
Blødgører, stabilisator og antimontrioxid tilsætter kabelproducenten selv til PVC-råvaren. Herudover tilsætter producenten 10-25 pct. kridt som fyldstof. Pigment tilsættes i form af masterbatch.
PE-råvarerne leveres som brugsklare compounds. Dog tilsætter producenten pigmenter i form af masterbatch.
Denne råvare er tilsat antioxidanter i mængder under 0,2 pct. Typen af antioxidant er fortrolig.
Under halvdelen af PE-råvaren er tilsat et organisk peroxid (dicumyl peroxid). Dette peroxids funktion er at initiere dannelsen af tværbindinger i PEX-laget. Der tilsættes omkring 1 pct. peroxid til polymeren.
| Forside | | Indhold | | Forrige | | Næste | | Top |
Version 1.0 Juli 2006, © Miljøstyrelsen.
|