| Forside | | Indhold | | Forrige | | Næste |
Miljø- og sundhedsforhold for plastmaterialer
9 Polyurethanbranchens råvarer
Se også:
Polyurethanbranchens processer
Additiver
Emissioner ved forarbejdning af hærdeplast
Kemiske belastninger i arbejdsmiljøet
Plast og affald
Miljø- og sundhedsvurderinger
Brandegenskaber for plast
Referencer
Indholdsfortegnelse
Oversigtsfigur
9.1 Introduktion
Dette kapitel er i al væsentlighed baseret på rapporten ”Renere teknologi i plastindustrien. Del B: Hærdende polyurethanplast” (Plastindustrien i Danmark, 2000c) og Jensen et al. (2005), suppleret med oplysninger om udvekslinger med miljøet ved råvareproduktion, baseret på udgivelser fra den europæiske plastindustri, APME.
Råvaren ved fremstilling af polyurethan (PUR) består altid af isocyanat og en polyolblanding.
Isocyanater og polyolerne reagerer med hinanden ved dannelse af ure-thanbindinger, heraf navnet polyurethanplast. I nedenstående Figur 1 er strukturen for polyurethanbindinger angivet.
Figur 1. Struktur for polyurethanbindinger.
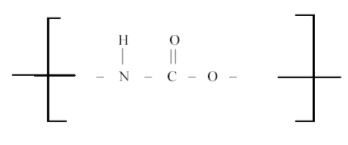
Polyolen leveres oftest som en del af et system, hvor der endvidere er tilsat additiver. "Polyolblandingen" skal således alene blandes med isocyanaten.
Enkelte virksomheder fremstiller deres egne polyolsystemer ved at blande de enkelte råvarer (polyoler, opskumningsmidler og additiver).
9.2 Polyoler
Kemisk er polyolen, som navnet angiver, kendetegnet ved at have to eller flere alkoholgrupper. De anvendte polyoler opdeles i to hovedgrupper nemlig polyethere og polyestere. Polyethere udgør mellem 80 og 90 pct. af polyolforbruget.
Polyolen er typisk iblandet katalysator, additiver m.m. og er typisk en del af et specielt "skræddersyet" system fremstillet til den enkelte PUR-producents specielle behov.
9.2.1 Polyetherpolyoler
Polyetherpolyoler til fleksibelt skum er typisk trifunktionelle forbindelser baseret på glycerin eller trimethylolpropan.
I nedenstående Figur 2 er en polyetherpolyol angivet.
Figur 2. Propylenoxid- og ethylenoxid-baserede polyetherpolyoler.
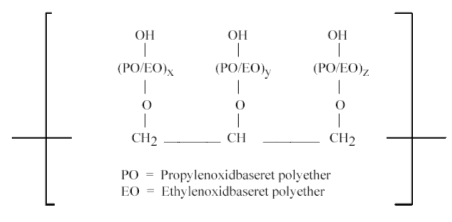
Alkoholgruppen (-OH) er den funktionelle gruppe, som kan reagere med isocyanat.
Polyetherpolyolernes molekylvægt kan varieres ved at variere alkoholgruppernes kædelængde (x,y,z). Til fleksibelt skum anvendes typisk polyethere med molekylvægt på 3.000 - 6.000 gram pr. mol. For hårdt skum er kæderne kortere, 500-2000 gram pr. mol, og antallet af funktionelle grupper ofte højere, typisk 3 - 5.
9.2.2 Polyesterpolyoler
De vigtigste polyesterpolyoler i PUR-sammenhæng fremstilles ud fra adipinsyre eller phthalsyreanhydrid, og alifatiske dioler med 2 - 6 C-atomer, diglykoler, glycerin eller trimethylopropan.
I Danmark er polyesterpolyoler typisk adipinsyrebaserede og anvendes fortrinsvis til fleksibelt skum.
Figur 3. Eksempel på en polyesterpolyol.
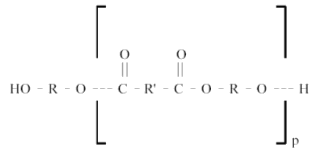
Ligeledes her er alkoholgruppen (-OH) den funktionelle gruppe, som kan reagere med isocyanat.
R kan være en hydrocarbon enten fra adipinsyre (alifatisk med 4 kulstofatomer), fra phthalsyreanhydrid (aromatisk med 6 kulstofatomer) eller hydrocarbon fra en alifatisk diol (med op til 4 kulstofatomer).
9.3 Isocyanater
Isocyanaten er den anden grundkomponent i PUR. Der findes mange forskellige isocyanatforbindelser. Ved fremstilling af PUR-produkter bruges altid isocyanater med minimum to funktionelle grupper. Disse kan reagere minimum 2 gange med polyolblandingens OH-grupper og danne polymerer.
I forbindelse med PUR anvendes altid isocyanater baseret på enten:
- MDI (diphenyl-methan-di-isocyanat) eller
- TDI (toluen-di-isocyanat)
I nedenstående Figur 4 er en isocyanatforbindelse angivet.
Figur 4. Eksempel på en isocyanatforbinelse

Isocyanater fremstilles ud fra reaktion mellem primære aminer og phosgen.
9.3.1 MDI
MDI anvendes typisk til fremstilling af isoleringsskum, fleksibelt formstøbt skum og integralskum. MDI findes i to forskellige former, nemlig monomer-MDI og polymer-MDI.
Monomer-MDI er "ren" ureageret monomer. Ved rumtemperatur er monomer-MDI et farveløst, krystallinsk stof. Monomer-MDI kan polymeriseres og danne polymer-MDI, som er en gulbrun væske. I praksis anvendes begge typer i plastbranchen.
I nedenstående Figur 5 er strukturformlen for MDI givet.
Figur 5. Strukturformel for monomer MDI.
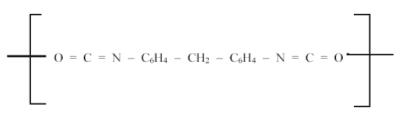
Polymer-MDI har typisk en gennemsnits-funktionalitet på 2,7 - 3 (monomer-MDI har funktionaliteten 2). Polymer-MDI's damptryk er stort set lig damptrykket for monomer-MDI. MDI's mættede damptryk ved 25°C er <0,00001 mbar.
9.3.2 TDI
TDI anvendes fortrinsvis i plastbranchen til fremstilling af blødt skum. Ved stuetemperatur er TDI en lavviskøs, glasklar væske.
I nedenstående figur 6 er strukturformlen for TDI angivet.
Figur 6. Strukturformel for TDI.
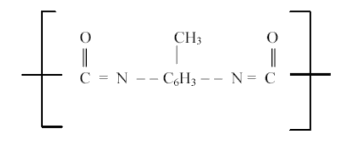
I forhold til MDI har TDI et relativt højt damptryk, hvilket medfører, at selv stænk og spild af små mængder kan give anledning til relativt høje TDI-koncentrationer i arbejdsmiljøet. Speciel opmærksomhed skal derfor rettes mod håndteringen heraf. TDI’s mættede damptryk ved 20°C er 0,02 mbar. I praksis anvendes en blanding af 2,4-TDI og 2,6-TDI i forholdet 80/20 – i sjældnere tilfælde også 65/35.
9.3.3 Præpolymerer
Isocyanater kan i visse specielle tilfælde være forpolymeriseret med polyol, hvorved der opnås en bedre kontrol over hærdeprocessen.
Dette anvendes kun i meget begrænset omfang og hovedsageligt til fleksibelt integralskum, hvor stor styrke er påkrævet. Præpolymeriserede isocyanater har en relativ høj viskositet, hvilket vanskeliggør anvendelsen i almindeligt produktionsudstyr.
9.4 Hjælpemidler og additiver
Der anvendes en bred vifte af hjælpemidler og additiver ved produktionen af PUR. I de følgende afsnit tegnes der et overordnet billede af, hvilke kombinationer af stofgrupper/funktioner, der typisk anvendes.
9.4.1 Katalysatorer
Til at katalysere dannelsen af urethanbindingen, samt for at begrænse dannelsen af uønskede sidereaktioner, anvendes basiske forbindelser som f.eks. tertiære aminer eller organiske metalforbindelser og tinforbindelser.
Katalysatorerne er typisk tilsat polyolen af systemproducenten i koncentrationer på i alt 0,5-3 pct. Enkelte producenter blander dog selv deres råvarer.
9.4.2 Tværbindere og kædeforlængere
Udover tilsætning af katalysatorer tilsættes typisk lavmolekylære, flerfunktionelle alifatiske eller aromatiske alkoholer eller aminer som kædeforlængere og cross-linkere (krydsbindere).
Stofferne deltager i polyol-isocyanat reaktionerne og får dermed en væsentlig indflydelse på polymerstrukturen og dermed på plastens mekaniske egenskaber.
Kædeforlængere er difunktionelle, tværbindere (cross-linkere) er tri- eller polyfunktionelle. Specielt anvendte kædeforlængere er 1,4-butandiol og diethyltoluendiamin. Som cross-linkere anvendes typisk glyceroler og di- samt triethanoldiaminer.
Kædeforlængere og cross-linkere er ligesom katalysatoren typisk tilsat polyolen af systemproducenten i koncentrationer på 2 - 5 pct.
9.4.3 Opskumningsmidler
Opskumningsmidler eller blæsemidler grupperes i to grupper nemlig fysiske opskumningsmidler og kemiske opskumningsmidler.
Fysiske opskumningsmidler. Reaktionen mellem isocyanat og polyol udvikler varme, hvorved de fysiske opskumningsmidler fordamper. Den dannede gas fastholdes i "lommer" i den hærdende PUR, hvorved cellestrukturen opstår.
Opskumningsmidlet tilsættes polyolråvaren. Tidligere har først CFC-gasser og siden HCFC-gasser været anvendt, men dette er ikke tilladt i dag på grund af deres uønskede egenskaber med hensyn til nedbrydning af ozonlaget og bidrag til klimaændringer. HFC- og FC-gasser anvendes stadig, men det vil som hovedregel ikke være tilladt at importere, sælge eller anvende HFC og andre industrielle drivhusgasser efter 1. januar 2006.
Som alternativ anvendes i dag kulbrinter som cyclopentan, isopentan og n-pentan til opskumning af PUR i fjernvarme- og køle/fryseskabsbranchen.
Kemiske opskumningsmidler. Kemiske opskumningsmidler virker ved at de som følge af en kemisk reaktion danner en gas, der jfr. de fysiske opskumningsmidler medvirker til cellestrukturdannelsen. I PUR-plast til fleksibelt skum og portpaneler anvendes vand, som reagerer med isocyanat og danner gassen CO2. Det er også muligt at anvende flydende CO2.
9.4.4 Cellestabilisatorer
For at stabilisere den dannede skum, indtil PUR-plasten er hærdet, tilsættes ofte en skumstabilisator. Denne er et overfladeaktivt stof f.eks. polysiloxan-polyether-copolymer eller analoge siliconeolier. Dette additiv styrer endvidere om cellestrukturen bliver åben eller lukket.
9.4.5 Brandhæmmere
Til visse anvendelser af PUR-plast er det nødvendigt at brandhæmme polymeren. Der kan anvendes fosfor-, halogen-, og kvælstofholdige forbindelser.
9.4.6 Andre additiver
Udover ovennævnte additiver tilsættes ofte organiske farvepigmenter og til visse typer fleksibelt skum endvidere blødgørende additiver. Disse virker ved at påvirke fordelingen af hårde og bløde segmenter i skummet.
Der kan tilsættes UV-stabilisatorer for at beskytte skummet mod sollys og hydrolysestabilisatorer (antioxidanter) for at modvirke hydrolyse af esterbindingerne. Disse stabilisatorer er tilsat af råpolyolfabrikanten.
Endelig kan PUR tilsættes "filler" i form af calciumcarbonat, formalet glas m.m.
9.4.7 Slipmiddel
Ved støbning af emner i PUR-plast påføres formen et slipmiddel, således at produktet slipper formen. Endvidere anvendes slipmidlet til at kontrollere glans m.m. på støbte emners overflade.
Slipmidlet er typisk et eller flere faste stoffer, der er opløst eller opslæmmet i et opløsningsmiddel.
9.5 Udvekslinger med miljøet ved produktion af råvarer
Sammenslutningen af plastproducenter i Europa, APME, har i deres rapporter blandt andet beskrevet udvekslingerne med miljøet ved produktion af de vigtigste råvarer til polyurethanproduktion, MDI, TDI og polyol. APME’s beregninger, der er dokumenteret i APME (1999), er gengivet i lettere bearbejdet/forkortet version i Tabel 1.
|
Enhed |
MDI |
TDI |
Polyol |
Energiforbrug |
|
|
|
|
Elektricitet |
MJ |
14,02 |
19,29 |
17,67 |
Olie/gas |
MJ |
21,61 |
23,43 |
34,28 |
Andet |
MJ |
59,35 |
66,65 |
41,30 |
Totalt |
MJ |
94,99 |
109,37 |
93,25 |
|
|
|
|
|
Brændselforbrug (totalt) |
|
|
|
|
Råolie |
mg |
500.000 |
550.000 |
780.000 |
Gas/kondensat |
mg |
1.100.000 |
1.200.000 |
720.000 |
Kul |
mg |
320.000 |
330.000 |
230.000 |
Metallurgisk kul |
mg |
18.000 |
21.000 |
550 |
Brunkul |
mg |
100.000 |
290.000 |
180.000 |
Tørv |
mg |
370 |
180 |
350 |
Træ |
mg |
810 |
390 |
1.000 |
Biomasse |
mg |
4.300 |
6.400 |
130.000 |
|
|
|
|
|
Emissioner (luft) |
|
|
|
|
CO2 |
mg |
3.400.000 |
5.000.000 |
3.100.000 |
CO |
mg |
2.800 |
3.400 |
1.800 |
CH4 |
mg |
18.000 |
23.000 |
12.000 |
SOx |
mg |
15.000 |
19.000 |
13.000 |
NOx |
mg |
15.000 |
21.000 |
14.000 |
Chlor |
mg |
1 |
<1 |
2 |
Kulbrinter (uspecificeret) |
mg |
4.000 |
4.400 |
2.600 |
Aromatiske kulbrinter (uspecificeret) |
mg |
73 |
130 |
7 |
Støv |
mg |
4.700 |
6.500 |
11.000 |
|
|
|
|
|
Emissioner (vand) |
|
|
|
|
COD |
mg |
5.300 |
1.200 |
3.400 |
BOD |
mg |
810 |
15 |
640 |
NO3- |
mg |
150 |
7.100 |
6.000 |
NH4+ |
mg |
200 |
840 |
9 |
Kulbrinter (uspecificeret) |
mg |
39 |
190 |
35 |
|
|
|
|
|
Affald |
|
|
|
|
Mineralsk affald |
mg |
84.000 |
120.000 |
220.000 |
Slagge og aske |
mg |
21.000 |
28.000 |
21.000 |
Blandet industriaffald |
mg |
11.000 |
6.900 |
31.000 |
Regulerede kemikalier |
mg |
4.700 |
11.000 |
40.000 |
Inert kemikalieaffald |
mg |
2.800 |
1.600 |
11.000 |
Tabel 1. Udvekslinger med miljøet ved produktion af 1 kg råvarer (MDI, TDI og polyol). Efter APME (1999).
| Forside | | Indhold | | Forrige | | Næste | | Top |
Version 1.0 Juli 2006, © Miljøstyrelsen.
|